- Главная
- Оборудование для печатных плат
- Оборудование для поверхностного монтажа
- Технологии производства плат и поверхностного монтажа
- Инструмент для печатных плат и Запасные части
- Материалы и Химикаты для печатных плат и поверхностного монтажа
- Гальваническое оборудование
- Лабораторное и аналитическое оборудование
- Сервис и техническое обслуживание
- Как нас найти
- Начало раздела
- Главный технолог
- Технологии производства
- Консультации
- Контакты
Оптимизация химического состава иммерсионного серебра по меди
Г-жа Дагмара Чарик, г-н Том Тайсон, г-н Эрик Стафстром, доктор Рон Моррисси.
Техник Инк.
Крэнстон Р.И.
Optimizing Immersion Silver Chemistries For Copper.
Ms Dagmara Charyk, Mr. Tom Tyson, Mr. Eric Stafstrom, Dr. Ron Morrissey
Technic Inc
Cranston RI
Авторский перевод ЛЕЙТЕСА ИЛЬИ, гл.технолога ООО РТС Инжиниринг.
АННОТАЦИЯ
Химия иммерсионного серебра уже несколько лет пропагандируется как состав для финишного паяемого покрытия. Существуют различные коммерчески доступные продукты, которые имеют серебро в широком диапазоне значений толщины. Некоторые химические вещества из-за своей очень агрессивной природы могут привести к увеличению толщины покрытия. Большая разница в толщине серебра на одной и той же плате влияет на время смачивания припоем особенно со сплавами SAC. Большой разброс толщины серебра можно преодолеть при сборке, но это обычно требует более точного процесса сборки с более длинным или более горячим профилем пайки. В настоящее время проводится исследование по оценке химического состава иммерсионного серебра на основе нитратов по сравнению с другими потенциальными источниками серебра. В ходе исследования оценивалось влияние нескольких типов добавок на конструкцию печатной платы. Данные о толщине, скорости разрушения меди и пористости паяемого покрытия привели к появлению новых теорий о том, как контролировать нанесение иммерсионного серебра. Были найдены специальные составы, которые обеспечивают беспористое покрытие с минимальное воздействием на медь. Был выбран конкретный испытательный образец, имеющий заземляющие плоскости, изолированные дорожки, соединенные между собой площадки и различные процессы металлизации.
ВВЕДЕНИЕ
Защита медной поверхности от окисления – конечная цель всех многочисленных финишных покрытий, которые сегодня доступны на рынке. Технологические изменения в связи с увеличением функциональности компонентов и экологического законодательства создали общеотраслевую потребность в покрытиях поверхности, не содержащих свинца. Глобальное законодательство, наконец, привело к хорошо предсказанному изменению от хорошо известного и понятного процесса выравнивания припоя горячим воздухом (HASL) к покрытию химическим никелем и иммерсионным золотом (ENIG). ENIG был выбран потому, что он имеет долгую и по большей части успешную историю с широким спектром услуг и широким окном процесса сборки. Кроме того, за прошедшие годы была проделана большая работа несколькими поставщикам, чтобы понять, предсказать и, по большей части, устранить явление, называемое черными КП.
Однако есть две основные причины продолжать поиск альтернатив ENIG:
- Прочность паяного соединения;
- Расходы.
С точки зрения металлургии, паяное соединение с ENIG формируется на слое никеля/фосфора. Этот слой может содержать различное количество фосфора у разных поставщиков химического никеля, для контроля производственных параметров и скорости нанесения иммерсионного золота. Химический никель хорошо паяется, а фосфор - нет. Конечным результатом использования ENIG является снижение прочности паяного соединения, что становится критическим, поскольку шаг становится меньше 1 мм, особенно в конструкциях с BGA и micro-BGA. Для производителя это превращается в необходимость введения дополнительных этапов и выборочного нанесения ENIG, что увеличивает количество этапов технологического процесса и, в конечном итоге, их стоимость.
Диаграмма 1: Альтернативы HASL с пропорциональной стоимостью.
