- Главная
- Оборудование для печатных плат
- Оборудование для поверхностного монтажа
- Технологии производства плат и поверхностного монтажа
- Инструмент для печатных плат и Запасные части
- Материалы и Химикаты для печатных плат и поверхностного монтажа
- Гальваническое оборудование
- Лабораторное и аналитическое оборудование
- Сервис и техническое обслуживание
- Как нас найти
- Начало раздела
- Главный технолог
- Технологии производства
- Консультации
- Контакты
Разработка высокоэффективного покрытия химическим никелем
и иммерсионным золотом (ENIG) для обеспечения максимальной надежности.
Роберт Шпреманн; Рик Николс; Сандра Нелле; Атотек Дойчланд ГмбХ; Берлин, Германия.
Designing a High Performance Electroless Nickel and Immersion Gold to Maximize Highest Reliability.
Robert Spreemann; Rick Nichols; Sandra Nelle; Аtotech Deutschland GmbH; Berlin, Germany.
Авторский перевод ЛЕЙТЕСА ИЛЬИ, гл.технолога ООО РТС Инжиниринг.
АННОТАЦИЯ.
Последние самые высокие требования к надежности требуют высокоэффективного покрытия химическим никелем и иммерсионным золотом (HP ENIG). Новая спецификация IPC 4552A переориентировала отрасль в отношении коррозии никеля. Интерпретация существующей спецификации, которая оценивает коррозию по трем уровням, сложна и при неправильном толковании может привести к неверным отказам. Очевидный способ избежать возможных неверных толкований — полностью удалить все признаки коррозии. Способность к пайке и стойкость к коррозии под воздействием окружающей среды также являются очень важными факторами при обсуждении высокой надежности. Они будут оцениваться испытаниями на высокоскоростной сдвиг (HSS) и испытаниями в газовой камере. В дополнение к более строгим требованиям предъявляемым к высокой надежности, система HP ENIG должна демонстрировать хорошие характеристики базового уровня.
Целью этой статьи также является оценка того, есть ли какая-либо «добавленная стоимость» или непреднамеренные преимущества для HP ENIG. Примером этого может быть превосходное распределение золота и связанный с ним потенциал сбережения золота. Данные, полученные в рамках плана эксперимента (DOE), будут использоваться для оценки влияния характеристик химического никеля в сочетании с традиционным и не содержащим цианидов иммерсионным золотом на общепризнанные ожидания в отношении качества. Ожидается, что результаты будут практичными и пригодными для производственных решений, подкрепленными надежными данными, и есть надежда, что они могут развеять мифы в среде производства печатных плат (ПП).
Ключевые слова: высочайшая надежность, коррозия никеля, коррозионная стойкость, способность к пайке, черная прокладка.
Сокращения:
- ASR – в состоянии поставки.
- ENIG - химический никель иммерсионного золото.
- BS - сдвиг шарика.
- CBP – усилие отрыва шарика в холодном состоянии.
- CN - цианид.
- CNF - без цианидный.
- CV - коэффициент изменений.
- DOE - план экспериментов.
- HP - ENIG с высоким содержанием фосфора.
- МАГ - увеличение.
- МП – среднее содержание фосфора.
- Ni – никель.
- NSS - испытания на высокоскоростной сдвиг.
- P – фосфор.
- PCB - печатная плата.
- SEM - cканирующий электронный микроскоп.
- SST - тест на растекание припоя.
- Т – температура.
ВВЕДЕНИЕ И ПРЕДЫСТОРИЯ.
Печатные платы являются неотъемлемой частью многих электронных устройств. Спрос на более универсальные и мощные устройства критически влияют на размер таких устройств, что приводит к ужесточению требований к производителям печатных плат. Помимо неуклонного уменьшения числа контактов, электронные устройства также все чаще используются при более высоких рабочих температурах [1], а также в более суровых условиях окружающей среды. Таким образом, термическая стабильность паяного соединения, а также коррозионная стойкость становятся все более и более важными [1], что создает потребность в высокоэффективных покрытиях ENIG. А именно, специально разработанного процесса с использованием электрохимического никеля с высоким содержанием фосфора (> 9,5-13% мас.% P) и иммерсионного золота в качестве окончательного покрытия [2].
К сожалению, в нескольких исследованиях утверждается, что более высокое содержание фосфора в слое Ni должно приводить к ухудшению качества слоя по сравнению со слоем Ni со средним содержанием фосфора. Среди прочего утверждалось, что смачивание Ni ухудшается с увеличением содержания фосфора [3]. Или что прочность паяных соединений на сдвиг должна снижаться из-за появления слоя, богатого фосфором, на границе соединения [4] наряду с более высокой частотой хрупких разрушений на границе раздела никель-олово (Ni-Sn) [5]. Таким образом, цель этой статьи состоит в том, чтобы опровергнуть устаревшие данные и показать, что HP ENIG может удовлетворить самые высокие требования в отношении способности к пайке, надежности паяных соединений, прочности паяных соединений и коррозионной стойкости.
МЕТОДЫ, МАТЕРИАЛЫ И ЭКСПЕРИМЕНТАЛЬНАЯ ЧАСТЬ.
Материалы и очистка.
Используемые тестовые образцы были изготовлены производителем печатных плат. Подложки были очищены с помощью мокрого химического процесса перед ENIG.
Покрытие ENIG и технологический процесс.
Технологический процесс показан на рисунке 1.

Микротравление Гальванич. травл. Активация Химникель Иммерс. золотоРис. 1: Схематическое изображение технологического процесса ENIG.
Очищенная медная поверхность активировалась палладиевым катализатором и покрывалась в ванне для химического восстановления никеля с средним содержанием фосфора (Mid-P), а также в ванне для химического восстановления никеля с высоким содержанием фосфора (High-P). Последним этапом процесса было погружение испытательных плат со слоем High-P Ni в ванну с золотом без цианида (CNF Au), а испытательной платы со слоем Mid-P Ni — в обычную ванну с цианидом, содержащую золото (CN Au).
Толщина никеля и золота регулировалась в диапазоне 4-6 мкм никеля 40-60 нм золота.
Инструменты и методы измерения.
Однородность толщины слоя никеля и золота исследовали методом рентгенофлуоресцентного измерения (XRF). Образцы микрошлифов были изготовлены путем заливки эпоксидной смолы, с последующей шлифовкой и полировкой. Образцы исследовали также методами оптической микроскопии и сканирующей электронной микроскопии (СЭМ). Используемое оборудование для испытания прочности соединения алюминиевой проволоки представляло собой производственный автоматический клиновидный агрегат от поставщика материалов диаметром 25 мкм и разрывной нагрузкой прибл. 15 г. Производственный тестер растяжения использовал скорость растяжения 500 мкм/сек. Количество испытаний на образец составляло 30. Настройки параметров, использованные для соединения двух клиньев, можно увидеть в Таблице 1.
Таблица 1: Настройки параметров, используемые для испытаний проволочного соединения.
