- Главная
- Оборудование для печатных плат
- Оборудование для поверхностного монтажа
- Технологии производства плат и поверхностного монтажа
- Инструмент для печатных плат и Запасные части
- Материалы и Химикаты для печатных плат и поверхностного монтажа
- Гальваническое оборудование
- Лабораторное и аналитическое оборудование
- Сервис и техническое обслуживание
- Как нас найти
- Начало раздела
- Главный технолог
- Технологии производства
- Консультации
- Контакты
Формирование отверстий печатных плат
Для начала хочу вернуться к определению печатных плат из «Википедии» в части наличия в печатных плат отверстий, с помощью которых происходит объединение проводников на слоях в единую электрическую схему.
«Печатная плата содержит монтажные отверстия и контактные площадки для монтажа выводных или планарных компонентов. Кроме того, в печатных платах имеются переходные отверстия для электрического соединения участков фольги (проводящего рисунка), расположенных на разных слоях платы. Именно с помощью этих элементов происходит коммутация отдельных электронных компонентов в единую схему.»
Объединение в единую электрическую схему происходит в два этапа:
- - формирование монтажных и переходных отверстий;
- - металлизация отверстий.
В последнее время появилось множество новых инновационных технологий изготовления печатных плат. Таких как технология послойного наращивания (рис. 76), технология заполнения отверстий (рис. 77),технология формирования отверстий в любом слое (ALIVH) (рис.78), технология ALOX (рис.79).
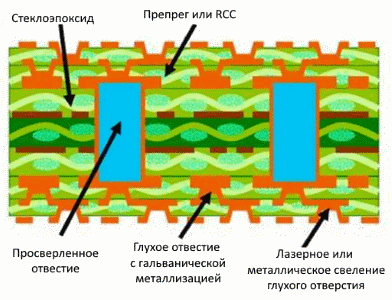
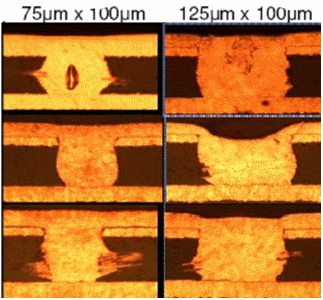
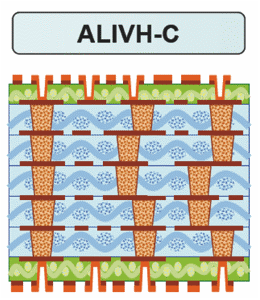
Формирование отверстий в любом слое
Однако наиболее распространенной в РФ пока является технология на базе формирования сквозных монтажных и переходных отверстий, а также межслойных переходов (рис.80).
Первый этап этой технологии - а именно, формирование отверстий мы и рассмотрим в этом разделе.
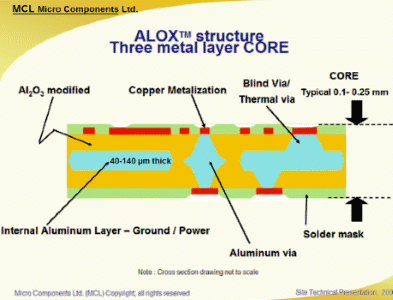
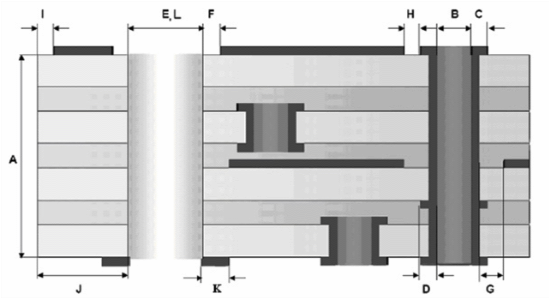
Механическое сверление отверстий
Механическое сверление выполняется твердосплавными сверлами при этом рекомендуемая линейная скорость резания (для стеклотекстолита) – 2,5 м/сек., является фундаментальной величиной, и на ее базе рассчитываются рекомендуемые обороты сверления в зависимости от диаметра сверла.
Nоб/мин =150х10³/πDмм
Так например для Ø сверла 0,2мм рекомендуемые обороты N= 220тыс. об/мин.
При этом следует иметь в виду, что указанные в документах прозводителей станков, сверл, ламинатов рекомендуемые режимы сверления следует рассматривать только как первый шаг в подборе режимов. В реальном производстве они будут зависеть от сочетания многих факторов в том числе от:
- -марки используемых ламинатов;
- - марки используемых инструментов;
- - станков и оснастки;
- - нормативов по стойкости сверл и допустимого числа переточек;
- - качества станка для переточки и квалификации персонала выполняющего переточкку и т. д.
Задача технолога – выбор оптимального режима, опираясь на рекомендуемые режимы, фундаментальную величину линейной скорости резания, подачи –(рекомендуется применять режим: толщина меди в слое на 1 оборот сверла), рекомендации по стойкости сверла ( «закон 12 дюймов» ,который рекомендует переточку или замену сверла после того, как оно просверлит суммарную толщину равную 12-ти дюймам). Для переточки твердосплавных сверл необходим специальный станок, аттестованный по точности исполнения геометрии сверла. В производстве прецизионных многослойных печатных плат, с уменьшением диаметров сверл и допусков на изменение диаметра, переточка используется ограниченно.
