- Главная
- Оборудование для печатных плат
- Оборудование для поверхностного монтажа
- Технологии производства плат и поверхностного монтажа
- Инструмент для печатных плат и Запасные части
- Материалы и Химикаты для печатных плат и поверхностного монтажа
- Гальваническое оборудование
- Лабораторное и аналитическое оборудование
- Сервис и техническое обслуживание
- Как нас найти
- Начало раздела
- Главный технолог
- Технологии производства
- Консультации
- Контакты
Обработка и покрытие поверхности базовых материалов, обеспечивающее высокую адгезию.
Процессы адгезионной подготовки поверхности используются в технологии изготовления печатных плат для обработки поверхности меди, и в первую очередь перед нанесением фоторезистов ( в т.ч. паяльной маски), т.е. участвуют в этапе фотолитографического формирования рисунка слоев (как проводящих слоев, так и слоя паяльной маски). Задача этих процессов обеспечить адгезию между фоторезистом и поверхностью меди достаточную для стойкости при воздействиях технологических рабочих сред.
Для паяльной маски – необходимо обеспечить еще и стойкость при воздействии технологии монтажа и эксплуатационных воздействиях т.к. она является конструкционным (базовым) материалом. В кроме того адгезионная подготовка используется для обработки слоев перед прессованием. В этом случае она обеспечивает стойкость структуры многослойных печатных плат при дальнейших технологических и эксплуатационных воздействиях.
Проблемы обеспечения адгезионной подготовки представляется целесообразным рассматривать с точки зрения обеспечения требований к прецизионности рисунка печатных плат (в частности появления новых классов точности по ГОСТ 53429 -2009 «Платы печатные. Основные параметры конструкции»). Итак мы определили, что в техпроцессе изготовления печатных плат адгезионная обработка поверхности проводится на трех этапах:
- перед нанесением СПФ (сухого пленочного фоторезиста, его еще называют травильным или прайм- резистом);
- перед нанесением паяльной маски (ПМ);
- перед прессованием печатных плат,и ее задачей является обеспечение монолитной структуры многослойных печатных плат (с внутренними слоями и склеивающими прокладками) в процессе изготовления.
Подготовка поверхности под СПФ и ПМ.
Как уже говорилось выше подготовки под СПФ и ПМ обеспечивают фотолитографическое формирование рисунка и поэтому очень схожи между собой. Они могут выполняться 3-мя способами (щеточной, гидроабразивной и химической обработкой) и будут рассмотрены в одном разделе.
Во всех описаниях фоторезистов рекомендуемая шероховатость поверхности ( R z ) под их нанесение - около 1-2 мкм. ГОСТ 53432- 2009 «Платы печатные. Общие технические требования к производству» специфицирует необходимую шероховатость после подготовки поверхности, как 1,5 – 2,5 мкм.
Щеточная обработка поверхности.
Щеточная обработка (зачистка) производится абразивными валиками, является наиболее дешевой и производительной. (Рис. 23.)
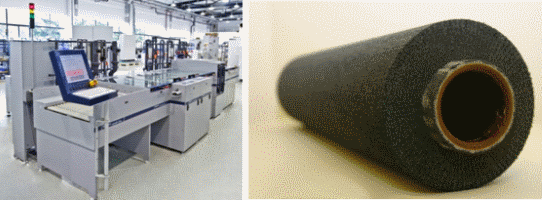
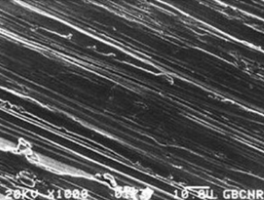
после щеточной зачистки.
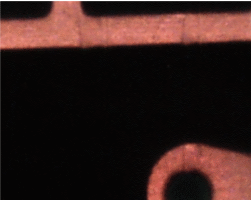
проводников образования поперечных
рисок после щеточной зачистки.
Щеточная зачистка обладает однако недостатком, заключающемся в том, что она формирует на поверхности, четко выраженные, продольные риски в направлении движения заготовки. (Рис. 24.)