Параметр | Первое испытание | Второе испытание |
Сила (мГ силы) | 90 | 90 |
Время (мсек) | 25 | 25 |
Сила сцепления (к ньют) | 20 | 25 |
Условия испытания на отрыв холодного шарика и испытания на сдвиг шарика следующие. Используемые шарики припоя были из сплава SAC 305. Диаметр шарика 450 мкм. Используемый флюс относится к производственному типу (Tacky Fluх). Профиль оплавления показан на рис. 2.
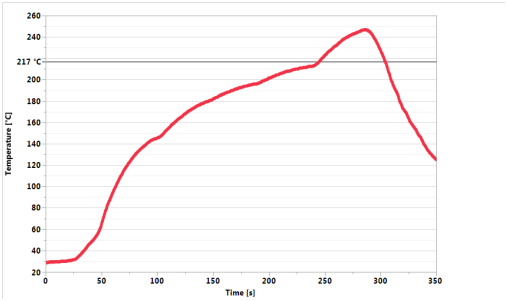
Рис. 2. Профиль бессвинцового оплавления, используемый для испытаний на отрыв холодного шарика и испытания на сдвиг; пик – T = 250°C.
Для всех испытаний на пайку использовалась производственная печь оплавления. Оплавление проводилось в атмосфере азота для испытания на отрыв холодного шарика, испытания на сдвиг шарика и высокоскоростного сдвига. Для испытаний использовались производственные испытательные платы с массивами шариковых выводов (BGA), определяемыми паяльной маской, с освобождением в ПМ 380 мкм. Настройки для испытания на отрыв холодного шарика, сдвига шарика и теста на высокоскоростной сдвиг можно найти в таблице 2.
Таблица 2: Настройки, используемые для холодного вытягивания шарика, сдвига шарика и испытания на сдвиг при высокой скорости.
Тест | Картридж | Скорость | Высота | Время задержки | Кол-во шаров |
Усилие сдвига в хол. сост. | 5 кг | 5 мм/с | 3-4 ч | 30 | |
Усилие сдвига шарика | 5 кг | 210 мкм/с | 50 мкм | 4 ч | 30 |
Высокоскоростной сдвиг | Картридж | 0,6 м/с | 20 мкм | 4 ч | 20 |
Кроме того, были проведены тесты на индикатор припоя (SI) и тесты на растекание припоя (SST). В этих случаях использовался принтер для нанесения паяльной пасты с производственной паяльной пастой. Атмосфера оплавления представляла собой воздух со следующим профилем оплавления.
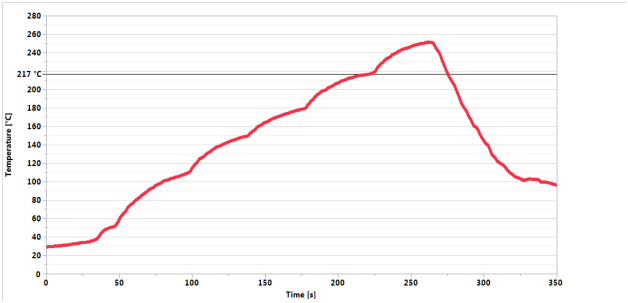
Рис. 3: Профиль бессвинцового оплавления, используемый для индикатора припоя и теста на растекание припоя; пик-T = 248°C.
Для теста на растекание припоя диаметр трафарета составлял 1000 мкм с количеством точек 5. Для оценки использовали оптический микроскоп производственного типа. Для испытаний селективной пайки использовали заводскую машину для селективной пайки с настройками см. таблицу 3. Толщина тестируемой печатной платы составляла 1,5 мм, для оценки использовался оптический микроскоп производственного типа.
Таблица 3: Настройки, используемые для испытания селективной пайки.
Припой | SAC 305 |
Флюс | Имеющийся в производстве |
Размер паяльного сопла | 18 мм внутри; 20 мм снаружи |
Температура припоя | 280°C |
Концентрация флюса | 30% |
Скорость флюсования | 25 мм/сек |
Скорость пайки | 6 мм/сек |
Испытание в солевом тумане проводилось в соответствии с ISO 9227:2006.
РЕЗУЛЬТАТЫ / ОБСУЖДЕНИЕ.
Распределение толщины золота и скорость покрытия.
Наличие одинаковой толщины золота выгодно для коммерческого применения, поскольку позволяет сэкономить средства за счет более низкой минимальной толщины золота, которое необходимо наносить. Производители печатных плат могут быть обеспокоены тем, что Ni с высоким содержанием фосфора не может обеспечить распределение золота, к которому они привыкли используя Ni со средним содержанием фосфора. Это связано с тем, что считается, что более благородные свойства никеля с высоким содержанием P могут повлиять на качество нанесения золота (Au). Чтобы показать, что можно наносить золото с таким же распределением также поверх слоя High-P, была изготовлена запатентованная тестовая плата с различными размерами площадки (рис. 4), которая затем была измерена с помощью метода рентгенофлуоресцентного измерения (XRF).
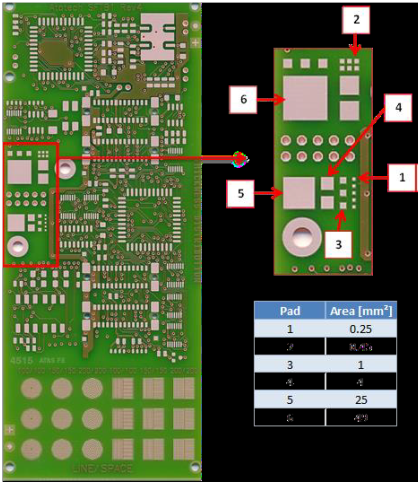
КП | Площадь (мм2) |
1 | 0,25 |
2 | 0,45 |
3 | 1 |
4 | 4 |
5 | 25 |
6 | 49 |
Рис. 4: Распределение толщины испытательной платы компании, измеренные контактные площадки и размер контактных площадок.
Результаты можно увидеть на рис. 5. Нанесение Au одинаковой толщины в ванне с золотом, не содержащей цианид, на High-P Ni и в обычной ванне с Au, содержащей цианид, на Mid-P Ni привело к аналогичному или, возможно, даже немного лучшему распределению толщины Au для High-P Ni. В дополнение к толщине Au там также отображается толщина Ni, а также содержание P в слоях Ni.
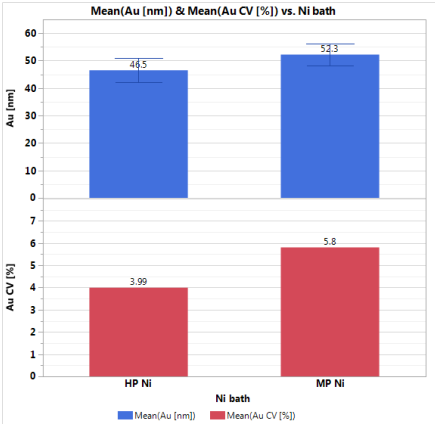
а) Толщина Au и стандартное изменение.
