- Главная
- Оборудование для печатных плат
- Оборудование для поверхностного монтажа
- Технологии производства плат и поверхностного монтажа
- Инструмент для печатных плат и Запасные части
- Материалы и Химикаты для печатных плат и поверхностного монтажа
- Гальваническое оборудование
- Лабораторное и аналитическое оборудование
- Сервис и техническое обслуживание
- Как нас найти
- Начало раздела
- Главный технолог
- Технологии производства
- Консультации
- Контакты
Базовые материалы для печатных плат
(по материалам «дорожной карты» IPC по межсоединениям).
Для начала – как относится к временным прогнозам приведенным в таблице 3 этого раздела. Приведу цитату из одной из «дорожных карт»:
«Для понимания степени актуальности приводимых долгосрочных прогнозов следует учитывать, что по признанию экспертов IPC во второй год реализации только 30% условий долгосрочных прогнозов были выполнены, еще 30% были исключены из дальнейшего рассмотрения, а 40% для воплощения в жизнь требуют соответствующего пересмотра. Это послужило причиной для того, чтобы IPC , члены IPC и представители Совета по Стратегическому планированию сочли необходимым продолжить углубленные изыскания в вышеуказанных областях.»
Несколько слов об инфраструктуре производства печатных плат и перспектив развития этого сектора индустрии.
Производство печатных плат исторически делится на:
- Технологические расходные материалы
- Основные (базовые) материалы
- Оборудование
К основным (базовым) материалам относятся полимеры, армирующие волокна, медная фольга слоев, а также другие материалы, такие как паяльная маска, маркировочные краски (чернила) и заполнители для отверстий. В данном обзоре охвачены различные уровни работ по CEM, FR-4, BT/эпоксидным полимерам, полиимиду, цианатэстеру и фтороуглероду. Многослойные материалы должны отвечать повышающимся температурным требованиям для бессвинцовой и безгалогенной сборки, и наконец, иметь повышенное сопротивление электромиграции (CAF). Химический состав становится все более сложным, а производители полимеров изобретают новые вещества для обеспечения потребностей индустрии. Кроме того, исследуются альтернативные способы армирования для стеклоткани, которые бы позволяли осуществлять лазерное сверление и другие инновационные техпроцессы.
Изолирующие и диэлектрические материалы для жестких печатных плат.
К сожалению фольгированные ДЭ выпускаемые отечественными производителями отличаются нестабильным воспроизведением декларируемых в НТД технических характеристик. При этом, увы, не все разработчики и производители РЭА осознают, что использование некачественных базовых материалов приводит к ухудшению технических характеристик ( в первую очередь надежностных) РЭА в целом. Лучшими и наиболее стабильными характеристиками из числа отечественных материалов (с которыми я сталкивался на практике) обладают, на мой взгляд, материалы производства «Молдавизолит» г. Тирасполь и «Технотех» г. Йошкар-Ола.
Тем не менее, необходим обязательный входной контроль базовых материалов. Причем, если импортные материалы (по причине их стабильного качества) могут проверяться только на наличие действующих сертфикатов, то по отечественным - необходимо проводить входной контроль по полной программе на соответствие требованиям ГОСТ 26246 или других НТД, действующих на предприятии в рамках «Системы менеджмента качества» (если таковая имеет место быть).
На данный момент при послойном нанесении применяются разнообразные материалы. Армированный слоистый диэлектрик, применяемый в настоящий момент для печатных плат, а также неармированный диэлектрик, применяемый в основном для гибких печатных плат, сочетаются в различных вариантах применения с целью получения конечного продукта малой толщины.
Таким образом, прессование слоев различных материалов, включая связующие вещества, заставляет разрабатывать новые циклы прессования, которые позволяют достичь необходимых параметров времени, давления, вакуумной обработки, нагрева, остывания для получения оптимальных показателей производительности. Фактически, материалы с "наслаиваемой пленкой" являются обычными для Японии, где доминирует технология "переходных отверстий к любому слою" (ALIVH). Это принципиально новый метод по сравнению с материалами, армированными стекловолокном, которые широко распространены в Северной Америке.
Ключевые показатели для различных материалов перечислены в таблице 1.
ПОКАЗАТЕЛЬ | Обычная технология | Передовая технология |
Пропиточный полимер (основа диэлектрика) | Стандартный FR-4 Tg 130-180°C Без наполнителя плохо высушивается |
Высокотемпературный полимер Низкая ДЭ постоянная и к-т рассеивания Специальный полимер для герметизации ИС Специальные наполнители для улучшения свойств |
Пропитываемая ткань | Стекло Е 106,1080, 2116, 7628 |
Без стекловолокна, нетканые и гибридные армирующие материалы для получения сверхтонких нитей стекла Е |
Пропиточный процесс | Соответствующая технология пропитки (на базе прессовки) Однородность полимера +/- 2-3% |
Однородность составляющих полимера ±1.0-1.5% |
Медная фольга | Фольга 18 мкм Низкий профиль Высокий коэффициент теплового расширения |
9 мкм Очень низкий профиль |
Массовый процесс наслоения (прессования) | Плата с 4-6 слоями | Плата с 4-10 слоями |
В ней различаются особенности состояния обычных, качественно новых и передовых технологий. Обычная технология применяется для крупносерийного рентабельного выпуска изделий с хорошо отработанным процессом производства. Качественно новая технология применяется для производства изделий более мелкими партиями и все еще находится на стадии изучении. Передовая технология отображает текущие предельные возможности производства, поэтому по данной категории производятся очень малые партии изделий.
Очевидна тенденция к более тонким базовым материалам с более высокими рабочими характеристиками. Более тонкие, с более низким профилем, медные слои и армирование (либо отсутствие армирующего слоя) позволяют получить более гладкую поверхность, более точные характеристики линий/зазоров между ними, а также общее снижение толщины печатных плат.
