- Главная
- Оборудование для печатных плат
- Оборудование для поверхностного монтажа
- Технологии производства плат и поверхностного монтажа
- Инструмент для печатных плат и Запасные части
- Материалы и Химикаты для печатных плат и поверхностного монтажа
- Гальваническое оборудование
- Лабораторное и аналитическое оборудование
- Сервис и техническое обслуживание
- Как нас найти
- Начало раздела
- Главный технолог
- Технологии производства
- Консультации
- Контакты
Технологичность печатных плат (DFM-design for manufacturing)
4.Обеспечение технологичности (DFM-design for manufacturing), с использованием инновационных технологий.
Все организации, так или иначе, имеют отношение к обеспечению технологичности печатных плат (DFM) . Путем нескольких итераций происходит «приработка» заказчика к стороннему (контрактному) исполнителю.
Основные источники проблем, возникающие на этом пути следующие:
- При ведении разработки точно не определен производитель.
- Если производитель определен, разработчик не учитывает возможности производства (причины разные, одна из распространенных – элементарно лень знакомиться с технологическими параметрами производства и непонимание, зачем вообще это необходимо - «диктат разработчика»).
- Изготовитель не сформировал конструкторско-технологические нормы (КТН) своей производственной базы, или сформировал не полно и/или не четко.
Итак, путем последовательных итераций разработчик «нащупал» возможности изготовителя, в свою очередь изготовитель понял, что от него хотят, т.е. часть DFМ-технологии пройдена путем «проб и ошибок».
Следующая стадия, которая в дальнейшем должна стать правилом – очередной «образ» возможностей и требований должен быть отработан как «знание» и внедрен в систему проектирования и разработки. В результате разработчик РЭА будет обладать системой «красных флажков», и соответственно, соблюдение этого коридора, обеспечит контролируемый производственный цикл и предсказуемый результат.
Итак коротко о некоторых аспектах и существующих проблемах, которые позволят разработчикам и производителям печатных плат и ЭМ более эффективно использовать DFM-технологии:
1. Для решения задач DFM необходимо знание всех инфраструктурных составляющих и понимание их взаимовлияния и взаимодействия. Ведь разработка любого проекта сводится к решению 3-х главных задач: функциональность, минимизация стоимости изготовления, надежность в эксплуатации.
2. DFM имеет смысл, как комплексная система для всех инфраструктурных составляющих. Выпадение, полное или частичное, какой-либо из инфраструктурных составляющих, приводит к существенной деструкции всей системы и невыполнению, какой-либо из упомянутых выше главных задач, (чаще всего последних двух).
3. Одним из главных заблуждений разработчиков, с которыми я сталкивался в своей практике, является убеждение, что проблемы DFM (технологичности) являются значимыми, только на стадии серийного производства. В реальной жизни это приводит к необходимости кардинальной переработки проектов после их принятия на стадии прототипирования и при подготовке серийного или даже мелкосерийного производства, с соответствующим увеличением сроков. Кстати большинство проектов спецтехники рассчитаны на серии несколько десятков штук, которые и серией-то в полном смысле нельзя назвать. На самом деле проблемы DFM должны в полной мере учитываться и решаться уже на стадии опытных образцов, а еще лучше прототипов и макетов.
5. Нормативно-техническая база еще одна из составляющих инфраструктуры, сдерживающая внедрение DFM из-за своей недоразвитости . Создавать собственную систему значит терять много времени. Именно по этому я счел необходимым привести выше примеры КТН, в разработке которых принимал участие. Хорошим подспорьем в решении этой задачи могут быть также международные стандарты, используемые хотя бы как справочные.
6. Существенной частью инфраструктуры DFM является освоение передовых перспективных технологических операций, позволяющих разработчикам реализовать новые функциональные характеристики электронных модулей, как правило в части увеличения плотности, скорости передачи сигнала, и т.п. Имею в виду такие актуальные на сегодняшний день операции как:
- прямое формирование рисунка, лазером или с помощью струйных принтеров;
- изготовление печатных плат методом послойного наращивания (SBU – Subsequent Вuilding – Up);
- планаризация путем заполнения отверстий гальваническими методами и органическими составами;
- встраивание пассивных и активных компонентов внутрь многослойных печатных плат ( в том числе в рамках « систем –в-корпусе» и микросборок).