Режим осциляции (высокочастотное поперечное микроперемещение вращающихся щеток) снижает этот эффект, но усложняет конструкцию, а следовательно и цену оборудования.
Гидроабразивная (пемзовая) обработкака.
Для подготовки поверхности печатных плат перед нанесением СПФ и паяльной маски более оптимальным способом подготовки поверхности является пемзовая обработка (зачистка). Данный метод позволяет получить более равномерную форму шероховатости поверхности с разнонаправленным рельефом и очистить ее от загрязнении.( Рис.26.).

после гидроабразивной (пемзовой) зачистки.
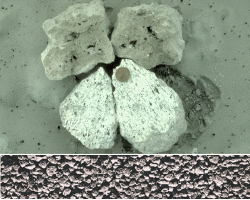
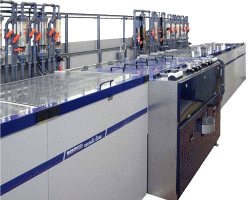
(пемзовой) зачистки.
Однако при использовании этого процесса, следует очень внимательно относиться к выбору размера зерна пемзового порошка. Выбирать размер зерен порошка следует таким образом, чтобы они не забивали отверстия печатных плат. Заклиненные в отверстиях под давлением гидроабразива зерна пемзы очень трудно извлекаемы. Эта ситуация особенно критична для позитивного процесса, т.к. на этапе пемзовой подготовки наружных слоев в отверстиях пока еще только тонкий слой гальванической затяжки и после фотолитографии будет произведена основная металлизация.
В этих условиях наличие посторонних частиц в отверстиях недопустимо. Кроме того следует отметить, что оба способа механической подготовки (щеточная и пемзовая зачистки) при обработке поверхности под нанесение паяльной маски могут служить источниками дефектов для прецизионного рисунка. У проводников шириной 150 ÷ 125 мкм ( а тем более 100 - 80 мкм и менее) адгезия к диэлектрику невелика из-за их малой площади. Сдвиговые усилия, возникающие при механических способах обработки, могут приводить к отрыванию отдельных участков прецизионных проводников от диэлектрического основания.
Марка пемзового порошка «3/0N» (Рис 27.) была специально разработана для применения в производстве печатных плат. Эта марка содержит, в основном, очень мелкие частицы и на взгляд выглядит, как белая пудра. Большинство других марок содержат относительно большие абразивные гранулы , которые могут выводить из строя оборудование пемзовой зачистки за короткий период времени.
Часть пемзового порошка марки 3/0N в виде пудры, работает как смазка, и таким образом предохраняет от царапин большими кристаллами части насосов и трубопроводов технологического оборудования. Не смотря на высокую абразивность, срок службы всех частей установок, обрабатывающих поверхности, в которых используются пемзовый порошок марки 3/0N, достаточно долог. Что позволяет существенно увеличить срок эксплуатации сложного, а следовательно не дешёвого технологического оборудования (Рис.28).
Еще одним назначением мелких частиц является абсорбция жира и других загрязнений, а так же «мягкий» зачищающий эффект. Большие частицы, входящие в состав пемзового порошка марки 3/0N, так же абсорбируют грязь на своей поверхности, но главной их задачей является деформация меди, и «вырывание» загрязнений из углублений.
Химическая подготовка поверхности под сухой пленочный фоторезист (СПФ) и паяльную маску (ПМ).
Метод химической подготовки гарантирует отсутствие механических повреждений элементов рисунка. И для прецизионных печатных плат является практически безальтернативным. Правда здесь следует оговориться, что под термином «химическая подготовка» подразумевается структурное микротравление. Только этот способ химической подготовки, за счет интенсивного растравливания только межкристаллитных промежутков, обеспечивает оптимальную шероховатость, достаточную для обеспечения высокой адгезии фоторезистов. Обычное микротравление (например, персульфатное) не создает нужной шероховатости. Рис.29.
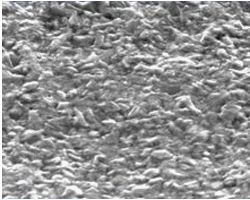
меди после персульфатного микротравления.
