- Главная
- Оборудование для печатных плат
- Оборудование для поверхностного монтажа
- Технологии производства плат и поверхностного монтажа
- Инструмент для печатных плат и Запасные части
- Материалы и Химикаты для печатных плат и поверхностного монтажа
- Гальваническое оборудование
- Лабораторное и аналитическое оборудование
- Сервис и техническое обслуживание
- Как нас найти
- Начало раздела
- Главный технолог
- Технологии производства
- Консультации
- Контакты
Припойная паста: основные характеристики материала / корреляция поверхностных характеристик
Нилеш Бадве, Шунфэн Ченг, Шриниваса Аравамудхан, Мукул Ренавикар.Корпорация Intel; Хиллсборо, Орегон, США
glemaster@creativeelectron.com
Авторский перевод ЛЕЙТЕСА ИЛЬИ, гл.технолога ООО РТС Инжиниринг.
АННОТАЦИЯ
Агрессивные форм-факторы, уменьшенный шаг, более тонкие корпуса и большее отношение размера корпуса к кристаллу приводят к более высокой деформации во время оплавления узлов поверхностного монтажа. Становится все труднее устранять дефекты узлов поверхностного монтажа, вызванные короблением, а именно: отсутствие смачивания (NWO), «голова на подушке» (HoP) и перемычки припоя (SB). Мы изучили несколько составов пасты с помощью ударных испытаний узлов поверхностного монтажа. Лабораторные характеристики также использовались для установления корреляции между характеристиками поверхностного монтажа и основными свойствами паяльных паст.
Мы обнаружили, что отсутствие смачивания (NWO) и «голова на подушке» (HoP) конкурируют друг с другом, имея корреляцию с активностью флюса используемого для очистки окислов на поверхности Cu. Риск образования перемычек (SB) коррелировал с высокотемпературной вязкостью, что указывает на дефект, вызванный реологией пасты. Показатели пригодности пасты для печати также показали хорошую корреляцию с тиксотропным индексом. Эти знания будут чрезвычайно полезны для разработки паяльных паст следующего поколения для устранения дефектов, вызванных короблением.
ВВЕДЕНИЕ
Полупроводниковая промышленность в настоящее время расширяет границы закона Мура, размещая все больше транзисторов на кристалле. Это приводит к более жестким требованиям к технологии корпусирования с точки зрения геометрических форм-факторов, таких как более тонкие корпуса, более тонкие кристаллы, большее отношение размера корпуса к размеру кристалла и меньший шаг пайки выводов.
Для корпусов с матрицей шариковых выводов внизу (Flip Chip Ball Grid Array (FCBGA)) все эти тенденции приводят к значительному увеличению коробления корпуса во время пайки оплавлением в технологии поверхностного монтажа из-за несоответствия коэффициента теплового расширения (КТР) кремниевого кристалла и подложки корпуса. Эта высокая деформация во время оплавления в технологии поверхностного монтажа SMT приводит к многочисленным дефектам в паяных соединениях межсоединений второго уровня (SLI). Эти дефекты включают в себя обрыв из-за несмачивания (NWO), «голова на подушке» (HoP) и перемычки припоя (SB).
Поскольку корпус нагревается в процессе бесвинцового оплавления до температуры 250°C для типичных составов паст типа Sn-Ag-Cu (SAC), степень коробления корпуса значительно возрастает. Это приводит к тому, что шарик припоя корпуса отходит от слоя паяльной пасты на контактной площадке печатной платы (ПП) в определенных областях матрицы шариков, а в других областях шарик припоя сжимается на контактной площадке печатной платы. Припои на основе SAC плавятся при температуре ~217-220°C в зависимости от содержания Ag и Cu. Если корпус значительно деформируется во время расплавления припоя, области сжатия заканчиваются дефектами перемычек припоя.
Если шарики припоя BGA соприкасаются с паяльной пастой, нанесенной на контактные площадки на печатной плате, существует вероятность того, что паста прилипнет к шарику BGA, пока корпус отходит от печатной платы во время оплавления. Это может привести к образованию дефектов связанных с несмачиванием, как показано на рисунке 1. Амир др. [1] обнаружили, что активность флюса измеряемая например через время смачивания и липкость паяльной пасты влияет на сопротивление дефектов несмачивания (NWO) при использовании ограниченного количества (3) паяльных паст.
Если паяльная паста не прилипает к шарику припоя BGA, а шарик отходит от паяльной пасты, нанесенной на контактную площадку, флюс паяльной пасты не сможет очистить оксид на поверхности шарика BGA, чтобы сформировать соединение между припоя из пасты и шарика BGA, что приведёт к дефектам типа «голова на подушке» (HoP), как также показано на рисунке 1. Амир др. [2] обнаружили также корреляцию вязкости и pH-стабильности паст с риском образования дефектов типа «голова на подушке» (HoP).
