- Главная
- Оборудование для печатных плат
- Оборудование для поверхностного монтажа
- Технологии производства плат и поверхностного монтажа
- Инструмент для печатных плат и Запасные части
- Материалы и Химикаты для печатных плат и поверхностного монтажа
- Гальваническое оборудование
- Лабораторное и аналитическое оборудование
- Сервис и техническое обслуживание
- Как нас найти
- Начало раздела
- Главный технолог
- Технологии производства
- Консультации
- Контакты
Новые отвердители на основе фосфора для печатных плат
А. Пиотровский*, М. Чжан*, Ю. Зильберман**, Эран Глуз**, С. Левчик*.
*ICL-IP, Тэрритаун. Нью-Йорк, США.
** IMI (Tami) Институт исследований и разработок, Хайфа, Израиль.
New Phosphorus-based Curing Agents for PWB.
A. Piotrowski*, M. Zhang*, Y. Zilberman**, Eran Gluz**, S. Levchik*.
*ICL-IP, Tarrytown, NY, USA.
**IMI (Tami) Institute for R&D Ltd., Haifa, Israel.
Авторский перевод ЛЕЙТЕСА ИЛЬИ, гл.технолога ООО РТС Инжиниринг.
АННОТАЦИЯ
В результате непрерывной промышленной тенденции на подукцию высокой плотности растет спрос на высоко термостойкие ламинированные материалы. Хотя эпоксидная смола определяет термическую стабильность, как часто используемый антипирен становится ограничивающим фактором в достижении более высокой стабильности. Признавая эту промышленную потребность, компания разработала новый огнестойкий отвердитель - Материал А. Это полимер на основе фосфора, который отверждает эпоксидную смолу по очень специфическому механизму. Обычные новолачные эпоксидные смолы, отвержденные материалом А и фенолформальдегидной смолой, имеют Tg >180 °C и Td >400 °C. Помимо высокой термической стабильности, Материал А также имеет коэффициент диэлектрических потерь ниже, чем у коммерческих антипиренов на основе фосфора.
ВВЕДЕНИЕ
Эпоксидные смолы широко используются как в промышленной, так и в бытовой электронике, благодаря их химической стойкости, механической прочности и электрическими свойствами. Чтобы быть полезными, эпоксидные смолы должны обеспечивать простоту обращения и обладать определенными физическими, тепловыми, электроизоляционными и влагостойкими свойствами. Например, эпоксидные смолы, демонстрирующие высокую термическую стабильность и высокую температуру стеклования, сохраняя при этом низкую диэлектрическую проницаемость и низкие диэлектрические потери, обладают желательной комбинацией свойств для электроники, особенно в высокотемпературной среде, такой как средством управления двигателем и т. п. Однако эпоксидные смолы легко воспламеняются. По существу, были предложены различные подходы к приданию эпоксидным смолам желаемого уровня огнестойкости. Такие подходы влекут за собой использование либо галогенсодержащих огнезащитных соединений, либо недавно появившихся безгалогенных огнезащитных соединений. Галогенированные соединения хорошо зарекомендовали себя и хорошо работают в большинстве применений, однако в настоящее время они подвергаются дополнительному изучению, и промышленность использует различные негалогенизированные соединения, в основном на основе фосфора, в качестве альтернативы бромированным огнестойким материалом. Хотя безгалогенные системы по-прежнему сталкиваются с проблемами, связанными с постоянно растущими требованиями к чувствительности к влаге, в некоторых вариантах безгалогенные решения могут обеспечить лучшие свойства для некоторых применений. Большинство антипиренов отрицательно влияют на многие физические и электрические свойства печатных плат. Таким образом, основной задачей при разработке антипиренов является поиск материалов, которые удовлетворяют всем электрическим, термическим, химическим и механическим свойствам, необходимым для оптимальной работы устройства. Поскольку антипирены на основе фосфора более эффективны, чем антипирены на основе Br, их можно использовать в значительно более низких концентрациях, что сводит к минимуму негативный эффект. Хотя многие химические вещества считались потенциальными безгалогенными антипиренами, в большинстве составов используется 9,10-дигидро-9-окса-10-фосфафенантрен-10-оксид (ДОФО), включенный либо в эпоксидную смолу, либо в отвердитель.