Еще раз вернусь к постановке основной задачи DFM. В отечественной, а чаще в зарубежной технической литературе все чаще встречаются следующие рассуждения:
«На сегодняшний день проектирование с учетом технологических требований часто не проводится, чтобы проекты были переданы в производство в более короткие сроки. Однако это выливается в создание труднореализуемых изделий. Если бы была упорядочена и внедрена технология ввода в производство нового изделия с учетом требований DFM, это позволило бы проводить готовые проекты с учетом технологических возможностей производства в соответствии с полными проектными требованиями, а также это значительно повысило бы качество изделий.
Результатом стало бы создание большего числа оптимизированных проектов, которые будут попадать на рынок быстрее и с меньшим количеством редакционных итераций.»
На самом деле, как правило, задача проектирования для производства сводится к тому, куда перераспределить трудоемкость:
- на стадию проектирования,
- или на стадию производства (подготовку производства, согласование правок проекта, трудоемкость изготовления с учетом нескольких итераций, трудоемкость исправления технологических дефектов, трудоемкость гарантийного обслуживания).
Решение этого вопроса лежит целиком в компетенции организаторов и руководителей разработки и изготовления современной РЭА.
Теперь ряд конкретных рекомендаций по соблюдению правил DFM.
Надо сказать, что хотя большинство действий по соблюдению правил DFM проводятся на рисунке наружных слоев печатных плат, направлены они на обеспечение, через характеристики элементов наружных слоев, симметрии действия сил поверхностного натяжения и бездефектного формирования паяных соединений. Это необходимо для того, чтобы не происходило сдвига компонента в процессе расплавления припоя. Ведь в процессе пайки при автоматизированном поверхностном монтаже ЭМ недоступны для каких- либо технологических манипуляций. Очень важно, чтобы нетехнологичные конструкторские решения, не обеспечивающие выполнения этого условия, были отсеяны на стадии подготовки производства (если они не были выполнены на стадии разработки).
Итак основой формирования паяного соединения является фаза смачивания расплавленным припоем вывода и ламели – поэтому дефекты паяных соединений поверхностного монтажа, как правило, связаны с разницей силы поверхностного натяжения расплавленного припоя на противоположных выводах компонентов , которая в значительной степени зависит от следующих характеристик:
- от периметра ламели;
- количества припоя на ламели;
- вязкости припоя.
Обязанностью конструктора в рамках обеспечения задач DFM является обеспечение этих требований. Несоблюдение при конструировании требований симметрии сил поверхностного натяжения приводит к образованию дефектов паяных соединений (в первую очередь «могильных камней).
На рис.1 показана часто встречающаяся конструкторская ошибка при формировании ламелей на полигоне. Как было сказано выше от периметра ламели зависит сила поверхностного натяжения. Разница периметров противоположных ламелей на рис. 1 = 8∆ (где ∆ зазор между проводящим рисунком и освобождением в ПМ). На миниатюрных компонентах относительная разница между периметрами 2(А+В) и 2(А+В) +8∆, формирует разницу сил поверхностного натяжения, которая, учитывая малый вес миниатюрных компонентов, может приводить к осевому смещению - вплоть до образования «могильного камня».
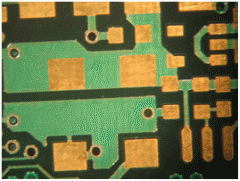
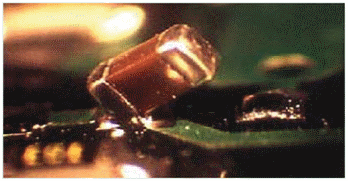
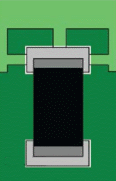
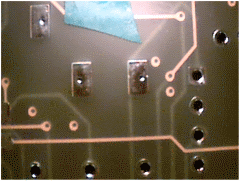
Необходимо при конструировании ламелей на полигоне делать разделение по периметру ламели и соединять ее с полигоном узкими перемычками. В этом случае не возникает большой разницы длины периметров ламелей и соответственно разницы сил поверхностного натяжения. (Рис.2.).
Еще одна типовая конструкторская ошибка - расположение отверстия в ламелях под пайку, что приводит к эффекту - который называется «воровство припоя отверстием» (такой устойчивый термин в технической литературе). Неконтролируемое количество припоя на ламели, связанное с этим эффектом, провоцирует возникновение дефекта, также связанного с разницей сил поверхностного натяжения на противоположных ламелях компонентов.