Однако это исследование было ограничено только двумя пастами. Амир также обнаружил, что скорость образования шариков припоя коррелирует с появлением дефектов типа «голова на подушке» (HoP), что указывает на механизм возникновения этого дефекта, основанный на активности флюса.
В области под корпусом флюс вытекает из под основания BGA во время начальной стадии повышения температуры процесса оплавления и иногда сливается с флюсом, вытекающим из под соседнего BGA. Этот поток флюса перед расплавлением паяльной пасты обеспечивает путь для формирования перемычки после того, как температура оплавления превысит температуру плавления припоя, как показано на рисунке 1.
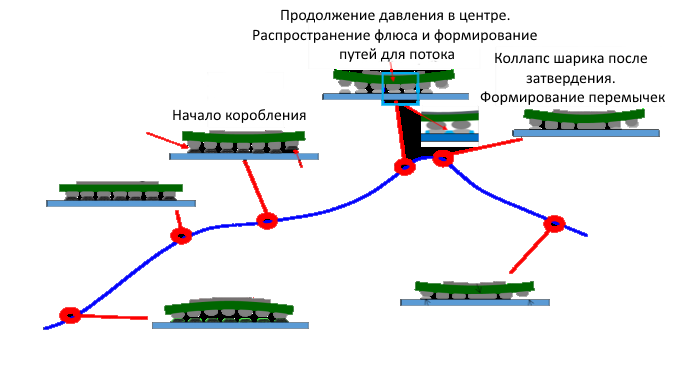
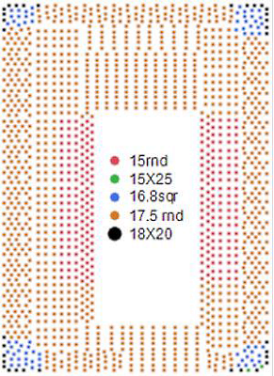
Всех этих потенциальных дефектов поверхностного монтажа, вызванных короблением, можно избежать, изменив объем пасты, на контактных площадках печатной платы, в областях массива контактных площадок, подверженных особенно высокому риску. Уменьшение апертуры трафарета в областях с высоким риском возникновения перемычек припоя может помочь уменьшить количество перемычек припоя за счет уменьшения объема паяльной пасты, нанесенной на контактные площадки печатной платы.
Увеличение объема пасты за счет большего отверстия трафарета поможет поддерживать постоянный контакт пасты с BGA и контактной площадкой во время оплавления. Это помогает устранить дефекты NWO и HoP в областях, где подложка корпуса максимально деформируется во время пайки оплавлением. Такие гибридные конструкции апертур трафарета, как показано на рисунке 2, могут помочь устранить большинство дефектов.
Дизайн КП также может помочь снизить риск возникновение перемычек. Например, на рис. 3 показаны две конструкции с одним и тем же расположением выводов. Для конструкции (а) легче формировать пути флюса/припоя, тогда как в конструкции (б) есть место для удержания флюса вокруг контактной площадки, что позволяет избежать флюсовых мостиков в период нарастания и, следовательно, припоя после оплавления.
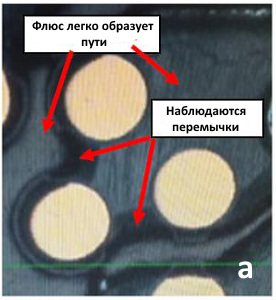
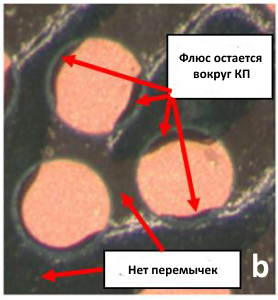
Рис. 3. Конструкция контактной площадки влияет на наличие флюса между контактными площадками припоя, чтобы обеспечить путь для припоя к перемычке
Оптимизация, показанная на рисунке 3 выше, способна устранить большинство дефектов, вызванных короблением. Тем не менее, некоторые корпуса по-прежнему демонстрируют чрезмерное коробление для конкретных BGA. На рис. 4 показаны встречные два корпуса одного и того же дизайна FCBGA. Большинство таких корпусов имеет коробление из-за высокой температуры, как показано на Рис. 4 (а), где красный цвет означает, область изгиба вверх. Тем не менее, на некоторых корпусах видно искривление вниз, как показано на рис. 4 (b), где синим цветом обозначена область, изгибающаяся вниз.
