- Главная
- Оборудование для печатных плат
- Оборудование для поверхностного монтажа
- Технологии производства плат и поверхностного монтажа
- Инструмент для печатных плат и Запасные части
- Материалы и Химикаты для печатных плат и поверхностного монтажа
- Гальваническое оборудование
- Лабораторное и аналитическое оборудование
- Сервис и техническое обслуживание
- Как нас найти
- Начало раздела
- Главный технолог
- Технологии производства
- Консультации
- Контакты
О некоторых конструктивно-технологических проблемах прессования многослойных печатных плат (Заметки практикующего технолога)
Автор: Илья Лейтес, главный технолог ООО "РТС Инжиниринг"
В статье предлагается единый подход к формированию конструктивно-технологических норм и методик контроля основных характеристик как при разработке, приемке, применении, так и в процессе производства многослойных печатных плат. Такой подход особенно важен в условиях динамично развивающейся среды контрактного производства, когда изготовитель печатных плат работает по документации, разработанной на другом предприятии, и в процесс изготовления и применения многослойных печатных плат вовлечены различные службы технического контроля.
Введение
Из общих соображений совершенно очевидно, что результирующая толщина и структура многослойной печатной платы (перечень составляющих прессования — слоев и листов препрега) связаны абсолютно однозначно. Однако на практике результирующая толщина, указываемая конструктором в сборочном чертеже многослойных печатных плат, очень часто не соответствует той толщине, которая физически реализуется после прессования пакета, набранного по спецификации. Это приводит к тому, что готовая многослойных печатных плат не может быть принята службами технического контроля. Анализ ситуации показывает, что конструкторы не всегда в состоянии выполнить адекватный расчет толщины с учетом всех конструктивно-технологических факторов, оказывающих на нее влияние.
Именно поэтому при подготовке производства многослойных печатных плат в ОАО НИЦЭВТ мы были вынуждены вводить обязательный проверочный расчет результирующей толщины. И в случае несоответствия расчетной толщины с указанной в конструкции приходится вести долгую процедуру переписки для согласования корректировок КД в этой части.
Это и послужило поводом для написания данной статьи в надежде, что разъяснения процессов, происходящих при формировании результирующей толщины многослойных печатных плат, помогут конструкторам более четко выпускать КД на многослойных печатных платах, что, в свою очередь, поможет сократить сроки их изготовления.
Связь результирующей толщины и структуры многослойных печатных плат
ГОСТ 23751-86 определяет толщину многослойных печатных плат как сумму толщин, входящих в конструкцию слоев, с учетом формулы из Приложения к ГОСТу на странице 11:
Нп = ∑Нс + (0,6…0,9)∑Нпр,
где Нс — толщина слоя многослойных печатных плат, Нпр — толщина прокладки (по стеклоткани).
Перечислим элементы конструкции, из которых складывается толщина печатной платы:
– сумма слоев ламината с учетом толщин диэлектрика и фольги (следует отметить, что в номенклатуре импортных материалов в обозначении указывается толщина диэлектрика, а в номенклатуре отечественных — суммарная толщина ламината (диэлектрик + фольга));
– сумма слоев препрега (склеивающих прокладок);
– дополнительная толщина меди, высаживаемая на поверхность наружных слоев при металлизации сквозных отверстий (почему-то очень часто конструкторы не учитывают эту добавку как при расчете суммарной толщины, так и при расчете плотности тока на проводниках наружных слоев). Эта толщина может достигать 30…50 мкм на каждом из наружных слоев в зависимости от режима и используемой химии, а в некоторых конструктивных вариантах многослойных печатных плат эти слои меди могут наноситься дважды, достигая величины, соответственно, 60…100 мкм, что вносит существенную поправку в результирующую толщину многослойных печатных плат;
– толщина паяльной маски. Здесь необходимо учитывать, что толщина сухой паяльной маски, как правило, бывает по 75 мкм с каждой стороны, а в случае использования жидкой паяльной маски дополнительная толщина лежит в интервале 20…30 мкм с каждой стороны. Как видим, разница существенная, и ее следует учитывать при расчете.
Теперь о самом главном. При прессовании происходит заполнение ожиженной смолой рельефа, образованного рисунком проводников внутренних слоев, и за счет этого происходит уменьшение толщины относительно арифметической суммы толщин составляющих структуры в твердом состоянии. Это уменьшение тем больше, чем больше рельеф, т.е. толщина фольги внутренних слоев, и чем менее насыщен рисунок. Степень насыщенности рисунка измеряется в процентах занимаемой площади проводников к общей площади заготовки с учетом рисунка технического поля. Современные САПРы оснащены инструментами, позволяющими вычислять эту величину.