Один из примеров борьбы с «воровством припоя отверстием». Отделение ламели от отверстия перемычкой ПМ. При этом перемычка должна быть достаточно широкой (≥ 0,5мм).
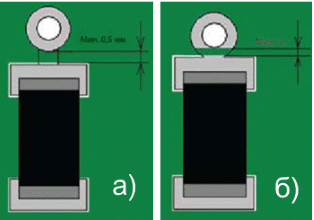
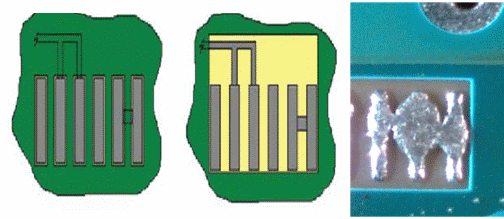
Еще один пример распространенного нарушения правил DFM, приводящего к снижению технологичности и ухудшению качества паяных соединений. При конструировании электрическое соединение соседних ламелей должно выполняться на периферии посадочного места и закрываться паяльной маской. Наличие электрических соединений внутри посадочного места затрудняет для оператора визуального контроля возможность отличить короткое замыкание, связанное с образованием мостиков припоя от схемного электрического соединения. В том числе следует иметь ввиду, что паяльная маска с таких соединений часто отлетает.
Также не допускается объединять в одну соседние ламели микросхем на посадочных местах поверхностного монтажа, и ламели, рядом стоящих чип-компонентов.
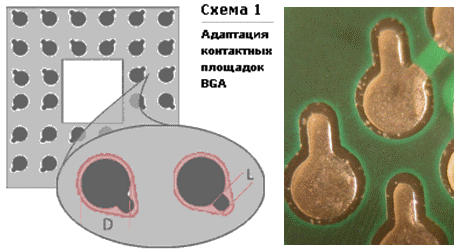
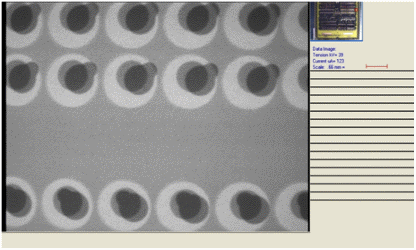
Несколько слов о проектировании посадочных мест компонентов BGA.
Пайка компонентов BGA один из наиболее сложных процессов в монтаже. Тем более, что количество выводов у этих компонентов растет при том, что сами компоненты становятся миниатюрнее.
Все паяные соединения надо контролировать. Большинство из них можно контролировать визуально. Но есть соединения, корректный контроль которых ( в частности паяных соединений BGA) возможен только рентгеном . Однако анализ рентгенограмм «требует комментариев». Необходим большой опыт оператора и понимание им физики процесса рентгеновского контроля для толкования обычных 2D рентгенограмм. Инструмент, облегчающий анализ рентгенограмм, – доработка конструктором посадочного места BGA, что также относится к области задач DFM. (Рис.6.)
Как не один раз было сказано определяющим моментом формирования качественного паяного соединения является наличие смачивания. Доработка конструктором посадочного места существенно облегчает процедуру определения наличия смачивания. Доработка заключается в придании контактной площадке на посадочном месте BGA определенной формы (с удлинением).
Рекомендуемые размерные соотношения доработанных контактной площадки: D≈4L. При наличии смачивания форма шарика на рентгенограмме становится вытянутой, и 2D рентгенограмма доработанного посадочного места позволяет с легкостью определить наличие смачивания на каждой контактной площадки. (Рис.7.)
В последнее время принято конструировать печатных плат с большим количеством компонентов BGA. Количество их выводов растет, шаги уменьшаются. Рассказанное становится на мой взгляд все более актуальным.
Здесь были рассмотрены некоторые аспекты задачи проектирования для производства (DFM), с точки зрения обеспечения норм технологичности при проектировании. Эти аспекты , конечно, относятся в первую очередь к проектированию и изготовлению прецизионнных печатных плат, но вполне актуальны и при производстве печатных плат 3-4 класса точности. Как уже говорилось ранее соблюдение норм DFM приводит к сокращению трудоемкости, увеличению % выхода годных, повышению эксплуатационной надежности выпускаемых изделий.
Буду рад, если кому-то изложенные выше сведения оказались интересными или полезными.
