- Главная
- Оборудование для печатных плат
- Оборудование для поверхностного монтажа
- Технологии производства плат и поверхностного монтажа
- Инструмент для печатных плат и Запасные части
- Материалы и Химикаты для печатных плат и поверхностного монтажа
- Гальваническое оборудование
- Лабораторное и аналитическое оборудование
- Сервис и техническое обслуживание
- Как нас найти
- Начало раздела
- Главный технолог
- Технологии производства
- Консультации
- Контакты
Монтаж компонентов в корпусах BGA
Авторы: Илья Лейтес, главный технолог ООО "РТС Инжиниринг"
Компоненты в корпусах BGA (Ball Grid Array — матрица шариковых выводов) представляют собой самый сложный элемент в классической технике поверхностного монтажа и вызывают максимальное число вопросов у технологов в связи с большим количеством дефектов, возникающих при пайке и проявляющихся на заключительных стадиях изготовления электронного узла, включая испытания. В статье приводится ряд технологических приемов, примеры оборудования и оснастки, что позволяет минимизировать подобные дефекты, появляющиеся в процессе монтажа.
Рис. 1. Микросхема в корпусе BGA (768 выводов с шагом 1 мм)
MSL | Срок годности | Условия |
1 | Не ограничено | ≤+30 °С / 85% RH |
2 | 1 год | ≤ +30 °С / 60% RH |
2а | 4 недели | |
3 | 168 ч | |
4 | 72 ч | |
5 | 48 ч | |
5а | 24 ч | |
6 | Время на этикетке |
Учитывая сравнительно высокую стоимость микросхем в корпусах BGA (особенно микро процессорных) (рис. 1) и техническую сложность их замены, становится очевидным стремление к минимизации в первую очередь дефектов монтажа и пайки компонентов этого типа. Рекомендации по обеспечению этой задачи можно представить в виде нескольких этапов, реализация которых является необходимым и достаточным условием достижения поставленной цели.
Подготовка и хранение компонентов Корпуса BGA, особенно в пластмассовых корпусах,крайне чувствительны к накоплению влаги из окружающего воздуха. Стандарт IPC (IPC/JEDEC JSTD020C «Классификация по уровню чувствительностик влажности негерметичных твердотельных компонентов поверхностного монтажа при пайке оплавлением») [1] специфицирует 8 уровней чувствительности компонентов к влаге (MSL — Moisture SensitiveLevel) (таблица).
Период с момента вскрытия защищенной от влажности вакуумной упаковки (Floor Life) до начала пайки определяет срок годности компонента. Наивысший уровень (MSL1) означает, что компонент не требует ни специальной вакуумной упаковки, ни температурной обработки перед процессом его монтажа, а также имеет неограниченный срок годности. При традиционной технологии («oловосвинец»)и температурах пайки, не превышающих 220–230 °C,защищенная вакуумная упаковка необходима лишь для интегральных схем крупных размеров, например BGA и PQFP с большим числом выводов.
При переходе на бессвинцовую технологию и температуры,на 30–40 °C превышающие температуру обычной пайки, целесообразно ориентироваться на пониженный (более жесткий) как минимум на одну ступень уровень MSL для компонентов в пластмассовой конструкции средних, а иногда и малых размеров.
По истечении срока годности (хранения в некондиционированных условиях), предусмотренного классификацией, безопасная для компонента пайка возможна только после процесса сушки, который требует тепловой обработки в печи в течение от 24 до 48 ч при температурах от +90 до +125 °C (применение вакуумной сушки увеличивает эффективность процедуры).
Как уже было сказано, компоненты в корпусах BGA и PQFP поставляются в вакуумной упаковке,однако по логистическим или производственным соображениям ее часто вскрывают потребители. Для того чтобы не тратить время на длительную сушку перед пайкой и избавиться от необходимости вести учет времени хранения компонентов после вскрытия данной упаковки до пайки, но при этом выполнить все требования обращения с компонентами, чувствительными к влаге, целесообразно оснаститьсборочно-монтажное производство шкафами сухого хранения (рис. 2).
Рис. 2. Шкафы сухого хранения серии X2M
Представленные в качестве примера шкафы предназначены для хранения материалов,чувствительных к влажности, поддерживают уровень влажности менее 5%, эффективно предупреждают окисление. Вот почему в этих шкафах следует осуществлять и межоперационное хранение всех элементов электронного модуля, подвергаемых мощному термическому воздействию групповой пайки поверхностного монтажа, чтобы избежать негативного проявления эффекта накопленной влаги.