Высокотемпературный ( HighTg) полимер увеличивает тепловую сопротивляемость слоя, при этом снижая общее тепловое расширение. Специальные составы для термоударопрочных эпоксидных полимеров улучшают надежность при пайке бессвинцовым припоем. Еще один важный вопрос производства печатных плат – уменьшение диаметра отверстия. Уменьшение диаметра отверстий позволяет увеличить плотность компоновки и функциональность производимых печатных плат.
Потребности в слоистых материалах
Вследствие быстрого перехода на технологии бессвинцовой пайки, а также ограничений по применению опасных веществ (RoHS), требуется срочное усовершенствование базовых материалов.
Здесь следует упомянуть несколько общепринятых заблуждений.
1.Технология бессвинцовой пайки окажет всего лишь незначительное влияние на рабочие характеристики базового материала.
2. Существующие материалы удовлетворяют требованиям бессвинцовой пайки.
Разница в точках плавления от 183˚C до 217˚C для оловянно-свинцовых и оловянно-серебряно-медных припоев, как и результирующие пиковые температуры от 230˚C до 260˚C привели к катастрофическим отказам печатных плат.
И хотя есть веские основания считать, что причиной некоторых отказов являются процессы производства печатных плат, сами по себе материалы -основы находятся на грани пригодности к применению в сборочно-монтажных операциях с бессвинцовой пайкой. Производители слоистых ламинатов, фольгированных медью, во всем мире имеют программы ускоренной разработки базовых материалов, совместимых с бессвинцовой пайкой.
Современные полимерные системы нацелены на включение полимеров широкого назначения с высокими рабочими характеристиками, альтернативных отвердителей для неоднородных и неорганических наполнителей с целью улучшения характеристик материала-основы. Функциональные свойства являются значимыми для совместимости с технологией бессвинцовой пайки, они включают температуру деструкции, время расслоения при 288 и 300˚C, КТР по оси Z и температуру стеклования. И хотя ни одно из отдельно взятых свойств не является значимым, сочетание данных показателей определяет свойства материалов, более подходящих для новых условий применения.
Улучшенные свойства по стойкости к электромиграции также привели к оживлению в деятельности поставщиков слоистых, фольгированных медью, ламинатов. Улучшения реализуются путем применения неагрессивных отвердителей, неорганических наполнителей и высоконадежных финишных покрытий. Также разработано некоторое количество продуктов с улучшенными свойствами по стойкости к электромиграции для применения в сборочных операциях бессвинцовой пайкой.
В общей тенденции прослеживается продолжение снижения диэлектрической постоянной (Dk) и коэффициента рассеивания (Df). для производства печатных плат с малыми потерями. На принятие в производство новых материалов влияют как легкость их изготовления, так и общая их стоимость. Обеспечивающие более высокую вычислительную производительность, но более дорогостоящие материалы на рынке не пользуются спросом, так же как и менее функциональные материалы, но производимые в больших объемах аналогично FR-4. Чувствительные к колебаниям цен термоотверждаемые альтернативы фторпласту получили быстрое развитие в изготовлении материалов с низким Dk и Df. Однако в некоторых случаях оказалось, что материалы с более высокой диэлектрической постоянной имеют лучшие характеристики в случаях применения в конструкциях, где необходимо формировать емкости.
Еще один новый предложенный материал – теплопроводящий диэлектрик. Данный материал допускает гораздо лучший отвод тепла от более мощных процессоров современных компьютеров.
Материалы для формирования встроенных распределенных конденсаторов на самом деле являются специальными многослойными структурами. Фактически, первыми материалами с распределенной емкостью были просто тонкие слои армированного стекло/эпоксидного ламината. На сегодня наметилась тенденция применения параэлектрических либо ферроэлектрических наполнителей в органических полимерах, либо производства специальных тонких диэлектрических слоев с помощью особых приемов, таких как осаждение из гелевых (коллоидных) растворов. При производстве поддерживаются исключительно чистые условия, соблюдаются исключительно строгие допуски, так как данные слои очень важны для электрического функционирования схем.
Требования к новым многослойным материалам также являются производными от требуемых технических факторов (таблица 2). В таблице 3 представлены ключевые технические факторы и их влияние на такие материалы, как полимеры, медная фольга, армирующие материалы, а также составные многослойные материалы. Изменения свойств на основе данных за текущий, ближайший и долгосрочный периоды сформулированы с опорой на максимум доступной информации. Анализ показывает, что технические требования, имеют место практически во всех областях производства материалов и их будущего развития.
В общем итоге, основные потребности отражены в требованиях по повышению плотности межсоединений, снижению размера отверстий, улучшению электрических и термических свойств, а также повышению надежности. В ответ на данные требования, требуется внедрение более тонких материалов, полимеров с повышенной температурой стеклования (Tg), материалов с улучшенной однородностью, более низкими диэлектрическими постоянными. К счастью для производителей данных материалов, в общем направлении развития существует значительное пересечение требований. К примеру, снижение профиля и толщины медной фольги совпадает с потребностями увеличения рабочей частоты, применения тонких проводящих линий и тонких слоистых материалов.