Создать единый дизайн трафарета, подходящий для обоих условий коробления, сложно. Если трафарет разработан на основе формы деформации угла вверх, больше пасты будет наноситься на угловые КП и меньше пасты в центр. Это может привести к дефектам NWO и HoP в центре и перемычкам припоя в углу корпуса. Паста, которая более устойчива к этим дефектам, в таких случаях обеспечит дополнительный запас для минимизации дефектов, тем самым улучшив выход SMT.
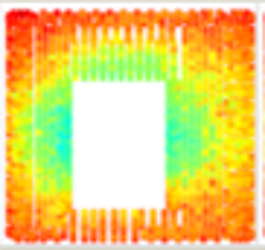
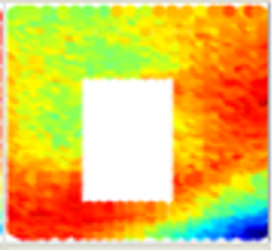
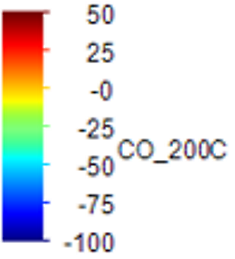
Рис. 4. Две разные упаковки из одной партии со значительно отличающимся профилем коробления при высокой температуре (200°C). Масштабная линейка показывает значения коробления в мкм
В текущем исследовании несколько паяльных паст оценивались с использованием ударных испытаний SMT, специально разработанных для форсирования проявления дефектов каждого типа. Фундаментальные свойства этих паст также были определены с помощью исследований характеристик на лабораторном уровне, чтобы установить, существует ли какая-либо корреляция между данными лабораторного уровня и характеристиками пайки оплавлением, количественно определяемыми выходом паяных соединений после пайки оплавлением.
ЭКСПЕРИМЕНТАЛЬНЫЕ ДЕТАЛИ
Материалы
Было получено восемь различных материалов для паяльной пасты от нескольких поставщиков. Все паяльные пасты содержали сплав SAC305 с припоем типа 4. Основным отличием протестированных паяльных паст был химический состав флюса. Флюс в паяльной пасте имеет сложный состав, обычно состоящий из канифоли/смолы, растворителя, активатора и некоторых реологических добавок [3, 4]. При повышении температуры в процессе оплавления растворитель во флюсе начинает испаряться, а активатор удаляет оксид с припоя и растворяет окисел на контактных площадках. Канифоль/смола размягчаются и разжижаются, что способствует смачиванию расплавленного припоя на поверхности контактной площадки и формированию паяного соединения [5, 6].
Некоторые паяльные пасты содержали флюсы, с галогенсодержащими соединениями. Некоторые содержали очень небольшое количество галогенов и соответствовали определению Международной электрохимической комиссии (IEC) о безгалогенности, а некоторые не содержали галогенов совсем. Ожидается, что галогены в флюсе паяльной пасты улучшат активность пасты. Уровень содержания галогенов в 8 паяльных пастах, оцененных в этом исследовании, указан в таблице 1.
Все 8 паст были протестированы на риск образования мостиков припоя. Ограниченные ресурсы ограничили возможность исследования ударными тестами NWO и HoP 6 и 5 пастами соответственно.
А | Ноль галогенов |
В | Ноль галогенов |
С | Ноль галогенов |
D | Безгалогеновые по IEC |
E | Безгалогеновые по IEC |
F | Безгалогеновые по IEC |
G | Содержащие галогены |
H | Содержащие галогены |
Ударные испытания NWO.
Условия ударных испытаний NWO были созданы на образцах с уменьшением объема пасты за счет конструкции апертуры трафарета. Это привело к низкому объему флюса для очистки оксида на поверхности контактной площадки печатной платы, что привело к дефектам NWO. Корпуса FCBGA имели размер 42x28 мм с шагом шариков 0,65 мм и размещались на печатной плате толщиной 0,8 мм. Специальный трафарет с апертурой меньше, чем обычно, был разработан для увеличения количества дефектов NWO.
Корпуса были выбраны с одинаковым диапазоном коробления для всех исследований, чтобы уменьшить влияние коробления как переменной на результаты. Оплавление SMT проводили на воздухе с пиковой температурой 245°C. Три этапа с 12 образцами были проведены в одинаковых условиях для обеспечения воспроизводимости. Данные об объеме пасты на выводе отслеживались и нормализовались, чтобы смягчить влияние дисперсии печати. Интенсивность отказов на уровне выводов измерялась с помощью процесса анализа отказов Dye-n-Pry (Dye-n-Pry FA).
HoP ударный тест.