Износ сверл приводит к недопустимому изменению диаметра сверления. Изготовленные на заводе сверла, как правило, не требуют проверки. Перезаточенные сверла необходимо проверять в первую очередь на правильность заточки вершины сверла. При этом, конечно же, главным критерием будет являться качество просверленных отверстий. Режим должен быть подобран таким образом, чтобы минимизировать дефекты сверления.
Основными из которых являются следующие:
А). «Шляпка гвоздя» (рис. 81).
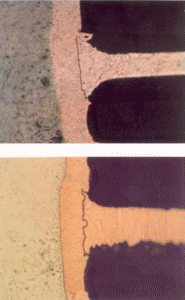
Деформация внутренних слоев меди на стенках отверстия, эта деформация принимает форму «шляпки гвоздя». Существует несколько типов «шляпки гвоздя». Наиболее распространенный тип наблюдается в отверстиях малого диаметра – термомеханические «шляпки гвоздя». Термомеханическая «шляпка гвоздя» возникает из-за чрезмерного нагрева, большого давления сверла и втягивания меди в направлении движения сверла. Сверла диаметром свыше 0.75 мм чувствительны и к термомеханической и к механической «шляпке гвоздя». Только механическая «шляпка гвоздя» характеризуется деформацией в одном направлении. Эта «шляпка гвоздя» как правило, сопровождается сильным замазыванием торца (наволакиванием смолы на торец) меди.
Причина:
- 1. Неправильно выбранная подача.
- 2. Неправильно выбранные обороты.
- 3. Неправильно выбранная скорость вытягивания сверла.
- 4. Недополимеризованная смола.
- 5. Засорение сверла.
- 6. Высокотемпературное растяжение меди / большое количество медных слоев.
- 7. Неправильно выбранный материал верхней или нижней прокладки.
Действия по исправлению:
- 1. Определить тип «шляпки гвоздя» (ШГ): односторонняя или двухсторонняя .
- 2. Односторонняя ШГ: уменьшить подачу или увеличить обороты. Двухсторонняя ШГ: уменьшить обороты или увеличить подачу.
- 3. На малых диаметрах сверел скорость вытягивания может быть уменьшена.
- 4. Недополимеризированный препрег будет допускать возникновение ШГ.
- 5. Контроль сверла от засорения. Засорение канавок (режущих кромок) может быть обусловлено конструкцией сверла, прилипающим алюминием верхней накладки на входе, недополимеризацией смолы, неправильно выбраным материалом нижней прокладки или недостаточным вакуумом при отсосе стружки.
- 6. Высокотемпературное растяжение медной фольги увеличивает образование ШГ, чем выше растяжение меди, тем более выраженным будет ШГ.
- 7. Некоторые виды верхнего и нижнего подкладочного материала прилипают к режущим кромкам сверла, приводя к ухудшению качества стенок отверстий.
Б). Замазывание (наволакивание смолы на торцы) (рис.82)
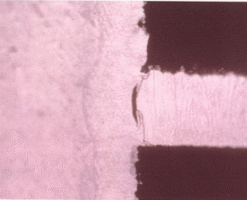
(наволакивание смолы на торцы)
Смола перемещенная из базового материала стенок отверстия в процессе сверления покрывает обработанный торец внутреннего слоя. Существует два типа замазывания смолой, «шляпки гвоздя», и термомеханическое замазывние, которое возникает из-за чрезмерного нагрева, но незаметно внешне (чисто снаружи). Механическое замазывание – значительное покрытие внутреннего слоя, цвета соответствующего используемой смолы.
Причина:
- 1. Недополимеризованная смола материала печатных плат.
- 2. Чрезмерные обороты.
- 3. Чрезмерная подача.
- 4. Слишком низкая подача при высоких оборотах (выделяется тепло).
- 5. Глубокое врезание в подкладку.
- 6. Тупое сверло / выкрашивание режущей кромки сверла.
- 7. Недополимеризованная смола в материале подкладки.
- 8. Не до конца проведенный процесс удаления наволакивания (слабый дисмиринг).
Действия по исправлению:
- 1. Проверить цикл прессовки, параметры нагрева и режимы обработки рассматриваемой партии.
- 2. Проверить обороты. Примечание: наиболее распространенный способ определения правильных оборотов – рассчитать об/мин для данного диаметра основываясь на рекомендуемой линейной скорости резания с учетом твердости обрабатываемого материала.
- 3. Очень большая величина подачи во время сверления создает сильное покрытие смолой торца внутреннего слоя меди. Это замазывание имеет тот же цвет, что и базовый материал. Обычно это имеет место при сверлах диаметром более 0.75 мм. Если подача слишком велика, надо уменьшать подачу пошагово на 20% до устранения проблемы.
- 5. Чрезмерная глубина захода сверла в подкладку вызывает ненужный нагрев, как результат – замазывание.
- 6. Тупые сверла или сверла с выкрашиванием режущей кромки создают нагрев, также проявляющийся в замазывании. Сверла должны быть заменены когда достигается рекомендуемое значение их стойкости. Выкрашивание может объясняться неправильным обращением, некорректным значением подачи, неправильно выбранным материалом накладки.
- 7. Недополимеризованная смола в подкладочном материале переносится на проводники внутренних слоев.
- 8. Недостаточный по времени или слишком слабый по интенсивности процесс удаления замазывания, неадекватно удаляет замазывание. Проведите необходимую корректировку или увеличьте время обработки, или если используется травление плазмой произведите необходимые изменения по составу газа мощности и/или времени в вакуумной камере.
