- Главная
- Оборудование для печатных плат
- Оборудование для поверхностного монтажа
- Технологии производства плат и поверхностного монтажа
- Инструмент для печатных плат и Запасные части
- Материалы и Химикаты для печатных плат и поверхностного монтажа
- Гальваническое оборудование
- Лабораторное и аналитическое оборудование
- Сервис и техническое обслуживание
- Как нас найти
- Начало раздела
- Главный технолог
- Технологии производства
- Консультации
- Контакты
Проектирование печатных плат и электронных модулей
Проектирование печатных плат для предприятия контрактного изготовления печатных плат и/или электронных модулей - ВАРИАНТ 1
Автор: Илья Лейтес, главный технолог ООО "РТС Инжиниринг"
1. ОБЛАСТЬ ПРИМЕНЕНИЯ
Настоящая инструкция является дополнением к ГОСТу 23751-86 (устаревший) и устанавливает рекомендуемые конструктивно-технологические нормы проектирования (КТНП) многослойных печатных плат (многослойных печатных плат), изготавливаемых методом металлизации сквозных отверстий и формирования наружных проводящих слоев методом «Тентинг».
Реализация настоящих КТН обеспечивает технологичность изготавливаемых многослойных печатных плат (нормативный процент выхода годных, установленный на предприятии; соответствие печатных плат НТД по качеству и надежности).
При проектировании гибко-жестких многослойных печатных плат (ГЖ многослойных печатных плат) или многослойных печатных плат с внутренними теплопроводящими слоями (многослойных печатных плат с ВТС) рекомендуется дополнительно использовать приложения к данной инструкции:
- «Конструктивно-технологические нормы на проектирование гибко-жестких плат»
- «Конструктивно-технологические нормы на проектирование многослойных печатных плат с внутренними теплопроводящими слоями».
2.КОНЦЕПЦИЯ ДОКУМЕНТА
2.1. Оптимизация конструкции печатных плат для обеспечения технологичности (проектирование для производства).
2.1.1. Правило максимального технологического запаса.
Не рекомендуется использовать минимально допустимые параметры и характеристики по всей площади печатных плат. Там где возможно, необходимо использовать менее жесткие нормы.
2.1.2. Правило минимальной толщины травления проводящего рисунка.
При проектировании прецизионного рисунка необходимо выбирать минимальную толщину меди, обеспечивающую функциональные свойства спроектированного узла .
2.1.3. Правило максимального зазора.
Для технологии «Тентинг» рекомендуется в критичных местах увеличивать зазор за счет уменьшения ширины проводников (например 125/150 мкм или 100/150 мкм вместо 125/125 мкм).
2.1.4. В связи с недостаточно подробным изложением приемосдаточных характеристик в ГОСТ 23752-79, не соответствующих современному технологическому процессу и современным используемым материалам, при приемке рекомендуется использовать «Дополнительные Требования», предварительно согласованные с изготовителем печатных плат(в основном относительно требований к внешнему виду паяльной маски, адгезионных подслоев, припоя после горячего лужения , металлизации отверстий диаметром более 3 мм).
3.ОСНОВНЫЕ ТЕХНИЧЕСКИЕ ХАРАКТЕРИСТИКИ
Технологические возможности производства печатных плат и используемых базовых материалов
Таблица 1.
1. Метод изготовления | Метод металлизации сквозных отверстий Формирование рисунка наружных проводящих слоев методом «Тентинг». |
2. Метод установки и пайки компонентов | Автоматизированный, технология поверхностного монтажа компонентов (ТПМК), смешанный монтаж. |
3. Соответствия стандартам многослойных печатных плат | ГОСТ 23752-79, 3 группа жесткости, или ANSI/IPC , 2 класс (3 класс по отдельным пунктам ANSI/IPC) |
4. Габариты многослойных печатных плат (мм) максимум | 450х545 (золочение 400х300) |
5. Допуск механообработки | 12 квалитет ISO (для прямоугольного контура) |
6. Шаг координатной сетки Основной Дополнительный |
Метрическая или дюймовая (допускается на одной плате использование метрической и дюймовой координатной сетки) 2,5 мм или 2,54 мм (100 mil) 0,05 мм или 0,051 мм(2 mil) |
7. Слойность многослойных печатных плат (количество проводящих слоев) | До 22 |
8. Материал для изготовления многослойных печатных плат | Тип FR-4 Марка DURAVER-E-Cu-104-ML (или аналогичный) Толщина фольги – 0,035-0,018 мм Толщина изоляции – 0,36 мм; 1,0 мм 0,46мм; 0,51мм; 0,2мм; 0,25мм; 0,18мм; 0,15мм (0,125мм; 0,1мм по предварительному согласованию) Другие материалы по предварительному согласованию. |
9. Стеклоткань прокладочная | Тип FR-4, марка DURAVER-E-104-ML, PREPREG 1080 05 АТ 01,толщина 0,063 мм Другие материалы по предварительному согласованию. |
10. Паяльная маска | Сухая пленочная 0,075 мм (3 mil) или жидкая по IPC/ANSI –SM-840 |
11. Маркировка | Краска маркировочная белая ф. Coats (Англия) или аналогичная, min ширина линии – 150 мкм,min шрифт 1,3; типовой - 1,5/200 |
4. РЕКОМЕНДУЕМЫЕ КОНСТРУКТИВНО-ТЕХНОЛОГИЧЕСКИЕ НОРМЫ
Требования к номинальным размерам при проектировании многослойных печатных плат
4.1. Требования к проводящему рисунку слоев.