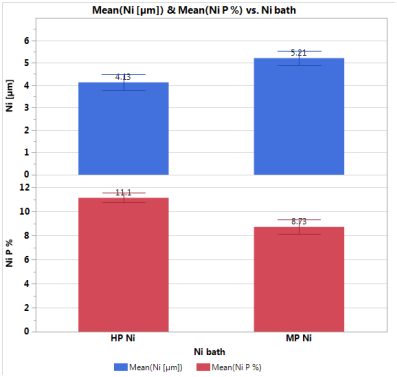
б) Толщина никеля и содержание фосфора.
Рис. 5: Средняя толщина золота (Au), измеренная с помощью рентгенофлуорисцентного анализа (РФА), а также коэффициент вариации (CV) для различных размеров КП, толщина Ni и содержание P на тестовой плате компании для Mid-P Ni и High-P Ni.
Паяемость.
Тест на индикатор припоя (SI) используется для измерения смачиваемости в зависимости от расстояния между напечатанными рисунками паяльной пасты (рис. 6). Шкала колеблется от 1 до 10 баллов (снизу вверх на рис. 6), где 10 — лучший показатель, указывающий на превосходное смачивание.
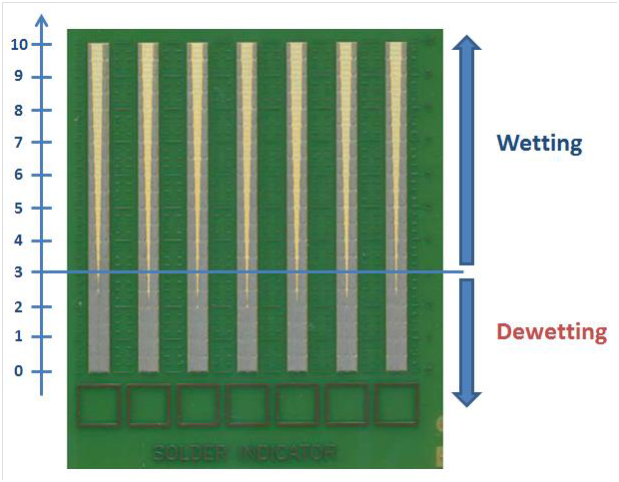
Рис. 6: Тестовая плата индикатора припоя с паяльной пастой.
После печати тестовые платы оплавляются в печи и паяльная паста должна сходиться, а результат можно прочитать по шкале. Результаты этого теста можно найти на рисунке 7.
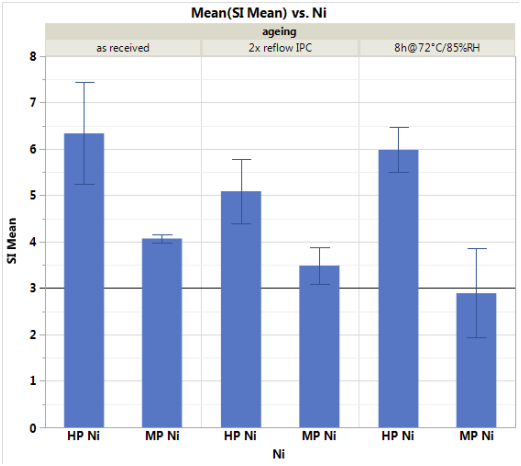
Рис. 7: Результаты теста индикатора припоя для никеля Mid-P и High-P и различных условиях старения.
Можно увидеть очень хорошее смачивание для High-P Ni (намного выше минимально допустимого критерия - 3) во всех условиях старения по сравнению с Mid-P Ni для аналогичной толщины Au.
Еще одним способом измерения смачиваемости слоя Ni/Au является испытание на растекание припоя. В этом тесте точка припоя печатается в середине круглой контактной площадки (рис. 8).
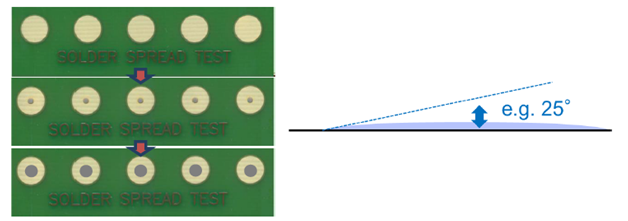
Рис. 8: Тестовая область смчивания припоя с нанесенной паяльной пастой (внизу) и без нее (вверху).
Во время оплавления тестовой платы точка плавится, и впоследствии можно измерить угол смачивания между припоем и слоем Au. Это дает представление о смачиваемости слоя. Результаты испытаний на растекание припоя представлены на рис. 9.
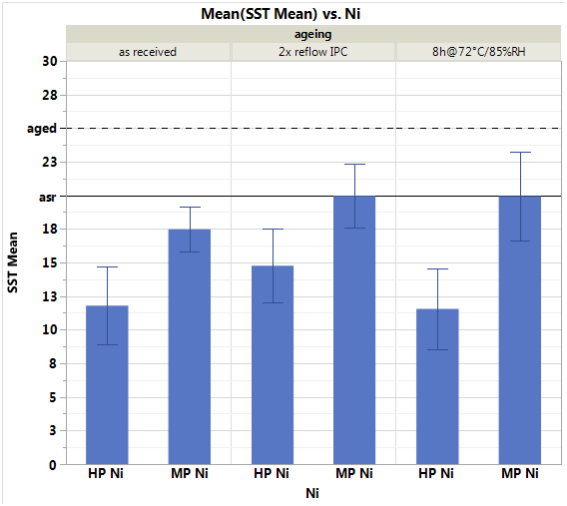
Рис. 9: Результаты теста на растекание припоя для сплавов Mid-P и High-P Ni и различных условий старения.
Что касается теста на растекание припоя, то меньшее число означает лучшее смачивание. Поэтому, как и в тесте SI, система HP ENIG демонстрирует значительно лучшую смачиваемость во всех условиях старения.
Последним тестом, дающим информацию о смачиваемости, является селективная пайка волной. В этом тесте одна сторона тестовой платы облужена (Рисунок 10), а затем проверяется, смог ли припой полностью смочить сквозные отверстия (PTH) (Рисунок 11).
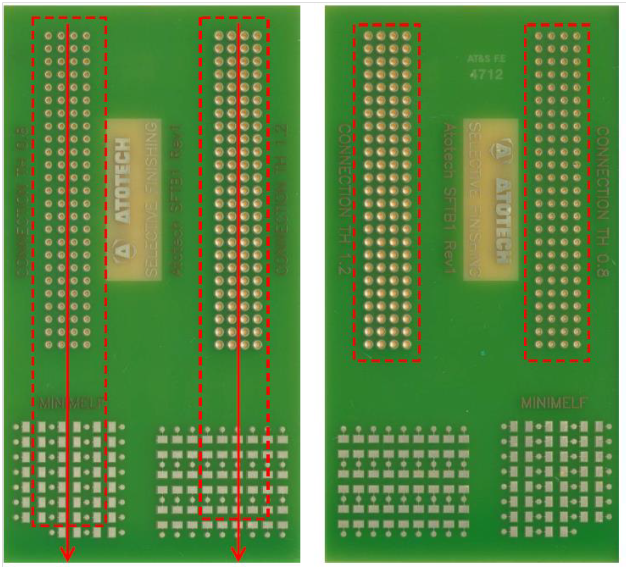
Рис. 10. Зона выборочного тестирования волной на стандартной испытательной плате компании. Место контакта припоя (слева) и оценка (справа).