Для ударных испытаний HoP использовались корпуса FCBGA с размером 42x24 мм, шагом шариков 0,65 мм и толщиной платы 0,8 мм. Для создания условий ударных испытаний корпуса нагревались при 125°С в течение 48 часов. Это обеспечивало образование толстого оксида на поверхности шарика припоя. Кроме того, был разработан более тонкий трафарет с меньшей апертурой для нанесения небольшого объема пасты с малой высотой печати. Это было сделано для создания дефицита флюса для очистки поверхности окисла.
Корпуса были выбраны с одинаковым диапазоном коробления для всех исследований, чтобы уменьшить влияние этой переменной. Оплавление проводили на воздухе с пиковой температурой 245°C. Тест был проведен дважды, чтобы обеспечить воспроизводимость с 16-ю корпусами. Данные об объеме пасты на уровне вывода отслеживались, чтобы смягчить влияние изменчивости в процессе печати. Анализ дефектов HoP был выполнен с использованием процесса Dye-n-Pry FA, в котором для каждой пасты измерялась частота отказов на уровне вывода
Ударные испытания перемычек.
Перемычка припоя обычно образуется, когда паяные соединения сжимаются во время оплавления, когда припой все еще находится в расплавленном состоянии. Специальное приспособление использовалось для создания условий ударных испытаний, чтобы увеличить количество перемычек. В этом приспособлении, как показано на рисунке 5 (а), использовались грузы (30 г) для сжатия центра корпуса во время оплавления. Само приспособление весило 5 г, что приводило к силе ~ 35 г воздействующей на верхнюю часть каждого корпуса.
Корпуса представляли собой корпуса BGA размером 20,5x16,5 мм с шагом шариков 0,4 мм на печатной плате толщиной 0,7 мм. Корпуса были выбраны с одинаковым диапазоном коробления для всех исследований, чтобы уменьшить влияние этой переменной. Оплавление SMT проводили в среде N2 с пиковой температурой 245°C. Данные были собраны по нескольким сборкам с 12 корпусами на сборку. Данные об объеме пасты на уровне вывода отслеживались и нормализовались, чтобы смягчить влияние изменчивости в процессе печати. Уровень дефектов типа перемычек определяли с помощью рентгеноструктурного анализа, как показано на рисунке 5 (b).
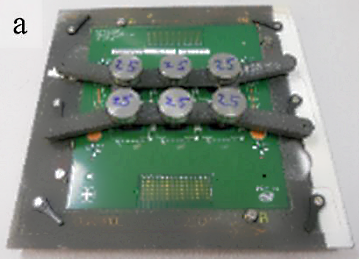
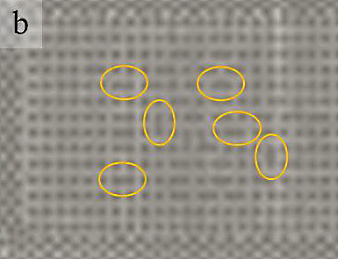
Распространение припоя на купоне с органической защите меди (CuOSP)
Зона | Время (мин:сек) | Температура (С) |
---|---|---|
1 | 0:45 | 145 |
2 | 0:45 | 165 |
3 | 0:45 | 210 |
4 | 2:15 | 245 |
5 | 2:15 | Зона охлаждения |
Растекание припоя, а также растекание флюса на купоне CuOSP измеряли под микроскопом. Два показания на растекание припоя были сняты как для припоя, так и для растекания флюса, как показано на Рис. 6.
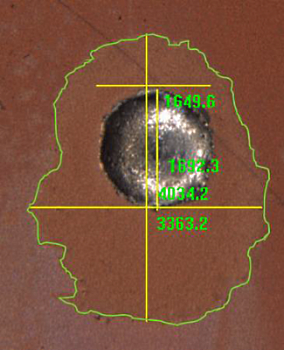
Вязкость
Вязкость паяльной пасты измеряли с помощью реометра Stresstech с пластинами диаметром 40 мм при зазоре 0,5 мм. Для измерения вязкости в зависимости от температуры от комнатной температуры до 90°C выполняли сканированием с динамическим линейным изменением температуры со скоростью линейного изменения 3,5°C/мин.
Липкость
Липкость паяльной пасты измеряли при комнатной температуре и при 50°C с помощью тестера липкости Malcom TK-1 с зондом диаметром 5,1 мм. Паста печаталась с помощью трафарета 0,25 мм на матовом стекле, нагретом на горячей пластине. Липкость измеряли при времени прессования 5 секунд, предварительной нагрузке 300 г и скорости 2,5 мм/сек в соответствии со стандартом IPC [7].