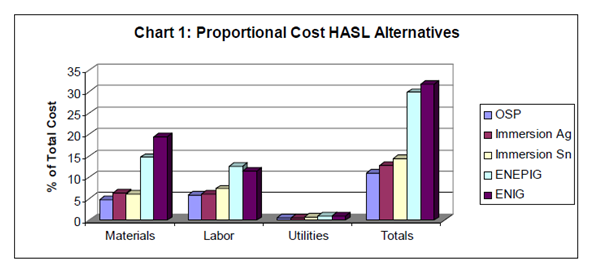
Учитывая, что рыночная цена золота достигла 20-летнего максимума, ENIG является одним из самых дорогих покрытий поверхности. Покрытие золотом составляет 70-80% стоимости покрытия ENIG. На диаграмме 1 показаны приблизительные затраты на процесс для нескольких коммерчески доступных альтернативах HASL. Органические консерванты для пайки (OSP) снижают затраты. По сравнению с ENIG и химическим никелем, химическим палладием, иммерсионным золотом (ENEPIG) в соответствии с многочисленными исследованиями - иммерсионное серебро и OSP обеспечивают прочные паяные соединения. В обоих случаях паяное соединение формируется непосредственно на поверхности меди. Однако OSP (ОСП), исторически хорошо работая с эвтектическим припоем, не может обеспечить рабочее окно для бессвинцовой пайки. Большая разница заключается в том, что припою необходимо проникнуть в OSP и соединиться с медной поверхностью, в то время как металлическое покрытие, такое как иммерсионное серебро или олово, становится частью паяного соединения. OSP ограничивает растекание припоя и возможность полного смачивания контактной площадки или сквозного отверстия. Химия иммерсионного серебра первого поколения стала второй или третьей по значимости альтернативой HASL (ХАСЛ). ENIG имеет самую высокое распространение, а OSP и иммерсионное серебро борются за второе место. Стоимость и паяемость были основными факторами, позволившим иммерсионному серебру добиться успеха на рынке. Каким бы сложным не было массовое производство с использованием иммерсионного серебра оно выявило некоторые проблемы, которые не наблюдались в лаборатории или во время первоначального тестирования. Подобно переходу на ENIG, агрессивный характер иммерсионной химии необходимо контролировать, чтобы обеспечить эффективность производства. Контроль иммерсионного химического состава должен начаться с понимания химических реакций во время процесса нанесения покрытия.
Иммерсионное покрытие.
При разработке химии иммерсионного серебра необходимо учитывать несколько факторов. Идеал состоит в том, чтобы обеспечить равномерный тонкий слой, который может быть легко растворен при пайке. Более тонкий слой оказывает меньшее воздействие на состав паяного соединения, и его растворение занимает меньше времени, что может быть критично из-за короткого времени затвердевания некоторых бессвинцовых припоев. Консистенция, особенно толщина паяемого покрытия, в конструкции печатной платы влияет на паяемость контактных площадок различной геометрии. Идеальный иммерсионный процесс предоставляет более широкое окно для сборки из-за улучшенной консистенции. Во-первых, чтобы произошла реакция , между нанесенным металлом и поверхностью должен существовать потенциал между покрытием и основным металлом, на который наносится покрытие. Теоретически, чем больше потенциал, тем агрессивнее становится реакция замещения (см. Таблицу 1: Электрохимический потенциал меди и серебра). Однако есть еще несколько факторов: таких как pH, температура и интенсивность потока раствора, которые будут влиять на динамику переноса материала на поверхность покрытия. Обычно наблюдается увеличение скорости реакции при снижении pH или увеличении температуры и движения раствора. Кроме того, добавки могут использоваться для комплексообразования как основного, так и плакированного металла.
Таблица 1: Электрохимический потенциал меди и серебра.