Требование | Полимер | Армирующий материал | Медная фольга | Многослойный материал | Прочее |
Более тонкие слои | Более тонкая ткань Более тонкие исходные материалы конструкции |
Более тонкая и низкопрофильная |
Допуск по толщине уменьшается | Нетканые материалы, Диэлектрические пленки, Медь, покрытая смолой |
|
Усовершенствованный контролируемый импеданс | Более низкая Dk |
Более низкая Dk, Допуск по толщине уменьшается Лучшее ориентирование волокон в пространстве |
Более единообразная толщина фольги | Допуск по толщине уменьшается Лучшее покрытие меди полимером Более однородный материалоснова в пределах 1-5мм. |
|
Более жесткий допуск Dk | Жесткий диапазон значений Dk | Жесткий диапазон значений Dk для высокоскоростных схем | |||
Более высокие частоты | Более низкая Dk, Более низкий Df, Слабое поглощение влаги |
Более низкая Dk, Более низкий Df, Слабое поглощение влаги |
Более низкий профиль | Более низкие и стабильные Dk и Df при повышении частоты, температуры и относительной влажности |
Совместимые с рабочей частотой финишные покрытия |
Рассеивание тепла | Повышенная теплопроводность стеклопластика |
Повышенная теплопроводность слоистого стеклопластика | Наполнитель с высокой теплопроводностью | ||
Теплостойкость | Повышенный Td при T288 и T300, Пониженный КТР по вертикальной оси, Повышенная стойкость к электромиграции. |
Улучшенное финишное покрытие, совместимое с полимером |
Свойство | Единицы измерения / условия | Текущий период | Ближайший период | Среднесрочный период | Долгосрочный период |
Электрические: | |||||
Dk | @ 1 МГц, 2 ГГц, 10 ГГц, 77 ГГц @ 1 МГц (v/25 мкм) | 3.8-4.8 | 3.5-4.8 | 3.5-4.8 | 3.0-4.8 |
Допуск | ±0.1 | ± 0.08 | ± 0.06 | ± 0.04 | |
Изменение влажности | 0.5-1% | 0.4-0.1 | 0.4-0.1 | 0.2-0.7% | |
Df | 0.015 | 0.010 | 0.010 | 0.005 | |
Термические: | |||||
Tg | (по DSC) (°C) | 130-260 | 150-260 | 150-260 | 170-260 |
Td | (по TGA -5% вес потерь) (°C) | 280 - 300 | 300 - 320 | 320 - 340 | > 340 |
T288 | минуты | 1-15 | > 30 | > 45 | > 60 |
T300 | минуты | 1-10 | > 20 | > 25 | > 30 |
T320 | минуты | 1-5 | > 5 | > 10 | > 15 |
КТР по осям x-y | 70-85 | 60-85 | 60-85 | 50-75 | |
КТР по оси z | ppm (30-260°C) | 4.5-5.5 | 4.0-5.0 | 4.0-5.0 | 3.5-4.5 |
ppm ниже Tg % (30-260°C) | Повышенный | Повышенный | Повышенный | ||
Теплопроводность | (w/m°C) | Лучше стеклопластика | Лучше стеклопластика | Лучше стеклопластика | Лучше стеклопластика |
Механические: | |||||
Адгезия проводников | кг/см на 0.5 мм ламинате | ||||
Внутренний слой | 35 мкм | 1.4-1.8 | 1.1-1.4 | 1.1-1.4 | 0.7-1.1 |
Внешний слой | 18 мкм | 1.3-1.6 | 0.9-1.3 | 0.9-1.3 | 0.6-1.0 |
Адгезия проводников при высокой температуре | кг/см230°C-1 мин. | Должно быть сделано | Должно быть сделано | Должно быть сделано | Должно быть сделано |
Проводник: | |||||
Профиль | RtM (мкм) | 8-12 | 6-10 | 6-10 | 4-8 |
Допуск по толщине | % | ±5% | ±4% | ±4% | ±4% |
Качество обработки поверхности | По IPC-4101 | Класс A, B | Класс B | Класс B | Класс 10 |
Прочность на разрыв | Тыс. фунтов на дюйм2 | 40-80 | 50-80 | 50-80 | 50-100 |
Удлинение | Комнатная темп. (%) | 5-15 | 8-15 | 8-15 | 8-15 |
Фактор травления | 180 °C (%) | 1-25 | 6-25 | 6-25 | 6-25 |
Фольга 35 мкм, 75/75 мкм | 2.4-2.5 | 2.4-3.0 | 2.4-3.0 | 2.8-3.0 | |
Основание платы: | |||||
Стабильность размеров | |||||
Отклонение | После травления (мкм/см) | <3 | <2 | <2 | 1 |
Масса армированного стеклотекстолита | Допуск (%) | 2-4 | 2-3 | 2-3 | 1-2 |
Содержание смолы | Допуск (%) | 2-3 | 2 | 2 | 1-2 |
Однослойное армирование | % от многослойного | 10-15% | 15-30% | 15-30% | 25-50% |
Кроме постоянного совершенствования существующих материалов в соответствии с прогнозами на будущее, требуется разработать некоторые новые материалы, чтобы соответствовать изменениям и требованиям в индустрии межсоединений. Для случаев применения межсоединений высокой плотности, крайне необходимы материалы с хорошими абляционными свойствами ( способностью испаряться), либо позволяющие получать тонкие печатные проводники.
Более того, также существует потребность в новых материалах, облегчающих изготовление встроенных интегральных компонентов, или улучшающих электрическую и тепловую производительность. В таблице 4 описано несколько новых и только появляющихся материалов и их свойств. Проблема состоит в точном определении того, как данные свойства можно применить в производстве печатных плат.
Новый материал | Показатель | Применение |
Медь, покрытая полимером | Более тонкий диэлектрик, неармированный, формирование отверстий лазером или плазмой | Микроотверстия |
Фольга для встроенных компонентов | Поверхности лучшего качества | Передовые печатные платы |
Резисторы | Точно выдержанное сопротивление Снижение плотности компоновки внешнего слоя |
Передовые печатные платы |
Тонкий слоистый материал для конденсаторов | Встроенный емкостной слой Снижение плотности компоновки внешнего слоя |
Передовые печатные платы |
Нетканые материалы (арамиды) | Лазерная и плазменная абляция, более низкая диэлектрическая постоянная, низкий КТР по осям xy, более высокая стабильность размеров, соблюдение толщины, высокая температура стеклования Tg, прекрасная стойкость CAF, малый вес |
Передовые печатные платы, микроотверстия, кристаллодержатель, тонкие линии и зазоры, применение в войсковой электронике / авионике |
Фольга осажденная на реверсивном токовом режиме | Улучшенное травление, более низкий профиль, Повышение процента выхода годных изделий |
тонкие линии и зазоры |
Поставщики слоистых материалов активно продвигают новые и постоянно совершенствующиеся продукты, удовлетворяющие потребности производителей печатных плат, упреждая технологические требования. В общем, направление развития производства слоистых материалов они определяются более тонкими конструкциями, более высокими частотами и повышенной плотностью компоновки. Требования поставщиков комплектующих стимулируют применение полимерных систем с более низкими фактором рассеивания и диэлектрической проницаемостью Dk/Df, более высокой температурой стеклования Tg, более высокой температурой разложения Td, более высокими результатами при T288/300/320 и пониженным влагопоглощением.
