- Главная
- Оборудование для печатных плат
- Оборудование для поверхностного монтажа
- Технологии производства плат и поверхностного монтажа
- Инструмент для печатных плат и Запасные части
- Материалы и Химикаты для печатных плат и поверхностного монтажа
- Гальваническое оборудование
- Лабораторное и аналитическое оборудование
- Сервис и техническое обслуживание
- Как нас найти
- Начало раздела
- Главный технолог
- Технологии производства
- Консультации
- Контакты
Реболлинг и проблема обеспечения надежности паяных соединений
Авторы: Илья Лейтес, главный технолог ООО "РТС Инжиниринг"
Обеспечение высокой надежности электронных модулей (для критически важных приложений), работающих в жестких условиях эксплуатации, требует применения особых методов пайки соединений. В статье обсуждаются вопросы применения BGA микросхем с бессвинцовыми шариками в устройствах с повышенными требованиями к надежности путем использования реболлинга при монтаже BGA-компонентов.
Реболлинг – замена шариковых выводов у микросхем в корпусе типа BGA (Ball Grid Array). Проблема замены (восстановления) шариковых выводов BGA-корпуса возникла в связи с необходимостью выполнения демонтажа/монтажа (перепайки) микросхем данного типа в случае, например, необходимости устранения короткого замыкания между выводами. Оборудование и технология этой операции отработаны и в настоящее время существует несколько технологических схем, из которых наиболее совершенной, по-видимому, является следующая. После демонтажа микросхемы производится очистка (удаление остатков припоя) контактных площадок; затем на контактные площадки трафаретом (или дозатором) наносится припойная паста. На пасту устанавливаются готовые шарики (их можно приобрести как расходный материал). Проводится цикл оплавления по стандартному тепловому профилю.
В результате выполнения этих операций микросхема считается восстановленной и готовой к следующему циклу пайки.
В связи с введением в 2006 году в Европе и некоторых других регионах директивы ROHS (Ограничение применения вредных веществ) в решении задачи реболлинга возникли новые проблемы, связанные с возможностью смешанной комплектации электронных модулей. Смешанная комплектация – это наличие в составе комплектующих электрорадиоэлементов (ЭРЭ) как со свинецсодержащим покрытием, так и с бессвинцовым покрытием выводов.
Необходимо подчеркнуть, что вопросы, рассматриваемые в данной статье, касаются только электронных модулей спецприменения, т.е. устройств, к которым предъявляются повышенные требования по надежности при жестких условиях эксплуатации в течение длительных гарантийных сроков. В частности, речь идет о военной, аэрокосмической, медицинской и сложной вычислительной технике, т.е. аппаратуре, отказ которой может привести к катастрофическим последствиям.
Ввиду особых требований к таким модулям, их комплектация вообще не должна в своем составе содержать так называемые бессвинцовые компоненты, поскольку надежность бессвинцовых паяных соединений ниже традиционной пайки эвтектическими свинцово-оловянными припоем (ПОС-61, Sn 63, Sn 62).
В директиве ROHS четко определены категории изделий, на которые распространяются ограничения по применению опасных веществ. Как показывает практика, специалисты слабо знакомы с этой директивой, поэтому имеет смысл перечислить здесь те 8 категорий изделий EEE (Electrical and Electronic Equipment), на которые она распространяется (изделия, функционирующие с напряжением, не превышающим 1000 В переменного тока и 1500 В постоянного тока):
- крупные бытовые электроприборы;
- малые бытовые электроприборы;
- информационно-технологическое и телекоммуникационное оборудование; потребительское оборудование;
- осветительная аппаратура; электрические и электронные инструменты;
- игрушки, принадлежности для отдыха и спорта;
- торговые автоматы.
Кроме того, в директивой ROHS определены следующие изделия EEE, на которые не распространяются ее требования:
- изделия военного и космического применения;
- отдельные виды медицинского оборудования;
- оборудование мониторинга и контроля; крупное стационарное промышленное оборудование;
- изделия, входящие в оборудование, находящееся вне рамок Директивы (например, в автомобилях, поездах, самолетах);
- изделия, входящие в раздел Fixed Installations, т.е. комбинацию нескольких видов оборудования, смонтированных для совместной работы и не поставляемые на рынок как отдельные изделия;
- аккумуляторы и батареи;
- запасные части для ремонта, обслуживания и усовершенствования оборудования, поставленного на рынок до 1-го июля 2006 г.
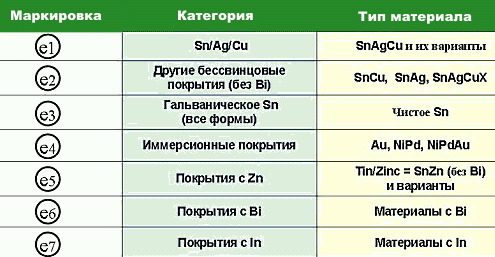
Рис. 1. Категории бессвинцовых материалов и их маркировка
Вспомните крылатую фразу лесковского Левшы: «Передайте царю-батюшке: англичане ружья кирпичом не чистят!»
