- Главная
- Оборудование для печатных плат
- Оборудование для поверхностного монтажа
- Технологии производства плат и поверхностного монтажа
- Инструмент для печатных плат и Запасные части
- Материалы и Химикаты для печатных плат и поверхностного монтажа
- Гальваническое оборудование
- Лабораторное и аналитическое оборудование
- Сервис и техническое обслуживание
- Как нас найти
- Начало раздела
- Главный технолог
- Технологии производства
- Консультации
- Контакты
Металлизация отверстий печатных плат
В процессе металлизации отверстий печатных плат выделяют 3 этапа:
- подготовка отверстий (обеспечивает удаление замазывания -desmear, и условие формирования торцевого контакта – прямой или обратный подтрав -etch-back);
- формирование проводящего подслоя на диэлектрике в просверленных отверстиях;
- гальваническое наращивание основного слоя меди, требования к которому изложены в п.2.3.4. ГОСТ 23752.
НТД о металлизации
По IPC H:d (aspect ratio) определяется, как отношение толщины (печатных плат) к минимальному диаметру просверленного отверстия (диаметру сверла).
По отечественному ГОСТ 23 751 -86 - H:d (или обратная величина - γ) определялась, как отношение толщины (печатных плат) к минимальному диаметру металлизированного отверстия, т.е. как минимум на 0,05 мм меньше (в вышедшем ему на замену ГОСТ Р 53429-2009) упоминание об «aspect ratio» отсутствует вообще.
Примечание. Тем не менее для достаточно глубокого понимания содержания статей и документов надо понимать, что отечественная норма соответствовала меньшей норме по IPC, особенно для малых диаметров (например H:d=20:1 или γ=0,05 по отечественным НТД для диаметра сверла 0,15 мм соответствует H:d=13,5:1 по IPC).
Еще один параметр, характеризующий металлизацию отверстий – распределение наносимой меди по длине отверстия (TP – англоязычная аббревиатура). Этот параметр позволяет оценить возможность техпроцесса металлизации (особенно для малых диаметров отверстия, использующих прямую металлизацию) наносить достаточную толщину столба металлизации без неадекватного сужения просвета отверстия. К сожаления отечественные НТД никак не специфицируют эту величину. На рис. 94 показаны два варианта оценки распределения:
- по IPC –наиболее точный;
- оперативный (TPMIN), часто используемый технологами – практиками для быстрой оценки.
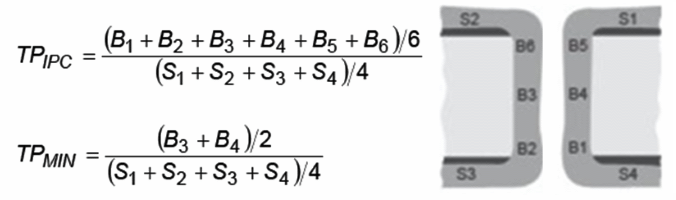
ГОСТ 23752 специфицирует минимально допустимую среднюю толщину металлизации для двухсторонних печатных плат – 20 мкм, для многослойных печатных плат – 25 мкм.
Подготовка отверстий
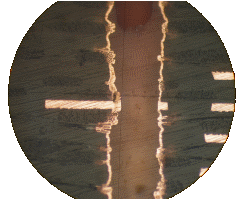
Известны 3 метода подготовки отверстий:
- Перманганатная обработка (дешевая и относительно эффективная, но имеет ограничения по маркам ДЭ – совсем не травит фторпласт и плохо работает с полиимидом).
- Плазмохимическая подготовка (требует сложного инженерного обеспечения и высоко квалифицированного персонала). Для стеклотекстолита при длительном воздействии или выборе агрессивных режимов по частоте сильно утравливает ДЭ, образуя внутри отверстия «щетку» стеклянных волокон (рис.95). При этом столб металлизации частично заполненный кончиками стекловолокон приобретает увеличенное, по сравнению со сплошной медью сопротивление.
