- Главная
- Оборудование для печатных плат
- Оборудование для поверхностного монтажа
- Технологии производства плат и поверхностного монтажа
- Инструмент для печатных плат и Запасные части
- Материалы и Химикаты для печатных плат и поверхностного монтажа
- Гальваническое оборудование
- Лабораторное и аналитическое оборудование
- Сервис и техническое обслуживание
- Как нас найти
- Начало раздела
- Главный технолог
- Технологии производства
- Консультации
- Контакты
Как рентгеновские технологии улучшают процесс сборки электроники
Гриффин Лемастер и Билл Кардосо, доктор философии.Креатив Электрон, Инк.; Сан-Маркос, Калифорния, США.
glemaster@creativeelectron.com
Авторский перевод ЛЕЙТЕСА ИЛЬИ, гл.технолога ООО РТС Инжиниринг.
АННОТАЦИЯ
В 1895 году Вильгельм Рентген открыл таинственный свет, который позволял ему видеть сквозь вещи, и назвал его рентгеновскими лучами. С тех пор рентгеновские лучи нашли широкое применение в процессе сборки электроники. Вместо «глубокого погружения» в один аспект рентгеновского контроля, в этой статье мы рассмотрим широкий спектр приложений:
- проверка электронных компонентов;
- проверка дефектов в режиме реального времени;
- обнаружение подделок;
- подсчет компонентов и выбор материалов;
- понимание механизма работы рентгеновского контроля;
- 2D, 2.5D и 3D рентгеновский контроль;
- поры, перемычки и отказы типа «голова на подушке» в компонентах с выводами вниз;
- конструирование для производства (DFM) и конструирование для рентгенографии (DFXI);
- искусственный интеллект.
Мы также обсудим, как искусственный интеллект (ИИ) меняет наши представления о рентгеновском контроле. То, о чем мы даже не мечтали всего несколько лет назад, теперь стало реальностью благодаря объединению ИИ и рентгеновского контроля. Кроме того, мы покажем вам серию реальных случаев того, как наша команда ученых, занимающихся ИИ, использует ИИ для решения самых сложных задач рентгеновского контроля. И помимо рентгеновского контроля, мы рассмотрим, как ИИ навсегда меняет способ производства и проверки чего-либо.
ВВЕДЕНИЕ
Рентгеновский контроль электронных компонентов в настоящее время является стандартной практикой для любой компании, работающей в электронной промышленности. Наиболее распространенные области применения включают проверку процессов, обеспечение качества и анализ отказов. Рентгеновский контроль достаточно универсален, чтобы пользователь мог выполнять все эти функции с помощью одного и того же инструмента. Следующая информация описывает многие проблемы, стоящие перед электронной промышленностью, и то, как рентгеновские лучи могут обеспечить их решение.
ПРОВЕРКА ЭЛЕКТРОННЫХ КОМПОНЕНТОВ (Принципы рентгенологического контроля).
Разрушающее тестирование хорошо работает во многих приложениях, но требует времени, труда и сложных инструментов. Электронные компоненты часто настолько малы, что любой деструктивный метод проверки может повредить то, что необходимо проверить. Неразрушающий контроль (NDT) — это любой анализ, выполняемый на компоненте без его повреждения. Рентген идеально подходит для всех, кто работает в области неразрушающего контроля. Он позволяет пользователям визуально проверять продукты, которые скрыты, заключены в кожух или иным образом недоступны для других средств контроля.
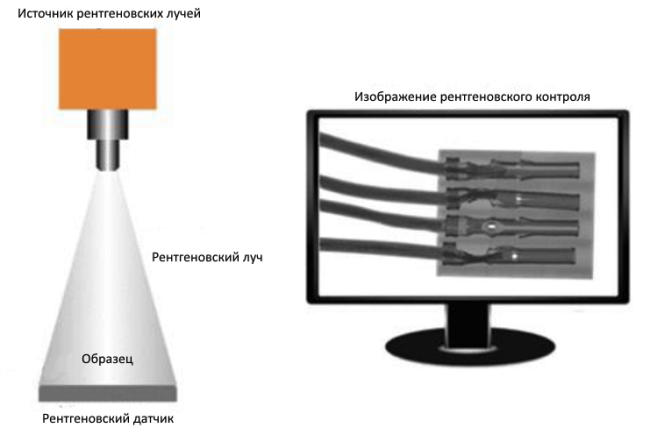
ПРОВЕРКА ДЕФЕКТОВ В РЕАЛЬНОМ ВРЕМЕНИ
Для производства готовой печатной платы (ПП) необходимо выполнить несколько шагов. На любом из этих этапов может возникнуть множество различных видов дефектов. Например, в процессе нанесения припоя могут возникать такие дефекты, как избыток припоя, перемычки припоя или недостаточное количество припоя. Во время размещения компонентов возникает несоосность, перепутанная полярность и дефекты отсутствия компонентов. В процессе оплавления мы обнаруживаем такие проблемы, как пустоты, перемычки, шарики припоя, избыток припоя и недостаточное количество припоя.