В). Выкрашивание (образование ореола) поверхности смолы на стенках отверстия. (Рис. 83)
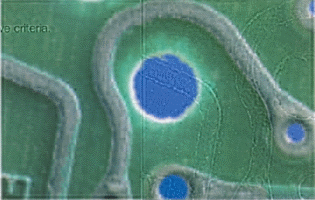
поверхности смолы
Повреждение смолы вблизи стенки отверстия. Повреждение может быть поверхностное или выкрашивание стенки отверстия. Поверхностное выкрашивание видно без помощи изготовления шлифов, и обычно сопровождается разрывом наружного слоя меди. Выкрашивание стенки отверстия происходит внутри отверстия между проводящими слоями и для его выявления обычно требуется изготовление шлифа.
Причина:
Поверхностные выкрашивания возникают из-за:
- 1. Высоких значений подачи.
- 2. Неправильно выбранного материала верхней накладки – мягкий или тонкий материал не достаточно хорошо поддерживает сверло, позволяя сверлу создавать заусенец на поверхности платы, который отделяет основную медную фольгу от смолы, и создает выкрашивание или трещины в смоле.
- 3. Неправильно выбранного подкладочного материала – если подкладочный материал не достаточно хорошо поддерживает многослойных печатных плат на выходе, материал будет вдавливаться вместо того чтобы сверлиться, создавая заусенец на выходе, который обычно образует повреждения под медью.
Повреждения стенки отверстия возникают из-за:
- 1. Чрезмерного нагрева или механического напряжения, возникающего, когда высокие скорости шпинделя используются с низкими значениями подачи.
- 2. Недополимеризованной смолы материала печатных плат.
- 3. Забивания рабочей части сверла смолой, медью, или материалом накладок\подкладок.
- 4. Неправильно выбранного материала подкладки.
Действия по исправлению:
- 1. Отрегулировать значение подачи, уменьшать ступенчато на 20% до устранения повреждений.
- 2. Сменить материал накладки на такой, который будет поддерживать сверло на входе.
- 3. Сменить подкладочный материал на более твердый. Подкладочный материал по твердости должен соответствовать материалу который сверлится.
- 4. Настроить обороты и изменить значение подачи до приемлемого уровня.
- 5. Проверить правильность процесса полимеризации, время выдержки при температуре, и цикл охлаждения.
- 6. Если выполненные шаги 1 – 5 не дали результат, причина забивания рабочей части объясняется :
- a. Материал накладки (алюминий) прилипает к сверлу (на малых диаметрах) препятствуя отводу стружки.
- b. Высокие обороты и низкие значения подачи приводят к нагреву смолы и её прилипанию к сверлу.
- c. Конструкция сверла, маленький диаметр сверла с недостаточной величиной канавки приводят к её забиванию.
- 7. Используйте более твердый подкладочный материал.
Г). Клиновые пустоты приводящие к «прометаллизации» на стадии металлизации отверстий. (рис. 84)
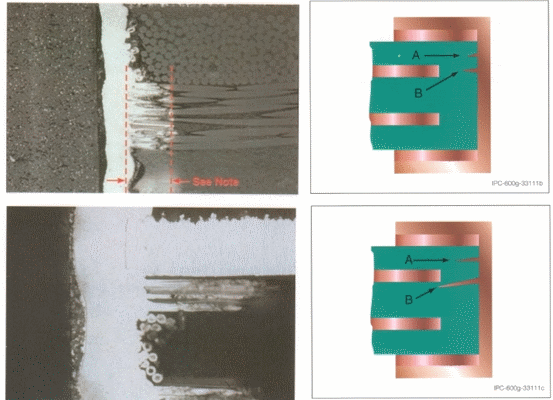
Распознается по поперечному шлифу как периферийное поникновение меди внутрь материала ламината. Похоже на «розовое кольцо», но с клиньями меди в местах выкрашенного материала, прилегающего к медному столбу металлизации отверстия.
Причина:
- 1. Неправильно выбранные режимы сверления.
- a. Условия сверления.
- b. Подача / скорость сверления.
- c. Материал верхней / нижней подкладки.
Корректирующие действия:
См. раздел «Выкрашивание (образование ореола) поверхности смолы на стенках отверстия».
Д). Заусенцы на наружных слоях фольги (рис 85.)
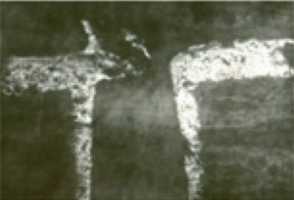
Деформация медной фольги на внешних слоях платы. Заусенцы могут быть как на входе, так и на выходе, и могут быть видны на обеих сторонах платы.
Причина:
Заусенцы на входе
- 1. Отсутствие верхней накладки.
- 2. Очень тонкая верхняя накладка для используемых режимов сверления.
- 3. Стружка скапливающаяся между накладкой и платой.
- 4. Слишком большое отверстие в прижимной пятке шпинделя, позволяющее вакууму поднимать тонкий подкладочный материал.
- 5. Мягкий материал накладки.
Заусенцы на выходе
- 1. Стружка скапливающаяся между платами, или между платой и нижней подкладкой.
- 2. Материал подкладки очень мягкий для материала который сверлится.