При этом следует учитывать, что смолы, содержащейся в препреге, должно хватить для заполнения рельефа, иначе получим непропрессовку. (Формула, приводимая в ГОСТе и упомянутая в начале статьи, вводит коэффициент, учитывающий эти процессы, — 0,6—0,9, при этом, однако, не определяет методику выбора конкретного коэффициента для конкретной платы. Кроме того, использование в формуле толщины «по стеклоткани» представляется малообоснованной в контексте физического смысла.)
В принципе, расчет по указанному выше алгоритму можно выполнить вручную, однако это долгая и трудоемкая процедура. Тем более, что за рубежом давно разработаны и применяются специальные калькуляторы, позволяющие достаточно адекватно рассчитать толщину конкретной многослойной печатной платы с учетом ее структуры и степени насыщенности рисунка.
На производстве ОАО НИЦЭВТ уже в течение нескольких лет при проведении упомянутого выше проверочного расчета в процессе подготовки производства многослойных печатных плат успешно применяется калькулятор фирмы ISOLA MultiCal 5.2. Он позволяет также оценить, достаточно ли будет смолы для заполнения рельефа проводящего рисунка слоев при выбранном количестве прокладок препрега.
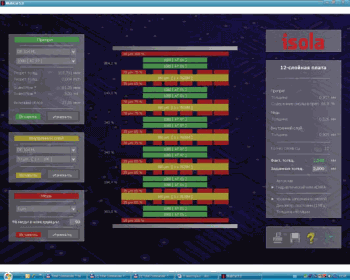
На рисунке 1 показан экран расчета результирующей толщины и достаточности смолы. Еще одна проблема, вроде бы носящая формальный характер, но, как выяснилось, способная оказывать существенное влияние на процедуру изготовления многослойных печатных плат, касается номенклатуры препрега. При работе с импортными материалами сегодня необходимо учитывать имеющую место и динамично нарастающую тенденцию увеличения разнообразия материалов, обладающих различными востребованными потребителем свойствами. Остается только дать совет конструктору (в особенности) и технологу следить за этим разнообразием. Чтобы не быть голословным приведу конкретные примеры.
Наиболее употребляемый в отечественных разработках препрег имеет номенклатуру 1080. Эта номенклатура определяет всего лишь форму плетения нитей стеклоткани, включенной в этот препрег, но при этом не определяет ни процентное содержание смолы, ни толщину препрега в исходном состоянии, ни его толщину после окончательной полимеризации — т.е. те факторы, которые напрямую влияют на результирующую толщину многослойных печатных плат.
Оказывается (думаю, для многих конструкторов и технологов это может стать откровением), эти характеристики определяются дополнительными буквами и цифрами, стоящими после номенклатуры 1080. Так, например, для стандартного FR4 марки DE104ML для препрега 1080 существуют две модификации — 1080 АТ 01 с толщиной 78,7 мкм и 1080 АТ 97 с толщиной 107,7 мкм, а для FR4 High Tg (с повышенной температурой стеклования) IS 420ML существуют модификации 1080 SR толщиной 78,7 мкм, 1080 RH толщиной 97,5 мкм и 1080 IS03 толщиной 72,3 мкм.
Если в заказе указана сокращенная номенклатура 1080, то в поставке может прийти любая из указанных модификаций. Дадут, что было на складе. И будут правы. Элементарный расчет показывает, что при использовании в стандартной 12-слойной многослойной печатной платы, содержащей DE104ML 1080 АТ 01 вместо DE104ML АТ 97, толщина изменится на 0,35 мм (что превышает поле допуска на толщину), а при использовании IS 420ML 1080 SH вместо IS 420ML 1080 SR03 толщина изменится на 0,1 мм (что соизмеримо с полем допуска). В этом случае вполне вероятен выход результирующей толщины многослойной печатной платы за пределы поля допуска, что, естественно, не позволит принять такие платы службам технического контроля.
В дополнение ко всему, использование разных модификаций препрега может привести к изменению волнового сопротивления (в случае, если оно учитывается при проектировании). Несколько слов стоит сказать и о подходах к установлению в КД допуска на толщину. Теория взаимозаменяемости и ГОСТ 23751 говорят о том, что допуск на результирующую толщину складывается из сумм допусков на толщины элементов, составляющих структуру. (Хочу обратить внимание заинтересованного читателя, что в предыдущих пунктах говорилось о расчете номинала без учета допусков).