Применяя рентгеновский контроль, мы можем выявить эти проблемы, чтобы убедиться, что используется правильный процесс. Часто в новых конструкциях процесс необходимо настраивать, регулируя профили нагрева, количество припоя, нанесение пасты и т. д. Выполнение рентгеновского анализа для изучения многих возможных дефектов, таких как пустоты, перемычки или поры, поможет инженеру-технологу в разработке правильного процесса. Это называется проверкой процесса и позволяет ответственному инженеру выполнить быстрый анализ для внесения необходимых изменений.
После того, как надлежащий технологический процесс запущен в массовое производство, можно использовать рентгеновский контроль для непрерывного анализа продукта и обеспечения статистического контроля процесса с помощью показателей качества. Эти данные в режиме реального времени покажут любые изменения в качестве или обеспечат выявление новых дефектов. Использование рентгеновских лучей позволяет наблюдать за тенденциями и реагировать на них наиболее эффективным образом.
ОБНАРУЖЕНИЕ ПОДДЕЛОК
С увеличением объема электроники, сбрасываемой на рынок, появляется огромное количество лома, часто содержащего устаревшие детали. Таким образом, сбор компонентов является крупным рынком труда в странах с более низкой заработной платой. Стремление снизить стоимость для OEM-производителей привело к тому, что происходит все больше и больше интернет-покупок критически важных компонентов. Таким образом, дорогие компоненты могут быть чрезвычайно ценными и нести с собой угрозу подделок. Рентгенография (или рентгеновский контроль) — это повсеместно используемый метод для всех стандартов обнаружения подделок, включая IDEA 1010B, CCAP 101, AS5553, AS6081 и AS6171.
Одним из конкретных методов выявления поддельных компонентов с помощью рентгеновских лучей является использование образцового рентгеновского изображения для сравнения с подозрительной партией. Процесс сравнения, будь то ручной или автоматический с использованием методов компьютерной визуализации, позволяет легко определить компоненты, которые не соответствуют заведомо хорошей поставке. Даже если заведомо качественный рентгеновский снимок недоступен, может быть очень полезно проверить партию. Любые отклонения, наблюдаемые в пределах одной и той же партии, должны быть помечены как подозрительные.
Некоторые распространенные тенденции, которые легко выявляются с помощью рентгеновского контроля, включают: непостоянный размер кристалла, отсутствие элементов кристалла, непостоянный каркас выводов, сломанные/отсутствующие проволочные соединения и непостоянное образование пустот при прикреплении кристалла. Негодный образец можно увидеть на рис. 2. В этом случае компонент был смешан с партией хороших образцов, что подчеркивает важность проведения 100% контроля.
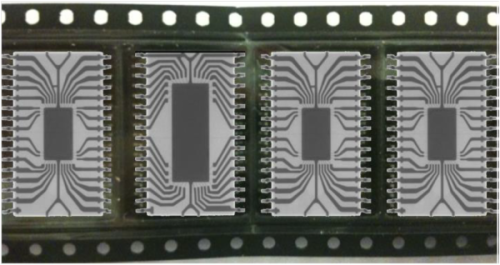
ПОДСЧЕТ КОМПОНЕНТОВ И ВЫБОР МАТЕРИАЛОВ
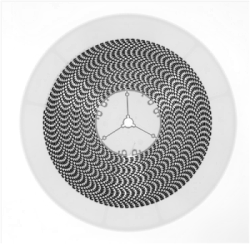
Рис. 3. Рентгеновское изображение компонентов на барабане
Инвентаризация является важнейшим аспектом любой производственной операции. Избыток потраченных денег может лечь на полки, недостаток может привести к дорогостоящим простоям. Это оказывает все большую необходимость поддерживать оптимальное количество на складе и иметь возможность отслеживать необходимое количество наиболее эффективным способом.