Подробности, разъяснения, любые вопросы - по моему e-mail: technolog@rts-engineering.ru, или по телефону, который можно найти на сайте компании www.rts-engineering.ru.
Это, что касается конструкторского обеспечения DFM. Но есть и технологический аспект, о нем кратко уже говорилось выше. Он касается в первую очередь расширения технических возможностей производства за счет освоения инновационного технологического оборудования и освоения инновационных технологических операций, что конечно должно быть в первую очередь интересно для технологов, для более четкого формулирования требований к правилам проектирования, обеспечивающих технологичность.
Очень часто в практической деятельности приходится сталкиваться с ситуацией, когда разработчик закладывает в конструкторскую документацию (КД ) необоснованно жесткие требования (типа - на всякий случай, хуже не будет) с целью «повышения надежности». А на самом деле, в случае, если требования КД не соответствуют возможностям производства, возникает противоположный эффект. Статистически доказано, что чем выше % выхода годных на приемо-сдаточных испытаниях и чем меньше количество, исправляемых дефектов, в процессе производства, тем выше надежность изделия, и наоборот.
По-видимому, это связано с тем, что часть дефектов пропускается при контроле, а часть скрытых дефектов ещё не проявляется при выходном контроле, но начинают проявляться на этапе эксплуатации. В этой связи очень важно для каждого конкретного производства во-первых иметь правила проектирования и во-вторых при запуске проекта корректировать КД с точки зрения максимально возможного расширения допусков на точность, поддержания технологических режимов на каждой из операций технологического процесса, естественно при сохранении требуемых технических характеристик изделия. Здесь очень важны уровень и глубина сотрудничества разработчика и технологов производства.
Казалось бы целесообразнее уделить больше внимания проектированию. Ведь проектирование делается один раз, а изготовление, как правило, - несколько. Однако , увы, до сих пор нет четкого осознания этого ни у разработчиков, ни у организаторов производства. Поэтому одной из ключевых задач раздела представляется формирование более тесного и глубокого взаимопонимания между конструкторами и технологами.
Таким образом задачи DFM являются существенными для снижения стоимости изготовления печатных плат и ЭМ, обеспечения минимальной трудоемкости и максимального процента выхода годных при производстве. Если эти условия не соблюдаются разработчиком проекта, они должны быть доработаны на производстве (с учетом его конкретных возможностей) подразделением подготовки производства.
Для облегчения подготовки производства на рынке имеется большое количество программных продуктов. «РТС Инжиниринг» предлагает такие программные продукты для подготовки и организации производства UCAM и Integr8tor, которые позволяют быстро и полно оценить технологу производства печатных плат соответствие входящего проекта технологическим требованиям и возможностям конкретной производственной площадки, а также при необходимости внести соответствующие корректировки.
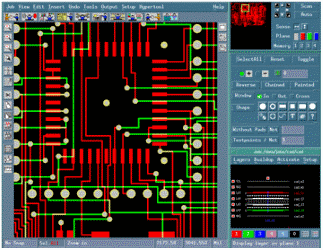
Программа UCAM - это наиболее полная, удобная для пользователя система управления технологическим процессом производства печатных плат, включающая в себя возможности проектирования, обработки данных и проверки технологичности производственного процесса. Использование UCAM позволяет эффективно снижать время и затраты на подготовку производства и производство печатных плат, исключить дополнительные расходы. UCAM является лидером применения в производстве печатных плат по всему миру.
В базе данных UCAM содержатся информация о заказчике, детализация производственного процесса, данные по анализу и проверке на соответствие производственному процессу. Нежелательные действия оператора могут быть заблокированы при помощи специальных систем защиты: Netlist Compare, Netlist Analysis и Image Compare.
Программа подготовки данных UCAM содержит в себе весь необходимый набор инструментария для обработки данных и контроля производственного процесса, а также возможности вывода данных для электрического и оптического контроля печатных плат, лазерных плоттеров, сверлильных и фрезерных станков и оборудования прямого нанесения рисунка. Параметры продукции могут содержаться в формате общей управляющей базы данных, либо в различных форматах других систем CAD/CAM.
Программа подготовки данных UCAM содержит в себе автоматизированный технологический процесс обработки данных, таким образом, исключая трудоемкий процесс редактирования. Например: самообучаемая функция загрузки списка апертур, функции проверки для поэтапной обработки данных или мультиплицирования.