Тиксотропный индекс
Для паяльных паст был проведен анализ скорости сдвига для измерения вязкости при различных скоростях сдвига в диапазоне от 0,1/с до 5/с при 25°C на реометре AR-G2. Тиксотропный индекс рассчитывали, взяв коэффициенты вязкости при скоростях сдвига 0,13/с и 1,3/с.
РЕЗУЛЬТАТЫ И ОБСУЖДЕНИЕ
Несмачивание (NWO)
Частота дефектов NWO на уровне выводов была рассчитана на основе процесса Dye-n-Pry с использованием уравнения (1).
𝑁𝑊𝑂 𝑅𝑎𝑡𝑒 =( 𝑁𝑜.𝑜𝑓 𝑠𝑜𝑙𝑑𝑒𝑟 𝑗𝑜𝑖𝑛𝑡𝑠 𝑤𝑖𝑡ℎ 𝑁𝑊𝑂/ 𝑇𝑜𝑡𝑎𝑙 𝑛𝑜.𝑜𝑓 𝑠𝑜𝑙𝑑𝑒𝑟 𝑗𝑜𝑖𝑛𝑡𝑠) × 100 (1).
Частота дефектов типа 𝑁𝑊𝑂 = (Числу паяных соединений с 𝑁𝑊𝑂/ Общее кол-во паяных соединений)× 100.
Значительная разница наблюдалась в частоте дефектов NWO между различными пастами. Коэффициент NWO варьировался от 0,2% до 33% для разных паст. Корреляции между содержанием галогенов в пасте и процентом дефектов NWO не наблюдалось. Однако между растеканием припоя по купонам CuOSP и скоростью NWO наблюдалась сильная корреляция, как показано на рисунке 7. Если флюс из пасты может легко очистить OSP на поверхности образца, это приведет к растеканию припоя большого диаметра. Чтобы избежать дефектов NWO, флюс должен выполнять свое флюсующее действие, растворяя OSP и удаляя оксиды меди с поверхности контактной площадки печатной платы до того, как паяльная паста отделится от контактной площадки, чтобы обеспечить большее сцепление пасты с контактной площадкой печатной платы чем с шариком припоя BGA.
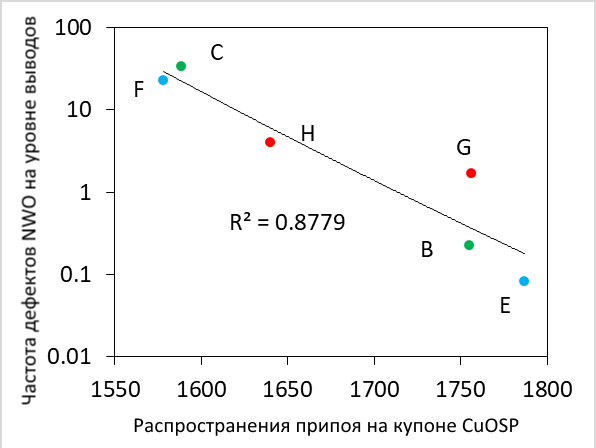
Как показано на Рисунке 8, пара протестированных паяльных паст, C и F, имела самый высокий уровень дефектов NWO, а также наибольшее уменьшение липкости, как и предсказывали Амир др. [1]. Пасты E и B с уменьшением ~ 25 % и 15 % соответственно были лучшими пастами для минимизации дефектов NWO. Пасты G и H имели минимальное уменьшение липкости, однако демонстрировали дефекты NWO на более высоком уровне, чем пасты G и H.
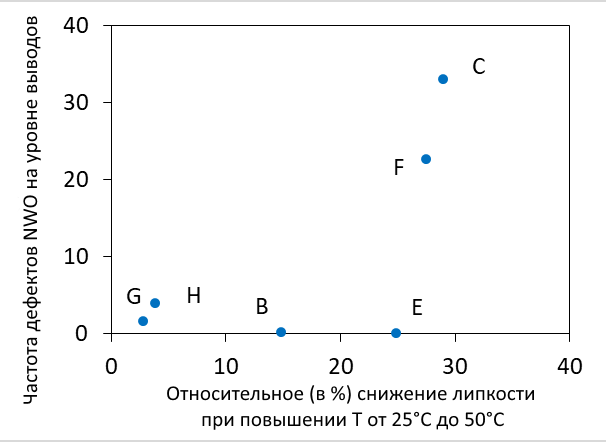
«Голова на подушке» (HoP)
Подобно NWO, скорость HoP также рассчитывалась на уровне выводов на основе процесса Dye-n-Pry с использованием уравнения (2).