Рентгеновский контроль может играть ключевую роль в подсчете компонентов. Поскольку большинство компонентов хранится на барабанах, содержащих тысячи деталей, традиционные методы подсчета деталей требуют много времени. Компоненты должны быть размещены на барабане, намотанными на катушку, затем должны быть намотаны на пустую катушку, а затем повторно намотаны на исходную катушку. Этот метод не позволяет подсчитать отсутствующие компоненты или другие аномалии, которые могут существовать на барабане.
С помощью рентгеновских лучей можно получить изображение всей катушки, даже не извлекая ее из упаковки, что еще больше снижает риск. Отдельные компоненты можно подсчитать и идентифицировать за считанные секунды. Используемая рентгеновская система может затем передавать эти данные в систему управления запасами производителя, чтобы помочь в анализе данных в реальном времени.
Понимание механизма работы рентгеновского контроля
Поскольку бюджеты на разработку нового продукта сокращаются, а устаревание деталей становится обычным явлением, многие организации находят выгоду в разборке старых продуктов, чтобы определить, как они работают и можно ли сделать то же самое дешевле и/или лучше. Этот процесс называется реверс-инжиниринг (обратное проектирование).
Обратное проектирование заполненной печатной платы (ПП) может занять много времени и быть сложным, поскольку необходимо соблюдать огромную осторожность, чтобы не повредить плату. Компоненты должны быть отпаяны и удалены, чтобы составить спецификацию, затем, чтобы определить правильную схему, необходимо отобразить наружные слои платы, а затем тщательно отшлифовать, чтобы обнажить следующий слой.
Поскольку это деструктивный процесс, делающий продукт негодным, его часто считают неприемлемым. Рентгеновские лучи позволяют визуализировать компоненты и отдельные слои платы, не повреждая ни одного компонента. Использование комбинации 2D и 3D рентгеновских снимков этот процесс может занять всего несколько минут, а не дней.
2D, 2.5D И 3D РЕНТГЕНОВСКИЙ КОНТРОЛЬ
Термины 2D и 3D используются в системах продаж для продвижения различных рентгеновских функций, что часто приводит к тому, что конкурирующие организации участвуют в войне спецификаций, так что же они на самом деле означают. Чтобы объяснить разницу, необходимо пересмотреть фундаментальную концепцию рентгеновских изображений, как показано на рис. 1.
Когда образец помещается в поле зрения рентгеновского датчика, освещаемого источником рентгеновского излучения, разная плотность образца будет по разному блокировать фотоны, в результате чего тень образца будет передаваться на рентгеновский датчик. Затем эта тень отображается в виде двухмерного рентгеновского изображения. Это плоский вид части образца, расположенной на пути рентгеновского луча. С помощью этой техники невозможно понять ни высоту, ни глубину.
Для получения 2,5D рентгеновского изображения необходимо отрегулировать ориентацию образца по отношению к пути рентгеновского излучения. Это просто двухмерное изображение, обеспечивающее трехмерное восприятие. Например, если образец вращается вокруг оси, перпендикулярной траектории рентгеновского луча, в потоке рентгеновского излучения в реальном времени, объект воспринимается как вращающийся трехмерный объект.
2.5D-визуализация эффективна, поскольку позволяет просматривать изображения под углом, предоставляя информацию о глубине или высоте объекта. Одним из основных преимуществ 2,5D-изображения является то, что компоненты, расположенные друг над другом, можно разделить, выявив возможные дефекты, которые иначе неразличимы в рамках простого 2D-изображения.
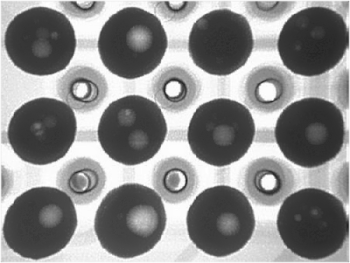
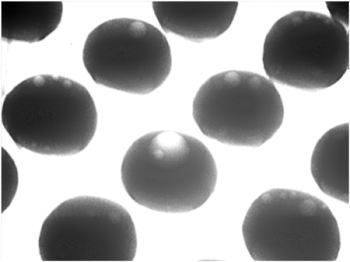
Трехмерное рентгеновское обследование также известно как планарная компьютерная томография (КТ). Это гораздо более дорогостоящий и трудоемкий процесс. Концепция КТ относится к использованию компьютера для создания объемного изображения анализируемого объекта. Компьютерная томография, часто используемая для обратного проектирования, позволяет пользователю заглянуть внутрь твердого объекта, получить данные поперечного сечения в любой ориентации, а также выполнить измерения и анализ внутренних структур.