- 3. Стружка забивает рабочую часть сверла.
Исправляющее действие:
Заусенцы на входе
- 1. Использовать накладку при сверлении всеми диаметрами сверл.
- 2. Заменить материал накладки на более толстый или более жесткий.
- 3. Очистить поверхность платы и накладки от пыли и стружки перед сверлением.
- 4. Заменить материал накладки на более жесткий или увеличить силу отсоса.
- 5. Использовать прижимную пятку с меньшим диаметром отверстия.
Заусенцы на выходе
- 1. Очистить подкладку, стол станка и обе стороны каждой платы перед установкой на стол. (Все материалы должны быть протерты мягкой тканью перед установкой на стол станка).
- 2. Заменить подкладочный материал на более твердый.
- 3. Отрегулировать забивание сверла (отверждение смолы, материал подкладок, накладок и т.д.).
Е). Рассовмещение
Совмещение соответствующих внутренних слоев с другими внутренними слоями или просверленными отверстиями. Рассовмещение – это выход за допустимый предел одного или более внутренних слоев относительно остальных слоев или просверленных отверстий. Вопросы рассовмещения быль подробно рассмотрены ранее в разделе, касающегося коррекции размерных изменений. Однако печатных плат 3-4 классов точности по ГОСТ Р 53429-2009 могут изготавливаться без применения техники коррекции размерных изменений путем устранения причин рассовмещения указанных ниже.
Причина:
Слой относительно слоя:
1. Неправильное использование или неправильная пробивка баз фотошаблона.
Слой относительно отверстия:
- 1. Положение базовых отверстий стола станка программно неправильно связано с базовым отверстиям платы.
- 2. Неправильные перемещения рабочих органов станка (короткие или длинные).
- 3. Шпиндель имеет слишком высокое биение.
- 4. Сверло отклоняется на входе или внутри сверлящегося пакета.
Действия по исправлению:
Слой относительно слоя:
- 1. Сделать фотошаблон пригодный для использования.
- 2. Откорректируйте фотошаблон с учетом компенсации размерных изменений.
Слой относительно отверстия:
- 1. Проведите перенастройку станка.
- 2. Проведите наладку станка для перемещения рабочих органов на правильные дистанции.
- 3. Замените цангу в шпинделе или замените шпиндель.
- 4. Измените материал накладки, скорость и подачу, или конструкцию сверла.
- 5. Настройте размерность программы сверления.
Примечание: Сначала откорректируйте совмещение слоев относительно друг друга, затем откорректируйте совмещение отверстий относительно слоев.
Информация и данные содержащиеся выше конечно могут быть использованы как надежный инструмент для устранения неисправностей, но все рекомендации даны без каких-либо гарантий. Поскольку различные производства и конструкции печатных плат обладают уникальными требованиями к процессу создания печатных плат, решение о применении или использовании приемлемых советов и идей упомянутых выше остается за пользователем. Нельзя определить совет или рекомендацию которые подходили бы всем пользователям.
Отдельная тема - формирование глухих отверстий. Поэтому хочу более подробно остановиться на ней.
С увеличением плотности рисунка печатных схем и широким применением BGA появилась необходимость получения глухих металлизированных микроотверстий. Изготовители печатных плат вынуждены осваивать технологии изготовления многослойных печатных плат с глухими металлизированными микропереходами, имеющими определенные конструктивно-технологические особенности.
Сверление глухих отверстий
Конструктивно-технологические особенности глухих отверстий и структуры многослойных печатных плат
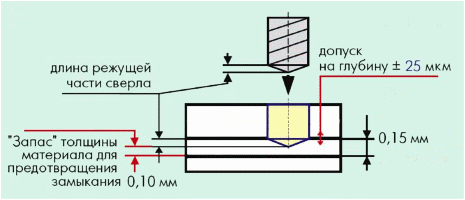
Глухие отверстия многослойных печатных плат предназначены для соединения наружных сигнальных слоев с одним или несколькими внутренними слоями платы.
Сверление глухих отверстий на заданную глубину до определённого слоя имеет принципиальное технологическое ограничение: – для получения качественной металлизации глухих отверстий необходимо, чтобы отношение H/d (отношение глубины сверления к диаметру отверстия) было не более 1:1 (оптимально- 0,8:1). Это означает, что чем больше глубина сверления глухого отверстия (и диэлектрический зазор между слоями), тем больше должен быть диаметр такого отверстия.
Для простого варианта получения глухих отверстий с наружного слоя на следующий ( второй) глубина сверления будет складываться из толщины наружной фольги (обычно 18 мкм), толщины диэлектрического зазора между слоями (0,1- 0,2 мм), толщины фольги второго слоя (18-35 мкм) и примерно половины конусной режущей части сверла (25-50 мкм) (рис.86).
Толщина диэлектрика между вторым и третьим слоями (под сверлом) должна обеспечивать отсутствие их замыкания между собой с учетом прохода части конусной режущей кромки сверла (25-50 мкм) сквозь фольгу нижнего слоя , допуска на толщину диэлектрика (слои 1-2) и допуска на точность выполнения глубины сверления (для современных сверлильных станков допуск по оси Z - ± 25 мкм и менее).
Регулировка глубины сверления на современных сверлильных станках осуществляется, как правило, двумя способами:
- - контактным методом, когда отсчет глубины сверления ведется от момента касания поверхности печатных плат ( возникновения электрического контакта). Для этого поверхность должна быть проводящей. Этот метод обеспечивает точность по глубине до 10 мкм.