Конечно, основной составляющей допуска на результирующую толщину будет вклад допусков на толщины ламината и препрега. Следует отметить, что практически у всех изготовителей этот допуск лежит в районе 10—12%. Дополнительный вклад вносят разброс толщины металлизации на наружных слоях, обусловленный краевыми эффектами в гальванических ваннах, и разнотолщинность, связанная с непараллельностью или деформацией плит пресса.
Вклад в разброс толщины, связанный с режимами прессования (температурой, временем и видом цикла), на их фоне крайне незначителен и занимает не более 20% поля допуска. Простой расчет показывает, что допуск на результирующую толщину для стандартных плат толщиной 1,6 мм не может быть меньше ±0,2 мм, а для более толстых — меньше ±0,3 мм (как, кстати, установлено ГОСТ 23751), и эти величины очень мало связаны с технологией (режимами) прессования.
Волевое желание некоторых конструкторов установить более жесткие допуски напоминает попытку поместить большее в меньшее, или приказом директора считать, что отныне 2*2 = 5. Для решения задачи ужесточения допусков на толщину необходимы либо технология селективного отбора исходных материалов (ламината и препрега), что приводит к существенному увеличению стоимости, либо использование прецизионного по толщине материала, который может быть поставлен любым солидным поставщиком, но изготавливается с использованием того же селективного отбора и имеет существенно более высокую цену.
В порядке лирического отступления должен отметить, что в течение своей достаточно продолжительной практики я часто сталкиваюсь с тем, что многие конструкторы не до конца осознают тот факт, что любая буква или цифра в КД (например, характеристика, размер, допуск) стоит денег, и чем более жесткие цифры закладываются, тем больших денег они стоят.
Методика измерения толщины
К сожалению, в отечественных стандартах методика измерения толщины отсутствует. В КД указан размер интегрально по всей поверхности платы, что приводит к возникновению разных подходов к измерению. Мне на практике приходилось сталкиваться с двумя.
В первом случае (на мой взгляд, правильный вариант) первый замер должен производиться в местах, где присутствуют все входящие в структуру многослойную печатную плату слои. Этот подход соответствует методике расчета, приведенной выше. Суммирование допусков всех составляющих структуру многослойной печатной платы соответствует допускам по ГОСТ 23751.
С другой стороны, после формирования рисунка наружных слоев на многослойной печатной плате появляются участки, где отсутствует медь наружного слоя, а иногда и ПМ, при этом разница толщины в таких местах по сравнению с местами, где все слои присутствуют, может составить от 0,1 до 0,25 мм, что соизмеримо с полем допуска и полностью разрушает логику расчета и прогнозирования номинала и допуска на толщину, и поэтому, с точки зрения физического смысла, является неправильным.
Проблемы изготовления многослойных печатных плат с заданным волновым сопротивлением (импедансом )
Стремление к увеличению вычислительной производительности аппаратуры формирует настоятельную потребность со стороны разработчиков узлов и печатных плат в изготовлении многослойных печатных плат с контролируемым импедансом (волновым сопротивлением).
В условиях отсутствия НТД на проектирование и расчет межсоединений таких многослойных печатных плат у разработчиков возникают затруднения по проектированию межсоединений с контролируемым волновым сопротивлением.
Это приводит к тому, что в условиях конкретного производства многослойных печатных плат, выполненная в точном соответствии с КД и требованием ГОСТов в части размерных характеристик, не соответствует заложенным (прогнозируемым) значениям волнового сопротивления.
Какие же основные технологические факторы необходимо учитывать при проектировании межсоединений с волновым сопротивлением:
1. Расчет волнового сопротивления возможен только для идеальных проводников. Поэтому для ПСИ по пункту измерения волнового сопротивления следует использовать только тест-купоны, на которых сформированы такие идеальные проводники (микрополоски, открытые и закрытые дифференциальные линии и т.д.).
Реальные проводники на рабочем поле многослойных печатных плат для ПСИ использованы быть не могут, так как содержат разветвления и переходные отверстия, существенно искажающие величину волнового сопротивления. Волновое сопротивление таких проводников может быть измерено как справочная величина.
2. Величинами первого порядка, влияющими на величину волнового сопротивления, являются ширина проводника, диэлектрическая постоянная диэлектрика и диэлектрическое расстояние до экрана.