- Травление в составах с плавиковой ( или др. концентрированной) кислотой (устаревший и очень вредный для персонала метод, сегодня практически не применяется в реальном производстве).
Химмеднение и прямая металлизация.
Эти химические процессы (в них не присутствует воздействие внешних источников тока) формируют проводящий подслой на диэлектрике в просверленных отверстиях, по которому впоследствии производят гальваническое наращивание меди. При этом реализуется один из основных параметров печатной платы: соотношение толщины печатной платы к минимальному диаметру сверления (H/d) при формировании достаточной толщины слоя пластичной гальванической меди на стенке отверстия. В современных высокоплотных прецизионных печатных платах это соотношение достигает 10…12/1 (а в наиболее сложных печатных плат и 20/1) – для сквозных отверстий и 1,0 - 1,2/1 (макс 1,5/1) – для глухих отверстий. Главной задачей, которая выполняется в результате этих процессов, является формирование надежных торцевых контактов.
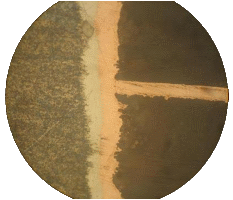
При химмеднении в торцевом контакте металлизированного отверстия печатной платы гальваническая медь, формируемая в процессе металлизации отверстия, контактирует с фольгой внутренних слоев через прослойку осадка химической меди. Эта прослойка является самым слабым местом. По своей природе химически осажденная медь имеет рыхлую пористую структуру, способную поглощать влагу, газы, растворы электролитов и обладающую низкой механической прочностью.
Разрушение торцевого контакта при эксплуатационных воздействиях (в основном, температурных, термоциклических) происходит, как правило, по слою химической меди. Одним из главных условий формирования надежного торцевого контакта является эпитаксиальное сращивание слоя гальванической меди столба металлизации и торца фольги, которое возможно только сквозь слой химической меди толщиной не более 0,8…1 мкм (рис.96). Таким образом, при реализации процесса химического меднения возникает довольно трудно разрешимая технологическая коллизия:
- с одной стороны, для надежного покрытия всей поверхности столба отверстия хочется нанести побольше химмеди (сделать ее потолще);
- с другой стороны, толщина химмеди для формирования надежного торцевого контакта и обеспечения эпитаксиального сращивания с фольгой слоя не должна быть больше 1- 1,5 мкм.
Не хочу сказать, что эта коллизия является неразрешимой, но она требует очень глубокого изучения химизма процессов и значительных усилий для поддержания составов рабочих растворов и режимов на всех стадиях процесса.
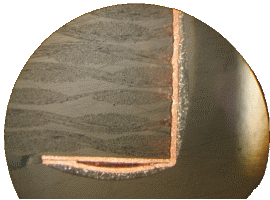
на поверхности печатных плат,
связанное с утолщенным слоем химмеди.
Нарушение адгезии «меди к меди»
Для примера могу привести ситуацию, которая на меня, как на человека, не имеющего фундаментального химического образования, произвела неизгладимое впечатление.
В техпроцессе химической металлизации, согласно которому мы работали много лет, ионы меди были связаны в комплексы с участием сегнетовой соли (калий-натрий виннокислый). Как выяснилось, в составе поставляемой соли могут находиться соли нескольких изомеров винной кислоты, из которых только один является комплексообразователем. Его массовая доля в производимом в РФ продукте не регламентируется и поэтому может меняться. Однако от содержания именно этого изомера напрямую зависит скорость осаждения, а следовательно, толщина слоя химической меди. При завозе каждой новой партии соли начинались проблемы с надежностью торцевых контактов. Понадобилось достаточно много времени и усилий, чтобы разобраться в причинах, отработать методики входного контроля соли. Но это всего лишь один пример одного из этапов многостадийного сложного процесса.