Металл | Реакция | Потенциал(V) | Иммерсионная реакция | Иммерсионный потенциал(V) |
Медь | Cu2+ + 2e- ↔ Cu | 0,340 | 2Ag+ + Cu → 2Ag + Cu2+ | 1,259 |
Серебро | Ag+ + e- ↔ Ag | 0,7996 |
Комплексообразователи могут быть специфическими или, по крайней мере, селективными в отношении отдельных металлов. С другой стороны, комплексообразователь, выбранный для меди может усилить реакцию замещения и фактически способствует коррозии медной поверхности. В обоих случаях коэффициент диссоциации каждого комплексообразователя указывает, насколько велик потенциал. При проектировании процесс иммерсионного серебра позволяет выбрать комплексообразователь для контроля скорости осаждения и в конечном итоге обеспечения равномерности покрытия серебром. Очень низкий уровень pH может стать главным фактором при нанесении иммерсионного серебра, подавляя влияние других факторов. При использовании низкого pH для стимулирования осаждения серебра оно становится очень эффективным и зависит от состояния поверхности. Изменение меди, например наличие ее зернистой структуры по сравнению с электролитической медью или различное смачивание поверхности создаст различную скорость растворения меди. В тяжелых случаях процесс иммерсионного серебра может выборочно удалить медь по краю проводника и КП, как показано на рисунках 1 и 2. Этот эффект из-за высокой скорости растворения меди, локально увеличит измеренную толщину серебра.
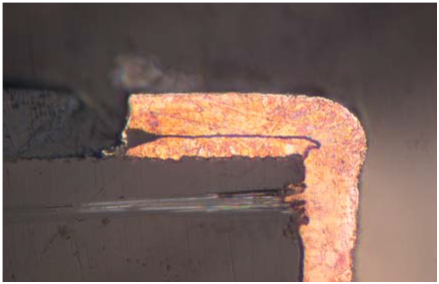
Рис. 1. Сечение при увеличении в 200 раз после электролитического нанесения серебра.
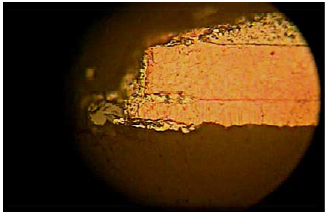
Рис. 2: Сечение КП с покрытием серебра при увеличении 400X после пайки.
Иммерсионный процесс с золотом стал менее агрессивным за счет увеличения pH, а химический никель стал более химически стойким за счет увеличения содержания фосфора. Тот же принцип относится к иммерсионному серебру. Контроль скорости нанесения покрытия приводит к повышению производительности при нанесении покрытия. В процессе нанесения иммерсионного серебра, скорость осаждения можно контролировать путем увеличения pH в сочетании с измерением количества химиката, вызывающего коррозию меди, и специфического комплексообразователя серебра. Это создаст единообразие для всех конструктивных особенностей печатной платы. В ходе разработки решающим оказался и другой фактор — выбор соли серебра. Серебро доступно в виде солей, которые растворяются в растворах кислот. Стоимость и доступность привели к использованию нитрата серебра для большинства существующих составов.
У нитрата серебра есть две основные проблемы:
- Во-первых, нитраты в кислых растворах увеличивают скорость удаления меди, и поскольку концентрация нитратов увеличивается - изменяется pH раствора. При нанесении серебра нитраты накапливаются, создавая меняющиеся условия и делают контроль pH критически важным.
- Во-вторых, ионное серебро имеет очень ограниченную растворимость в присутствии галогенов. В растворах нитрата серебра содержание хлоридов обычно ограничивается 10 ppm и менее. При концентрации выше 10 ppm хлорид вызывает проблемы с адгезией в большинстве процессов иммерсионного серебра на основе нитратов. Решение состоит в том, чтобы использовать готовый комплекс серебра, не содержащий нитратов. Устранение нитратов, устраняет необходимость контролировать накопление этого побочного продукта. Кроме того, использование комплекса серебра устраняет проблемы с загрязнением галогенами и позволяет работать с щелочным pH. Результатом значительной работы по разработке стала система, не содержащая нитратов и работающая в слабощелочном pH.
Результаты испытаний — новая формула состава иммерсионного серебра.
Путем статистической оценки нескольких программ экспериментов была разработана формула иммерсионного серебра с использованием растворителя меди с комплексом серебра. Комбинация позволяет процессу работать при слегка щелочном pH. Испытания показали, что конкретный выбор добавок является ключом к получению хорошей адгезии, равномерному покрытию, высокой стойкости к хлоридам и минимальному воздействия на химическую медь (подтравы).
Диаграмма 2: Толщина покрытия иммерсионного серебро при щелочном pH.