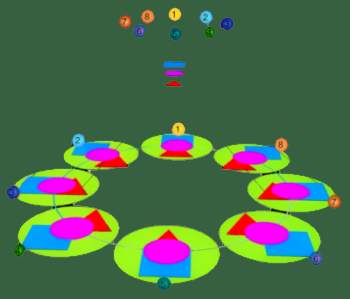
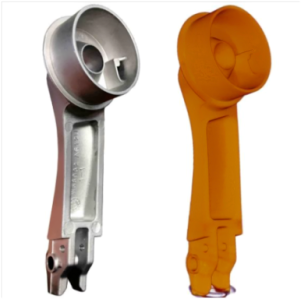
Для создания КТ-модели необходимо сделать несколько рентгеновских снимков одного объекта с разных ориентаций. Этого можно добиться, вращая источник рентгеновского излучения и датчик вокруг объекта или вращая объект в пределах пути рентгеновского излучения. Затем эти изображения анализируются и объединяются для создания 3D-изображения. Чем больше снимков, тем точнее модель. После того, как модель построена, ее можно использовать для анализа объекта способами, которые были бы очень сложными для традиционных 2D и 2.5D. Возможность создания поперечных сечений объекта позволяет реконструировать многослойные печатные платы. Также можно измерить микротрещины в паяных соединениях.
ПУСТОТЫ, ПЕРЕМЫЧКИ И ОТКАЗЫ ТИПА «ГОЛОВА НА ПОДУШКЕ» НА КОМПОНЕНТАХ С ВЫВОДАМИ ВНИЗ
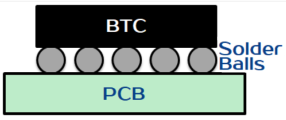
Растущее изобилие компонентов с выводами вниз произошло из-за того, что площадь на печатной плате очень дорога. Чтобы максимально использовать пространство, электроника миниатюризируется и сжимается, чтобы поместиться на наименьшей площади поверхности. Компоненты с выводами вниз (BTC -bottom terminated component), такие как корпуса с матрица шариковых выводов (BGA), четырехугольные безвыводные корпуса (QFN) и светоизлучающие диоды (LED), делают эту миниатюризацию возможной. Подключения к печатной плате расположены на нижней стороне компонента, а не по бокам. Это затрудняет проверку качества соединения.
Рентгеновские методы визуализации с высоким уровнем увеличения и просмотром под разными углами позволяют полностью осмотреть эти скрытые паяные соединения. Пустоты в паяных соединениях являются одним из самых простых дефектов для анализа и измерения. Многие пакеты программного обеспечения для рентгеновского анализа оснащены инструментом анализа пустот, который выделяет области с меньшей плотностью (пустоты) и дает процент от общей площади. Эта возможность позволяет конечному пользователю использовать количественное измерение качества продукта.
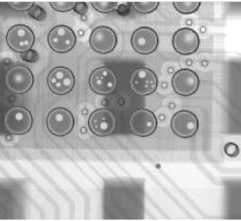
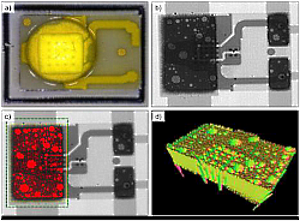
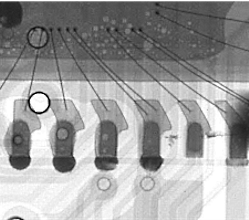
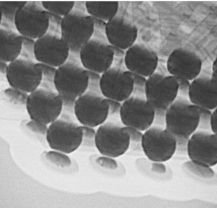
Другими распространенными дефектами, обнаруживаемыми в BTC, являются обрывы, перемычки припоя, создающие короткие замыкания, и неправильные формы, указывающие на проблемы с плоскостностью.