Теперь, что касается Integr8tor. Он является одним из пакетов UCAM, поставляемым в качестве опции. Integr8tor неоценимо полезен , поскольку он дает очень ясный синтаксис и правила для того, как детали проекта должны быть описаны, в том числе он проверяет правила конструирования, текстовые описания и даже аннотации - поскольку подход является однородным и четким.
Так как Integr8tor использует универсальный формат XML, выходные данные могут быть легко введены в базу данных, и это приводит к еще большим преимуществам. Он позволяет увидеть, что за продукт создан и при каких условиях. Это значит, что когда приходит запрос на , скажем, 10-слойную печатных плат, можно установить фильтр в базе данных Integr8tor для поиска аналогичного проекта и сравнить его с правилами проектирования входящего проекта. Если они схожи, то становится понятным, что производство может выполнить данный проект и можно предсказать технические проблемы, которые могут возникнуть у производителя
Теперь о новых тенденциях в производстве печатных плат и ЭМ:
- Основным трендом в нашей отрасли, конечно же, является миниатюризация, причем скорость научно -технического прогресса такова, что те, кто сегодня работает с 3-4 классом точности, завтра будут работать с 5-м – 6-м, а послезавтра - с 6-м – 7-м. Поэтому, учитывая, что в наших реалиях само техперевооружение производства тянется 1-2 года и бывает не чаще 1 раза в 5-7 лет, для того, чтобы принципы организации техперевооружения морально не устарели к моменту запуска производства , целесообразно ориентироваться не на сегодняшний уровень, а постараться спрогнозировать тренд развития на несколько лет вперед.
Кстати таким даром технического предвидения, надо отдать им должное, обладали мои учителя в ИТМ и ВТ, что позволило создать там в 90-х годах прошлого века сверх передовое производство печатных плат, многие из технических принципов которого актуальны и сегодня. Следует учесть, что оснащение производства передовой инновационной техникой позволяет существенно расширить возможности такого производства в части обеспечения технических характеристик прецизионных печатных плат и реализовывать собственные инновационные проекты на собственных производственных площадках.
В этом разделе хотелось бы обратить внимание читателя на инновационное технологическое оборудование, позволяющее существенно облегчить технологию производства прецизионных печатных плат с учетом всех требований проектирования для производства (DFM).
Каковы же особенности конструкторской подготовки производства и самого производства прецизионных печатных плат ? И возможна ли технологическая реализация постоянно ужесточающихся конструктивных требований к прецизионным печатных плат ?
При необходимости формирования прецизионных проводников и зазоров (75/75 мкм, а тем более 50/50 мкм при толщинах меди 30 и более мкм) становится актуальной проблематика технологического обеспечения малых допусков на ширины проводников и зазоров (т.е. обеспечение равномерности травления по всему рабочему полю) и возможность формирования проводников с высоким фактором травления ( 4-5 и более – т.е формирования проводников с вертикальными боковыми стенками).
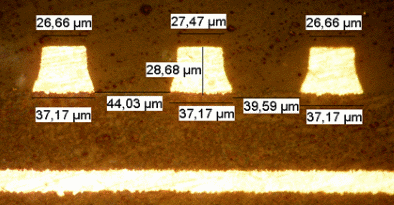
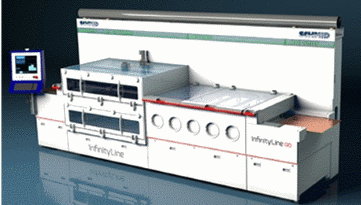
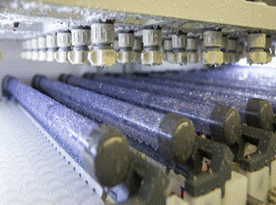
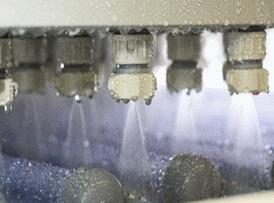
конструкция распылительных форсунок установки травления ф. Schmid.
Рис.10. Установка прецизионного травления Infinity Line с технологией NEO.
Как уже было сказано в качестве примера инновационного оборудования, решающего эти задачи, можно привести травильные машины ф. Schmid, оснащенные новыми травильными опциями (NEO- new etching options) (Рис. 10 ):
- дополнительным модулем интермиттирующего травления;
- системой вакуумного травления (Рис. 11 а);
- оптимизированной конструкцией распылительных форсунок с расширенным до 4-х бар интервалом рабочего давления (Рис. 11 б);
- обновленной системой управления динамикой потока травильного раствора;
-усовершенствованной транспортной системой.