Следует подчеркнуть, что причины появления смешанной (свинцовой и бессвинцовой) комплектации носят как субъективный, так и объективный характер. Среди этих причин можно отметить следующие.
1. Проблемы при разработке спецификации: разработчики не знают или не хотят учитывать фактор бессвинцовости.
2. Проблемы при закупке комплектующих ЭРЭ: снабженцы не знают или не хотят учитывать фактор бессвинцовости; поставщики настойчиво предлагают или по умолчанию включают в поставку бессвинцовые компоненты.
3. Непреодолимый ценовой или организационный барьер при закупке комплектации категории MIL.
Что же следует предпринять разработчикам и изготовителям аппаратуры специального назначения, учитывая сложившееся положение дел, для обеспечения действительно высоких требований по надежности устройств?
Ответ на этот вопрос может быть следующим.
1. Свести к минимуму бессвинцовую номенклатуру ЭРЭ, используемую в разрабатываемой аппаратуре.
2. Строго требовать от поставщиков сертификации микросхем, в том числе и по номенклатуре паяемого покрытия выводов. Номенклатура бессвинцовых покрытий по IPC 1066 приведена на рисунке 1.
3. При наличии смешанной комплектации реализовывать мероприятия по обеспечению требуемого уровня надежности.
Последний пункт следует рассмотреть особо. Надежность паяных соединений изделия зависит от сочетания применяемых при монтаже элементов покрытия и припоев. Можно выделить несколько вариантов этих сочетаний (в порядке уменьшения надежности).
1. Пайка свинцово-оловянным припоем по такому же или полностью обратно совместимому покрытию (е4). Этот вариант является идеальным с точки зрения обеспечения надежности.
2. Пайка свинцово-оловянными припоями по бессвинцовым покрытиям (е1, е2, е3) – допустимый и наиболее приемлемый вариант в условиях смешанной комплектации. В этом случае формируются паяные соединения с несколько увеличенным (по сравнению с эвтектикой) содержанием олова, что не приводит к существенному снижению уровня надежности паяных соединений.
3. Пайка бессвинцовыми припоями по бессвинцовым покрытиям (е1, е2, е3). Этот вариант соответствует требованиям директивы ROHS, однако не рекомендуется для применения в аппаратуре с повышенными требованиями по надежности. Его можно рекомендовать только для изготовления бытовой аппаратуры, особенно в случае ее экспорта в страны, где действует директива ROHS.
4. Пайка бессвинцовыми припоями по свинецсодержащим покрытиям. Этот вариант обеспечивает самую низкую надежность. В данном случае наблюдается явление так называемого отравления свинцом бессвинцовых паяных соединений, поэтому этот вариант не рекомендуется к применению.
Из перечисленных выше вариантов видно, что наиболее приемлемым решением, который можно рассматривать в качестве альтернативы самого надежного пути(вариант 1) является вариант 2. Поэтому именно его реализацию мы и рассмотрим подробно.
В качестве основных технологических и организационных методов, которые применяются при пайке с использованием эвтектического свинцово-оловянного припоя, можно выделить следующие. Минимальное использование бессвинцовых комплектующих. Использование комплектации с покрытием выводов с полной обратной совместимостью (е4 – для микросхем и иммерсионное золото – для печатных плат). Получение максимально полных и точных данных о паяемых покрытиях из сертификатов, а также используя тестовые комплекты паяемых покрытий (Lead-check) и рентгеновские анализаторы покрытий.
Использование наиболее эффективных материалов (например, свинецсодержащая припойная паста МР218 ф. Мультикор с повышенной температурой активности флюса позволяет паять покрытия е1, е2, е3 при повышенной температуре 240…250оС). При этом необходимо учитывать снижение уровня MSL по IPC . Перелуживание выводов компонентов.
Эта процедура известна и определена во всех зарубежных и отечественных стандартах, регламентирующих требования к выводам микросхем, покрытых гальваническим золотом. Этот процесс широко использовался в 60-80-х гг прошлого века при производстве аппаратуры спецназначения. (Оппоненты могут вспомнить о потере гарантии на микросхему. Однако, кому нужна гарантия, если пайки ненадежные?).
Возвращаясь к проблеме реболлинга, следует сказать, что рассматриваемый вариант сочетания покрытия и припоя, к сожалению, не применим для монтажа микросхем в корпусах BGA с бессвинцовыми шариковыми выводами. Дело в том, что именно материал шарика определяет металлургию паяного соединения и пайка бессвинцовых шариковых выводов свинецсодержащим припоем (припойной пастой) относится к варианту 4, не допустимому с точки зрения надежности.
Таким образом, для обеспечения надежности монтажа микросхем в корпусе типа BGA c бессвинцовыми шариками альтернативы реболлингу нет.
Рассмотрим некоторые общие положения, связанные с процессом пайки и контроля паяных соединений микросхем в корпусе BGA.