𝐻𝑜𝑃 𝑅𝑎𝑡𝑒 = (𝑁𝑜.𝑜𝑓 𝑠𝑜𝑙𝑑𝑒𝑟 𝑗𝑜𝑖𝑛𝑡𝑠 𝑤𝑖𝑡ℎ 𝐻𝑜𝑃/𝑇𝑜𝑡𝑎𝑙 𝑛𝑜.𝑜𝑓 𝑠𝑜𝑙𝑑𝑒𝑟 𝑗𝑜𝑖𝑛𝑡𝑠)× 100 (2)
Частота дефектов типа 𝐻𝑜𝑃 = (Числу паяных соединений с 𝐻𝑜𝑃 / Общее кол-во паяных соединений)× 100.
Общий показатель HoP варьировался от 0,2% до 2,8%, как показано на рис.9.
Рис. 9. Здесь наблюдается отрицательная корреляция между распространением припоя на купоне CuOSP и сопротивлением HoP пасты. Это указывает на потенциальный механизм, при котором активные компоненты флюса этих паст расходуются на очистку ОСП на контактной площадки и не могут очистить оксид на поверхности BGA.
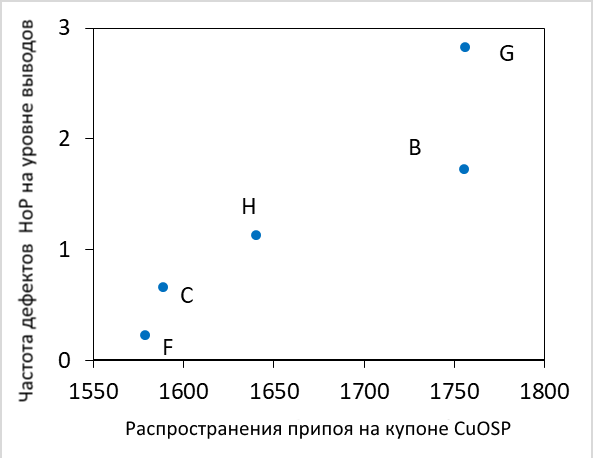
Перемычки припоя
Изменение коробления от платы к плате невелико и не учитывалось.
Однако из-за изменчивости, присущей процессу печати пасты, фактические объемы пасты, на контактных площадках печатных плат разные для каждого корпуса. На рис. 10 показано влияние объема печати на формирование перемычек. Объем пасты B имел значительное влияние на формирование перемычек. Это влияние затруднило оценку производительности пасты путем сравнения абсолютного количества перемычек без учета объема пасты. Высокое количество дефектов SB могло возникнуть из-за чрезмерного количества пасты, а не из-за различных свойств паст. На рис. 10 представлена диаграмма изменчивости объема пасты (Paste Volume) % для двух разных паст на двух разных платах. Красные точки обозначают объем пасты для выводов с перемычками. В других местах нет перемычек.
Для учета этого несоответствия используется метод взвешивания, который разработан для уменьшения воздействия объема пасты, чтобы можно было сравнить характеристики паст. Вставить объем пасты в процентах к объему апертуры трафарета измеряется с помощью инструмента для проверки пасты. При методе взвешивания объем пасты в процентах нормализован к диапазону (0,1) по уравнению (3), где - Norm_PasteVol — нормализованный объем пасты в процентах;
- PinperVol — объем пасты в процентах для для каждого вывода, а - MinPinperVol и MaxPinperVol - являются минимальным и максимальным процентным объемом пасты.Вес для каждого вывода с перемычкой, Wgted_PasteVol, рассчитывается по уравнению (4), которое обратно нормализованному объему пасты. Паста большей высоты будет иметь меньший вес. Сумма Wgted_PasteVol для всех выводов с перемычками в одном корпусе используется как взвешенная метрика (Weighted_SB_Risk) в уравнении (5)) для корпуса.
𝑁𝑜𝑟𝑚_𝑃𝑎𝑠𝑡𝑒𝑉𝑜𝑙 =𝑃𝑖𝑛𝑃𝑒𝑟𝑉𝑜𝑙−𝑀𝑖𝑛𝑃𝑖𝑛𝑝𝑒𝑟𝑉𝑜𝑙/𝑀𝑎𝑥𝑃𝑖𝑛𝑝𝑒𝑟𝑉𝑜𝑙−𝑀𝑖𝑛𝑃𝑖𝑛𝑝𝑒𝑟𝑉𝑜𝑙(3)
𝑊𝑔𝑡𝑒𝑑𝑃𝑎𝑠𝑡𝑒𝑉𝑜𝑙 =1/𝑁𝑜𝑟𝑚𝑃𝑎𝑠𝑡𝑒𝑉𝑜𝑙(4)
𝑊𝑒𝑖𝑔ℎ𝑡𝑒𝑑 𝑆𝐵 𝑅𝑖𝑠𝑘 = 𝑆𝑢𝑚 (𝑊𝑔𝑡𝑒𝑑𝑃𝑎𝑠𝑡𝑒𝑉𝑜𝑙 𝑓𝑜𝑟 𝑎𝑙𝑙 𝑆𝐵𝑒𝑑 𝑃𝑖𝑛𝑠 𝑜𝑓𝑎 𝑝𝑎𝑐𝑘𝑎𝑔𝑒) (5)
Рис. 11 иллюстрирует результаты взвешенного риска возникновения перемычек и коррелирует с вязкостью пасты при высоких температурах (90°С). Это указывает на то, что вязкость пасты падает ниже ~ 15 Па-с при 90°C, риск образования перемычек при оплавлении значительно увеличивается.