Проблема адгезии, связанная с увеличением толщины рыхлого, механически не прочного, газонаполненного слоя химической меди проявляется не только в районе торцевого контакта, но и по всей поверхности проводников наружного слоя, так как прослойка химмеди лежит везде, где на фольгу наносится гальваническая медь ( рис. 97).
К дополнительным недостаткам химмеднения можно отнести наличие в составе рабочих растворов и, следовательно, в сливах вредных (с очень низкими ПДК), трудно извлекаемых веществ (формалин, сегнетова соль, ЭДТА и др.).
Прямая металлизация лишена основного недостатка химмеднения – наличия дополнительного слоя между фольгой и гальванической медью. Проводящий подслой, формируемый в процессе прямой металлизации, на заключительной стадии процесса лежит только на диэлектрике. Естественно при условии его правильной реализации ( рис.98).
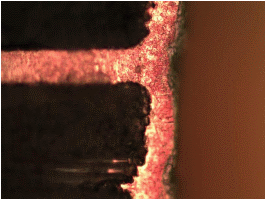
через прямую металлизацию
в районе торцевого контакта
Кроме того к преимуществам прямой металлизации следует отнести отсутствие выделения водорода («питинга»), приводящего к образованию дефектов металлизации отверстий, особенно малого диаметра. Еще одним преимуществом является возможность реализации процесса прямой металлизации на высокопроизводительных конвейерных установках.
Переход от химической к прямой металлизации не обязательно связан с приобретением новой линии. Поскольку процесс прямой металлизации имеет меньшую стадийность, линии химической металлизации достаточны для реализации этого процесса.
Существующие процессы прямой металлизации по типу формируемых токопроводящих слоев можно разделить на 3 типа. Приведу краткие их характеристики:
1. Токопроводящий слой на основе графита. Применяется в основном для двухсторонних печатных плат. Техпроцесс компактен, дешев, высокопроизводителен. Суть процесса состоит в обработке печатных плат в тонкодисперсной суспензии графита. Частицы графита, имеющие размеры от нескольких десятков до нескольких сотен нм, адсорбируются на обрабатываемой поверхности и после высушивания приобретают проводимость за счет наличия металлической связи между атомами углерода. Углеродные частицы с медной поверхности удаляются микротравлением.
К преимуществам процессов на основе графита следует отнести их простоту, компактность, относительную дешевизну, высокую производительность. Успех процесса во многом зависит от равномерности распределения частиц по размерам в суспензии. Иными словами, частички должны быть преимущественно одного размера. Однако в ходе эксплуатации суспензии они слипаются и укрупняются. Такие укрупненные частицы дают рыхлый, отслаивающийся осадок. Адгезия гальванической меди к нему недостаточна. Поэтому периодически необходимо проводить анализ суспензии графита, который требует соответствующего оборудования. Технологическое окно процесса, обеспечивающего достаточно высокую надежность, очень узкое, что предполагает выполнение частых корректировок и удорожает данную операцию. Поэтому процесс применяется, как правило, для изготовления двухсторонних печатных плат и многослойных печатных плат бытовой техники, эксплуатирующихся в аппаратуре с коротким жизненным циклом.
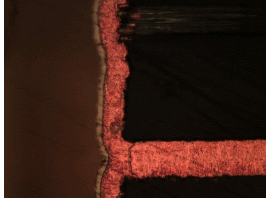
торцевого контакта при нарушении
технологии промежуточной промывки
2. Токопроводящий слой на основе палладия. Этот метод наиболее распространен для изготовления многослойных печатных плат, в том числе спецприменения. Его идея заключается в том , что уже на стадии активации палладий настолько диспергирован по поверхности, что образует сплошную проводящую (с полупроводниковой проводимостью) пленку без последующей стадии химического осаждения меди.
Существуют техпроцессы палладиевой прямой металлизации с разными механизмами формированиями коллоидных растворов. При этом адсорбция мицелл или промоутерного слоя происходит как на диэлектрике, так и на меди, и требует удаления этих слоев с поверхности меди активной промывкой и микротравлением для того, чтобы между фольгой и гальванической медью не оставалось разделительного слоя ( рис. 99 ).