Эти опции позволяют на горизонтальной конвеерной машине стабильно получать результат 40/40 мкм с фактором травления 5 и более. Пристыковка к этим машинам систем регенерации решает задачу обеспечения экологических проблем и замкнутого водооборота. (Рис.12.). Кроме того система регенерации позволяет в течении долгого времени поддерживать стабильные параметры травильного раствора по содержанию меди (плотности) и pH
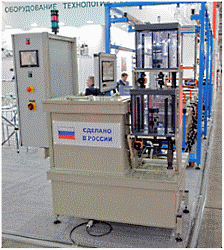
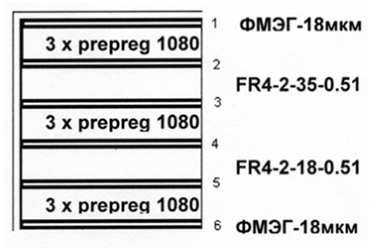
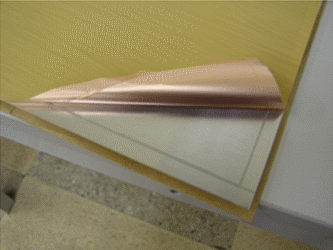
В 2018году «РТС Инжиниринг», как альтернативу установки регенерации щелочного травильного раствора ф. Меcer, презентовала на выставке ЭлектронТехЭкспо-2018 в Крокус Экспо установку регенерации собственной разработки и изготовления (Рис. 13), производительностью ок. 1кг меди в час.
При изготовлении прецизионных печатных плат ( в частности при монтаже на них прецизионных компонентов) становится актуальной проблема минимизации коробления. И конструктор должен понимать, что современное оборудование может обеспечить это только при выполнении определенных условий. Для минимизации коробления (т.е. для обеспечения технологичности сборки электронных модулей) рекомендуется при разработке использовать структуры с фольгой на наружных слоях и закладывать это в конструкторскую документацию (Рис.14). Эти структуры, в отличии от структур с ламинатом на наружных слоях, кроме того, что обладают существенно меньшей склонностью к короблению (особенно для 4-х и 6-ти слойных многослойных печатных плат), имеют ряд дополнительных преимуществ:
- экономичное использование основных и вспомогательных материалов;
- возможность использование технологии CAC (медь-алюминий-медь) (Рис. 15), позволяющую уменьшить высоту пакета в прессформе и сократить количество используемых технологических материалов;
- нет необходимости стравливания адгезивного покрытия с наружных слоев, что упрощает техпроцесс и снижает трудоемкость;
- отсутствует проблема рассовмещения слоев при прессовании 4-х слойных печатных плат.
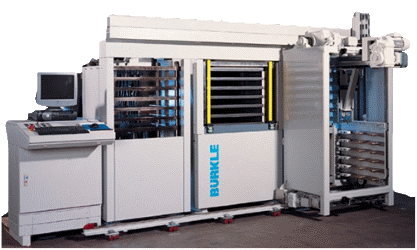
Для реализации процесса прессования с минимальным короблением РТС предлагает пресса давно и широко известной в РФ ф. Buerkle (для увеличения производительности оснащение участка может предусматривать, кроме основного «горячего» пресса, «холодный» пресс и автоматическую загрузку/выгрузку). (Рис. 16) При этом процесс наращивания производитедьности может происходить поэтапно, установкой дополнительных устройств в систему прессования.
Высокая гибкость системы позволяет конфигурировать прессовый участок с использованием ручных и автоматических загрузочно\разгрузочных устройств; различного количества холодных и горячих вакуумных прессов; различных вариантов транспортных и складских систем и другого вспомогательного оборудования в зависимости от номенклатуры изготавливаемых печатных плат и производительности.
Кроме того при производстве прецизионных печатных плат целесообразно использовать:
- сушку (в том числе вакуумную) слоев и препрега (минимизирует внутренние напряжения и коробление, что особенно важно при монтаже миниатюрных компонентов); - чистую зону на сборке пакета (нет посторонних включений внутри пакета многослойных печатных плат – имеет значение при уменьшении зазоров на проводящем рисунке) .Пресса ф. Bürkle, имея мощные плиты толщиной более 40 мм, позволяют, не деформируясь, использовать прессформы существенно меньшего размера, чем плиты пресса, что может быть актуально для производств, использующих большое разнообразие прессформ (в том числе и малых габаритов), что также снижает вероятность коробления печатных плат после прессования.