4.1.1. Минимальная ширина проводников в РСВ файле 0,125 мм (5 mil) [0,100 мм (4 mil)].
Примечание: в скобках[ ] указаны предельные нормы которые могут быть реализованы по предварительному конкретному согласованию.
4.1.2. Наименьшее номинальное значение зазора между элементами проводящего рисунка слоя, S (мкм) (в РСВ – файле) приведено в таблице 2.
Таблица 2.
Слой | S (мкм) типовое значение | Допустимое значение в технически обоснованных случаях |
Наружные слои | 175 | 150 |
Внутренние сигн. слои | 150 | 125 |
Освобождение во внутренних экранах – металлизированное отверстие | 250 | 200 |
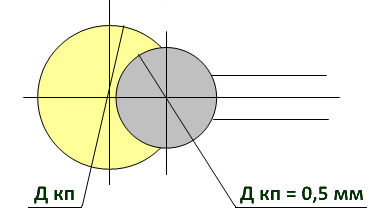
В узких местах допускается точечный зазор – 150 мкм для наружных слоев, 125 мкм - для внутренних.
Узким местом трассировки считается участок на плате в месте (точке) зазора между одной круглой контактной площадкой и другой круглой контактной площадкой, либо в месте (точке) зазора между круглой контактной площадкой и проводником.
4.1.3. Рекомендуется при трассировке расширять место соединения проводника с контактной площадкой путем впечатывания в геометрический центр соединения проводника и контактной площадки дополнительной контактной площадки диаметром 0,5 мм (пример см. рис. 1) или иным аналогичным способом.
4.1.4. Для неметаллизированных отверстий в проводящем рисунке (металла) необходимо делать освобождение 0,2 мм по контуру отверстия.
4.1.5. Размеры освобождения в экранах выбираются из условия
Досв. экр. – d ≥ 0,8 мм.
4.1.6. Зона запрета трассировки от края платы (в т.ч. края экранов) 0,5 Нмпп + 0,5 допуска на механообработку.
4.1.7. Выбор ширины проводников в зависимости от протекающего по ним тока, толщины меди и допустимого перегрева в соответствии с IРС 2221. «Общий стандарт по конструированию печатных плат» (для справки) (см. табл. 3).
Таблица 3.
Допустимый перегрев | Допустимый ток (а) для ширин проводников (мкм) | ||
125 | 150 | 500 | |
Толщина меди 50 мкм (наружный слой) | |||
10°С | 0,5 | 1 | 2,0 |
20°С | 0,75 | 1,3 | 3,0 |
30°С | 1 | 1,7 | 3,7 |
Толщина меди 18 мкм (внутр слой) | |||
10°С | 0,25 | 0,2 | 0,6 |
20°С | 0,37 | 0,3 | 0,9 |
30°С | 0,5 | 0,37 | 1,2 |
Толщина меди 35 мкм (внутр. слой) | |||
10°С | 0,12 | 0,25 | 0,4 |
20°С | 0,17 | 0,37 | 0,6 |
30°С | 0,25 | 0,5 | 0,75 |
4.2. Требования к структуре многослойных печатных плат.
4.2.1. Рекомендуется структуру печатных плат оформлять с указанием толщины металла проводящего рисунка слоев и расстояний между слоями. Рекомендуется использовать структуры с фольгой на наружных слоях. При отсутствии специальных указаний в КД будет применена структура по п.4.2.3.
Для справок: на структурах с использованием ламината на наружных слоях, нормы по короблению не гарантируются.
4.2.2. Реализуемая толщина металла:
- для внутренних слоев она может быть 18 мкм (предпочтительно для прецизионного рисунка – ширина проводников ≤150 мкм) или 35 мкм.
- для наружных слоев минимальная толщина металла 50 мкм, возможно изготовление рисунка наружных слоев с толщиной 70 мкм [90 мкм и более необходимо особо оговорить при заказе].
4.2.3. Рекомендуемые структуры многослойных печатных плат.
Примечание. Рекомендуются структуры с «фольгой на наружных слоях» из-за их меньшей склонности к короблению. По согласованию с заказчиком могут быть реализованы также и структуры с ламинатом на наружных слоях с учетом замечаний п. 4.2.1.