Распределение (отношение толщины меди в центре к толщине на входе в отверстие) в процессах прямой металлизации не более 75%. Надежно реализуемое H:d (aspect ratio) для сквозных отверстий 8:1, для глухих – 1,2:1.
3. Проводящий слой на основе проводящего полимера.
Проводимость в этом методе создается путем полимеризации мономеров органических веществ, причем из-за особенностей процесса полимеризации проводимость возникает только на участках диэлектрика внутри отверстия. Для этого метода стадия микротравления и промежуточной промывки не требуется, и поэтому процессы на основе проводящих полимеров обеспечивают высокую прочность связи Cu-Cu в торцевых контактах, которая сохраняется и после многократных термовоздействий. Однако проводимость этих слоев также сравнима по величине с проводимостью слоев на основе графита и сульфида Pd. Этот метод перспективен, инновационен, но мало освоен за рубежом. И совсем не освоен в РФ.
Суммируя выше изложенное к преимуществам прямой металлизации следует отнести:
- 1. Отсутствие в рабочих растворах формалина и сильных комплексообразователей.
- 2. Короткое время создания поверхностной проводимости диэлектрика - ~15 сек.
- 3. Используемые растворы обладают высокой стабильностью и не требуют «разгона» после технологических перерывов.
- 4. Отсутствие разделительного слоя в торцевом контакте.
- 5. Возможность создания поверхностной проводимости для широкого диапазона ДЭ.
- 6. Удовлетворительная рассеивающая способность для Н:d≤10 для сквозных отверстий.
- 7. Меньший объем химических анализов.
- 8. Нет меди в сливах.
Что же выбрать: химмедь или прямую металлизацию?
Если процесс химмеднения освоен, стабилен, понятен и нормально работает в течение долгого времени, по-видимому, надо следовать рекомендации: «От добра - добра не ищут». Если же речь идет о модернизации или создании нового производства, а планируемая номенклатура и объемы изготовления печатных плат требуют существенного снижения производственных издержек, и конструкция выпускаемых печатных плат (в первую очередь H:d) допускает использование прямой металлизации, тогда, наверное, стоит остановиться на одном из процессов прямой металлизации.
Следует учитывать, что проводящие слои предварительной металлизации, формируемые всеми тремя описанными ранее методами прямой металлизации, имеют относительно маленькую толщину и полупроводниковую проводимость, при этом дальнейшее наращивание толщины при гальваническом процессе происходит от входа в отверстие к его середине. Что ограничивает максимально достижимое распределение меди и соответственно максимально достижимое H:d.
Некоторые процессы палладиевой прямой металлизации позволяют увеличивать проводимость слоя предварительной металлизации за счет увеличения плотности засева поверхности диэлектрика палладиевыми мицеллами. Это несколько улучшает распределение меди в отверстии, но при этом увеличивает расход палладия и при всем при том не позволяет достичь проводимости как у химмеди. Так при технологии химмеди, слой предварительной металлизации имеет металлическую проводимость и дальнейшее наращивание толщины происходит в направлении перпендикулярном стенок отверстия. Это позволяет реализовать высокие величины параметра распределения меди в отверстии и соответственно реализовывать существенно более высокие, чем при прямой металлизации значения H:d.
В настоящее время в производстве многослойных печатных плат для создания проводящего слоя в отверстиях используется как химмеднение, так и прямая металлизация. Проводимость диэлектрических стенок отверстий создается уже на этапе активации, которая присутствует и в процессе химмеднения, и в процессе прямой металлизации. Однако в процессе прямой металлизации стадия химического осаждения меди исключается. В связи с этим прямая металлизация лишена недостатков, свойственных химмеди, и конечно же, предпочтительна для простых многослойных печатных плат с H:d до 10:1. Продолжающееся же использование химического меднения для изготовления относительно простых многослойных печатных плат в значительной степени связано с консервативностью производителей и их нежеланием отказываться от хорошо отлаженного процесса.