В исходном состоянии (до пайки) шариковые выводы микросхемы имеют близкую к сферической форму (см. рис. 2).
Рис. 2. Микросхема в корпусе типа BGA с шариковыми выводами
Рис. 3. «Коллапс» шарика в момент пайки микросхемы
Рис. 4. Отсутствие проседания микросхемы во время пайки из-за ненадежного соединения шариковых выводов с контактными площадками
Рис. 5. Рентгеновский контроль качества пайки микросхем в корпусе BGA
Рис. 6. Адаптация посадочного места корпуса BGA для контроля наличия смачивания
В процессе пайки при расплавлении материала шарика за счет сил поверхностного натяжения происходит проседание микросхемы (шариковые выводы принимают сплюснутую форму – так называемый «коллапс» шарика).
В этот момент происходит самоцентрирование микросхемы относительно контактных площадок посадочного места, и «коллапс» шариков является одним из основных признаков формирования надежного паяного соединения (см. рис. 3).
В свою очередь отсутствие проседания (см. рис. 4) говорит о ненадежности соединений и высокой вероятности нарушения контактов на ранних стадиях эксплуатации или уже во время наладки устройства, что подтверждается практикой.
Как правило, это происходит при пайке бессвинцовых шариков с использованием эвтектического олово-свинцового припоя по стандартному температурному профилю для эвтектики с максимальной температурой 210…220°С или при пайке микросхем с неоплавляющимися шариками какого-либо менее распространенного состава (например, 90% Рb, 10% Sn ).
Кроме визуального контроля формы шарика и наличия галтели смачивания, эффективным методом является рентгеновский контроль пайки микросхем в корпусе BGA. Критериями качества паяных соединений при рентгеновском контроле является правильность (сферичность) формы при виде сверху, повторяемость размеров, минимальное количество пустот, наличие галтели смачивания (см. рис. 5).
Контроль наличия трещин паяных соединений (которые могут возникнуть, как правило, на стадии эксплуатации или испытаний) производится с помощью исследовательских рентгеновских комплексов, оснащенных мощным программным обеспечением.
При пайке микросхем в корпусе BGA необходимо тщательно соблюдать требования MSL по IPC/JEDEC-J-STD-020C (см. таблицу 1).
Таблица 1. Срок годности компонента после вскрытия упаковки в зависимости от уровня MSL по IPC/JEDEC-J-STD-020C
MSL | Срок годности | Условия |
1 | неограничен | ≤30°С/85%RH |
2 | 1 год | ≤30°С/60%RH |
2а | 4 недели | ≤30°С/60%RH |
3 | 168 часов | ≤30°С/60%RH |
4 | 72 часа | ≤30°С/60%RH |
5 | 48 часов | ≤30°С/60%RH |
5а | 24 часа | ≤30°С/60%RH |
6 | Срок указан на этикетке | ≤30°С/60%RH |
Срок годности компонента после вскрытия упаковки (floor life) определяет период времени с момента вскрытия защищенной от влажности вакуумной упаковки до момента пайки компонента в процессе reflow. Наивысший уровень (MSL 1) означает, что компонент не требует ни специальной вакуумной упаковки, ни температурной обработки компонента перед процессом его монтажа, а также имеет неограниченный срок годности.
В случае пайки микросхем спустя срок, превышающий допустимый после вскрытия герметичной упаковки, необходимо проводить процедуру вакуумной сушки. При пайке микросхем с традиционными свинцовыми шариками (покрытиями выводов) по термопрофилю для смешанной комплектации с повышенной максимальной температурой следует ориентироваться на уровень MSL на 2 ступени выше указанного на упаковке.
Заключение
Отметим следующие основные выводы.
1. Бессвинцовая пайка не предназначена для применения в изделиях, к которым предъявляются повышенные требования к надежности и условиям эксплуатации.
2. На сегодняшний день нет возможности избежать смешанной комплектации, в том числе в электронных модулях аппаратуры специального назначения.
3. Существуют следующие методы решения проблемы смешанной комплектации, обеспечивающие приемлемые уровни надежности паяных соединений: использование полностью обратно совместимых паяемых покрытий; перелуживание микросхем с планарными выводами (желательно); реболлинг бессвинцовых шариков микросхем BGA (обязательно); использование технологии пайки смешанной комплектации припойными пастами с эвтектическим олово-свинцовым припоем и флюсом с повышенной температурой активности по соответствующему тепловому профилю.
В заключении следует сказать, что в ОАО «НИЦЭВТ» проведена модернизация монтажно-сборочного цеха, введено в эксплуатацию оборудование поверхностного монтажа (линейка автоматизированного оборудования английской фирмы Europlacer: трафаретная печать, установщик компонентов, конвекционная печь), позволяющее осуществлять технологический процесс поверхностного монтажа, в том числе в среде азота.
Кроме того, освоена технология реболлинга (для изделий, собираемых на линии поверхностного монтажа с последующим контролем паяных соединений на рентгеновской установке). Операция реболлинга проводится на профессиональном ремонтном центре (ф. Мартин, Германия).