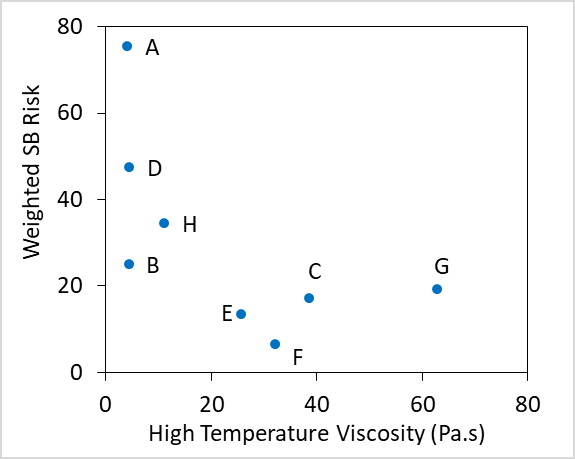
Аналогичный взвешенный подход к риску для дефектов HoP и NWO был исследован. Однако, поскольку испытание на растекание припоя CuOSP также включает в себя печать пасты, на результаты взвешенного подхода будут влиять объемы печати пасты для лабораторного уровня тестирования. Удивительно, но подход взвешенного риска не существенно влияет на результаты корреляции HoP и NWO.
Оплавление [8] при более высоких температурах от 180°C.до 205°C, например, также оценивалась. Не наблюдалась корреляция между горячим спадом и результатами ударного теста на перемычки для паст.
Производительность печати.
Стабильная производительность печати является ключевым аспектом для паяльной пасты, поскольку она существенно влияет на выход паяных соединений и качество после оплавления. Поэтому было проведено исследование пригодности к печати для ударного теста NWO. Соотношение площади апертуры трафарета для этого конкретного теста составило 0,60, что является более агрессивным, чем отраслевой стандарт - 0,66 для типовых паст T4. Технологическая способность (Cp) для печати пастой показала хорошую корреляцию с тиксотропным индексом паст, как показано на рисунке 12.
Более высокий тиксотропный индекс привел к более высокому Cp, т.е. лучшей эффективности печати. Поскольку тиксотропный индекс представляет собой отношение вязкости при низкой скорости сдвига к вязкости при высокой скорости сдвига, более высокий тиксотропный индекс указывает на истончение при сдвиге или относительно большее падение вязкости при высоких скоростях сдвига. Это будет означать относительно более низкую вязкость паяльной пасты во время сдвига пасты ракелем, чтобы обеспечить максимальное проникновение пасты в отверстия трафарета. После нанесения пасты с относительно низкой вязкостью при высокой скорости сдвига это также поможет во время отрыва трафарета, обеспечивая лучший перенос пасты на плату и меньшее прилипание к трафарету.
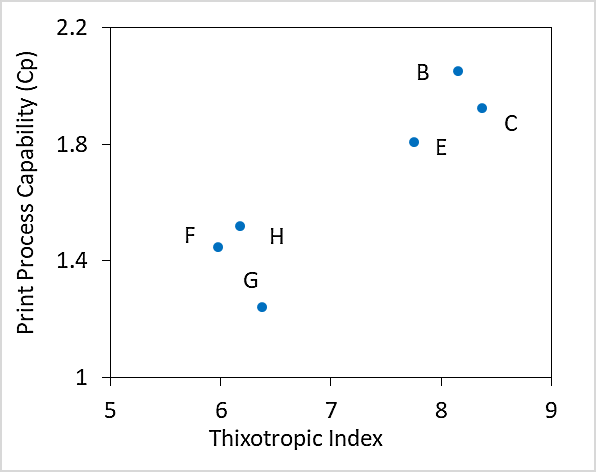
ВЫВОДЫ
Дефекты паяных соединений, вызванные короблением корпуса, можно уменьшить за счет конструкции материала паяльной пасты. Было обнаружено, что способность паяльной пасты очищать поверхность от органической защиты влияет на устойчивость пасты к NWO и HoP. Если активность паяльной пасты срабатывает раньше для очистки поверхности CuOSP, это сводит к минимуму риск NWO за счет раннего образования интерметаллических соединений на поверхности контактной площадки. Однако это снижает активность пасты для дальнейшей очистки от оксидов припоя, что увеличивает риск возникновения HoP. Этот аспект паяльной пасты необходимо оптимизировать, чтобы уменьшить дефекты HoP и NWO до приемлемого уровня. Лю и др. [9] предложили два разных метода, а именно: «маленькая точечная паста» и «шарик на пасте» для оценки устойчивости пасты к HoP.