4.2.3.1. Типовая толщина и структура проводящего рисунка наружных слоев
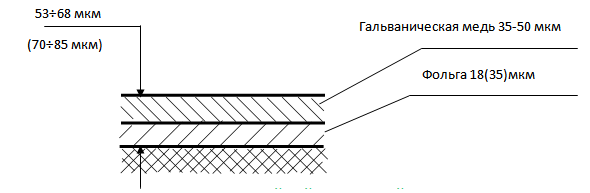
4.2.3.2. Рекомендуемая структура 4-х слойных многослойных печатных плат, толщина ~1,6 мм
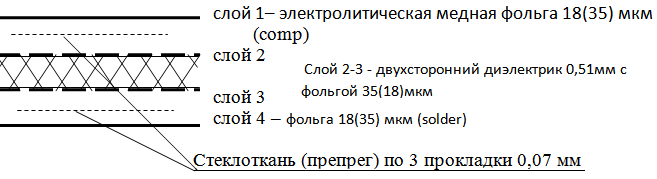
4.2.3.3. Рекомендуемая структура 3-ной многослойных печатных плат, толщина ~ 1,6 мм

4.2.3.4. Рекомендуемая структура 8-мислойной многослойных печатных плат, толщина ~ 1,6 мм
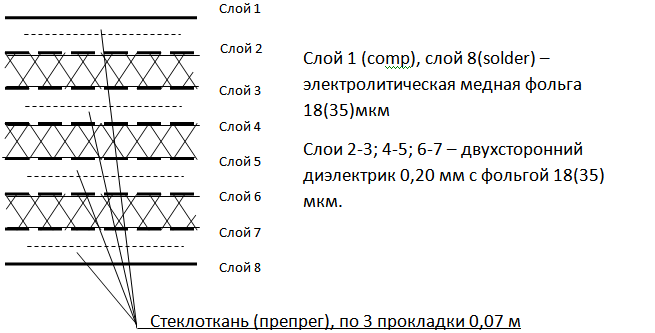
4.2.3.5. Рекомендуемая структура 10-слойных многослойных печатных плат, толщина ~ 1,6 мм
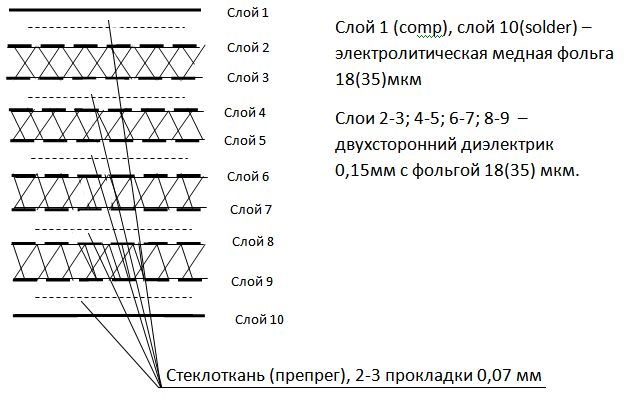
4.2.3.6. Рекомендуемая структура 12-тислойных многослойных печатных плат, толщина ~ 1,7 м
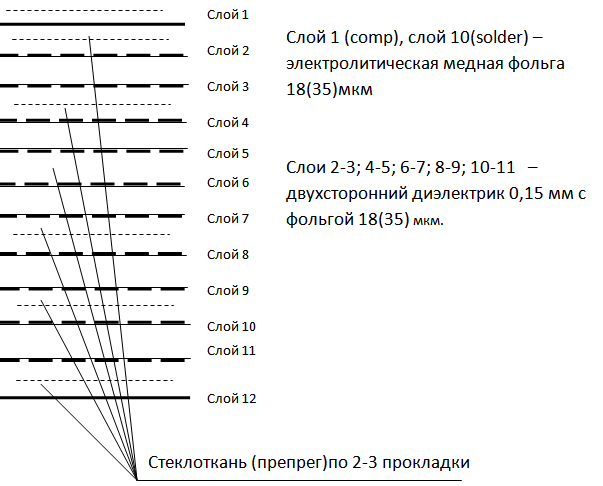
4.2.4. Структуры с количеством слоев более 12 или иными толщинами многослойных печатных плат требуют дополнительного согласования с изготовителем.
4.2.5. Толщина диэлектрика (расстояние между проводящими рисунками металла выбирается из следующего размерного ряда, мм:
1,0; 0,51; 0,36; 0,2; 0,15 (использование материала 0,25; 0,125 требует специального согласования).
4.2.6. Структура должна быть симметрична относительно средней линии поперечного сечения.
4.2.7. Предельные отклонения толщины многослойных печатных плат (∆Н), при толщине плат (Нмпп) приведены в таблице 4.
Таблица 4.
Нмпп, мм | До 2,2 | До 2,75 | До 3,3 |
∆Н, мм | ± 0,2 | ± 0,25 | ± 0,3 |
4.3.Требования, обеспечивающие выполнение норм по короблению многослойных печатных плат.
4.3.1.При соблюдении требований, изложенных в п.п. 4.2, изготовитель гарантирует выполнение требований по короблению – 1,5% макс., соответствующих IPC/ANSI, 2 класс.
4.3.2. Рекомендуемое соотношение сторон многослойных печатных плат (А:В) не более чем 2:1.
4.3.3. Для уменьшения вероятности коробления многослойных печатных плат при проектировании слоев необходимо соблюдать равномерное распределение проводящего рисунка по площади проводящего слоя («баланс меди»).
4.3.4. Установление более жестких норм по короблению – 1% макс. (3 класс IPC/ANSI) требует соблюдения дополнительных условий при проектировании.
4.3.4.1. Необходимо экранные слои выполнять в виде сетки с ориентировочными параметрами – шаг 2,5 мм ширина проводника 0,6 мм.
4.3.4.2. При неравномерном заполнении рисунка сигнальных слоев необходимо пробельные участки заполнять сеткой с параметрами, указанными в п.4.3.4.1.
4.3.4.3. Возможность реализации норм жестче чем 1% требует отдельного согласования.
4.4.. Требования к отверстиям.
4.4.1. Основная шкала сквозных трассировочных отверстий (мм) в таблице 5. Рекомендуется использование трассировочных переходных отверстий 0,4 или 0,5 мм.