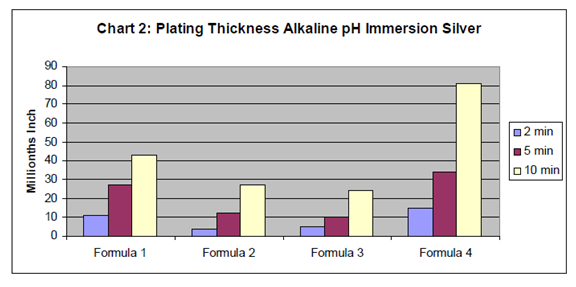
Чтобы рассмотреть худшие сценарии, время нанесения покрытия было увеличено до 5 и 10 минут, чтобы увеличить воздействие на химическую медь и гарантировать отсутствие проблем с адгезией, типичных для длительного времени погружения. (Таблица 2) В формулах варьировалась концентрация и конкретный выбор комплексообразователя и разтворителя меди. Что интересно, по мере увеличения толщины покрытия увеличивается и воздействие на химическую медь (подтравы). Толщина покрытия продолжает увеличиваться при использовании формул 1 и 4, а размер подтравов также увеличивается, как показано ниже в таблице 2.
Таблица 2. Эффект подтрава при использовании различных составов иммерсионного серебра.
Состав (формула) 1 | Состав (формула) 2 | Состав (формула) 3 | Состав (формула) 4 | |
5 мин. | ![]() |
![]() |
![]() |
![]() |
10 мин. | ![]() |
![]() |
![]() |
![]() |
Несмотря на то, что время погружения в 5 и 10 минут является чрезмерным, они показывают, что, поскольку формулы не обладают восстанавливающим потенциалом, они являются формулами для нанесения иммерсионного покрытия, а большая толщина возможна только при наличии меди, ускоряющей реакцию. Это указывает на то, что в покрытии серебра имеется пористость, способствующая реакции покрытия. Идеальный процесс должен быть самоограничивающимся, но при этом обеспечить быстрое начало. Первоначальные испытания, как и ожидалось, также показали, что более агрессивные растворители и комплексообразователи меди более склонны либо к чрезмерному воздействию на медь, либо к нарушению адгезии при испытаниях. Специальный выбор добавок был ключом к получению покрытия менее чем за 15 секунд, хорошей адгезии и отсутствию подтравов на боковых стенках (рис. 3).
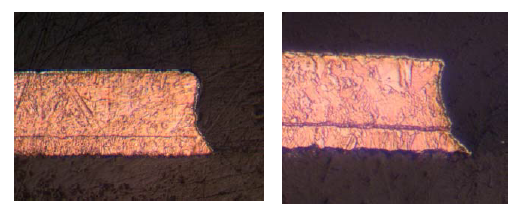
Рис. 3. 5-минутное покрытие безнитратным иммерсионным серебром в щелочной среде.
Согласно измерениям процесс без нитратов приведет к осаждению 10-15 микродюймов серебра за 2 минуты. Общее распределение толщины на типичной печатной плате с BGA находится в пределах 5–10 микродюймов. Большинство систем на основе нитратов имеют диапазон 20 миллионных долей, а иногда и больше. Для дальнейшей оценки распределения толщины были измерены особенности полноразмерной производственной панели после погружения на 2 и 5 минут. Типичное время погружения для этого процесса составляет 2 минуты. Однако было потрачено 5 минут для оценки самоограничивающего характера новой формулы.
Диаграмма 3. Средняя толщина иммерсионного серебра в зависимости от конструкции контактной площадки и времени покрытия.