Скальцо [10] предложил тест на схватывание для изучения термостойкости пасты. Мы считаем, что можно использовать дополнительные тесты для оценки риска HoP/NWO от паяльных паст. Снижение липкости, как и предсказывали Амир др. [1] не показало такой сильной корреляции с характеристиками NWO паст, как растекание припоя по купонам CuOSP. Было замечено, что частота дефектов типа перемычек для некоторых паст хорошо коррелирует с высокотемпературной вязкостью. Как только вязкость падает, флюс из пасты может легко вытекать. Это в конечном итоге обеспечивает путь для миграции расплавленного припоя с одной площадки печатной платы на соседнюю площадку во время оплавления, тем самым увеличивая риск образования перемычек. Высокий тиксотропный индекс свидетельствует о хорошей печати паяльных паст.
В целом не наблюдалось корреляции между содержанием галогенов в паяльных пастах и риском образования в них дефектов NWO или HoP. Это указывает на то, что смолы, кислоты и амины в пасте оказывают большее влияние на активность, чем содержание галогенов.
Результаты этого исследования будут использованы для разработки паяльной пасты следующего поколения у различных поставщиков пасты. Они также могут использоваться производителями собраных плат (OEM/ODM) для оценки уровня риска для различных паст образования различных типов дефектов и для проверки качества различных партий материала.
Благодарность
Авторы хотели бы поблагодарить доктора Джинлин Ван и Питера Маккенну за поддержку в характеристиках лабораторного уровня. Авторы также благодарят доктора Райо Аспандиара за помощь в редактировании рукописи.
ЛИТЕРАТУРА
1. Амир, Дуди, Сатьяджит Валвадкар, Шриниваса Аравамудхан и Лилия Мэй. «Проблемы дефектов BGA типа несмачивания». Материалы международной конференции SMTA. 2012.
2. Амир, Дуди, Райо Аспандиар, Скотт Баттарс, Вей Чин и Парамджит Гилл. «Режимы отказа SMT с «головой на подушке»». Материалы международной конференции SMTA (2009 г., стр. 409-421.
3. Индиум, «Понимание химии флюса». Доступно в интернете:documents.indium.com/qdynamo/download.php?docid=296.
4. Ленц, Тони и Ф. К. Т. Сборка. «Рассеивание «черной магии» паяльной пасты». Материалы конференции IPC Apex Expo, 2015 г.
5. Д. Балух и Г. Миноуг, «Основы технологии паяльной пасты», Материалы международной конференции Global SMT & Packaging, декабрь 2017 г. Доступно в Интернете: https://www.smtnet.com/library/files/upload/fundamentals_of_solder_paste_technology.pdf
6. Ито М. Общие сведения о паяльной пасте. Технический отчет, KOKI Company Limited, Токио, Япония, 1999 г.
7. IPC-TM-650, пункт 2.4.44 «Паяльная паста — испытание на липкость» Доступно на сайте: https://www.ipc.org/TM/2.4.44.pdf
8. IPC-TM-650, пункт 2.4.35, «Испытание паяльной пасты на осадку». Доступно в Интернете: https://www.ipc.org/TM/2.4.35.pdf.
9. Лю, Ян, Памела Фиакко и Нин-Ченг Ли. «Тестирование и профилактика от возникновения дефекта типа «голова на подушке»». Материалы международной конференции SMTA, 14–18 октября 2018 г., Роузмонт, Иллинойс, США, Конференция по электронным компонентам и технологиям (ECTC), IEEE, 2010 г., стр. 451-455.
10. Бат, Джасбир, Роберто Гарсия, Нориёси Учида, Хадзиме Такахаши, Гордон Кларк и Манабу Ито. «Исследование и разработка оловянно-свинцовых и бессвинцовых паяльных паст для уменьшения дефектов пайки компонентов в виде «головы на подушке»». Материалы международной конференции Global SMT & Packaging, Том 9, вып. 12 (2009): 10-16.