Трассировочные переходные отверстия 0,3 мм использовать в технически обоснованных случаях (только в узких местах). Допускается на одной плате использование трассировочных переходных отверстий диаметром 0,3; 0,35 и 0.4 мм.
Таблица 5.
Минимальный диаметр сверла, мм | 0,3 (0,25) | 0,35 | 0,4 | 0,5 |
Толщина платы, мм до | 1,6 | 2,0 | 2,5 | 3,5 |
Диаметр отверстия, мм после металлизации и лужения (золочения) | Не регламентируется (обеспечивается технологией) |
|||
Диаметр КП, мм в РСВ файле | 0,7 | 0,75 | 0,8 | 0,9 |
Допускается при изготовлении печатных плат уменьшать диаметр сверления переходных отверстий без согласования с заказчиком.
4.4.2. Основная шкала сквозных монтажных металлизированных отверстий указана в таблице 6.
Таблица 6.
Диаметр мет. отв. в готов. плате с допуском (для справки) | 0,7(-0,13) | 0,8(-0,13) | 0,9(-0,13) | 1,0(-0,13) | 1,1(-0,13) |
Диаметр сверла | 0,8 | 0,9 | 1,0 | 1,1 | 1,2 |
Рекомендуемый диаметр КП (минимальный диаметр КП) | 1,3 (1,2) | 1,4 (1,3) | 1,5 (1,4) | 1,6 (1,5) | 1,7 (1,6) |
4.4.3. В целях повышения качества и надежности изделия, в зависимости от области применения, рекомендуется минимальную разность диаметра контактной площадки (Дк.п.) и диаметра сверла (d сверла) выполнять в РСВ-файле согласно таблице 7
Таблица 7.
Область применения | ДК.П. - d сверла | Примечание |
1* | 0,5 мм | Требуется согласование КД с разработчиком |
2 | 0,4 мм | |
3 | 0,35 мм | По возможности ограничить количество мест с таким соотношением. С обязательным выполнением рекомендаций |
4 | 0,3 (0,25) мм | Только в местах, где необходимо реализовать минимально допустимые зазоры |
*1 – печатных плат, предназначенные в летные образцы изделий (серийные).
2 – печатных плат, предназначенные в возимые образцы изделий.
3 – печатных плат, предназначенные в стационарные наземные изделия.
4 – печатных плат для образцов, прототипов.
4.4.4. Рекомендуется для сверл менее 0,5 мм увеличивать КП на нижнем слое (Solder) в РСВ файле на (0,1÷0,05) мм. (для компенсации случайного изгиба сверла).
4.4.5. Размер диаметра сверла выбирается из ряда кратного 0,1 мм за исключением 0,25; 0, 35; 1,15 (мм).
4.4.6. Расстояние от края металлизированного отверстия (без КП) до ближайшего проводника на внутренних слоях, в т.ч. до края освобождения в экранах, 0,4 мм минимум.
4.4.7. Толщина металлизации отверстий по ГОСТ 23752-79 – 25 мкм минимум.
4.4.8. Для металлизации в отверстиях диаметром более 3 мм не гарантируется соответствие с требованиями п.2.3.4., ГОСТ 23752 – 79.
4.4.9. В контактных площадках вокруг крепежных металлизированных отверстий диаметром более 3 мм гарантированная металлизация реализуется с помощью металлизированных переходов диаметром 0,4; 0,5 мм по контуру отверстия.
4.5.Требования к слою паяльной маски
4.5.1. Жидкую паяльную маску применять: в случае необходимости золочения контактов печатного разъема; финишного покрытия иммерсионным золотом. При этом тентирование отверстий жидкой паяльной маской диаметром более 0,4 мм не гарантировано.
При применении жидкой паяльной маски при разработке (разводке) печатной платы все монтажные и переходные отверстия следует открывать от паяльной маски (т.е. не делать тентирование отверстий жидкой паяльной маской). Исключение составляют переходные отверстия на посадочном месте корпусов BGA, они всегда должны быть закрыты (тентированы).
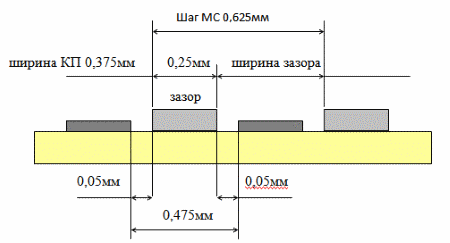
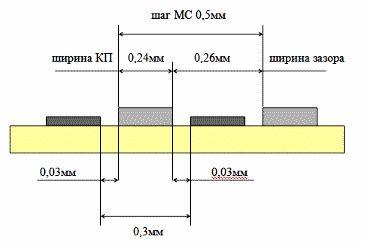
4.5.2. Сухую паяльную маску рекомендуется применять в случае разработки (разводки) платы для монтажа микросхем в корпусах с планарными выводами. При этом ширина перемычек не может быть менее 180 мкм.
4.5.3. При применении сухой паяльной маски переходные отверстия диаметром менее 0,6 мм должны быть покрыты паяльной маской, отверстия диаметром 0,6 мм и более открыты (т.к. на отверстиях 0,6 мм и более тент не гарантирован), отклонения от этих требований оговариваются особо.
4.5.4. Не допускается тентировать защитной паяльной маской отверстия с одной стороны печатных плат.
4.5.5. Освобождения в паяльной маске (припуск на размер А элементов рисунка паяльной маски относительно элементов рисунка металла наружного слоя печатных плат).