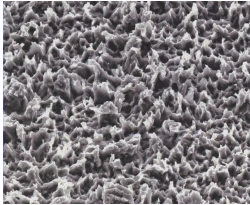
меди после обработки составом
MecEtchBond CZ 8100 фирмы MEC.
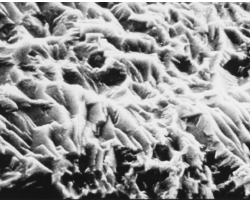
меди после обработки составом
Circuposite Etch 3330 фирмы DOW.
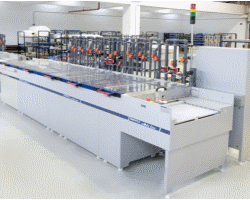
подготовки поверхности.
До последнего времени единственными процессами структурного микротравления на рынке были процессы подготовки поверхности фирмы МЕС. (Рис. 30). Они обеспечивали прекрасную адгезию СПФ. Однако при этом основным их недостатком была поставка в виде готовых рабочих растворов, что существенно увеличивало стоимость реализации операции адгезионной подготовки.
В настоящее время фирма DOW предлагает процесс подготовки поверхности Circuposite Etch 3330, получивший название «селективное микротравление», который, обеспечивает хорошо развитую поверхность (Рис.31.) и одновременно обладает рядом преимуществ:
- - поставляется и корректируется в виде концентратов, что обеспечивает экономичный расход;
- - имеет низкую удельную стоимость в состоянии поставки;
- - универсален в применении (годится как для подготовки под СПФ, так и под паяльную маску);
- - для формирования этого адгезионного покрытия используется стандартное конвейерное оборудование для химической подготовки поверхности.(Рис. 32)
Еще раз повторю, что метод химической подготовки следует считать наиболее подходящим для изготовления печатных плат с прецизионным рисунком. Однако он требует очень аккуратного обращения. Количество допустимых повторных обработок должно быть строго ограничено. В процессе обработки стравливаются большие объемы материала (меди), поэтому необходимо очень внимательно и четко отслеживать режимы обработки и составы рабочих растворов по концентрации отдельных компонентов, плотности и уровню рН.
Особенно это критично при обработке печатных плат на стадии, когда уже имеется металлизация в отверстиях и, в первую очередь, при позитивном процессе. При позитивном процессе резист наносится на гальваническую затяжку (толщиной всего 5-7 мкм ), еще до основной гальванической металлизации; и поэтому, при неоптимальных режимах химической подготовки, его толщина может существенно уменьшаться, вплоть до образования непрокрытий в отверстиях.
При химической подготовке печатных плат с металлизированными отверстиями (формирование рисунка наружных слоев, слоя паяльной маски) необходимо строго контролировать скорость микротравления на уровне не более 0,8-1,0 мкм за один проход . При этом не рекомендуется повторная обработка. Кроме того целесообразно увеличивать толщину гальванической металлизации с учетом стравливаемой при последующих подготовках меди ( в зависимости от числа химических подготовок в последующем технологическом маршруте и допустимом количестве повторов).
Адгезионная подготовка перед прессованием.
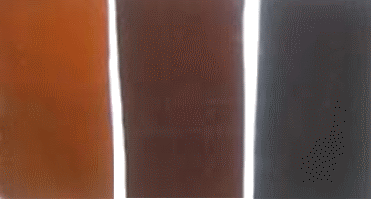
Прочность сцепления поверхности медного рисунка внутренних слоев с материалом диэлектрика при прессовании – одно из важнейших условий изготовления многослойных печатных плат, определяющих надежность многослойных печатных плат и её стойкость при технологических и эксплуатационных воздействиях в течении всего жизненного цикла. Для повышения прочности сцепления поверхности проводников внутренних слоев с материалом диэлектрика применяют операции, позволяющие различными путями увеличить удельную поверхность меди за счет развития микрорельефа.