При этом на большинстве производств, в особенности тех, которые заботятся о перспективах своего развития, по-видимому целесообразно принять следующую стратегию организации на этапе гальванического нанесения:
Технологические подходы
Поскольку соотношение печатных плат с большим и малым H:d (aspect ratio) соответственно ≈20%/80% целесообразно иметь 2 линии металлизации:
Высокопроизводительную - с прямой металлизацией (палладиевой или проводящими полимерами) для печатных плат с «малым» H:d≤ 8:1 (т.е для изготовления больших количеств относительно простых печатных плат). Такая линия обеспечит текущую программу и может быть основой контрактного производства.
Относительно малопроизводительную - с химмедью, с гальваническим заполнением отверстий, для печатных плат с «большим» H:d (до 20:1), вибрацией, безвоздушным перемешиванием (сопла Вентури), принудительной подачей раствора по площади заготовки (для изготовления сложных, инновационных, но достаточно дорогих печатных плат). Такая линия позволит разработчикам реализовать инновационные идеи и сократит цикл прототипирования и сроки реализации новых разработок в целом.
Основная гальваника.
Гальваническое осаждение меди было открыто в 1838 г. русским академиком Б.С. Якоби. С этого времени меднение широко применяется во многих отраслях промышленности.
Вообще существует большое разнообразие рабочих процессов гальванического меднения, но в производстве печатных плат, как правило, используются процессы на основе кислых сульфатных электролитов, обладающие следующими преимуществами:
- - высокая рассеивающая способность;
- - обеспечение высокой пластичности осаждаемой меди;
- - минимальное воздействие на фоторезисты (при работе по полуаддитивному процессу);
- - простота и технологичность в эксплуатации;
- - приемлемая стоимость материалов, применяемых для приготовления и корректирования электролита (включая контроль и корректировку по содержанию добавок).
Количественно процессы гальванической металлизации описываются законами Фарадея, согласно которым масса вещества высадившегося при электролизе прямо пропорциональна количеству электричества. Коэффициентом пропорциональности является теоретический электрохимический эквивалент (К), связанный с постоянной Фарадея
F = 96 500 кл\(г x атом)
Для двухвалентной меди К = 1,186 г\кл. На практике теоретический эквивалент достигается очень редко. Электричество расходуется на побочные процессы на электродах. Отношение действительно осажденной массы к предполагаемой называется выходом по току.
В РФ распространено нанесение основного гальванического покрытия в 2этапа:
- - так называемая – «гальваническая затяжка» -≈ 6 мкм;
- - основная гальваника – 15 ÷20 мкм.
Такая стратегия удобна по двум причинам:
- - к двум указанным процессам предъявляются технически противоположные требования (в затяжке главной задачей является рассеивающая способность, обеспечивающая хорошее прокрытие столба отверстия, а в основной гальванике главной задачей является пластичность, обеспечивающая технологическую и эксплуатационную стойкость);
- - нанесение коррозионно более стойкого гальванического покрытия «затяжкой» поверх тонкой предварительной химической металлизации, позволяет увеличивать допустимые межоперационные промежутки, что очень удобно в реальном производстве.
Рассеивающая способность и пластичность медного покрытия, обеспечиваются добавками в электролите, концентрацию которых необходимо контролировать и поддерживать в определенных пределах.
Контроль концентрации добавок проводят с помощью ячейки Хулла или методом вольтамперометрии (CVS).
А) Для осуществления быстрого исследования и тестирования работоспособности различных электролитов, применяемых в гальваническом производстве, используется электрохимическая ячейка с угловым катодом - ячейка Хулла.