4.5. 5.1. Для контура мех. обработки 0,2 по контуру внутрь тела платы.
4.5.5.2. Для металлизированных отверстий Дкп + 0,2 мм (0,1 мм по контуру), для неметаллизированных отверстий Дсв + 0,2 мм.
4.5.5.3. Для микросхем с шагом 0,625 мм в РСВ-файле ширина контактной площадки 0,375 мм, ширина зазора = 0,250 мм, величина освобождения под паяльную маску 0,475 мм (см. рисунок 1).
4.5.5.4 Для микросхем с шагом 0,5 мм в РСВ – файле ширина контактной площадки 0,24 мм и менее, ширина зазора – 0,26 мм, величина освобождения под паяльную маску 0,3 мм (см. рисунок 2).
4.5.5.5. В случае, если микросхема с шагом выводов 0,5 мм имеет фактический размер вывода более 0,24 мм возможны два варианта технического решения:
Вар. 1. Применяется жидкая паяльная маска (с учетом требований по п.2.15) с шириной К.П. – 0,27 мм, шириной зазора – 0,23 мм, величиной освобождения – 0,33 мм, перемычкой 0,17.
Вар. 2. Освобождается весь ряд ламелей от перемычек, выполненных паяльной маской (возможно применение сухой паяльной маски).
4.6. Требования к проектированию слоя сеткографической маркировки.
4.6.1.Типовая высота шрифта 1,5 мм min при ширине линии 0,2 мм min.
4.6.1.1.Допускается в отдельных местах использовать шрифт 1,3 мм с шириной линии 0,15 мм.
4.6.1.2. Виртуальный зазор (минимальное расстояние) между линиями сеткографической маркировки и КП а также ламелями под пайку не менее 0,5 мм.
Примечание. В случае нанесения маркировки струйным принтером требования к рисунку маркировки в соответствии с техническими возможностями оборудования.
4.7. Требования к проектированию посадочных мест компонентов (элементы проводящего рисунка наружных слоев).
4.7.1.Компоненты поверхностного монтажа могут устанавливаться с двух сторон многослойных печатных плат.
4.7.2. Корпуса со штыревыми выводами рекомендуется устанавливать только со стороны одного слоя.
4.7.3. КП посадочных мест проектируется под технологию автоматизированного поверхностного монтажа компонентов (ТПМК) и не рассчитаны на ручную пайку.
Рекомендуется: КП проектировать с учетом методов пайки (ИК или волна); они должны быть различными для резисторов и конденсаторов одного типо-размера – в соответствии с рекомендациями IPC/ANSI – SM – 782, а также учитывать направление движения узла в процессе пайки и теневые эффекты. Для волны все чип-компоненты должны быть установлены параллельно одной стороне.
4.7.4.При проектировании не допускается:
4.7.4.1.Проектировать переходные отверстия в ламелях (КП) под установку элементов поверхностного монтажа, либо касательно их. Переходное отверстие должно быть отделено от ламелей под установку элементов поверхностного монтажа перемычкой паяльной маски шириной 0,5 мм min.
4.7.4.2.Объединять в одну соседние ламели микросхем, а также ламели рядом стоящих чип-компонентов.
4.7.4.3.Проектировать перемычки, соединяющие две ламели, в промежутках между ламелями микросхем поверхностного монтажа.
4.7.5. Для КП (ламелей)элементов, монтируемых в отверстия или на поверхность и присоединенных к слоям земли, питания или большим полигонам, необходимо предусматривать в этих слоях тепловые барьеры (утонения, рассечки).
4.7.6. Минимальное расстояние до ближайшего корпуса должно быть не менее высоты наивысшего из двух соседних корпусов.
4.8. Дополнительные требования (рекомендации) по проектированию посадочного места под корпуса, имеющие в качестве выводов матрицу шариковых выводов на дне корпуса - Ball Grid Array (BGA).
4.8.1. Конфигурация элементов посадочного места компонентов BGA приведены на рисунке 3.
4.8.2. Размеры элементов посадочного места компонентов BGA приведены в таблице 8.
Таблица 8.
Шаг выводов корпуса ВGA, мм | Диаметр КП под пайку шариков (соmр),мм | Диаметр КП сквозных трассировочных отверстий, мм | Диаметр сверла, мм | В/ (∆) min Мин. ширина линий – зазор, мм |
Диаметр освобождений в паяльной маске, мм | Зазор КП-ПМ по контуру, мм | ||||
comp | sold | внут | comp | sold | внут | |||||
1,5 | 0,6 | 0,7 | 0,8 | 0,8 | 0,4 | 0,4 | 0,4 | 0,2 | +0,2 | 0,100 |
1,27 | 0,6 | 0,7 | 0,8 | 0,8 | 0,4 | 0,4 | 0,4 | 0,15 | +0,1 | 0,05 |
1,27 | 0,6 | 0,7 | 0,8 | 0,8 | 0,3/0,35 | 0,2 | 0,2 | 0,15 | +0,1 | 0,05 |
1,0 | 0,5 | 0,7 | 0,8 | 0,65 | 0,3/0,35 | 0,2 | 0,2 | 0,125 | +0,1 | 0,05 |
1,0 | 0,45 | 0,65 | 0,7 | 0,7 | 0,3 | 0,15 | 0,175 | 0,125/0,15 | +0,1 | 0,05 |
0,8 | 0,35 | 0,6 | 0,7 | 0,65 | 0,3/0,25 | 0,15 | 0,15 | 0,100/0,125 | +0,1 | 0,05 |
4.8.3. Для шагов между шариковыми выводами 1,0 и 0,8 мм разводку экранных слоев в зоне посадочного места BGA проводить отдельными проводниками, в окне освобождения в экранном слое в размер корпуса BGA.