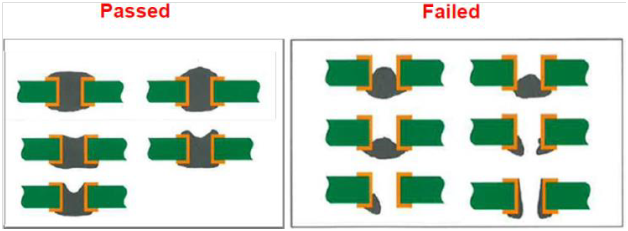
Рис. 11. Критерии прохождения и непрохождения теста на селективную пайку.
Глядя на рисунок 12, можно увидеть результаты испытаний на селективную пайку для систем Mid-P и High-P Ni ENIG. Опять же, как и в обоих предыдущих тестах High-P Ni показывает значительно лучшую паяемость во всех условиях по сравнению с Mid-P Ni. Общая лучшая способность к пайке High-P Ni по сравнению со Mid-P Ni может быть объяснена ссылкой на отчет в статье [6]. В этом отчете упоминается, что загрязнение ванны из-за коррозии, а также окисление на поверхность Ni ответственны за то, что поверхность становится несмачиваемой. Таким образом, использование слоя High-P Ni должно уменьшить возникновение этих двух возможных причин, поскольку он более устойчив к коррозии/окислению, чем слои Mid-P Ni. Кроме того, для достижения аналогичных результатов смачивания для системы MP ENIG потребуется большая толщина Au. Таким образом, HP ENIG предлагает ещё и огромное преимущество по стоимости за счет меньшего расхода золота, при этом демонстрируя превосходную способность к пайке.
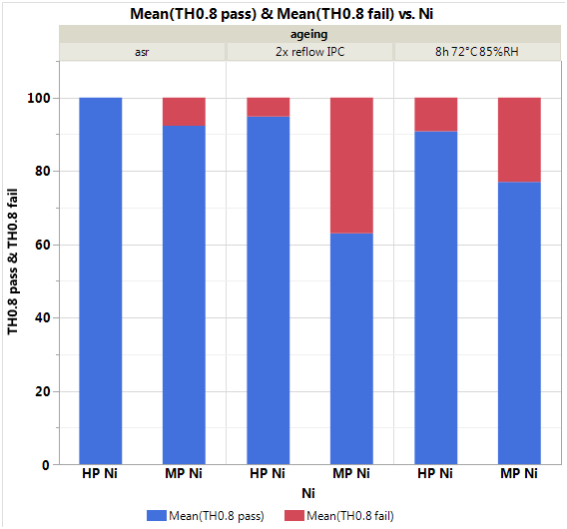
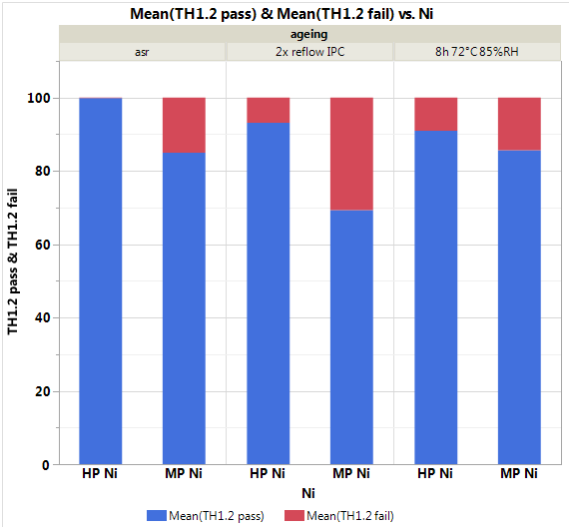
Рис. 12. Результаты селективной пайки волной припоя для различных размеров сквозных отверстий (диаметром 0,8 и 1,2 мм).
Испытания на надежность.
Надежность паяного соединения может быть проверена, например, с помощью теста на сдвиг шарика, отрыв холодного шарика, а также испытания на сдвиг при высокой скорости. В этом исследовании были проведены все три вышеупомянутых теста на надежность, чтобы найти различия между протестированными уровнями ENIG. В тесте на сдвиг шариков используется инструмент для срезания шариков припоя на определенной высоте и с определенной скоростью. Измеряется усилие, необходимое для отрыва шарика припоя. Кроме того, также записывался режим разрушения для проверки хрупких паяных соединений. Вместо этого в испытании на отрыв холодным шариком используется зажим для отрыва шарика припоя от подложки в вертикальном направлении и измерения силы отрыва до разрушения. Испытание на высокоскоростной сдвиг, как следует из названия, является более быстрой версией обычного испытания на сдвиг шарика, но в дополнение к испытанию на сдвиг шарика также регистрируется общая энергия, необходимая для отрыва шарика припоя.
Прочность на сдвиг, а также режим разрушения при испытании на сдвиг шарика можно увидеть на рис. 13. Кроме того, классификацию режима разрушения можно увидеть на рис.14. Оба типа никелевых ванн демонстрируют хорошую прочность на сдвиг, а также хороший режим разрушения с отсутствием интерметаллических трещин.
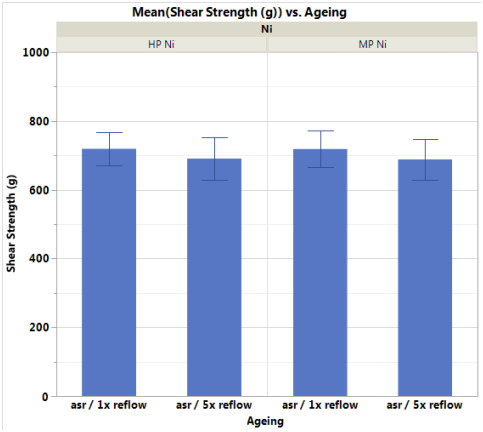
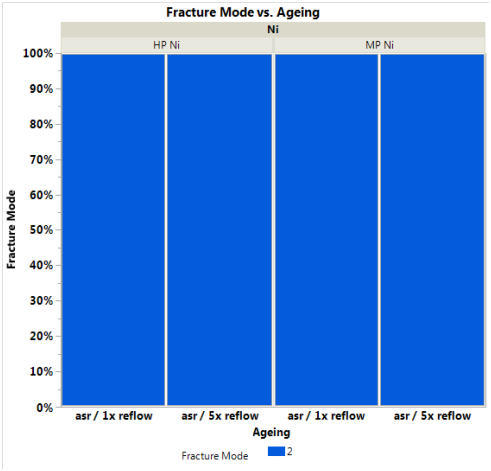
Рис. 13. Прочность на сдвиг (вверху) и характер разрушения (внизу) при испытании на сдвиг в шариках для различных никелевых ванн и условий старения.
Режим 1 | КП оторвана |
Режим 2 | Толщина интерметаллида <5% |
Режим 3 | Толщина интерметаллида <25% |
Режим 4 | Толщина интерметаллида <95% |
Режим 5 | Толщина интерметаллида <95% |
Рис. 14. Классификация видов разрушения для испытания на сдвиг шарика.