При прессовании под воздействием температуры и давления расплавленная (находящаяся в «квазижидком» состоянии) смола препрега затекает в углубления микрорельефа медной поверхности, обеспечивая после отверждения смолы формирование механических связей и получение за счет этого единого монолита. Кроме того, учитывая низкую физическую адгезию эпоксидной смолы к металлической меди, целесообразно наносить промежуточный (адгезионный) слой, обладающий повышенной адгезией к металлической меди с одной стороны и эпоксидной смоле с другой. В течении ряда лет с этой целью применялся процесс оксидирования меди.
На практике в процессе оксидирования на поверхности меди образуется смесь закиси меди (Cu 2O) красно-коричневого цвета и окиси меди (CuO) черного цвета. Соотношение количества этих оксидов в смеси будет зависеть от таких параметров техпроцесса, как: температура, время обработки, соотношения окислительного и щелочного компонентов. Получаемый в результате цвет оксидированной поверхности будет различным (рис.33).
Оксидные слои будут отличаться друг от друга не только по окраске, но и по таким параметрам, как :
- - толщина слоя;
- - кристаллическая структура;
- - адгезия к диэлектрику.
Увеличение интенсивности цвета оксида свидетельствует об увеличении толщины оксидного слоя. При этом при переращивании кристаллов черного оксида возникает характерное явление ломкости кристаллов. Визуально этот тип оксида не отличается от черного, но если потереть по поверхности такого оксида кусочком белой ткани, то она окрасится в черный цвет. Поэтому такой оксидный слой называется «черный мел». Этот тип оксида имеет очень рыхлую структуру.
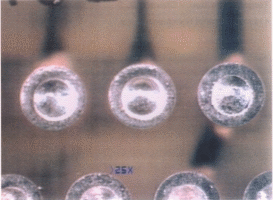
из IPC- A- 600.
При прессовании кристаллы такого оксидного слоя ломаются и плохо сцепляются со смолой препрега, что приводит к нарушениям связи между слоями. Работая по режиму получения черного оксида, мы не застрахованы от того, что при определенных соотношениях окислителя и щелочи в растворе не создадутся условия, благоприятные для образования оксида «черный мел».
Кроме того, как выяснилось, оксидное покрытие имеет еще один существенный недостаток получивший название «розовое кольцо» (Рис.34.)
Этот эффект проявляется на готовой плате, но возникает уже на операциях подготовки плат перед химической металлизацией. Кислые растворы предварительной обработки воздействуют на оксидные слои, выходящие в торец сквозного отверстия. Если оксидный слой подтравливается, то вокруг отверстия образуется розовое кольцо – обнажившаяся медь. На готовой плате это выглядит, как более светлая область вокруг контактной площадки (КП) по сравнению с темной оксидированной поверхностью (на полигонах это действительно кольцо) .
Растворимость в кислотах различных типов оксидного слоя практически одинакова, однако, за счет уменьшения толщины слоя, возможность проникновения кислых растворов и, следовательно, вероятность появления эффекта «розового кольца» в ряду оксидов - “черный мел” > черный > коричневый >бронзовый - существенно снижается от начала к концу перечня.
Следует отметить, что на возможность проникновения кислых растворов в значительной степени влияют операции сверления и прессования. Неправильно подобранный режим прессования, недостаточная текучесть смолы препрега, могут приводить к нарушениям связи между оксидированной поверхностью внутреннего слоя и материалом диэлектрика, то есть к появлению пустот между слоями. Если эти пустоты имеют выход в отверстия, то создается дополнительная возможность для проникновения кислых растворов и возникновения эффекта «розового кольца».
Некачественная сверловка отверстий может приводить к выкрашиванию, смолы , граничащей с оксидированной медной поверхностью, что также способствует проникновению кислых растворов и появлению «розового кольца».
В IPC-A-600 в части эффекта «розового кольца» написано буквально следующее:
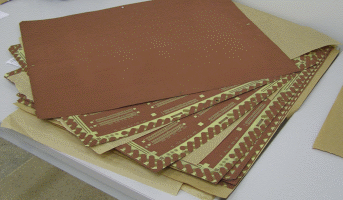
адгезионным покрытием Circubond фирмы DOW.