4.8.4. Разводку по наружным слоям (comp, sold) рекомендуется проводить только от внешних рядов КП. Выбор конкретного варианта проводить по согласованию с изготовителем.
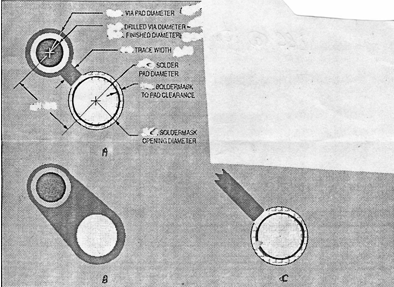
Рис. 3. Варианты геометрии контактных площадок (КП) для BGA
А) КП и межслойный переход с освобождением в паяльной маске
В) КП типа слезки
С) КП и подходящий к ней сигнальный проводник
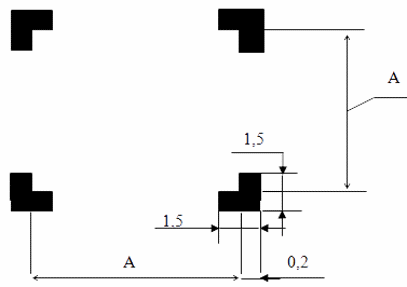
Рис. 4. Угловые реперы для BGA-компонентов
А – наружный габарит корпуса BGA
Для BGA с шагом 1,27 мм допускается 2 угловых репера.
Для BGA с шагом 1 мм допускается 3 угловых репера.
Для BGA с шагом 0,8 мм желательно 4 угловых репера для точности установки.
4.8.5. Не допускается выполнять переходные отверстия в КП для распайки шариков BGA-компонентов. (за исключением случаев заполнения отверстий).
4.8.6. Для компонентов BGA в рисунке наружного слоя рекомендуется уголками (угловыми реперами) обозначить габариты корпуса: ширина линии 0,2 мм, длина полок уголка – 1,5 мм.
Допускается в качестве угловых реперов использовать фрагменты проводников наружного слоя.
4.8.7. Не рекомендуется расположение компонентов BGA с двух сторон печатных плат напротив друг друга.
4.8.8. Для обеспечения автоматизированного рентгеновского контроля качества пайки BGA-компонентов рядом с КП для пайки шариков, вводится дополнительная КП касательная основной под углом 45° диаметром равная половине диаметра (0,5 D) основной КП.
Освобождение в паяльной маске 0,05 по сложному контуру составной КП (основная и дополнительная должны быть освобождены от паяльной маски).Рис. 5
4.9. Дополнительные требования к технологической адаптации, обеспечивающие автоматизированный монтаж.
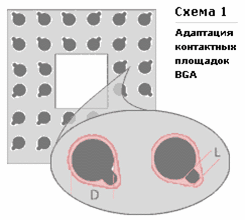
4.9.1. Для обеспечения возможности автоматизированной сборки необходимо внесение дополнительных реперных знаков.
4.9.2. Рекомендуемая форма реперных знаков – ромб с углом 90° (квадрат повернутый на 45°) или «бабочка» - 2 квадрата, касающиеся одним углом.
4.9.3.Размер стороны ромба 1,5 мм. Размер стороны квадратов в «бабочке» 1,3 мм.
4.9.4.Размер освобождения в паяльной маске круг диаметром на 0,5 мм больше размера репера ( его диагонали).
4.9.5.Выбор места расположения репера в поле платы произвольный – участок, где нет рисунка. Допускается расположение реперов внутри посадочных мест компонентов. Расположение реперов не ближе 5 мм к краю платы.
4.9.6. Количество реперов – 2 шт. на фрагмент (плату). Желательно расположить реперы по диагонали фрагмента (платы). При сборке на групповую многофрагментную заготовку необходимо ввести дополнительно 2 репера на заготовку вне рабочего поля фрагментов.
4.9.7. При расположении монтажных элементов с 2-х сторон реперы также должны быть расположены с обеих сторон фрагмента (платы).
4.9.8. Для одного типа плат реперы должны быть всегда в одинаковых координатах. Координаты реперов нижней и верхней стороны независимы.
4.9.9. Для элементов QFP, TSOP с шагом выводов 0,5 мм и менее ( а также BGA), рекомендуется по диагонали каждого посадочного места вводить 2 индивидуальных репера микросхемы (ромб 1,5 х 1,5 мм) с освобождением в паяльной маске. Расположение реперов должно быть таким, чтобы они не перекрывались корпусом микросхемы.
Примечание. Для оборудования с инновационными системами видео распознавания образов возможно использование в качестве реперов и иных элементов рисунка слоев печатных плат.
5. Перечень документов для реализации заказа изготовления печатных плат
5.1. Файл проекта в формате PCAD 4,5; PCAD 8,5; PCAD 2002, Gerber файлы RS274X.
5.2. КД на бумажном носителе или информация в АСАD (DWG), содержащие следующие данные:
А) чертеж с габаритно-присоединительными размерами
Б) структура платы в соответствии с п.3
В) таблица КП и сверл
Г) таблица описания слоев РСАD
Д) сетка трассировки (дюймы, метрическая, псевдодюймовая)
Е) технические требования.