В то же время, от производителей медной фольги требуется разработать более тонкие и гладкие виды фольги, а также развивать технологии совершенствования равномерности травления. Будущие требования для производителей армированных материалов - это более воспроизводимые электрические свойства, материал с низкой диэлектрической проницаемостью Dk, более тонкие и с оптимизированным плетением - ткани, а также новые высоконадежные финишные покрытия.
Повышенный спрос на портативные устройства общего назначения определяет выбор в пользу более тонкой конструкции с повышенной плотностью компоновки. Спрос на беспроводные устройства, работающие в гигагерцовом диапазоне частот на значительных уровнях мощностей, определяет потребность в более качественных материалах. Кумулятивный эффект всех требований к комплектующим – это общая тенденция к переходу на применение более тонкой медной фольги с более низким профилем, усовершенствованных полимерных систем и армированных материалов для обеспечения более низких показателей диэлектрической проницаемости Dk и тангенса угла потерь Df, а также к созданию новых материалов и изделий в порядке реализации данных требований.
Стала очевидной тенденция к более широкому применению материалов с огнестойкими добавками; FR-4 с дополнительными полимерными системами для инновационных схем. В общем итоге, изменения в армирующих материалах и медной фольге не так велики, за исключением постоянного давления в сторону производства все более тонких изделий и требований уменьшения ширины проводников и зазоров между ними. Однако скорость внедрения данных свойств не так велика, как ожидалось.
Требования по повышению плотности межсоединений и развитию технологии микроотверстий ставят дополнительные условия для разработки многослойных материалов. Как результат, разработаны, либо находятся в разработке несколько новых материалов, которые должны облегчить реализацию повышенной плотности компоновки и малых диаметров переходных отверстий.
Варианты исполнения корпусов элементов как факторов, определяющих усовершенствование материалов, можно разделить на четыре основных категории.
К данным категориям относятся:
- Бессвинцовая пайка, требующая огнестойких добавок к FR-4 следующего поколения.
- Миниатюризация, зависящая от требований по изготовлению более легких изделий с более высокой плотностью компоновки.
- Соединительные изделия, обеспечивающие более высокие скорости обработки сигналов и повышенную целостность (снижение искажений) сигналов, в особенности в высокоскоростных вычислительных системах.
- Безгалогеновые материалы как в компонентах, так и в подложках
Данные факторы являются ключевыми для выбора подходящей передовой технологии изготовления материалов. Они также служат основой разработок по новым, передовым материалам, применяющимся в соединительных подложках.
Традиционные многослойные материалы, фольгированные медью применяются в индустрии многие годы, так как они отвечают требованиям по монтажу и формированию межсоединений электронных компонентов. Изделия для широкого потребления, в особенности портативные и телекоммуникационные, требуют, чтобы данные материалы производились в виде многослойных плакированных медью, чтобы снизить размер и массу. Развивающиеся рынки плат для персональных и портативных компьютеров определят потребность в тонких соединительных материалах с высокими рабочими характеристиками.
Перечень характеристик данных материалов:
- Материалы и процессы для получения встроенных компонентов, таких как резисторы и конденсаторы.
- Полимерные системы повышенной прочности с высокими тепловыми характеристиками.
- Тонкие слоистые материалы с гладкими поверхностями, обеспечивающие применение технологии формирования микроотверстий.
- Тонкая непористая металлическая фольга.
- Альтернативы армированных стекловолокном материалов для сверхтонких подложек внутренних уровней многослойных плат.
- Материалы с низкой диэлектрической проницаемостью для применения с ВЧ и РЧ, а также приемы обработки данных материалов.
- Безгалогеновые материалы-основы.
Материалы для гибких печатных плат
Наиболее часто, гибкие платы разрабатываются для производства неармированных многослойных структур; однако некоторые разработчики изделий успешно применяют сверхтонкие армированные многослойные материалы для более жесткого контроля над процессом. Гибкий материал-основа обычно выбирается либо для того чтобы, сделать возможным его многократное изгибание, либо монтаж платы в изогнутом состоянии в корпусе электронной сборочной единицы.
Обзор материалов в данном разделе затрагивает вопросы состояния и изготовления, связанные с проводниками, изготавливаемыми на гибких органических подложках, которые разработаны с целью их применения в качестве соединительной основы для сборочной единицы, либо для интеграции различных активных и пассивных компонентов. Гибкие печатные платы находят применение там, где соединительные структуры подвергаются интенсивному многократному изгибанию (например, приводы жестких дисков, принтеры), либо там, где требуется поглощение вибрации и ударных нагрузок (например, изделия военного назначения). Большинство гибких печатных плат не попадают под требования по динамическому изгибанию, но должны быть гибкими, чтобы их можно было установить в трехмерном статичном положении. Данная характеристика способствует миниатюризации переносного электронного оборудования и определенных изделий медицинского назначения.
Для специальных изделий также применяются мембранные переключатели (клавиатуры) и однослойные структуры, которые используются как альтернатива монтажным жгутам.
Существуют определенные ограничения по применению гибких печатных плат. Применение монтажных подложек данного типа связано с преимуществами, вытекающими из их гибкости. Например, стабильность размеров неармированных материалов ниже, чем у армированных, поэтому нужно применение нестандартных требований к технологической оснастке и необычных технологических маршрутов, что все вместе сказывается на повышении затрат на производство. Такие материалы (в основном, полиимид), имеющие более высокую температуру стеклования (Tg), пригодны для пайки при более высоких температурах, что и требуется при использовании бессвинцовых припоев, но они более дороги по сравнению с аналогичными жесткими подложками.
Текущее состояние гибких плат, изготавливаемых из органических базовых материалах, обеспечивает получение некоторых уникальных свойств. Благодаря универсальности применения, электронные модули (сборки), построенные на основе гибких плат, являются наиболее интенсивно развивающимся сегментом в семействе электронных межсоединений.