Ячейка Хулла представляет собой гальваническую ванну объёмом ≈ 250 мл, в которой катод расположен к аноду под углом ≈ 50⁰. При электроосаждении в такой ячейке при средней плотности 2 А/дм2 (соответствует силе тока 1А) на катодной пластине реализуются плотности тока от 0,1 А/дм2 на дальнем от анода участке до 8-9 А/дм2 на ближнем к аноду участке.
Основные функции ячейки Хулла:
- - быстрое определение возможных причин неполадок работы электролита на основании полученного покрытия;
- - определение рассеивающей способности электролита по току (качественная характеристика состава электролита по основным компонентам);
- - определение рассеивающей способности электролита по металлу (зависимость толщины покрытия от плотности тока);
- - определение расхода блеско образующих добавок, проверка качества блеско образователей;
- - определение количества блеско образующих добавок, необходимых для корректирования электролита; выбор рабочего диапазона плотностей тока, определение внешнего вида покрытий в зависимости от плотности тока;
- - оценка степени загрязнения электролита ионами тяжёлых металлов и органическими веществами, проверка качества основных химикатов;
- - сравнительная характеристика различных блеско образующих добавок.
При тестировании электролита в ячейке Хулла с целью определения возможных причин дефектов покрытия, он должен быть откорректирован по содержанию основных компонентов (на основании данных химического анализа) и по рН (при необходимости). Электроосаждение проводится обычно в течение 10-20 минут на заранее подготовленную пластину. Сила тока составляет в большинстве случаев 1 А.
Кроме определения возможных причин брака, ячейка Хулла может использоваться для определения количества блеско образующих добавок, необходимого для корректировки электролита. Для этого в подготовленную для исследования пробу вводится небольшое количество добавки (10-15% от исходной концентрации). Если при этом удовлетворительный результат не получен, то снова вводится добавка в том же количестве, и так до получения блестящего покрытия. После этого суммарное количество введенной добавки пересчитывается из объема ячейки на объем процессной ванны.
Еще одной важной функцией ячейки Хулла может быть входной контроль качества добавок, поступающих на производство, а также сравнительная характеристика различных добавок, в изобилии предлагаемых производителями в современных условиях рынка. В этом случае, используя свежеприготовленные электролиты, можно оценить (или сравнить) качество покрытия, получаемого при различных плотностях тока при применении данной добавки, определить ее примерный расход, стабильность процесса и, таким образом, установить соответствие добавки техническим условиям, сравнить экономические показатели (качество-расход-цена) различных добавок.
Б) Последнее время все более широкое распространение получают процессы использующие для контроля концентрации добавок циклическую вольтамперометрию.
При работе с электролитами меднения отверстий печатных плат для получения блестящих покрытий особое внимание следует уделять анодам. Обычно используют аноды марки АМФ, не дающие шлама и содержащие 0,03‒0,06 % фосфора. В настоящее время промышленностью выпускаются шариковые аноды, которые загружаются в процессные ванны в титановых корзинах.
Допустимо применять аноды из чистой рафинированной меди (99,9 %), содержащей не более 0,1 % примесей.
Взвешенные частицы шлама обычно являются причиной грубого шероховатого осадка. Для предотвращения попадания шлама в электролит рекомендуется аноды помещать в чехлы из кислотостойкого материала и вести непрерывную фильтрацию электролита.
Пластичность — это основной критерий качества осаждаемого медного покрытия.
Чем это вызвано?
Известно, что в структуре печатных плат имеются материалы. ТКР которых может отличаться на несколько порядков. Под воздействием температур при изготовлении, монтаже и эксплуатации платы возникают растягивающиеся усилия по высоте столба металлизации, то есть вдоль металлизированного отверстия. Это растяжение, в зависимости от конструкции платы, может составлять до 8-10 %. Чтобы столб медного покрытия внутри отверстия выдержал это растяжение без разрыва, медь должна обладать достаточной пластичностью. В первую очередь это относится к печатных плат поверхностного монтажа, так как они в процессе групповой пайки в конвеерных печах подвергаются нагреву до 200-260 С⁰.