5.3. От заказчика необходимо официальное подтверждение о полной или неполной реализации КТН (данная «Инструкция по проектированию»). В случае неполной реализации КТН необходимо подробно указать какие нормы не соблюдены.
6. Перечень документов и форма поставки компонентов для реализации заказа на изготовление узла на печатных плат (монтаж), изготовленной «на стороне».
6.1. Чертеж в АСАD с техническими требованиями и указанием габаритно присоединительных размеров (учтенный экземпляр КД, положенный в архив).
6.2. Допускается использовать упрощенный вариант чертежа представляющий собой совмещенный рисунок КП под пайку и слоя маркировки со схемными обозначениями.
6.3. Спецификация содержащая позиционный номер, название и маркировку компонента, тип корпуса, схемное обозначение в примечании, дополнительные требования по монтажу нестандартных элементов. Компоненты должны быть сгруппированы по номиналам.
Примечание . Документация должна быть изготовлена в четком виде, однозначно понимаема, легко читаема без дополнительных оптических средств, пригодная к размножению на стандартной множительной технике.
6.4. Накладная с перечнем и количеством передаваемых компонентов.
Примечание. Входной контроль компонентов и их пересчет не производится. Заказчик несет ответственность за качество и правильный подбор комплектации.6.5. Компоненты должны поставляться в заводской упаковке.
Чип компоненты желательно поставлять на катушках или обрезках ленты максимальной длины микросхемы в вакуумной упаковке. Излишки будут возвращены после монтажа, заказанных узлов. При нарушении вакуумной упаковки изготовитель не отвечает за внутренние повреждения микросхем при пайке.6.6. Для составления программ автоматизированного монтажа и контроля необходимо передать полные САD-данные в текстовом файле (импортированные из системы САD) содержащие:
- схемные обозначения (Refds)
- наименования компонентов и номиналы (Devname)
- тип корпуса (Type)
- координаты центров компонентов (Centroid) или координаты I вывода
- угол поворота (Angle)
- на какой стороне стоит компонент (Side)
6.7. Корпуса используемых компонентов должны соответствовать всем требованиям к компонентам, предназначенным для поверхностного монтажа. В частности, выдерживать воздействие всех технологических сред и термоудар при нахождении в печи (Т = 240÷260 0 С в течении 1,5 минут). В ином случае необходимо в технических требованиях указать особые условия по монтажу.
6.8. Входной контроль печатных плат заказчика не производится. Заказчик отвечает за обеспечение качества печатных плат, в т.ч. в отношении пригодности к монтажу и температуростойкости.
6.9. Дополнительно к требованиям п.6 необходимо предоставить виртуальную информацию по конструкции печатных плат (рсв или gerber-файлы) для изготовления трафаретов припойной пасты.
7. Рекомендуемое оформление технических требований в конструкторской документации на печатную плату.
7.1. Многослойная печатная плата из N слоев (структура) с травленными проводниками. Компоненты поверхностного монтажа расположены на (одной/двух) сторонах платы. Компоненты со штыревыми выводами расположены на одной стороне платы. Защитная паяльная маска (ПМ) с двух сторон платы. Припойное покрытие олово-свинец на двух сторонах платы и в монтажных отверстиях. Маркировка на (одной/двух) сторонах платы.
7.2. Готовая плата должна соответствовать требованиям ГОСТ 23752-79, 3 группа жесткости и данным техническим требованиям.
7.3. Материал для изготовления многослойных печатных плат термостойкий негорючий стеклоэпоксидный диэлектрик класса FR-4 («DURAVER» Е-104-МL фирмы «ISOLA», тип и марка приведены в таблице, либо аналогичный классу FR-4).
7.4. Материал припойного покрытия Гор. ПОС-61 ГОСТ 9.314-86, либо материал покрытия контактных площадок и ламелей химический никель 5 мкм, химическое золото 0,2 мкм (хим. Ni – 5, хим. Au – 0,2) или аналогичный.
7.5. Припойное покрытие на ламелях для компонентов поверхностного монтажа, на КП для элементов со штыревыми выводами и в отверстиях, не закрытых паяльной маской, выполняется в соответствии с требованиями ГОСТ 9.301-86. Припой расплавлен и выровнен горячим воздухом. Толщина не регламентируется, обеспечивается технологией и топологией КП.
7.6. Материал паяльной маски – (жидкий фотополимер или сухой пленочный фоторезист) должен соответствовать требованиям IPC/ANSI-SM-840. Защитная паяльная маска по чистой меди выполняется в соответствии с ANSI-SM-840 В, класс 3.
7.7. Ручная маркировка (при необходимости) выполняется белой маркировочной краской AQXZ500T фирмы «Коутс» (или аналогичной).
7.8. Металлизация крепежных отверстий диаметром более 3 мм не регламентируется.
7.9. Минимально допустимая ширина линий 0,08 мм на наружных слоях и 0,1 мм на внутренних слоях.
.10. Допустимое отклонение от номинала расстояний между осями любых крепежных, переходных или монтажных отверстий ± 0,10 мм. Обеспечивается инструментом.
7.11. Восстановление дефектов печатных плат по ГОСТ 27200-87 (устаревший) (количество допустимых восстановленных дефектов печатных проводников на внутренних слоях - до 6, на внешних – до 3-х.