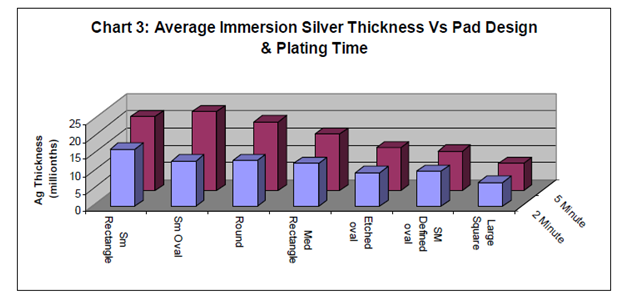
На диаграмме 3 показана средняя толщина нескольких типов элементов: от маленьких прямоугольных площадок для QFP до больших квадратов для радиаторов на больших устройствах BGA. Общее распределение по толщине за 2 минуты составляет примерно 10-15 микродюймов. Увеличив время погружения более чем в два раза - до 5 минут, диапазон толщины действительно изменился примерно с 5 до 10 микродюймов. Однако диапазон гораздо уже, чем у ранее испытанных иммерсионных серебряных покрытий на основе нитратов. Более однородное серебро означает более равномерную пайку элементов печатной платы разных размеров. Данные о толщине на графике 3 также имеют определенную тенденцию. Некоторые особенности демонстрируют большую разницу в толщине при нанесении покрытия в течение 2 и 5 минут. Эта разница отображена на графике 4.
Диаграмма 4: Изменение толщины серебра в зависимости от времени погружения 2 минуты по сравнению с 5-минутным покрытием
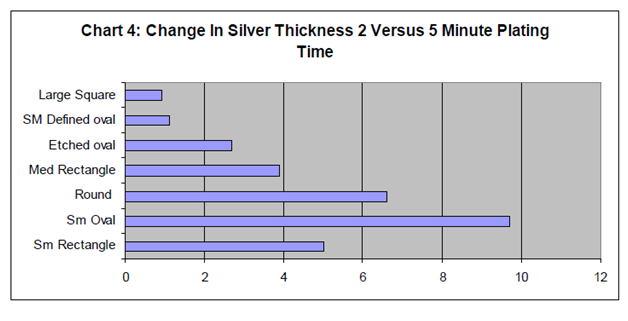
Как и ожидалось, меньшие размеры элементов приводят к большей толщине . Однако диаграмма 4 показывает, что когда время погружения увеличивается, более мелкие элементы имеют более высокую разницу в толщине. Площадь поверхности круглых, маленьких овальных и маленьких прямоугольных КП очень похожа, но маленькие овальные КП имели наибольшее изменение толщины серебра при увеличении времени погружения. Там где площадь поверхности и равномерность распределения по толщине должна быть одинаковой маленький овал действительно имеет самое высокое соотношение периметра к площади, что указывает на то, что боковые стенки влияют на толщину покрытия. Это также может быть поддержано SM (паяльной маской). Овал дает результаты, аналогичные большому квадрату. Травленый овал имеет тот же размер, что и овал SM, но имеет более высокую среднюю толщину и большую разницу при более длительном времени погружения. Овал SM не имеет подтрава боковых стенок, тогда как боковые стенки травленых овалов помогают увеличить толщину покрытия. В этом вопросе необходимо провести дополнительную работу, но даже при контролируемой норме покрытия по безнитратной формуле кажется, что боковые стенки все таки влияют на толщину покрытия. Если процесс нанесения иммерсионного серебра более агрессивен, разница в толщине серебра между разными геометриями печатных плат будет только больше. Дополнительным преимуществом нового иммерсионного серебра, не содержащего нитратов, является толерантность к хлоридам. Ключом является использование промышленного комплекса серебра, допускающего содержание хлоридов в сотни частей на миллион без влияния на толщину или раствор для покрытия. Существующие системы на основе нитрата серебра не могут выдерживать концентрацию более 10 ppm. хлорида. Однако такая высокая толерантность к хлоридам не только позволяет использовать городскую воду в ванне серебрения, но также устраняет одну из причин необходимости предварительного погружения перед нанесением покрытия.
Резюме и заключение.