- - бесконтактный метод , когда отсчет глубины сверления реализуется программно с помощью оптической линейки, установленной на суппорте вертикальной подачи станка. Этот метод обеспечивает точность по глубине до 15 мкм.
Практика исполнения глухих отверстий показывает, что толщина
диэлектрика, следующего за слоем, до которого сверлятся глухие отверстия, должна быть не менее 0,14-0,20 мм (например 2-3 прокладки препрега 1080) (при использовании ламинатов для наружных слоев). При этом диэлектрический зазор между дном глухого отверстия и следующим слоем получается примерно 100-150 мкм, что вполне достаточно для обеспечения необходимого сопротивления изоляции.Для выбора структуры многослойных печатных плат с глухими отверстиями с наружного слоя на второй (наиболее простой вариант) - рассмотрим два основных типа структуры:
- 1) структура с фольгой на наружном слое (рис.87.1);
- 2) «парная структура» (рис.87.2) – ламинат для 1-2 слоев.
В первом варианте (рис.87.1.) наружные слои получают припрессовыванием фольги через необходимое количество прокладок препрега к пакету из ламинатов (слои со второго по предпоследний). Данная структура меньше подвержена короблению. В этом конструктивном варианте имеется возможность использования более тонкой фольги (5-9 мкм) для получения прецизионного проводящего рисунка наружных слоев.
Существенным недостатком данной структуры является дополнительное влияние на разброс толщины диэлектрика между слоями 1-2 и последний-предпоследний). Из-за изгиба и перекоса плит пресса и прессформ (особенно, если они не очень толстые) он может достигать 50 мкм и более. Соответственно усложняется проблема получения оптимальной глубины сверления глухих отверстий. Чтобы гарантировать отсутствие замыкания слоев, в этом случае толщина диэлектрика следующего слоя под дном глухого отверстия должна быть не менее 0,2-0,25 мм.
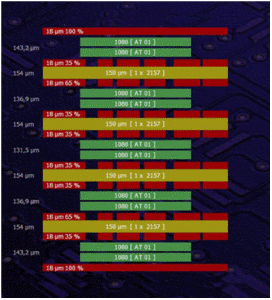
печатных плат
с фольгой на наружных слоях
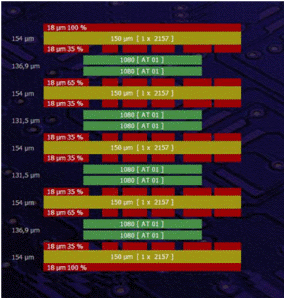
многослойных печатных плат
При втором варианте («парная структура») (рис.82.2) для наружных слоев используются фабричные ламинаты, которые имеют меньший разброс по толщине (±10 %), что существенно облегчает сверление на заданную глубину. Для данной структуры, как отмечалось выше, для надёжного диэлектрического зазора под дном глухого отверстия достаточно толщины 0,14-0,20 мм.
Для повышения надежности можно дополнительно на этапе подготовки производства сделать освобождения в слое меди под дном глухого отверстия, если это позволяет топология проводящего рисунка соответствующего слоя.
Для оценки качества и контроля глубины сверления глухих отверстий целесообразно предусмотреть на технологических полях заготовки и между фрагментами плат тестовые контактные площадки, на которых производится предварительная пробная сверловка.
Опыт сверления глухих отверстий не показал каких-либо преимуществ от использования специализированных сверл (конусных и «трапециевидных») ни при самом сверлении, ни при последующей металлизации.
Формирование глухих отверстий
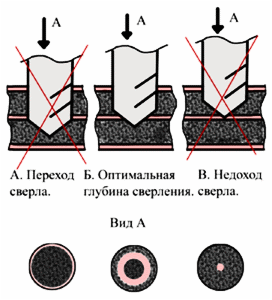
Вид глухих отверстий при визуальном контроле
Теперь еще раз подробнее о сверлении на заданную глубину.
При контактном сверлении отсчет глубины сверления глухого отверстия начинается при касании сверла наружной фольги пакета многослойных печатных плат. Поэтому в качестве материала для накладок можно использовать только неметаллические материалы (меланин, гетинакс).
Наиболее важной задачей является определение оптимальной глубины сверления глухого отверстия. Она складывается из расстояния между фольгами наружного и заданного слоя, толщин фольг этих слоев и половины конусной режущей части сверла (25-50 мкм).
При достижении сверлом заданного слоя возможны три варианта дальнейшего его прохождения (рис.88).
Вариант А (переход сверла (рис.88А))- сверло конусной режущей частью полностью проходит фольгу заданного слоя. При этом варианте затруднен визуальный контроль глубины сверления, виден только тонкий боковой торец фольги внутреннего слоя. Значительно сокращается диэлектрический зазор до следующего слоя, так как длина конусной режущей части сверла составляет 50-100 мкм (в зависимости от диаметра сверла). Многолетний опыт сверления глухих отверстий свидетельствует так же о том, что при этом варианте происходит сильное замазывание (наволакивание смолы) внутреннего торца слоя с последующими проблемами его очистки при подготовке под металлизацию. Это можно объяснить сильным разогревом и износом особенно места перехода конусной режущей части сверла в цилиндрическую при выполнении глухих отверстий.