Глядя на прочность на отрыв в испытании на отрыв холодного шарика (рис. 15, слева), опять же, не видно никакой разницы для никеля со средним и высоким содержанием никеля, но, несмотря на то, что прочность на отрыв аналогична, существуют значительные различия в режимах разрушения никеля (рис. 15, справа). Режимы разрушения слоя Mid-P имеют тенденцию быть более хрупкими по сравнению с режимами разрушения слоя High-P Ni (рис. 16).
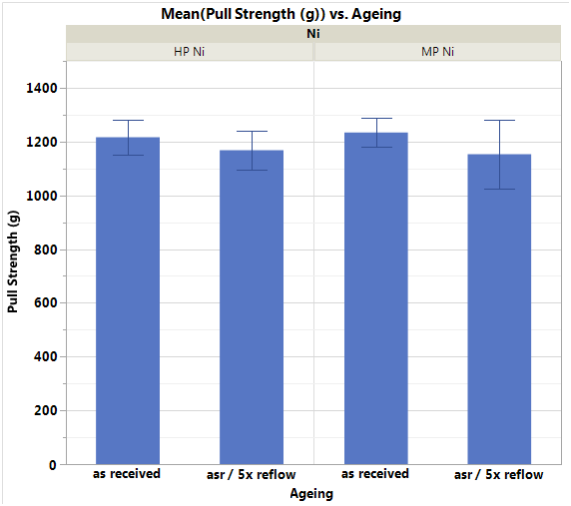
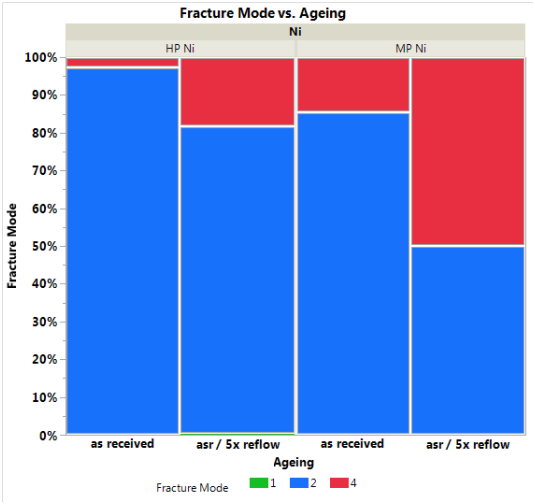
Рис. 15. Прочность на отрыв (вверху) и характер разрушения (внизу) при испытании на отрыв холодного шарика для различных никелевых ванн и условий старения.
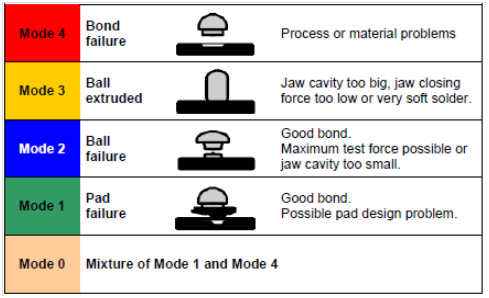
Рис. 16. Классификация видов разрушения при испытании на отрыв холодного шарика.
Режим 4 | Обрыв шарика |
Процесс или проблемы с материалом |
Режим 3 | Выпячивание шарика |
Полость зажима слишком большая, усилие зажима слишком мала или припой слишком мягкий. |
Режим 2 | Обрыв шарика |
Хорошая сварка. Максимально допустимое тестовое усилие или усилие зажима слишком малы. |
Режим 1 | Обрыв КП |
Хорошая сварка. Возможно проблема с конструкцией КП |
Режим 0 | Смесь режимов 4 и 1 |
Те же тенденции, что и при отрыве холодного шарика, также можно увидеть и при испытании на высокоскоростной сдвиг (рис. 17). В состоянии поставки оплавление обоих слоев никеля демонстрируют одинаковую общую энергию и схожие режимы разрушения (рис. 17 (справа) и рис. 18). Но после пятикратного оплавления общая энергия, а также режимы разрушения стали значительно хуже для слоя Mid-P Ni по сравнению со слоем High-P Ni. Эта разница в режимах разрушения при отрыве холодного шарика, а также при высокоскоростном сдвиге между Mid-P Ni и High-P Ni может быть связана с образованием интерметаллических соединений различного типа (IMC). Известно, что на образование IMC и растворение никеля влияет содержание фосфора в слое никеля. Электролитический Ni демонстрирует гораздо более быстрое растворение Ni в припое, а также более быстрый рост IMC по сравнению с никелем, полученным химическим способом [7].
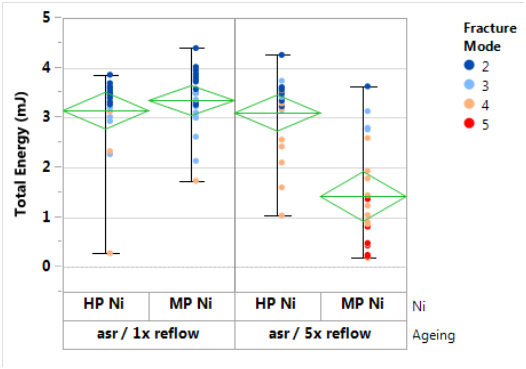
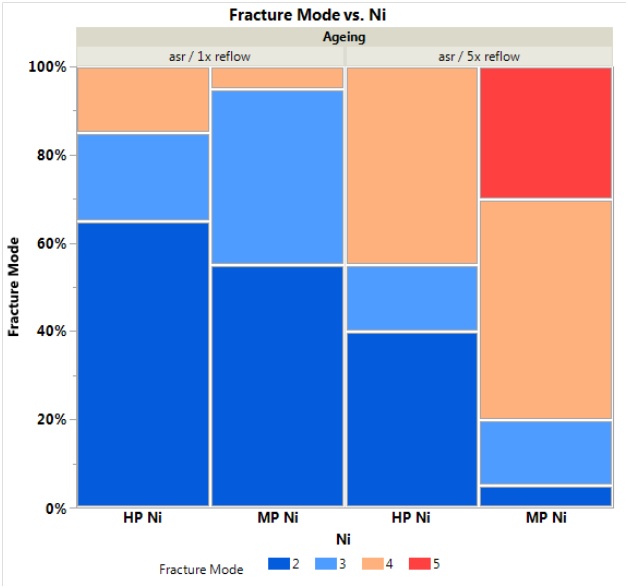
Рис. 17. Полная энергия (слева) и режим разрушения (справа) при испытании на высокоскоростной сдвиг для различных ванн Ni и условий старения (скорость сдвига 0,2 м/с, высота сдвига 20 мкм).
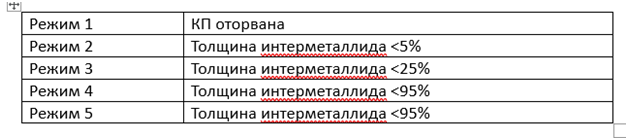
Рис. 18. Классификация режимов разрушения для испытаний на высокоскоростной сдвиг.