Как таковой, существует растущий интерес и желание разобраться как в тонкостях применения гибких плат, так и сборочных единиц на их основе. Как результат, имеет место заинтересованность в расширении производственной базы, но определенного централизованного источника или "фильтра" для такой информации нет. Таким образом, не всегда можно найти перспективные (доказавшие пригодность) решения; однако, существует значительное число преимуществ применения гибких плат в серийном производстве.
К основным преимуществам относятся:
- Гибкость – включая способность изгибаться для установки в трех плоскостях (перегибы при монтаже).
- Стойкость к изгибаниям при эксплуатации (для применения в условиях динамических изгибов).
- Пригодность к изготовлению схем с малыми размерами элементов и с высокой плотностью компоновки.
- Малый вес, что помогает контролировать общий вес изделия.
- Малая толщина для изготовления плат с низким профилем.
- Гибкие печатные платы в высшей степени пригодны к обработке «с рулона на рулон», со всеми вытекающими экономическими преимуществами такой технологии.
К второстепенным преимуществам относятся:
- Безадгезивные тонкие гибкие слои ( < 25 мкм ) в полностью гибких конструкциях либо в виде гибких слоев встроенных в жесткие платы (могут помочь конструкторам снизить индукцию и электромагнитные помехи - EMI).
- Тонкие гибкие диэлектрики без наполнителя или с наполнителем в виде керамики пригодны к применению в качестве планарных емкостных слоев.
- Лучшее рассеивание тепла с гибких слоев, из диэлектрика с наполнителем в виде керамики.
- Низкая диэлектрическая постоянная (от ≈ 2,5 до 3,5), что способствует повышению скорости прохождения сигнала.
- Низкий коэффициент рассеивания (до 0,005), что способствует снижению затухания сигнала.
- Низкий коэффициент теплового расширения (КТР), что способствует снижению напряжений на паянные соединения.
- Полиимидные материалы выдерживают высокие температуры и пригодны к бессвинцовой пайке.
- Наличие фольгирования сверхтонкой медью.
- Высокое напряжение пробоя, (если требуется).
- Стойкость к возникновению поверхностных токов утечки (CAF).
- Подходят к применению в изделиях с высокой плотностью межсоединений (HDI): пригодность к лазерному сверлению и тонкий медный слой позволяют получать узкие линии и зазоры.
Производство гибких материалов для печатных плат
Для всех гибких печатных плат все более важными становятся требования к стабильности размеров и теплостойкости материала-основы, что повышает интерес к применению полиимидной диэлектрической пленки без клеящего вещества во все большем числе случаев применения. Типовые процессы производства полиимидов без клеящих веществ показаны на Рисунке 22. В то же время, большинство традиционных материалов, где применяется клеящее вещество, скорее всего, найдет дальнейшее применение благодаря тому, что они хорошо освоены индустрией.
В то время как полиимидные и полиэстерные материалы-основы так и будут широко применяться, другие материалы обладают интересным потенциалом, благодаря текущей ситуации в мире, как с точки зрения технологии, так и сточки зрения экономики.
Таким образом, в ближайшее время мы можем стать свидетелями экспериментирования с новыми материалами и способами обработки.
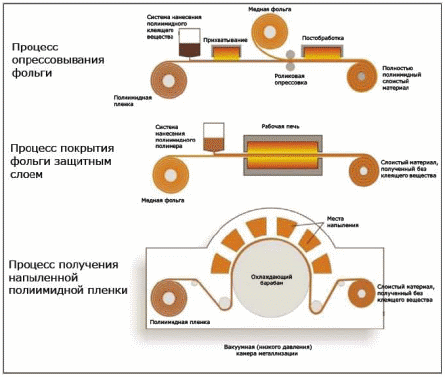
Существует несколько проблем, стоящих перед индустрией производства гибких печатных плат, в особенности это возрастающее применение бессвинцовых припоев. Стабильность размеров, несоответствие КТР, высокая температура обработки, точное размещение, выбор соответствующего финишного покрытия и отмывка – перечень показателен, но неполон.
Перечень некоторых текущих и ожидаемых проблем:
- Стабильность размеров материала – Повышение стабильности размеров материала – это постоянная проблема и цель. Требуется, как достигнуть более высокого объема выпуска с учетом текущей конкуренции, так и помочь производителю выдержать все более жесткие допуски, выдвигаемые для изделий.
- Транспортировка материала по техпроцессу – Снижение повреждений при технологической транспортировке материала крайне важно в производстве гибких печатных плат. Транспортировка – одна из первейших причин появления дефектов в производстве печатных плат.
- Уменьшение размеров элементов печатного рисунка – Потребуется соблюдение более строгих допусков на размеры элементов печатной платы, для применения в будущих высокоскоростных межсоединениях. По мере уменьшения размеров элементов, проблемой, которую нужно будет преодолеть, останется способность их точного воспроизведения.
- Сокращение времени – Снижение времени разработки давно является крайне важным вопросом в условиях рынка с быстро меняющимися старыми и появляющимися новыми продуктами. Будет приветствоваться любое перспективное решение в области конструкции, материалов или техпроцессов.
- Давление цен – В сегодняшней отрасли производства РЭА ожидается постоянное снижение затрат, поэтому производитель ищет как более дешевые материалы, так и техпроцессы, чтобы удовлетворить требования покупателя. Однако до сих пор остается неясным, как повлияет на ценообразование текущая экономическая ситуация в мире.
В общем итоге, проблемы, стоящие перед индустрией производства печатных плат, в основном остаются те же, что и на протяжении всей истории существования отрасли. В основном они связаны с целями и задачами по снижению затрат и повышению производительности.