Дефект типа «голова на подушке» возникает, когда шарик припоя на выводе BGA не прижимается к контактной площадке во время процесса оплавления. Это приводит к ситуации, когда шарик припоя может соприкасаться, но не прилипать к контактной площадке. Электрические сигналы могут быть прерывистыми, и рассеивание тепла будет нарушено. Чтобы обнаружить «голову на подушке», требуется рентгеновская система с высоким увеличением и универсальным манипулированием образцами. Образец должен быть перемещен так, чтобы можно было отобразить профиль шара, таким образом чтобы не накладывались какие-либо другие элементы компонента, мешающие обзору.
КОНСТРУИРОВАНИЕ ДЛЯ ПРОИЗВОДСТВА (DFM) И КОНСТРУИРОВАНИЕ ДЛЯ РЕНТГЕНОВСКОГО КОНТРОЛЯ (DFXI)
Требование проверки BTC с помощью рентгеновского изображения поставило перед разработчиками печатных плат новую задачу. Новая компоновка платы должна не только экономить место и соответствовать требованиям к продукту, но также должна быть разработана таким образом, чтобы весь производственный процесс был максимально быстрым и эффективным. Это включает в себя проверки качества. В предыдущем разделе были объяснены основные различия между 2D, 2.5D и 3D, одним из которых является время проверки.
Если требуются 2,5D- и 3D-рентгеновские проверки, эти процессы влекут за собой дополнительное время и дополнительные затраты для контроля качества. В идеале для обеспечения максимальной производительности требуется только двухмерный рентгеновский контроль. Однако при 2D-рентгеновском контроле любые перекрывающиеся компоненты в поле зрения будут создавать дополнительные проблемы в процессе контроля.
На следующих изображениях показаны примеры трудностей, возникающих при проверке печатных плат, которые не были сконструированы для обеспечения рентгеновского контроля (DFXI). На рис. 13 показана двусторонняя печатная плата с BGA на одной стороне и конденсаторами и другими компонентами, расположенными на другой стороне. Перекрывающиеся компоненты требуют 2,5D- или 3D-контроля, чтобы различать элементы, в которых могут быть дефекты. Многослойные платы, компоненты установленные друг на друге и радиаторы усложняют рентгеновский контроль. Необходим учет этих аспектов.
КОНСТРУИРОВАНИЕ ДЛЯ ПРОИЗВОДСТВА (DFM) И КОНСТРУИРОВАНИЕ ДЛЯ РЕНТГЕНОВСКОГО КОНТРОЛЯ (DFXI)
Требование проверки BTC с помощью рентгеновского изображения поставило перед разработчиками печатных плат новую задачу. Новая компоновка платы должна не только экономить место и соответствовать требованиям к продукту, но также должна быть разработана таким образом, чтобы весь производственный процесс был максимально быстрым и эффективным. Это включает в себя проверки качества. В предыдущем разделе были объяснены основные различия между 2D, 2.5D и 3D, одним из которых является время проверки.
Если требуются 2,5D- и 3D-рентгеновские проверки, эти процессы влекут за собой дополнительное время и дополнительные затраты для контроля качества. В идеале для обеспечения максимальной производительности требуется только двухмерный рентгеновский контроль. Однако при 2D-рентгеновском контроле любые перекрывающиеся компоненты в поле зрения будут создавать дополнительные проблемы в процессе контроля.
На следующих изображениях показаны примеры трудностей, возникающих при проверке печатных плат, которые не были сконструированы для обеспечения рентгеновского контроля (DFXI). На рис. 13 показана двусторонняя печатная плата с BGA на одной стороне и конденсаторами и другими компонентами, расположенными на другой стороне. Перекрывающиеся компоненты требуют 2,5D- или 3D-контроля, чтобы различать элементы, в которых могут быть дефекты. Многослойные платы, компоненты установленные друг на друге и радиаторы усложняют рентгеновский контроль. Необходим учет этих аспектов.