Реболлинг (замена шариковых выводов)
Неоднократно обращался к проблеме реболлигнга, поэтому в данной статье не буду растекаться по древу, а интересующихся подробностями отошлю к [2, 3]. Тем не менее коротко повторю. Наиболее надежным для компонентов BGA является паяное соединение, все элементы которого состоят из свинцовооловянной эвтектики (ПОС61, Sn62, Sn63). Шарики иного состава (в том числе Sn100, SAC,Pb90Sn10 и пр. ) для компонентов, используемых в электронных модулях для спецтехники,следует заменить с помощью операции реболлинга.
Причем шарики надо устанавливать на припойную пасту (а не флюс-клей, который не может обеспечить достаточное количество припоя для формирования качественного паяного соединения). Предвижу традиционное возражение: «Но при этом мы потеряем гарантию». Да, потеряете, зато получите надежное паяное соединение. Можно не менять шарики и сохранить гарантию, и в результате получить малонадежное соединение.
Рис. 3. Ремонтный центр PDR
Рис. 4. Фидер для шариков, которым могут оснащаться установщики Europlacer
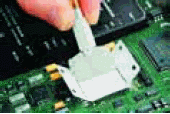
Выберите сами, что для вас важнее. Реболлинг является востребованной в мировой практике операцией, а потому на рынке имеется большое количество материалов (шарики широкой номенклатуры, припойные пасты), оборудования (ремонтные центры, фидера для подачи шариков в установщиках) (рис. 3, 4) и оснастки (трафареты и ракели для локального нанесения припойной пасты и шариков) (рис. 5), обеспечивающие еt реализацию. В частности, представленный в качестве примера на рис. 4 ремонтный центр оснащен бесконтактным контролем температуры компонента/ПП, инновационной системой ИК-нагрева, возможностью оптического совмещения компонента с посадочным местом.
Пайка компонентов в корпусах BGA
Компоненты BGA, как и многие другие аналогичные компоненты, при всей сложности их монтажа обладают замечательным свойством самоцентрирования в момент расплавления припоя и формирования паяного соединения. Это свойство обусловлено силами поверхностного натяжения при смачивании расплавленным припоем соединяемых элементов. Оно нивелирует дефекты совмещения, сдвиг компонентов относительно друг друга и реализуется при соблюдении двух основных условий: припой должен смочить соединяемые поверхности,корпус должен иметь возможность смещаться,то есть не быть заневоленым.
Рис. 6. Припойная паста на ламелях посадочного места BGA
При пайке компонентов BGA следует иметь в виду, что при монтаже многовыводных корпусов BGA (со стороной 30 мм и более) предъявляются жесткие требования по копланарности как корпуса, таки печатной платы в месте монтажа компонента. Эти условия должны обеспечиваться в том числе и в момент нагрева обеих деталей до температуры пайки. Частично некопланарность может быть компенсирована толщиной слоя припойной пасты, нанесенной на ламели печатной платы.
Обычно это 0,15 мм и определяется толщиной трафарета (рис. 6). Поведение печатной платы в части коробления при температурных воздействиях труднопрогнозируемо и минимизируется конструктивными приемами. Основными из них — симметрия поперечного сечения многослойных печатных плат, структура многослойных печатных плат с фольгой на наружных слоях, баланс меди.
Аналогичные процессы могут происходить в динамическом режиме при механических воздействиях (вибрации, ударах, ускорении)и могут быть, как правило, решены оптимизацией конструкционных решений по механической фиксации печатной платы в корпусе. Основные виды дефектов, возникающих при пайке BGA, причины их появления и способы борьбы с ними достаточно подробно рассмотрены в международном стандарте IPC7095B «Проектирование и реализация процессов монтажа с применением BGA» [4].
Контроль качества паяных соединений
Контроль качества паяных соединений корпусов с матрицей шариковых выводов обладает особенностями, в первую очередь связанными с ограниченными возможностями их визуализации. Приборы визуального контроля позволяют контролировать не более двух наружных рядов выводов (рис. 7).
Рис. 7. Оптическая система VPI-1000 для контроля качества паяных соединений шариковых выводов
Оптоволоконная система визуализации контролирует перекосы корпуса в вертикальном направлении, отсутствие или наличие «коллапса» шариков. «Коллапс» шариков — деформация шариков в вертикальном направлении в процессе пайки оплавлением. В сочетании с отсутствием перекоса корпуса эффект «коллапса» позволяет судить о формировании качественного паяного соединения.