Перспективные решения проблем, перечисленных выше, потребуют объединить усилия всех участников цикла производства в отрасли. В качестве примера, можно увидеть, что усовершенствованные способы технологической транспортировки и более качественный материал обеспечивают устранение ручной работы и контроль над параметрами техпроцесса, влияющими на изменение размеров, а все вместе ведет к более предсказуемой и воспроизводимой обработке. Области, которым следует уделить внимание – это процессы нанесения защитного слоя и прессования многослойных плат. Также следует более глубоко понимать влияние, которое оказывают на изделие этапы термообработки и различные процессы, такие как плазменное травление, которое применяется для подготовки к металлизации в отверстиях гибких структур, и где клеящее вещество может быть подвержено более агрессивному воздействию.
В отличие от этого, полиимид без клеящего вещества не требует плазменного травления, а может обрабатываться стандартными составами снятия наволакивания на основе перманганата калия.
Безадгезивный материал более подходит для формирования переходных отверстий, полученные отверстия имеют одинаковое основное соотношение и высокое качество стенок, их потенциал нужно изучить более тщательно. Воспроизводимая обработка позволяет выполнять более точную коррекцию фотошаблона для коррекции предсказуемых размерных изменений.Полностью полиимидное исполнение (жесткая основа, наращенные слои, заливка кристаллов, перераспределяющие коммутационные слои за счет использования межсоединений на уровне пластины и дискретные встроенные пассивные компоненты) может решить проблемы механической и электрической надежности. Прямое лазерное экспонирование позволит более легко осуществлять коррекцию рисунка (масштабирование) с учетом изменившихся позиций реперных точек. Корректировка после травления (пробивка откорректированных баз) – является предпочтительной операцией для компенсации усадок материала-основы при стравливании части меди.
Гибкие материалы-основы доказали свою надежность даже в виде тонких диэлектрических пленок (например, менее 20 мкм), без возникновения токов утечки между цепями при стандартных напряжениях. Кроме того, электрические и физические рабочие характеристики гибких материалов-основ могут легко превзойти жесткие армированные (а значит, неоднородные) альтернативы.
Данное преимущество происходит из того факта, что диэлектрические характеристики обусловлены только литьевым полимером , формирующим гибкий материал.
В этом состоит отличие от влияния других материалов, таких как армированный стеклоэпоксид, где следует учитывать свойства полимера и армирующего слоя, чтобы получить нужную диэлектрическую постоянную (Dk). Таким образом, в случае с гибким материалом учитывается только литьевой полимер, в то время как в случае с жестким материалом, свойства будут отличаться в зависимости от типа армирующего слоя, содержания смолы и толщины.
Материалы подложек для монтажа (коммутационных подложек).
Следуя тенденции продолжающегося развития корпусов полупроводниковых устройств, в этом разделе сосредоточим внимание на технологии материалов и операциях, относящихся к разработке подложек для различных форм корпусов с матрицами выводов. В целом, подложки для полупроводниковых кристаллов определяются, как коммутационные структуры («интерпозеры») на основе диэлектрика в качестве механической основы для поддержки и обеспечения электрических соединений между элементами кристалла и структурой основной схемы. Термины «подложка» и «интерпозер» часто используются для указания на одно и то же – промежуточный слой, используемый для электрического межсоединения, а также для заземления и распределения питания.
Производство подложек для компоновки полупроводников является, в некотором роде, специализированным сегментом электронной промышленности. Это, отчасти, является следствием их уникальных требований к высокой плотности цепей, специальных электрических характеристик и термоустойчивости. Хотя использование выводных рамок для соединения подложки, смонтированной на полупроводниках, не является чем-то необычным для поставщиков компонентов, наиболее распространенным применением, широко используемым в настоящее время, является матричная компоновка контактов: корпуса с матричным расположением выводов, корпуса BGA и LGA.
Существует несколько типов компоновочных подложек, но две основные категории определяются, как «жесткие» из-за особенностей материалов или различных методов армирования и «ленточные» (или пленочные), неармированные гибкие подложки. Жесткие подложки поставляются в фиксированной форме, дающей относительно плоскую поверхность, тогда как ленточные или пленочные подложки часто значительно тоньше и в некотором роде поддаются изменению формы. Ранние жесткие подложки, разработанные для компоновки полупроводников, в основном производились с использованием керамических составов, представляя собой очень жесткую, механически и термически прочную основу. Хотя керамические материалы продолжают использоваться в некоторых матричных корпусах, где требуется высокий уровень термической стойкости, органическим подложкам более низкой стоимости отдается предпочтение в большинстве коммерческих применений корпусов матричного типа для корпусирования полупроводниковых устройств.
Для производства подложек на органической основе доступно большое число армированных диэлектрических материалов. Многослойная подложка, разработанная для матричной компоновки, может иметь один, два или несколько слоев для корпусирования полупроводниковых устройств с повышенным числом выводов. Когда требуется два и более слоя , металлические площадки и дорожки связываются друг с другом металлизированными сквозными или глухими отверстиями, во многом так же, как в обычной печатной плате, используемой для сборки второго уровня. Два материала, широко используются для многослойных подложек - это FR4, традиционный слоистый материал на основе эпоксидной смолы, и БТ (бисмалеимид-триазин), более продвинутый и высокочастотный синтетический материал. Растущее число слоистых материалов типа FR-4 включают механически прочные, армированные диэлектрики с физическими свойствами, пригодными для компоновки полупроводников, и свойствами равными материалу БТ.
Несколько композиций имеют относительно высокую Tg (температуру стеклования), низкую диэлектрическую постоянную и проявляют отличные изолирующие свойства. С другой стороны, из-за более раннего начала использования для корпусирования полупроводников, для многих производителей предпочтительными многослойными материалами стали синтетические материалы БТ. На рынке продолжают появляться новые многослойные подложки от некоторых известных поставщиков. Эти материалы были разработаны с использованием передовых эпоксидных смол и композитов на основе их смесей. Ожидается, что это сделает многослойные материалы БТ конкурентоспособными и возможно приведет к большему снижению цен на подложки. Был также разработан материал, обеспечивающий улучшенную высокочастотную производительность, и в то же время простой в изготовлении, основанный на промышленных стеклотекстолитах. Этот материал представляется, как реактопласт, армированный стеклотканью и наполненный керамическими составляющими. Эта специализированная комбинация материалов дает очень высокую температуру стеклования (Tg >280°C), идеальную для применения в условиях высоких температур.