При выполнении процесса электроосаждения меди очень важно следить за чистотой электролита. Загрязнение электролита органическими веществами — основная причина дефектов металлизации в том числе связанных с уменьшением пластичности. Источниками органических загрязнений являются:
- - фоторезисты;
- - продукты разложения добавок.
Кстати первая причина при «тентинг»-методе исключается, поскольку при этом методе изготовления гальваническое меднение наносится на плату без фоторезиста , что является одним из достоинств метода.
Причины разложения добавок:
- - Попадание в электролит подготовительных растворов микротравления, содержащих перекисные соединения, что является следствием плохой межоперационной промывки.
- - Поляризация анодов, которая может возникать при избытке хлоридов в электролите, а также при высокой анодной плотности тока и использовании нефосфористых анодов. Дефекты, возникающие при загрязнении электролита органическими веществами:
- - неравномерное покрытие;
- - точечная коррозия;
- - отсутствие блеска;
- - уменьшение пластичности.
Для получения пластичных осадков в мировой практике используют сернокислые электролиты меднения со специальными добавками.
Для исключения дефектов покрытия, вызванных накоплением органических загрязнителей, производится очистка электролита.
В производствах для очистки рабочих растворов обычно используют угольную ткань. АУСФ — это активированная угольная ткань, имеющая высокую сорбционную емкость, благодаря чему время очистки электролита от органических примесей существенно сокращается. Ткань АУСФ значительно упрощает технологию очистки электролитов от органических примесей (не требуется предварительной промывки и прокаливания ее при высокой температуре). Процесс очистки электролитов прост и удобен, может производиться на работающей ванне в непрерывном режиме.
Надежность печатных плат во многом определяется пластичностью металлизации отверстий. Поэтому контроль пластичности медных осадков – важный фактор технологического обеспечения надежности межсоединений.
В настоящее время наибольшее распространение получили два метода контроля пластичности.
А) Контроль на растяжение с использованием разрывной машины.
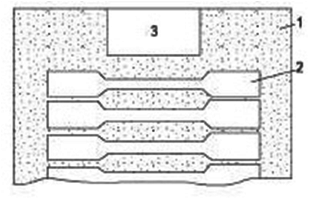
тест образцов для испытаний
на разрывной машине
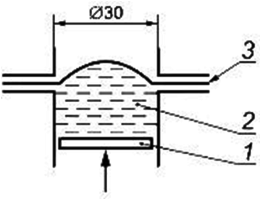
гидравлическое выдавливание.
1 - поршень; 2 - вода; 3 - испытуемый образец
IPC 6012 специфицирует допустимую пластичность на уровне не хуже 12% (14% для изделий аэрокосмического применения).
Это традиционно понятный метод, но не очень удобный в производстве, так как требует проведения дополнительных фотолитографических операций.
В) Дуктилометрический метод (контроль гидравлическим выдавливанием по п.2.4.4. IPC 650.)
Может быть использован, как оперативный метод в производстве, так как не требует фотолитографии, но требует наличия специального оборудования и ПО. Результат не соответствует значениям растяжения плоских медных образцов (Закону Гука).
Оба метода включены в ГОСТ 9.317-2010 ЕСЗКС. «Покрытия металлические. Методы измерения пластичности».
При изготовлении печатных плат гальваническое наращивание меди (20-30 мкм, в исключительных случаях до 70 мкм) осаждают из сернокислых, а также пирофосфатных и борфтористоводородных электролитов. Цианистые ванны дают наилучшие результаты, но используются крайне редко ввиду их высокой токсичности.
Размещение электродов сказывается на распределение плотности тока и, соответственно, на распределение толщины металлизации по площади заготовки. Как правило, по краям заготовки толщина выше из-за краевого эффекта. Для обеспечения равномерности покрытия по площади заготовки в конструкцию ванны вводятся проводящие и ДЭ экраны, обеспечивающие выравнивание силовых линий в промежутке между катодами и подвеской.