Была разработана новая иммерсионная химия серебра, которая заменяет нитрат серебра промышленным раствором комплекса серебра и действует при слегка щелочном pH. В результате получается процесс, который быстро запускается и обеспечивает гораздо более постоянную толщину серебра на печатных платах различной геометрии. Процесс является само ограничивающимся и исключает агрессивное воздействие на медь, наблюдаемое в системах на основе нитратов. На основе этой работы была разработана теория распределения толщины, обычно наблюдаемого при нанесении иммерсионного серебра на контактные площадки разных размеров. Оказывается, что при увеличении отношения периметра объекта к площадь поверхности, толщина иммерсионного серебра также увеличивается. Проблема заключается в том, что при очень агрессивных процессах нанесения иммерсионного покрытия неравномерность толщины может превышать 20 микродюймы, и их воздействие может вызвать подтравы на проводниках или боковых стенках КП. Общий диапазон разброса толщины при использовании этого нового процесса обычно составляет менее 10 микродюймов. Это обеспечивает гораздо более однородную поверхность, что чрезвычайно важно, поскольку она не содержит свинца. В процессе сборки серебро должно смешаться с паяным соединением. В таблице 3 показаны расчеты процентного увеличения содержания серебра на основе толщины иммерсионного серебра и толщины трафарета. Имейте в виду, что контактные площадки малого размера с мелким шагом будут иметь наибольшую толщину иммерсионного серебра и для мелкого шага обычно толщина трафарета должна быть меньше, что приводит к нанесению меньшего количества паяльной пасты.
Таблица 3: Приблизительное увеличение содержания серебра в паяном соединении в % от толщины иммерсионного серебра (из расчета на 90% металла, SAC 305).
Толщина серебра (дюймах) | Толщина трафарета (дюймах) | |||
0,005 | 0,006 | 0,007 | 0,008 | |
5 миллионных | 0,21% | 0,17% | 0,15% | 0,13% |
10 миллионных | 0,42% | 0,35% | 0,30% | 0,26% |
20 миллионных | 0,84% | 0,70% | 0,61% | 0,53% |
30 миллионных | 1,27% | 1,06% | 0,90% | 0,79% |
40 миллионных | 1,69% | 1,41% | 1,21% | 1,06% |
Основываясь на этих расчетах, 30 микродюймов иммерсионного серебра могут изменить весовой процент серебра в паяном соединении более чем на 1%. В сплавах SAC обычно содержание серебра составляет 3–4 %, поэтому иммерсионное серебро может изменить содержание серебра на 25-30% от общего количества. Как показано в таблице 4 изменение толщины серебра на 1% может изменить температуру ликвидуса на целых 10 ᵒС.
Таблица 4. Температуры ликвидуса и оплавления сплавов SAC.
Смесь припоя | Температура ликвидуса (Сᵒ) | Температура оплавления(Сᵒ) | Диапазон температуры оплавления(Сᵒ) |
Sn-3.0Ag-0.5Cu* | 220** | 238-248 | |
Sn-3.2Ag-0.5Cu | 218 | 238-248 | 217-218 |
Sn-3.5Ag-0.75Cu* | 218 | 238-248 | |
Sn-3.8Ag-0.7Cu | 210** | 238-248 | 217-210 |
Sn-4.0Ag-0.5Cu | 217-219 | ||
Sn-4.0Ag-1.0Cu* | 220** | 238-248 | 217-220 |
Sn-4.7Ag-1.7Cu* | 244** | 237-247 | 217-220 |
Новый процесс иммерсионного серебра гораздо меньше зависит от конструкции печатной платы. Он предлагает изготовителю более широкий допуск к загрязнению хлоридами и улучшенную консистенцию серебряного покрытия. Для сборщика это означает, что разные печатные платы будут имеет одинаковую относительную производительность пайки, а также допускать использование широкого спектра компонентов, используемых в современной электронике.
Использованная литература.
- Джонсон Р.В., Ван В., Палмер М., «Термическая циклическая усталость межсоединения», 1998 г.
- Ватанабэ, Ю., «Разработка процесса покрытия поверхности печатных плат для повышения надежности и прочности паяного соединения», Современные материалы для корпусирования . Процессы, свойства и интерфейсы. (Advanced Packaging Materials: Processes, Properties and Interfaces), 2001, стр. 165-170.
- Роджерс К., Хиллман К., «Влияние материалов покрытия, размера контактной площадки и геометрии контактной площадки на прочность шарикового вывода из припоя на сдвиг», Центр продуктов и систем CALCE Electronics.
- Зиверт, Т. «Свойства бессвинцовых припоев, версия 4.0», Национальный институт стандартов и технологий, 11 февраля 2002 г.