Часто армированные подложки имеют два и более слоя трассировки, а для объединения пассивных устройств в этих слоях существует несколько методов. Например, в 4-хслойной подложке сигнальные слои могут быть разведены в верхнем или нижнем наружных слоях подложки (или в обоих), тогда как внутренние слои в основном используются для заземления и разведения номиналов питания.
Ленточные подложки для матричной компоновки состоят из высокопрочного и высокотемпературного полимерного материала, такого как полиимид. Этот материал отличается низкой диэлектрической постоянной, равной 2,2 при 1 МГц, низким тангенсом угла диэлектрических потерь и влагопоглощением не более 0,1 масс.%, и покрыт слоем тонкой медной фольги с одной или двух сторон. Альтернативным пленочным материалом является жидкокристаллический полимер (ЖКП), идеально подходящий для применения в высокоскоростных полупроводниковых компоновках. Он также имеет низкую диэлектрическую постоянную, равную 2,9, и очень низкое влагопоглощение (0,05 масс.%).
Ламинаты на основе ЖКП также доступны в виде многослойного материала, покрытого с двух сторон тонким слоем меди, и используются для многослойных структур с использованием соответствующих промежуточных склеивающих пленок. Недостатками неармированных гибких подложек являются высокая стоимость материала основы, сложность в обращении во время обработки и в поддержании плоской формы во время осуществления второго уровня сборки. Основными преимуществами гибких подложек полупроводников являются их малый вес, высокая химическая стойкость, способность выдерживать экстремальные рабочие температуры и возможность производства с высокой производительностью методом «с рулона на рулон».
В настоящее время методология подложек, применяемая к матричному типу полупроводниковой компоновки, использует одну из следующих диэлектрических систем:
- Керамика
- Стеклоэпоксид FR-4
- Стеклоэпоксид ( БТ)
- Полиимидная пленка (ПИ)
- Фторопласт (ПТФЭ)
- Жидкокристаллический полимер (ЖКП)
- Реактопласт, усиленный стеклотканью и наполненный керамическими составляющими
Керамика (глинозем – окись алюминия )
Глинозем – это соответственно сконструированная керамическая основа, часто выбираемая для полупроводниковой компоновки, для условий эксплуатации требующих очень высоких рабочих температур. Основной диэлектрический материал, часто смешанный с кремнеземом или микроэлементами для повышения физических свойств или производственной эффективности, имеет довольно низкую стоимость и широко применяется во многих случаях для изготовления высокопроизводительных устройств. Глиноземные подложки были разработаны для монтажа как с проводными соединениями, так и с перевернутыми кристаллами (flip-chip) с использованием процессов аддитивной металлизации (вольфрамом или медью) для обеспечения основы проводника. Поскольку материал физически стабилен, обычной практикой является интегрирование пассивных сопротивлений и индуктиивностей в конструкцию внутрикорпусной схемы.
Стеклоэпоксид (СЭ и БT)
Существует несколько разных материалов, используемых для производства многослойных подложек. Два материала, широко используемые для многослойных подложек - это FR4, традиционный слоистый материал на основе эпоксидной смолы, и БТ (бисмалеимид-триазин), более продвинутый и высокопроизводительный синтетический материал. Для многих производителей предпочтительным ламинированным материалом стала смола БТ, имеющая высокую Tg, низкую диэлектрическую постоянную и хорошие изоляционные свойства. На самом деле, сейчас БТ несомненно является материалом стандартных подложек для BGA, а также используется в фольгированных материалах для компоновки «в размер кристалла» (CSP – chip sase pakage). В Таблице 5 сравниваются основные физические свойства материалов основ полупроводниковых подложек.
Тип | Смола | Армирование | Tg (°С) | Класс горючести по оценкам лаборатории UL |
FR-4 | Эпоксидная | Стеклоткань Е-типа | 130 - 170+ | 94V-0 |
Эпоксид- БT (FR-5) | Эпоксидная/Бисмалеи-мид-триазин | Стеклоткань Е-типа | 170 - 230 | 94V-0 |
Пленка ПИ | Полиимид | Нет | 250 - 265 | 94HB |
ПТФЭ | Фторопласт | Стеклоткань Е-типа | мин. 175 | 94V-0 |
Смешивание бисмалеимида/триазина и эпоксидной смолы обеспечивает улучшенные термические, механические и электрические характеристики по сравнению со стандартными эпоксидными системами. Состав БТ/эпоксид имеет характеристики, делающие его отличным выбором для производства больших по размеру панелей. Преимущества, такие как высокая Tg (180°C), низкий коэффициент теплового расширения и отличная электроизоляция при высокой влажности или повышенной температуре, делают его хорошим материалом для такого выбора.
Новые ламинированные подложки, выпускаемые на рынок, такие как представленные компаниями Hitachi Chemical, Nelco International и Sumitomo Bakelite, состоят из улучшенных эпоксидных смол или эпоксидных смесей. Эти материалы соответствуют директиве RoHS, и ожидается, что они сделают ламинированные материалы БТ конкурентоспособными, что может привести к большему снижению цен на подложки. Данные Таблицы 6 детализируют четыре основные электрические характеристики наиболее распространенных материалов основы подложки для компоновки полупроводников.
Тип | Объёмное удельное сопротивление | Диэлектрическая постоянная при 1 МГц |
Диэлектрическая прочность (В/мил) | Пробой диэлектрика |
FR-4 | 106 Мом/см | 4.3 - 4.6 | 1000 - 1500 | >40 кВ |
Эпоксид- БT | 107 Мом/см | 4.0 | 1750 - 1500 | >40 кВ |
Пленка ПИ | 106 Мом/см | 4.0 | 2000 - 1500 | |
ПТФЭ | 106 Мом/см | -4.0 - 4.5 | >60 кВ |
Значения диэлектрических постоянных могут значительно меняться в зависимости от толщины, окружающих условий и рабочей частоты. Рекомендуется связаться с поставщиком материалов для подтверждения требования по диэлектрической постоянной.