7.12. Минимально допустимый зазор 0,1 мм на участках открытых от ПМ и 0,08 мм на участках закрытых ПМ.
7.13. Габаритные размеры по 12 квалитету.
7.14. Допуск на расстояние от края печатных плат до оси любого отверстия в соответствие с допуском на габаритные размеры.
7.15. Коробление не более 1,5 % измеренное по методике IPC/ANSI – ТМ 650 кл.2.
7.16. Допускается неоднотонность адгезионного покрытия на металле внутренних слоев просвечивающих сквозь диэлектрик основания.
7.17. Параметры элементов печатной платы приведены в таблице № Х и № ХХ
7.18. * - размеры для справок.
7.19. **- размеры обеспечиваются инструментом.
7.20. На наружных слоях многослойных печатных плат
Маркировать травлением по ГОСТ 26.020-80 или шрифтами САПРа соответствующего размера;
1)наименование платы, шрифт 2,5-Пр3,
2)децимальный номер сборочного чертежа многослойных печатных плат, шрифт 2,5-Пр3,
3)идентификатор проводящего рисунка платы, шрифт 2,0-Пр3,
4)децимальный номер сборочного чертеж панели, шрифт 2,5-Пр3,
5)версия многослойных печатных плат, шрифт 2-Пр3,
6)версия панели, шрифт 2-Пр3,
7)№ заказа, (заводской номер платы).
Маркировать сеткографией или струйным принтером по ГОСТ 26.020-80 или шрифтами САПРа соответствующего размера:
1)контур установки компонентов, обозначение посадочных мест компонентов по спецификации,
2)ключ ориентации компонентов,
3)идентификатор сборки панели, шрифт 2-Пр3,
4)контур места клейма представителя заказчика и ОТК для многослойных печатных плат и панели,
5)контур места знака предприятия-изготовителя.
7.21. Клеймить клеймо ОТК.
7.22. Клеймить клеймо представителя заказчика.
7.23. Маркировка клейма приемки и ОТК вручную.
7.24. Маркировать переменную часть заводского номера по вручную.
Приложение 1 к инструкции
Краткие конструктивно-технологические нормы, реализуемые на производстве.
1. Размер заготовки от 350х250 до 500х600.
2. Количество слоев до 22.
3. Проводник/зазор – 0,15/0,15 мм (0,125/0,150*), (0,125/0,125 мм) или 0,1/0,125*мм).
4. Минимальный диаметр сверления – 0,3 мм (0,25* или 0,2*мм)
5. Минимально допустимое соотношение (Dкп – dсв) – 0,4 (0,3*)мм.
6. Минимально допустимый зазор между краем металлизированного отверстия и освобождением в экранах – 0,4 мм.
7. Отношение толщина/минимальный диаметр сверла (Н:d) не более 7 (10*).
8. Минимальная толщина металла на наружных слоях 50 мкм.
9. Паяльная маска обязательно. Односторонне тентирование отверстий не допускается.
10. Зазор паяльная маска - КП (ламели):
- для КП отверстий – 0,1 мм по контуру;
- для ламелей 0,05 мм (0,025*)по контуру, либо групповое освобождение;
- для контура печатных плат - 0,2 мм по контуру;
- минимальная ширина перемычки в ПМ – 180 мкм (если меньше выполнять групповое освобождение).
*- требует дополнительного согласования
Данные краткие КТН являются неофициальным справочным документом и не отражают в полном объеме требований для обеспечения технологичности при производстве печатных плат.
Подробный документ:
Рекомендуемые конструктивно-технологические нормы могут быть высланы по официальному запросу.
Приложение 2 к инструкции.
Необходимые данные из cad-программ для монтажа печатных плат
Х-координата - центр координат компонента по оси Х.
Y-координата - центр координат компонента по оси Y.
Поворот - поворот компонента на плате при монтаже.
Тип - название оболочки компонента (1206, QFP160 и т.д.).
Значение - значение компонента ( 1.1k, 100nF, BC123A и т.д.).
Ссылки - ссылки компонента на плату ( R1, C33, IC5, D11 и т.д.).
Сторона - сторона на которой монтируется компонент ( TOP, BOTTOM ).
Важно , чтобы вся информация для одного компонента из CAD размещалась на одной строке.
Если CAD-файл включает избыточную информацию, нет необходимости её удалять.
Если Ваша CAD-программа не в состоянии создать один информационный список для всех данных, можно использовать два отдельных файла, сгруппированных по ссылкам компонентов на плату.
Например :
CAD-файл1 -- C1 1206 100Nf
CAD-файл2 -- C1 X-коорд. Y-коорд.
Координаты центров компонентов выражаются в миллиметрах и через (.), например:123.25, допускается вывод этой информации в mils и через запятую.
Также допускается вместо значения угла поворота (90., 180., и т.д.) использовать коды.
Пример информационного файла импортированного из CAD-программы.
RefDesign ator | PartLabel | PinCount | Side | MountTYPE | Rot | X | Y |
C1 | 0805_X7R_25V_5%_100nF | 2 | BOTTOM | SMD | 180 | 17,78 | 138,113 |
HL1 | AL307BM | 2 | TOP | THROUH | 180 | 207,01 | 2,54 |
D1 | XC4006E-4PQ160 | 160 | TOP | SMD | 0 | 17,78 | 127 |