«Свидетельств того, что «розовые кольца» влияют на функционирование [платы], нет. Чрезмерное присутствие «розовых колец» может рассматриваться как индикатор неудовлетворительного качества реализации технологических процессов, но не является неприемлемым. Главное внимание должно быть уделено контролю за адгезией слоев, очистке и кондиционированию отверстий».
В связи с появлением на рынке предложения новых альтернативных адгезионных покрытий слоев перед прессованием острота и актуальность проблемы «розового кольца» существенно снизилась. Новые процессы формирования адгезионного покрытия предлагают, структурированную микротравлением, медную поверхность обрабатывать органическим антиоксидантом, образующим органо-металлическое соединение с наружным слоем атомов меди, что существенно увеличивает сцепление со смолой в процессе прессования. Одним из примеров такого покрытия является процесс Circubond фирмы DOW (Рис. 35).
Иногда адгезионные покрытия при нанесении имеют некоторую неравномерность цвета по площади, особенно заметную на больших полигонах. На внутренних слоях при просмотре сквозь слой смолы во время приемо-сдаточных испытаний эта неравномерность цвета может быть принята за непропрессовку, хотя таковой не является. Рекомендуется после изготовления поперечных шлифов подтверждающих отсутствие расслоений создавать образцы внешнего вида, утвержденные в установленном порядке.
Реализуется процесс Circubond на стандартном оборудовании для химической подготовки, внешне не отличающимся от представленного на рис.32.
Еще в 2006г. под руководством д.т.н. Галецкого Ф.П. в ИТМ и ВТ были проведены исследования, подтверждающие целесообразность перехода на органо-металлические покрытия для адгезионной подготовки слоев перед прессованием с учетом их не подверженности эффекту «розового кольца» и более высокой по сравнению с оксидами стойкостью к термоударам.
различных видов адгезионных покрытий слоев и смолы до и после термоудара.
№ п/п |
Тип адгезионного слоя | Адгезионная прочность, г/3мм | Уменьшение адгезионной прочность после термоудара (%) | |
До термоудара | После термоудара | |||
1. | Circubond (Dow) | 320 | 270 | 16 |
2. | Bond Film (Atotech) | 220 | 185 | 16 |
3. | Бронзовый оксид | 200 | 80 | 60,0 |
4. | Коричневый оксид | 250 | 175 | 30,0 |
5. | Черный оксид | 220 | 140 | 36,4 |
6. | Черный мел | 165 | 40 | 75,8 |
7. | Пемзовая обработка | 50 | ||
8. | Персульфатное микротравление | 80 | ||
9. | Адгезионный слой фольги в состоянии поставки | 400 |
Для сравнения в таблице 7 приведены данные по адгезионной прочности после пемзовой обработки, персульфатного микротравления, оксидирования, органо-металлического покрытия для адгезионной подготовки слоев перед прессованием и адгезионная прочность после прессования фольги с заводским адгезионным слоем. Учитывая, что обеспечение адгезии на различных этапах технологического процесса является важнейшей задачей, позволяющей в полной мере реализовать надёжностные характеристики печатных плат, и особенно печатных плат с прецизионным рисунком (6-7 кл точности по ГОСТ 53429 -2009), можно сделать следующие выводы:
1. Химическая подготовка (селективное микротравление) наилучший инструмент для создания прецизионного рисунка печатных плат с точки зрения обеспечения адгезии СПФ и ПМ. Однако он требует очень взвешенного технического решения о применении и очень аккуратного технологического обращения. (Обладает достаточно узким технологическим окном).
2. Внедрение органо-металлического покрытия слоев перед прессованием (в замен оксидирования или других методов подготовки поверхности) существенно повышает надежность многослойных печатных плат, а также стойкость многослойных печатных плат к технологическим и эксплуатационным воздействиям.
Еще одной причиной мотивирующей к использованию химического способа адгезионной подготовки перед прессованием является то, что при наличие на слое прецизионных проводников, имеющих малую площадь контакта с подложкой и в связи с этим принципиально меньшую адгезию, они могут быть оторваны от основания при использовании механической подготовки.