Типичный корпус с матричной конфигурацией выводов на основе ламинированного материала состоит из кристалла с проводными соединениями на подложке, сделанной из стеклоэпоксида или бисмалеимид-триазина, покрытого с двух сторон тонким слоем меди. Помимо основы для корпусов ИС, подложки также используются для межсоединений системы вводов кристалла на элементы межсоединения основной платы. Электрическое сопряжение между элементом кристалла, подложкой и основной платой производится через проводники, вытравленные из медной фольги, припрессованной к одному или нескольким слоям подложки. Медные слои на внешней поверхности обычно покрываются золотом, наносимым методом замещения (иммерсионным), поверх слоя химического никеля. Никель предотвращает взаимное проникновение меди и припоя, в то время как золото ингибирует окисление и увеличивает способность к пайке.
Полиимидная пленка (ПИ)
Эта адаптивная система материала основы разработана с применением полиимидной смолы, подходящей для применения в любых электронных корпусах, которые могут потребовать максимальных характеристик. В частности, теплостойкость делает это материал привлекательным для применений с высокими температурными требованиями, а низкий коэффициент теплового расширения (КТР) обеспечивает отличную надежность металлизированных сквозных отверстий. Пленочные полиимидные подложки состоят из высокопрочного и высокотемпературного полимерного материала.
Главным преимуществом пленочных подложек является их малый вес и возможность прецизионного формирования проводников. Этот материал доказал свою идеальность для лазерной абляции при изготовлении очень маленьких деталей с микроотверстиями. Физически материал очень прочный и является идеальной основой для применения в матричных компоновках с малым шагом. Полиимидная пленка обладает отлично сбалансированными физическими, тепловыми, электрическими и химическими свойствами в широком диапазоне температур (от -270°C до +400°C). Точный контроль толщины, исключительная плоскостноть пленки плюс улучшенная адгезия и отличная объемная стабильность являются стандартными свойствами полиимидных пленок.
Фторопласт ( политетрафторэтилен - ПТФЭ)
В зависимости от требований, имеется несколько вариантов производства многослойных подложек из ПТФЭ (Teflon®)/стеклоткани. Наиболее распространенным вариантом производства подложки является многослойный гибрид, в котором армированный ПТФЭ, с двух сторон плакированный медью, склеен с двухсторонним FR4 или с многослойной структурой из FR4, с использованием стандартных препрегов из FR4 и соответствующего цикла прессования. Многослойная структура целиком из ПТФЭ может быть создана только путем специальной технологии прессования при очень высоких температурах. Если для диэлектрика требуются ВЧ-свойства, используются клееные пленки из сополимера тетрафторэтилена и гексафторпропилена или из хлортрифторэтилена. Хотя диэлектрические свойства материала могут быть основным фактором при выборе ПТФЭ/стеклоткани, пользователи должны осознавать, что материал имеет минимальные значения прочности на отрыв меди, равные ≈ 18 Н/мм даже для медной фольги 17,5 микрон. Одним из основных недостатков материала является трудность обеспечения металлизации сквозных отверстий. Однако поставщики и производители материала утверждают, что они разработали процессы для обработки поверхности тефлона позволяющие его металлизировать.
Жидкокристаллический полимер (ЖКП)
Обычно ЖКП имеют высокую механическую прочность при высоких температурах, предельную химическую стойкость и природную способность к замедлению горения. Хотя ЖКП имеет высокий коэффициент теплового расширения по вертикали, материал противостоит растрескиванию под напряжением при повышенных температурах в присутствии большинства химических веществ, включая ароматические и галогенированные углеводороды, сильные кислоты, газы и другие агрессивные вещества промышленного назначения. Частично из-за существующей цены на материал основы и минимальный опыт у производителей плат по его использованию, ЖКП не имеет широкого применения в корпусировании полупроводниковых кристаллов. Однако некоторые специалисты утверждают, что тонкий листовой материал может служить высокоэффективной основой подложки, к которой прикрепляются полупроводниковые микросхемы и в которую можно встроить даже устройства микроэлектромеханических систем (МЭМС).
Реактопласт, усиленный стеклотканью и наполненный керамическими составляющими
Материал на основе углеводорода, наполненный керамическими компонентами и усиленный стеклотканью, обеспечивает контролируемую диэлектрическую постоянную и низкие потери. В отличие от СВЧ материалов на основе ПТФЭ, для него не требуется специальной обработки для подготовки сквозных отверстий. Поставщики материала заявляют, что стоимость изготовления плат и сборки сравнима с стеклотекстолитами. Материал основы имеет диэлектрическую постоянную в диапазоне от 3,38 до 3,48 и классифицирован, как UL94V-0 (негорючий). Были разработаны соответствующие препреги, чтобы дать возможность пользователям создавать высокочастотные многослойные носители с использованием большинства стандартных технологий обработки FR4.
Поставщики утверждают, что благодаря узким диэлектрическим допускам и низким потерям материал демонстрирует отличные высокочастотные характеристики. Структура материала стабильна по размерам и имеет довольно низкий тепловой коэффициент изменения диэлектрической постоянной и небольшой коэффициент теплового расширения по вертикали, а также низкий коэффициент линейного расширения в плоскости . Хотя этот материал дает отличную функциональность продуктов, требующих стабильной передачи высокочастотных сигналов , у него нет широкой базы для поставок, и из-за ограниченности его применения стоимость производства может быть несколько выше, чем для подложек на основе более распространенных FR-4, БТ или полиимида.
Для многих применений высокая цена подложек высокой плотности была недостатком. Поскольку компании усовершенствовали свои процессы и контролировали использование материалов,цены снизились. Аналитики ожидают, что в этом направлении снижение продолжится на уровне от 10 до 15 процентов в год. В перспективе для пользователей ожидаются более высокая стабильность в размерах, более жесткий контроль разницы КТР и улучшенные электрические и термические свойства..
Далее об этапах технологического процесса изготовления печатных плат (в том числе прецизионных печатных плат 6-7го классов точности)..