2.1. При учете ширины проводников следует (особенно при формировании проводников субтрактивным методом) кроме допусков на ширину принимать в расчет и трапециедальность поперечного сечения (фактор травления) (см. рис. 2).
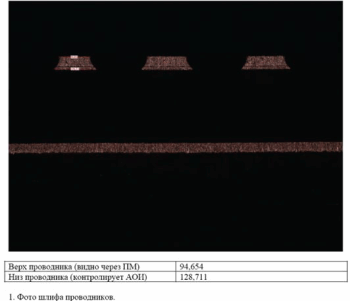
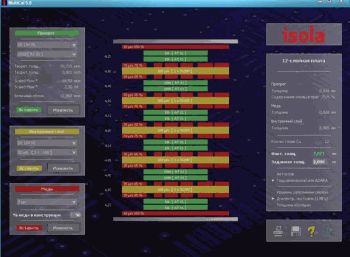
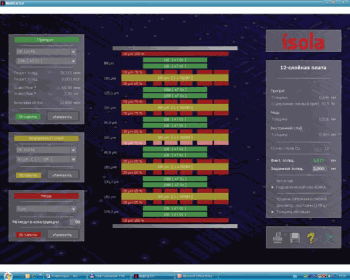
2.2. При учете ε необходимо иметь в виду, что стандартный FR4 имеет широкий допуск на величину = 4,5…5,5 для ламината и препрега в состоянии поставки. Одним из факторов, определяющим ε, является соотношение смолы и стеклоткани в диэлектрике.
В случае с препрегом, как было рассказано выше, при прессовании смола заполняет промежутки в рельефе проводников, и в диэлектрикрическом зазоре содержание смолы уменьшается относительно исходного состояния, соответственно, изменяется значение ε.
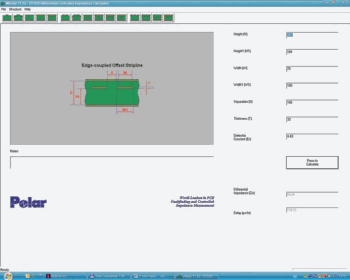
Это изменение будет зависеть от плотности рисунка, т.е. будет различным для разных слоев и для разных типов плат. Упомянутый ранее калькулятор Multi Cal позволяет, в том числе, рассчитывать изменение ε в конкретных структурах конкретных многослойных печатных плат.
2.3. Те же факторы влияют и на изменение диэлектрического расстояния между проводником и экраном. Multi Cal позволяет учитывать изменение и этого параметра в условиях конкретной структуры многослойных печатных плат. На рисунках 3 и 4 показаны экраны расчета значений ε и диэлектрического зазора.
3. Толщина проводника также влияет на волновое сопротивления (правда, как величина второго порядка). Здесь следует учитывать, что на производствах, которые используют для подготовки поверхностей проводящего рисунка химическую обработку, особенно структурное микротравление, толщина исходной фольги на внутренних слоях может уменьшаться на 2—3 (а иногда и более) мкм. Относительно исходной фольги 18 мкм это может вносить существенный вклад в изменение волнового сопротивления.
4. Как и в случае с толщиной, сумятица в подходах к проектированию межсоединений с волновыми сопротивлениями заставляет при подготовке производства проводить проверочный расчет волновых сопротивлений, указанных в КД заказчика.
Специалистами Производственного комплекса ОАО «НИЦЭВТ» (начиная со времени их работы на производственной площадке ИТМ и ВТ) опробованы множество методик расчета волнового сопротивления.
В результате мы остановились на калькуляторе CITS 25, который позволяет учитывать все приведенные выше факторы и при этом дает в результате расчета величины волнового сопротивления, совпадающие с получаемыми на нашем производстве. На рисунке 5 показан экран для выбора типа линии и расчета волнового сопротивления.
Заключение
В условиях динамично развивающейся системы контрактного производства, когда изготовитель печатных плат работает по документации, разработанной на другом предприятии, и в процесс изготовления и применения многослойных печатных плат вовлечены различные службы технического контроля, очень важными становятся единые подходы к формированию конструктивно-технологических норм и методик контроля основных характеристик как при разработке, приемке, применении, так и в процессе производства.
Надеюсь, содержание этой статьи поможет в формировании таких единых подходов к описанным, не тривиальным, на мой взгляд, проблемам, относящимся к разработке и изготовлению многослойных печатных плат.