Вариант В – недостаточная глубина сверления (рис.88В): сверло доходит до фольги, частично углубляется в неё, не пронизывая её до диэлектрика. Визуально при контроле мы видим розовую точку в центре отверстия на темном фоне диэлектрика. При этом варианте после металлизации мы получим практически точечный контакт, что недостаточно для формирования надежного электрического соединения при дальнейшей металлизации.При этом разброс допусков на глубину сверления, реализуемую станком, и толщины диэлектрика может приводить даже к тому, что на части отверстий будет недоход сверла до фольги заданного слоя, возникнут обрывы связей и брак всей платы уже на стадии выходного контроля.
Вариант Б - оптимальная глубина сверления (рис. 88Б): сверло частично проходит фольгу заданного слоя, примерно половина конусной режущей части сверла выходит в низлежащий диэлектрик (25-50 мм).
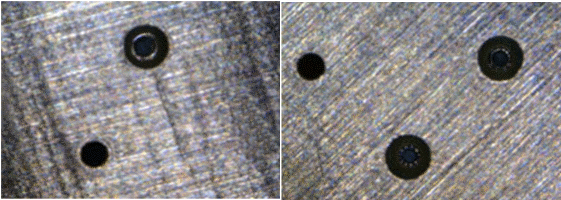
на сл.3 10-ти сл. многослойных печатных плат) (х 200)
При визуальном контроле мы видим достаточно широкое розовое кольцо. С учетом погрешности сверления (по оси Z) и допусков на толщину проходимых диэлектриков размер медного кольца внутреннего торца в глухих отверстиях по полю групповой заготовки может меняться (рис. 89). Но практически исключаются варианты А (переход) и вариант В (недоход сверла).
Поперечное сечение медного торца за счет формирования его под углом конусной частью сверла будет иметь значительную площадь, достаточную для обеспечения надежного электрического контакта. При этом происходит минимальное наволакивание смолы на внутренний торец.
По всем этим причинам вариант Б при сверлении глухих отверстий (с частичным прохождением фольги заданного слоя) является наиболее оптимальным с точки зрения выбора глубины сверления, надежности электрического соединения и обеспечения необходимого сопротивления изоляции.
В таблице 8 приведены параметры глухих отверстий (с наружного на следующий слой) и используемых материалов (толщина фольги наружных и внутренних слоев – 18 мкм).
Параметры мм | Толщина диэлектрика (сл.1-2) | ||||
0,1 | 0,125 | 0,15 | 0,20 | 0,25 | |
Суммарная толщина диэлектрика и фольг наруж. и внутр. слоя (мм) | 0,136 | 0,161 | 0,186 | 0,236 | 0,286 |
Глубина сверления Н (мм) | 0,16 | 0,185-0,19 | 0,22 | 0,27 | 0,33 |
Диаметр отверстия d (мм) | 0,2 | 0,2-0,25 | 0,25 | 0,3 | 0,35 |
Диаметр КП (мм) | 0,45 | 0,45-0,5 | 0,50 | 0,55 | 0,6 |
Отношение Н/ d (≤1) | 0,8 | 0,93-0,95 | 0,88 | 0,9 | 0,94 |
Половина длины конус. режущей части сверла (мм) |
25 | 25-30 | 30 | 35 | 40 |
Толщина диэлектрика следующего слоя (сл. 2-3) (мм) |
0,15 (или 2 пр.1080) |
0,15 (или 2 пр.1080) | 0,15 (или 2 пр.1080) | 0,20 (или 3 пр.1080) | 0,20 (или 3 пр.1080) |
Средняя величина диэлектр. зазора между дном глух. отв. и фольгой след.слоя (мм) | 0,125 | 0,120- 0,125 | 0,120 | 0,165 | 0,160 |
Поскольку при сверлении глухих отверстий сильно изнашивается конусная часть сверла, целесообразно для обеспечения качества глухих отверстий установить предельное количество отверстий на 1 сверло – 500-700 отверстий . Режимы сверления (подача, скорость вращения) глухих отверстий аналогичны режимам сверления сквозных отверстий для каждого диаметра сверла
Оборудование для механического сверления.
Для реализации операции механического формирования отверстий «РТС Инжиниринг» предлагает линейку сверлильных станков ф. Pluritec. Подробные технические характеристики этих станков можно найти на нашем сайте www. rts-engineering.ru . Я бы хотел подробнее остановиться на аспекте обеспечения точности на этих станках. Ф. Pluritec предлагает тест для контроля позиционной точности расположения центров отверстий, так как она является одним из ключевых моментов, обеспечивающих изготовление печатных плат 6-7классов точности по ГОСТ Р 53429-2009 с хорошим % выхода годных (рис.90).
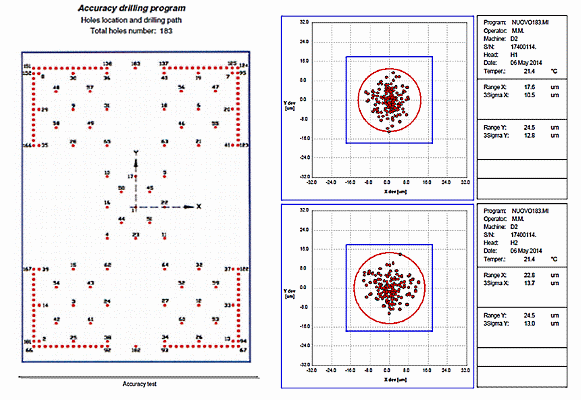
Оценка точности сверления – методика, которой заключается в том, что по одной и той же программе сверлятся большое количество отверстий на образце 400х550 мм и на специальной машине замеряется отклонение центров просверленных отверстий от идеального (запрограммированного) положения. Кол. отверстий ок. 200 (183), что соответствует оценке на уровне 3σ (99,73% или≈ 1 случай выхода за пределы допуска на 150 отверстий).