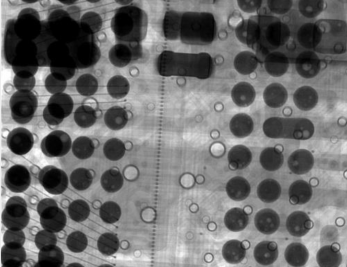
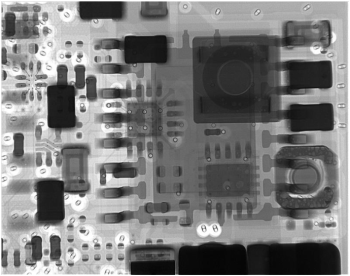
ИСКУССТВЕННЫЙ ИНТЕЛЛЕКТ
По мере того, как новые технологии становятся доступными, жизненно важно изучать их возможные эффекты в текущих процессах. Последние разработки в области искусственного интеллекта (ИИ) трансформируют индустрию рентгеновских изображений. Применяя методы и алгоритмы, используемые в машинном обучении, рентгеновские изображения можно анализировать так, как никогда раньше. ИИ работает в процессе обучения. Алгоритмы получают ряд переменных и результатов, связанных с этими переменными.
При достаточном количестве входных данных система изучит коррелирующие факторы, а затем сможет прогнозировать результаты на основе этих входных данных. Например, чтобы создать модель, которая классифицирует рентгеновские изображения как «ГОДНЫЕ» или «НЕ ГОДНЫЕ», в базу данных изображений необходимо загрузить несколько заранее определенных изображений. Алгоритмы программного обеспечения затем изучат особенности изображений, которые обозначают его как «ГОДНЫЕ» или «НЕ ГОДНЫЕ». По мере того, как в обучающую базу данных загружается большее количество изображений, достоверность полученного прогноза будет увеличиваться.
Одна из проблем с автоматическим рентгеновским контролем (AXI -avtomatic X-ray inspektion) заключается в том, что он ограничен естественной изменчивостью, которая может возникнуть. Возможно, его можно научить только проверять пустоты припоя на BGA, но он не будет фиксировать мусор в изделии. С помощью искусственного интеллекта мы теперь можем выявить известные, и неизвестные отказы. Кроме того, надежность часто возлагается на оператора машины, который должен сделать оценку "годен/не годен". Но операторы зависят от уровня опыта и состояния человека. Машинное обучение может выполнять эти функции с высокой скоростью и не подвержено усталости.
На следующих изображениях показано реальное исследование, проведенное на мобильных телефонах. Большое количество рентгеновских изображений, классифицированных как «хорошие» и «плохие» были введены в базу данных. Эта база данных изображений была использована для создания модели, которая будет анализировать и классифицировать новые изображения. На рис. 15 показано, как эта модель ИИ может правильно найти и пометить отсутствующие винты на плате внутри телефона.
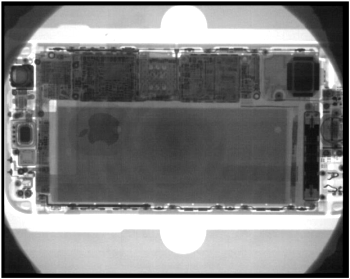
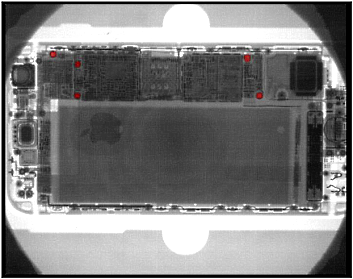
Рис. 15. Использование ИИ для поиска отсутствующих компонентов
Следующее исследование касается упаковки медицинских устройств.Устройство должно быть упаковано таким образом, чтобы оно не подвергалось дополнительной деформации, ослабляющей структуру трубки внутри. Модель ИИ может уловить любые перегибы в трубке и отметить их местоположение.
Внедрение ИИ необходимо любой технологической компании для того, чтобы она оставалась актуальной. Поскольку вся электронная промышленность движется к Индустрии 4.0 ИИ повысит эффективность процессов, улучшит связь и снизит затраты.
ВЫВОД
В течении последних нескольких десятков лет сборка электроники продвинулась вперед по нескольким направлениям. Вместе с миниатюризацией, необходимой для того, чтобы добиться значительных успехов, процессы и стандарты, используемые в производстве, должны жестко контролироваться. Рентгеновский контроль позволяет проводить внутренний осмотр продукции без каких-либо повреждений детали.
Для того, чтобы идти в ногу с технологическим прогрессом по мере создания более сложных продуктов технология, лежащая в основе рентгеновского контроля, также развивается. Достижения в области искусственного интеллекта и другие методы обработки изображений будут продолжать продвигать электронику для проектирования и производства продуктов высочайшего качества.