Известно, что при прессовании происходят размерные изменения. Величина размерных изменений после прессования может достигать на заготовках 500х600 мм - 0,15 – 0,2 мм.
При прессовании многослойных печатных плат (также как при прессовании ламината) происходит нагрев пакета до температуры превышающей температуру стеклования (Tg) смолы склеивающих прокладок (препрега); переход смолы в квазижидкое состояние (состояние высокой текучести).
Различные материалы, входящие в состав пакета многослойных печатных плат и имеющие различные КТР, приобретают различные размерные изменения и при остывании и затвердевании смолы препрега (переходе в состояние низкой текучести) эти размерные изменения фиксируются (и приобретают необратимый характер). Они тем больше, чем больше разнообразие, входящих в состав пакета многослойных печатных плат материалов, по КТР, толщинам и маркам ламинатов слоев, по степени заполнения слоев проводящего рисунка (соблюдения «баланса меди») и массы других конструктивных и технологических факторов.В этом случае при изготовлении прецизионных печатных плат, конечно, требуется компенсация размерных изменений.
Одной из главных задач компенсации размерных изменений является совмещение массивов отверстий и контактных площадок на наружных слоях с соблюдением требований «гарантийного пояска» (величины D-d/2), особенно на наружных слоях. Чем меньше разница между диаметром контактной площадки и диаметром сверла (D-d ), тем более требовательная печатная плата к необходимости компенсации размерных изменений для увеличения надежности и % выхода годных печатных плат.
Стандартами сильнее ограничивается смещение отверстия в сторону проводника во избежание его «подрезки». Уменьшение влияния «подрезки» проводника легко решается введением «слезок» в рисунок печатных плат ( Рис. 17.). Это существенно увеличивает процент выхода годных изделий.
Вообще эта процедура конечно должна быть выполнена конструктором на стадии проектирования. В большинстве CAD и CAM она выполняется одним «кликом». Очень рекомендую выполнять это на стадии подготовки производства, если это не сделали конструкторы-разработчики .
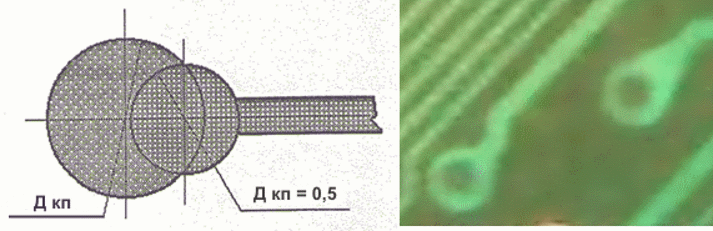
Но даже установка «слезок» не может до конца решить проблемы совмещения массивов контактных площадок и отверстий для прецизионных печатных плат, где величина (D-d )/2 может уменьшаться до 0,1-0,075 мм. Таким образом прецизионные печатные платы особенно требовательны к компенсации размерных изменений.
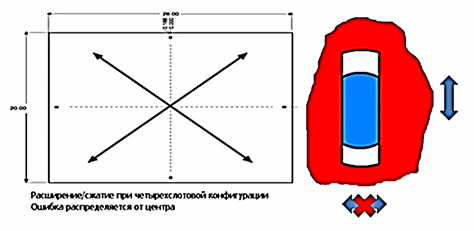
Размерные изменения сильно связаны с проектированием для производства (DFM) и зависят от соблюдения «баланса меди» ( обеспечения равномерности заполнения медью рисунка слоя) и от качества используемого препрега и ламината.
Нарушение «баланса меди» конструктором и использование в структуре многослойных печатных плат некачественных материалов может привести к существенному увеличению размерных изменений и усугубить потребность их компенсации.
Говоря о размерных изменениях, стоит разобрать существующие методы создания структуры многослойных печатных плат - PinLam и MassLam. При их использовании по разному формируются и компенсируются размерные изменения.
Благодаря слотовым отверстиям, при использовании системы PinLam деформации носят линейный характер. Слоты сформированы таким образом, что слои имеют возможность только четко направленных размерных изменений (только вдоль лысок штифтов, а не поперек).