По этому тесту станки Pluritec укладываются в ±12-13 мкм, что позволяет прогнозировать ±18мкм на уровне 6σ.
Примечание. «6σ» - это метод управления процессами, основанный на статистической оценке данных процесса.
К методикам замера точностных параметров оборудования этот термин не имеет ни какого отношения. Ведь для достоверной (с точки зрения формальной математики) оценки на уровне 6σ (99,99966% или≈ 1 случай выхода за пределы допуска на 300 000 образцов) необходимо сверлить и тестировать нереально большое кол-во отверстий (несколько сотен тысяч) .
Теперь о том, почему я считаю проблемы обеспечения точности важными для прецизионных печатных плат. В условиях устойчивого тренда миниатюризации РЭА в целом возникает все большая потребность в прецизионных печатных плат, где для формирования переходных отверстий используются сверла все меньшего и меньшего диаметра. Сверла диаметром менее 0,35 мм имеют резко увеличивающуюся склонность к отклонению от вертикали при столкновении с элементами армирования диэлектрика печатных плат (например стекловолокнами). Причем эта склонность тем больше, чем меньше диаметр сверла и чем больше диаметр стекловолокна. Это связано в первую очередь уменьшением частичек порошка твердого сплава из которого спекаются сверла.
В своей практике я не встречал случаев использования в реальном производстве механического сверления сверлами диаметром менее 0,15 мм. Использование таких сверел требует очень высоких оборотов шпинделя. Например для сверла диаметром 0,1 мм по формуле на стр.141 расчетные обороты шпинделя должны быть ≈ 500тыс. об\мин. Такие обороты технически очень трудно реализовать. Поэтому представленные некоторыми фирмами производителями сверла диаметром 0,05 мм и даже 0,02 мм следует считать скорее демонстрацией возможностей производства, нежели образцами реальных инструментов.
Еще несколько слов о сверлильно-фрезерных шпинделях (именно шпинделях, а не станках). На мой взгляд сверлильно-фрезерный шпиндель плохо сверлит и плохо фрезерует. Дело в том , что к сверлильным и фрезерным шпинделям предъявляются разные и технически абсолютно противоречивые требования. Сверлильный шпиндель должен обеспечивать высокие обороты и держать аксиальные нагрузки, фрезерный шпиндель должен в первую очередь держать радиальные нагрузки, при существенно более низких требованиях к оборотам. Сверлильные шпиндели, как правило, делаются на воздушных подшипниках, которые очень плохо держат радиальные нагрузки. Фрезерные же шпиндели делаются на шариковых подшипниках, которые не могут обеспечивать высокие обороты.
Решая использовать якобы универсальные сверлильно-фрезерные шпиндели, надо очень четко представлять имеющиеся у них ограничения по реализации оптимальных режимов и сверления и фрезерования. В этой связи мне очень нравится решение ф. Pluritec примененное в модели C-FLEX, оснащенной в стандартном исполнении двумя независимыми шпинделями сверлильным – до 180тыс. об/мин и фрезерным - до 80тыс. об/мин (когда работает один – другой запаркован в нерабочем положении). На мой взгляд этот станок наиболее подходит для оснащения многономенклатурного производства прецизионных печатных плат.
Инструмент для механического сверления.
В качестве инструмента для механического сверления «РТС Инжиниринг» предлагает твердосплавные сверла ф. Union Tools, выдерживающие сверления 10-12 тыс отверстий и выпускаемые следующими сериями:
- Серии MD/MC/MV/MCV: Предназначены для сверления сквозных и глухих микроотверстий диаметром до 0,25 мм.
- Серия ST: Сверла серии ST принадлежат к типу Straight (прямое сверло). Данная серия предлагает экономичные решения в сверлении широкого спектра материалов.
- Серии UC/UV/NT: Сверла данных серий принадлежат к типу Under Cut (увеличенный диаметр режущей кромки) и предназначены для получения высококачественных сквозных и глухих отверстий диаметром от 0,3 до 1,6 мм.
- Серия SX: Сверла серии SX принадлежат к типу Under Cut (увеличенный диаметр режущей кромки). Сверла данной серии специально разработаны для сверления слотов.
Лазерное сверление.
Как уже говорилось ранее в связи с устойчивым трендом миниатюризации и появлением инновационных структур печатных плат (рис.91), требующих отверстий малого диаметра, которые невозможно реализовать механическим сверлением с одной стороны; и способности лазерной техники производительно формировать отверстия малого диаметра ( с увеличением диаметра формируемых отверстий производительность лазерных устройств резко падает) – лазерные станки устойчиво заняли свою нишу в индустрии производства инновационных печатных плат.