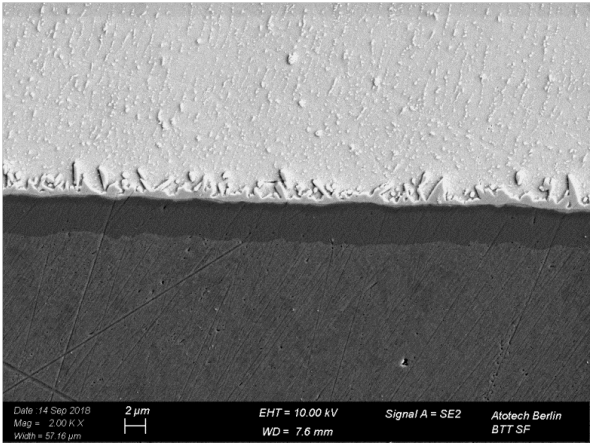
a) HP Ni после 1-кратного оплавления.
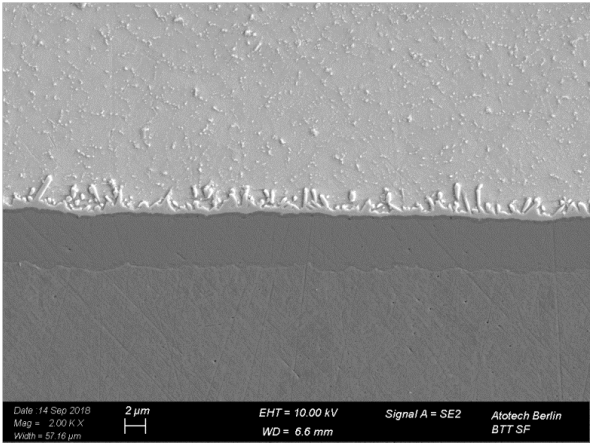
b) MP Ni после 1-кратного оплавления.
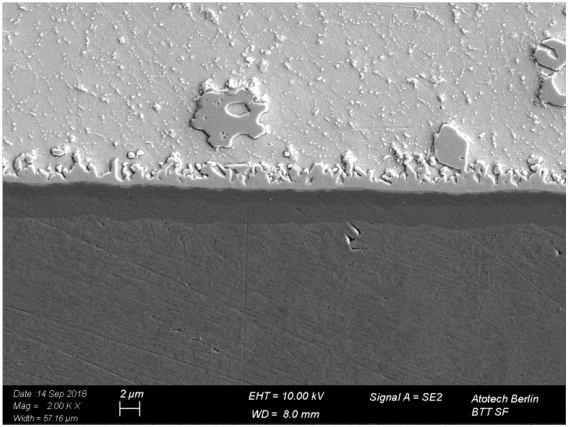
c) HP Ni после 5-ти кратного оплавления.
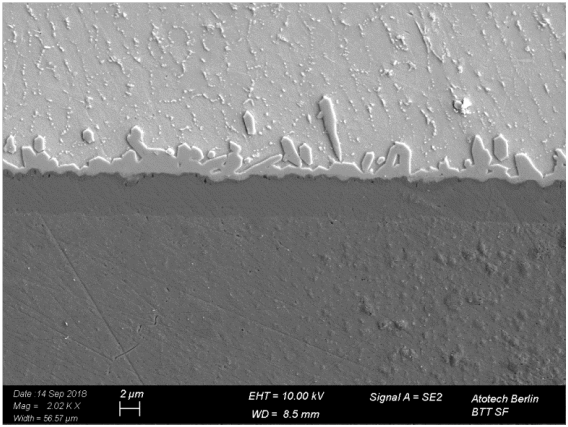
d) MP Ni после 5-ти кратного оплавления.
Рис. 19. СЭМ (2000x) микрошлифов шариков припоя для High-P Ni (слева)
и Mid-P (справа) после 1-кратного и после 5-кратного оплавления.
Это подтверждается СЭМ изображениями микрошлифов припаяных шариков. На рисунке 19 можно увидеть общий вид IMC. для HP и MP Ni в состоянии поставки и после 1- кратного и 5-кратного оплавления. Что касается условий оплавления слои MP и HP Ni, показывают аналогичный рост IMC. После 5-кратного оплавления оба типа слоев Ni демонстрируют рост IMC, но структура IMC изменилась. IMC High-P Ni по-прежнему состоит из игольчатых структур, но для MP структура содержит больше узелков. При более тщательном рассмотрении IMC для MP и HP Ni (рис. 20) можно увидеть отчетливую темную окраску. Эта темная полоса представляет собой слой, обогащенный люминофором, который растет и становится все больше и больше с увеличением количества циклов оплавления, тогда как для слоя HP можно увидеть только некоторое изменение, указывающее на обогащение фосфором слоя Ni. Возможно, этот отчетливый растущий и пористый слой, обогащенный фосфором, ответственен за ухудшающиеся режимы разрушения MP Ni с увеличением циклов оплавления.
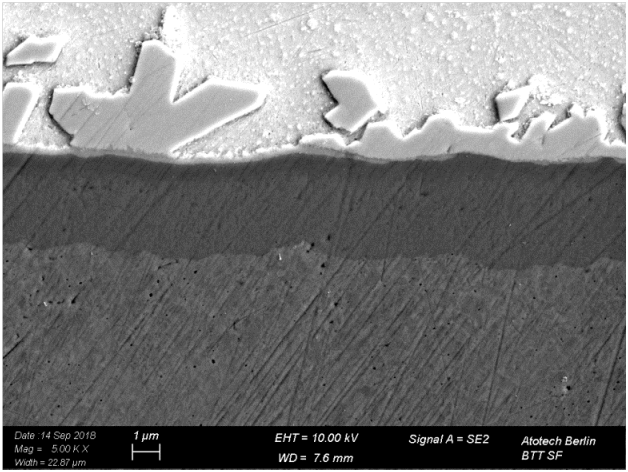
a) HP Ni после 1-кратного оплавления.
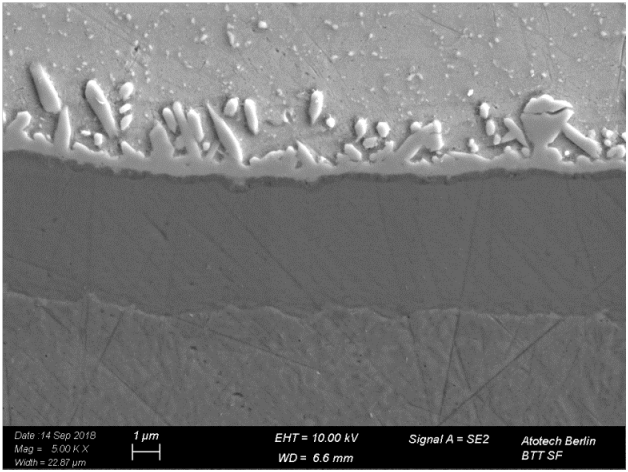
b) MP Ni после 1-кратного оплавления.