Данный эффект наблюдается только в случае шариковых выводов из материала с температурой плавления ниже температуры пайки. Рентгеновский контроль обладает большими потенциальными возможностями проверки паяных соединений шариковых выводов, но, к сожалению, требует комментариев.
Необходима интерпретация рентгенограмм, что может быть реализовано только высокопрофессиональными специалистами с хорошим уровнем инженерного образования, поскольку здесь необходимо понимание конструкции конкретного паяного соединения и процесса пайки.
Обычно рентгеновское контрольное оборудование оснащено программным обеспечением, позволяющим оценить определенные характеристики паяных соединений в автоматическом режиме, минимизируя влияние субъективного фактора. На рисунках, приведенных ниже, показан пример рентгеновского оборудования (рис. 8), которое выполняет контроль BGA-микросхем, пайки активных и пассивных компонентов, пустот,плохих соединений, проводных соединений, а также идентификацию шариков припоя и варианты программной обработки рентгенограмм(рис. 9–11).
Поскольку процесс формирования паяного соединения физически сводится к смачиванию элементов расплавленным припоем, контроль качества таких соединений заключается в наличии или отсутствии, анализе формы и величины галтелей. Для автоматизации данного контроля необходимы индикаторы смачивания на ламелях под пайку. Эти индикаторы могут быть сформированы доработкой посадочного места BGA (на рис. 12 L ≈ D/4).
Наличие подобных индикаторов существенно упрощает процедуру рентгеновского контроля, позволяет использовать более простое, а следовательно, и более дешевое оборудование (рис. 13). Рентгеновские томографы позволяют проводить более прецизионный анализ соединений, однако требуют существенно большего временного и вычислительного ресурса, имеют ограничения по размеру анализируемых образцов, да и стоят в разы дороже.
Рис. 8. Установка рентгеновского контроля
Рис. 9. 2D-рентгенограмма паяных соединений корпуса BGA
Рис. 10. Программная обработка рентгенограммы
Рис. 11. Анализ пустот в паяных соединениях шариковых выводов программной обработкой рентгенограммы
Рис. 12. Доработка посадочного места BGA
Рис. 13. Рентгенограмма паяных соединений BGA c индикаторами смачивания
Рис. 14. Микросхема в корпусе BGA c металлической крышкой-радиатором
Повышение эксплуатационной надежности электронных модулей с компонентами BGA
Компоненты BGA, особенно с металлическими крышками-радиаторами (рис. 14), обладают значительной массой, поэтому могут требовать дополнительной фиксации для динамической разгрузки паяных соединений. Очень технологично, а потому заманчиво, совместить эту фиксацию с нанесением влагозащитного покрытия.
Однако любимые нашими конструкторами многократно испытанные и выдержавшие испытания отечественные влагозащитные составы (как правило,двухкомпонентные) УР 231, ЭП 730, ЭП 9114,ЭП 4100 при отверждении набирают значительные внутренние напряжения и могут, наоборот, ослаблять или даже разрушать паяные соединения шариковых выводов BGA.
Для решения задачи, сформулированной в начале раздела, больше всего подходят влагозащитные лаки толстого нанесения. Это обычно составы полиуретановые составы,которые сочетают хорошие влагозащитные свойства с высокой эластичностью, гарантирующей отсутствие разрушающих внутренних напряжений.
Следует отметить, что максимальная эластичность и минимальные внутренние напряжения достигаются при создании очень постепенных, медленных (не форсированных) условий отверждения (до двух суток при нормальной температуре и влажности).
Дополнительные технологические преимущества этих составов заключаются в следующем: однокомпонентность, возможность нанесения толстых слоев (до 200 мкм) в один прием, технологическое отверждение до отсутствия прилипания путем краткосрочного УФ-облучения.
В заключение хочется сказать, что описываемый процесс настолько многогранный и многофакторный, что вряд ли мне удалось рассмотреть все его аспекты и нюансы. И если копнуть глубже, можно найти еще много интересного. буду доволен, если кому-нибудь в профессиональной деятельности помогли мои рассуждения.
Литература
1. IPC/JEDEC JSTD 020C. Moisture / ReflowSensitivity Classificasion for Nonhermetic SolidState Surface Mount Devices.
2. Лейтес И. Бессвинцовая директива: что насожидает в ближайшем будущем // Производство электроники. 2006. № 4.
3. Лейтес И. Реболлинг и проблема обеспечения надежности паяных соединений //Производство электроники. 2008. № 12.
4. IPC 7095B. Design and Assembly ProcessImplementation for BGAs.