При этом итоговые размерные изменения формируются пропорционально от центра к периферии слоя (многослойных печатных плат) , т.е. эти изменения имеют линейный характер и последующая коррекция размерных изменений после прессования производится проще и быстрее. ( Рис.18).
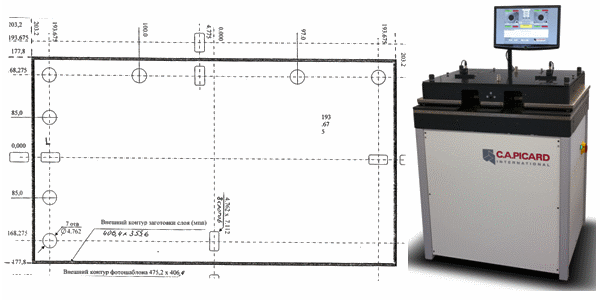
Таким образом, если процесс прессования происходит при использовании техники PinLam (прессование в прессформах с слотовыми штифтами), плата при прессовании будет иметь линейные размерные изменения. Для их коррекции достаточно 2-х (максимум 4-х) реперов по периферии, при этом для того, чтобы минимизировать смещение сверла от центров контактных площадок , достаточно одного коэффициента масштабирования для всей площади заготовки.
Когда же плата имеет нелинейные искажения (при использовании технологии MassLam - прессование в бесштифтовой прессформе механически зафиксированного по периферии пакета многослойных печатных плат), линейной оптимизации будет уже недостаточно для минимизации смещения сверла от центров контактной площадки . В этом случае необходимо разбить площадь заготовки на несколько секций (фрагментов).
При проектировании заготовки для каждого фрагмента необходимо предусмотреть реперные точки и при анализе коэффициенты масштабирования рисунка будут заданы индивидуально для каждого фрагмента.
Не забудьте , что после введения коэффициентов масштабирования на наружных слоях печатных плат, необходимо соответствующее масштабирование вводить при формировании слоев паяльной маски (ПМ), а иногда и маркировки.
Для выполнения операции компенсирования размерных изменений после прессования РТС Инжиниринг предлагает рентгеновские станки Inspecta ф. Pluritec, которые могут компенсировать как линейные так и нелинейные размерные изменения. (Рис. 20.).
Уникальность станков заключается в том, что они могут быть использованы для решения широкого круга производственных задач :
- сверления только базовых отверстий с компенсацией размерных изменений имеющих линейный характер (по 2-4-м реперным точкам с коэффициентом масштабирования - единым для всей площади );
- сверления с рентгеновской корректировкой и фрезерования за один «установ» ;
- оптимизации по множеству мишеней на каждом фрагменте многослойной платы для компенсации размерных изменений, носящих нелинейный характер (получающихся по технологии MassLam)
Использование патентованного акрилового стола на станках ф. Pluritec также следует отнести к уникальным свойствам так, как он позволяет располагать реперы – мишени практически в любом месте по площади заготовки, что расширяет возможности конструирования и подготовки производства с точки зрения требований DFM ;
- опционно станки могут быть использованы для сверления и фрезерования на заданную глубину контактным и бесконтактным способом (актуально для формирования глухих отверстий и изготовления гибко-жестких печатных плат), а также для техники «обратного сверления» (backdrilling) на СВЧ платах.
Патентованный акриловый стол станков, позволяет располагать реперы (для размерной компенсации после прессования по методу Masslam) практически по всей площади рабочего поля станков.
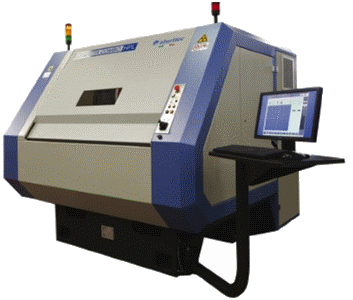

Следует отметить, что в Европе контрактные производства, как правило, оснащаются оборудованием и PinLam, и Masslam . РТС может предложить универсальный комплект такого оборудования с использованием установок ф. Picard и ф. Piergiacomi. (Рис. 21.). Последнее время в технической литературе появились интересные сообщения о гибридной технологии, совмещающей в себе элементы PinLam, и Masslam и успешно используемой для изготовления сверхпрецизионных печатных плат (HDI в терминологии, применяемой за рубежом).