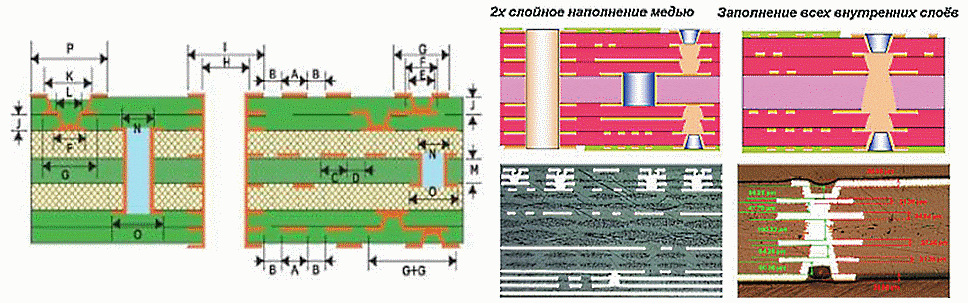
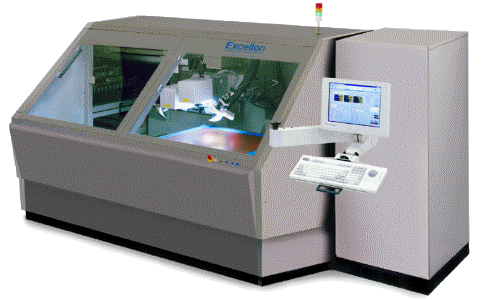
COBRA ф. Excellon.
При изготовлении печатных плат используются 3 типа лазеров:
- Газовый лазер (СО 2 ) -10,2мкм ( сверление ДЭ);
- Твердотельный лазер (YAG) -1,06мкм (сверление меди);
- Эксимерный лазер (УФ) – 0,355мкм ( универсальный - сверление и ДЭ, и меди). При этом когда мы говорим «сверление» - имеем в виду процесс испарения материала (абляцию).
Последние два отличаются лишь наличием у эксимерного лазера устройства утроения частоты. «РТС Инжиниринг» представляет на российском рынке установку лазерного сверления COBRA ф. Excellon (рис. 92), оснащенную т.н. гибридным (СО2+УФ) лазером.
Принцип действия гибридного лазера заключается в следующем (рис. 88):
Длина волны в УФ лазера (1064 : 3) 355 нанометров. Это называется утроение частоты. - Длина волны 1064 производится с помощью твердотельного лазера из кристалла неодима. Его излучение затем проходит через кристалл утроения частоты для получения выходного УФ луча. Типичная длительность импульса твердотельного лазера этого типа составляет от 20 до 120 наносекунд. УФ лазер при 355 нм режет большинство материалов (в том числе и, в первую очередь , медь).
CO2 лазер излучая на длине волны 9600 нм режет только органические материалы и стекло. Но при этом его луч отражается от меди или других металлов. Большим преимуществом использования гибридной системы является "автоматический контроль глубины" , УФ лазер очень энергоэффективен и может быстро прорезать металл. СО2 лазер из-за высокой энергии в импульсе может удалить большое количество диэлектрика быстро и без термического повреждения. Но дойдя до низлежащего слоя меди автоматически остановится.
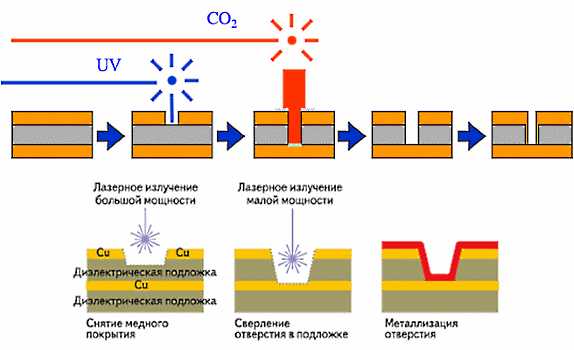
В конце цикла, коротким импульсом УФ лазера производится очистка отверстия, требуемая для качественной металлизации.
В связи с вышеизложенным гибридный лазер обладает рядом существенных технологических преимуществ:
- диаметр микроотверстий до 20мкм.
- Высокая точность.
- Нет опасности повреждения низлежащих слоев меди.
- Возможность испарения множества различных материалов
Альтернативой гибридному лазеру являются УФ пиколазер впервые представленный на рынке технологического оборудования для производства печатных плат ф. Шмоль и УФ лазер ф. LPKF.
Эти лазеры, как правило, используются на основной частоте 1064 нм с или без утроения частоты. При этом они будут резать медь и органические материалы, включая большинство диэлектриков. На этих длинах волн при использовании обычного лазера высока вероятность расслаивания стандартного материала FR4 на стеклоткани 1080, но при очень короткой длительности импульса этот эффект снижается.
Поскольку энергия импульса очень мала из-за их короткой длительности ( в «пикосекундном" лазере длительность импульса в тысячу раз меньше, чем у традиционных УФ лазеров), - значительно больше импульсов необходимо, чтобы удалить такое же количество материала. Так как этот лазер будет резать медь , также как и диэлектрик, - у него нет "автоматического контроля глубины". Глубина должна контролироваться по параметру инструмента – например, скорости формирования глубины отверстия , что выполнить очень сложно. Пико лазер может хорошо работать, при испарении или фрезеровании однородного материала, но когда дело доходит до печатной платы с FR-4 1080, 106 и т.д. задача становится проблемной, особенно в местах резки узлов стеклянного волокна и остановки на нижнем слое медной фольги без его повреждения.