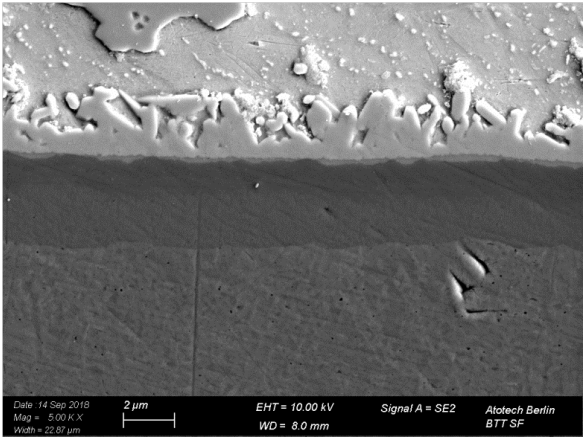
c) HP Ni после 5-ти кратного оплавления.
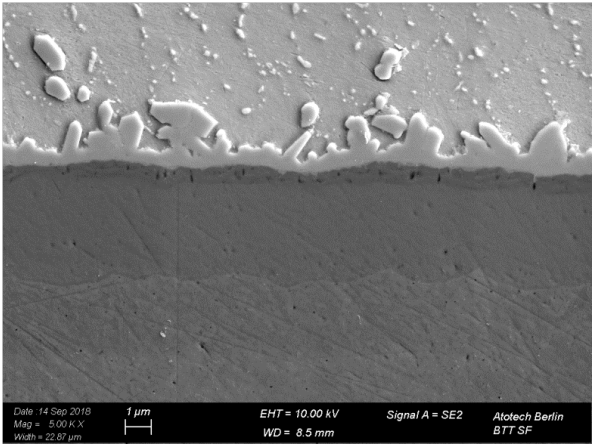
d) MP Ni после 5-ти кратного оплавления.
Рис. 20: Микрошлифы SEM (5000x) шариков для High-P Ni (слева) и
Mid-P (справа) после 1-кратного, и после 5-ти кратного оплавления.
Свариваемость.
Для испытаний на привариваемость алюминиевой проволоки два конца были приварены ультразвуком к поверхности платы. После этого было проведено испытание на отрыв проволоки, отрыв из середины проволоки и регистрация силы отрыва, а также режима разрушения. Возможно, для соединения алюминиевой проволоки можно ожидать другого поведения, поскольку концы привариваются к поверхности с разной твердостью. Но, как видно на рис. 21 (слева), оба слоя никеля смогли легко превзойти допустимый критерий минимальной средней прочности на отрыв - 7,5 г.
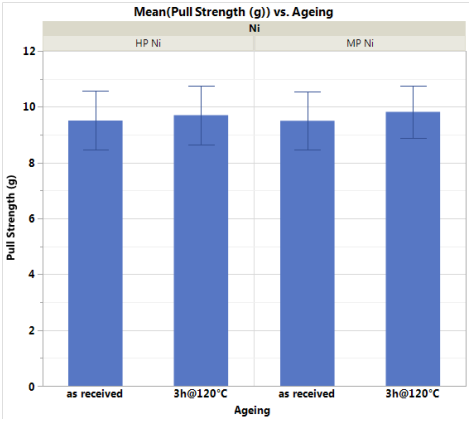
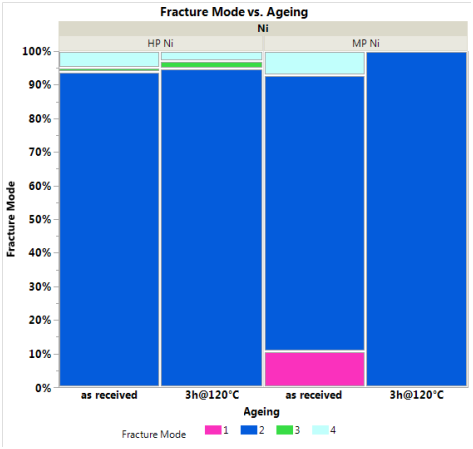
Рис. 21. Прочность на отрыв и характер разрушения алюминиевой проволоки для различных слоев никеля и условий старения.
Ni High-P имеет более низкую твердость (Рисунок 23), а также меньшую шероховатость поверхности, чем Ni Mid-P (Рисунок 24). Оба фактора играют ключевую роль в привариваемости, поскольку тонкие слои золота повторяют контуры подстилающей поверхности никеля [8].Это может быть причиной того, что режимы разрушения слоя High-P Ni немного лучше, чем режимы разрушения слоя Mid-P Ni.
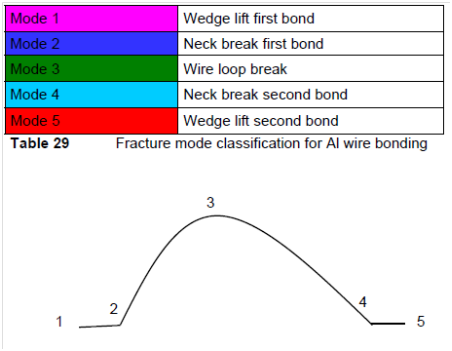
Режим 1 | Опускание клина у первой сварки |
Режим 2 | Обрыв по утонению шейки первой сварки |
Режим 3 | Обрыв по петли |
Режим 4 | Обрыв по утонению шейки второй сварки |
Режим 5 | Опускание клина у второй сварки |
Рис. 22. Классификация видов разрушения при соединении алюминиевой проволокой.
![Рис. 23. Твердость слоя Ni в зависимости от содержания фосфора [9].](imgTPPP/tpPP_68_23.png)
Рис. 23. Твердость слоя Ni в зависимости от содержания фосфора [9].
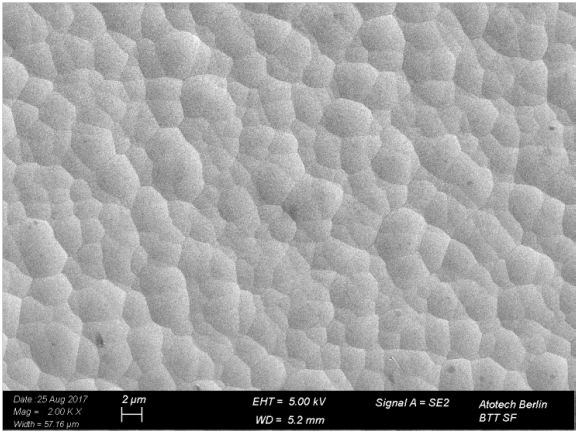
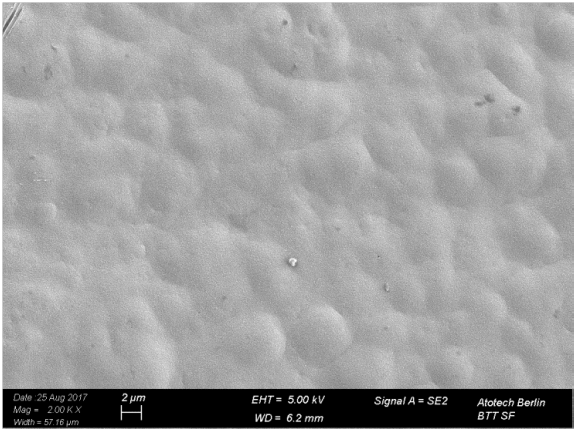
Рис. 24: СЭМ-изображения поверхности слоев Mid-P и High-P Ni.
Коррозия.
С выходом новой спецификации IPC 4552A коррозия оказалась в центре внимания производителей печатных плат. Коррозия может произойти либо при нанесении иммерсионного золота (Au) на слой Ni, либо при воздействии любой агрессивной среды. Следовательно, толщина покрытия, а также его пористость имеют большое значение для коррозионной стойкости ENIG. Нанесение никеля с высоким содержанием фосфора снижает склонность покрытия к пористости, что приводит к усилению сопротивления коррозии. Другими преимуществами покрытия ENIG с высоким содержанием фосфора являются:
- Меньше или нет границ зерен, на которых может начаться коррозия.
- Покрытия имеют тенденцию образовывать пассивные поверхности, обеспечивающие дополнительную защиту [9].
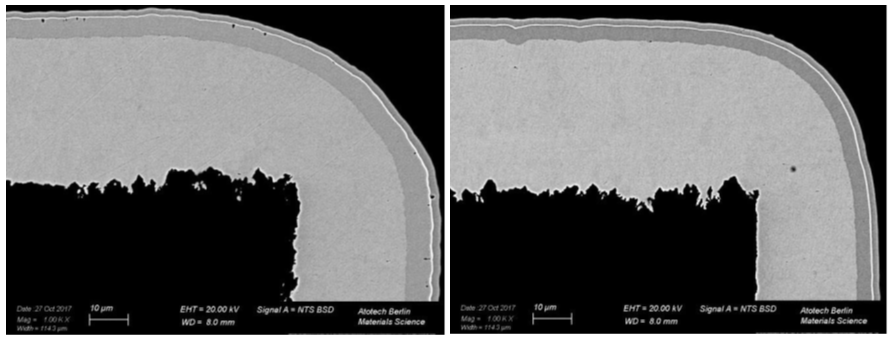
Рис. 25. Типичные изображения микрошлифов СЭМ (1000х) для Ni со средним содержанием P (слева) и Ni с высоким содержанием P (справа).
Чтобы сравнить слои никеля Mid-P и High-P (примеры см. на рис. 25) в отношении коррозионного воздействия в иммерсионной ванне для нанесения золота обе системы ENIG оценивали в соответствии с IPC 4552A. Как видно на Рисунке 26, High-P Ni имеет лучшую коррозионную стойкость и, таким образом, не оставляет места для неправильного толкования.
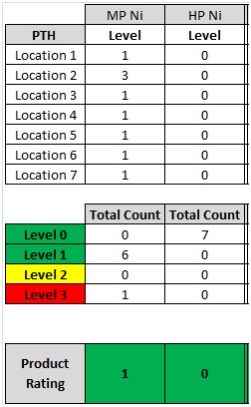
Рис. 26. Оценка коррозии в соответствии с IPC 4552A для моделей Mid-P и Ni с высоким содержанием фосфора.
Испытание в нейтральном солевом тумане (NSS) является одним из многих методов определения коррозионной стойкости системы слоев ENIG. Условия этого испытания вызывают ускоренное коррозионное воздействие, которое может свидетельствовать о коррозионной стойкости соответствующего образца. Результаты теста NSS можно найти в таблице 4. Из-за агрессивного характера этого теста обе системы ENIG демонстрируют коррозию, но ENIG с HP Ni смог выдержать коррозионное воздействие лучше, чем MP ENIG из-за более высокого содержания фосфора. Этот результат делает HP ENIG лучшим решением для печатных плат, которые должны работать в агрессивной среде.
Таблица 4: Результаты испытания в нейтральном солевом тумане (до 144 часов) для MP ENIG и HP ENIG.
acp | 24ч | 48ч | 96ч | 144ч | |
ЭНИГ (МП) | ![]() |
![]() |
![]() |
![]() |
![]() |
ЭНИГ (HP) | ![]() |
![]() |
![]() |
![]() |
![]() |
Выводы.
Целью данной статьи было преодоление мифов в среде производства печатных плат относительно покрытия HP ENIG. Можно ясно показать, что HP ENIG обеспечивает значительно лучшую паяемость, чем MP ENIG, при одинаковой толщине слоя золота, что может привести к огромным экономическим преимуществам, поскольку можно наносить более тонкие слои Au с тем же качеством, что и у стандартного MP ENIG. Кроме того, HP ENIG также обеспечивает высокую надежность паяных соединений, особенно после нескольких циклов оплавления, возможно, из-за меньшего растворения никеля и другого роста IMC по сравнению с MP ENIG. Более низкая твердость и шероховатость поверхности HP Ni также, по-видимому, положительно влияют на характеристики режима разрушения алюминиевой проволоки. Наконец, структура, а также электрохимически более благородное поведение HP Ni делают его лучшим выбором от воздействия агрессивных сред, будь то иммерсионные ванны Au и/или коррозионная среда.
Благодарности
Авторы хотели бы поблагодарить компанию KSG Leiterplatten GmbH, изготовившую образцы, использованные в этом исследовании.
Использованная литература
- С. Ниланд, «Влияние фосфора на фазообразование и фазовый рост в химически осажденных выводах Ni/P и контактах», Факультет III - Факультет материаловедения Технического университета, Берлин, 2002.
- К. Дж. Х. Р. Д. Х.-Дж. С. Свен Лампрехт, «Влияние объемного содержания фосфора в слоях химического никеля на целостность паяного соединения и их использование в качестве поверхности соединения золотой и алюминиевой проволоки», Atotech, 2004.
- С. К. Л. А. С. Мей З., «Анализ отказов и метод доработки электронной сборки с покрытием химическим никелем/ иммерсионным золотом», в SMTA International, Чикаго, 1999.
- YCCKNTMO Alam, «Влияние времени реакции и содержания фосфора на механическую прочность границы раздела, образованного между эвтектическим припоем Sn-Ag и связующей площадкой Au/химическим методом Ni(P)/Cu», Журнал практической физики, том. 94, нет. 6, стр. 4108-4115, 2003.
- П. А. М. Р. П. Снуговский, «Химические межсоединения Ni/Au с иммерсией: исследование черной площадки в проволочных соединениях и паяных соединениях», Журнал материалов в электронике, том. 30, нет. 9, стр. 1262-1270, 2001.
- П.-Э. Тегехолл, «Обзор влияния интерметаллических слоев на хрупкость оловянно-свинцовых и бессвинцовых припоев», Отчет проекта IVF, 2006–2007 гг.
- Ю. К. Ахмед Шариф, «Межфазные реакции на электролитическом никеле и химическом никеле (P)», Журнал сплавов и соединений, том. 393, стр. 135-140, 2005.
- Г. Харман, «Соединение проводов в микроэлектронике», McGraw Hill, 2010, стр. 183–223.
- Р. Паркинсон, «Свойства и применение химического никеля», Институт развития никеля.