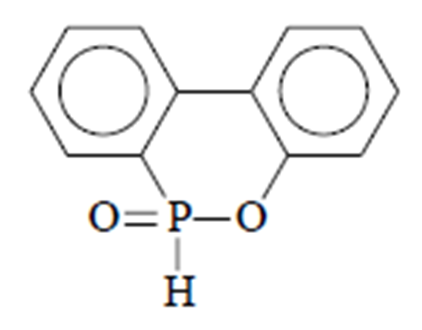
Структура ДОПО.
Таблица 1. Коммерческие антипирены для ПББ на основе фосфора.
Название продукта | Описание | Преимущества | Недостатки |
DOPO | Монофункциональный реактивный фосфинат | Относительно недорогой и надежный вариант для простых составов FR4. | Должна быть проведена предварительная реакция с эпоксидной смолой, более высокая стоимость, ограниченные изменения в рецептуре. |
DOPO-HQ | Продукт реакции DOPO и бензохинона. | Хорошие электрические свойства, эффективность. | Низкая растворимость, требует предварительной реакции. Более высокие затраты после реакции с эпоксидной смолой. |
Циклические феноксифосфазены | Добавка | Отличные электрические свойства. | Низкая Tg, действует как пластификатор, высокая стоимость. |
DOPO-BPA | Продукт реакции формальдегида и DOPO. | Хорошо работает при температуре среднего диапазона с хорошей термической стабильностью. Высокий % P (фосфора). Гибкость в составлении рецептур. | Требуются наполнители для улучшения Tg и характеристик печи. |
Di DOPO | Два блока DOPO, соединенные этиленовым мостиком. Нереактивный. | Хорошие электрические свойства, гибкий в рецептуре. | Твердое вещество, используемое в качестве наполнителя, должно быть хорошо диспергировано. |
В Таблице 1 приведен только один пример антипирена на основе фосфора, который не основан на ДОРО, то есть циклические феноксифосфазены, которые необходимо использовать при гораздо более высоких уровнях фосфора, чем антипирены на основе ДОРО. ДОРО представляет собой реакционноспособную монофункциональную молекулу, и ее можно включать в эпоксидную сетку. Чтобы эффективно использовать ДОРО, его необходимо предварительно прореагировать с многофункциональными эпоксидными смолами. Такая предварительно прореагировавшая эпоксидная смола имеет гораздо меньше реакционноспособных центров, что приводит к более низкой Tg. Такая предварительно прореагировавшая эпоксидная смола DOPO имеет низкое содержание % P, что резко ограничивает любые изменения рецептуры. Недавно разработанное производное ДОРО и бисфенола А имеет гораздо более высокий процент P и растворимо в обычных растворителях. Этот продукт является дифункциональным, что улучшает плотность сшивок, что приводит к более высокому Tg. DOPO-BPA — это значительный шаг вперед к повышению производительности. Однако достичь Tg >170 °C и термической стабильности Td >370 °C этого материала очень сложно, и в большинстве рецептур для достижения твердого V-0 используются наполнители. Признавая необходимость высокой термостабильности печатных плат, компания разработала новый огнестойкий отвердитель, который обеспечивает желаемый уровень огнестойкости, высокую температуру стеклования (Tg) и высокую термическую стабильность (Td) термореактивной смолы, такой как эпоксидная смола. Хотя использование антипиренов обычно отрицательно влияет на электрические свойства, материал А обеспечивает отверждение смолы с низким Dk и достаточно низким Df. Поскольку материал А совместим со смолами с низким Dk, это позволяет получать ламинаты с превосходными электрическими свойствами.
Таблица 2 – Физические свойства материала А.
Свойство. | Оценка. |
Вид | Светло-коричневые хлопья или порошок |
Химическая природа | Полимер |
Температура размягчения | >130°С |
Содержание фосфора | 6,5-7% |
Тg | 130°С |
Молекулярная масса | ~1200 |
Термическая стабильность(Т°С при которой имеется 5% мас. потери) | 340-355°С |
Растворимость в изопропиловом спирте (МЭК) | >40% |
Растворимость в ацетоне | >40% |
Вязкость 60% раствора МЭК (сантипуаз) | 710 |
Вязкость 70% раствора ацетона (сантипуаз) | 1900 |
Вязкость лака при 60% сухого остатка(сантипуаз) | 220 |
Реактивный эквивалент | 220 |
Функциональность | Многофункциональный |
КПД незаполненной системы FR, В-0 | 2-2,5 мас.% Р |
Нанесение эпоксидной смолы | Вулканизирующий агент |
Материал А представляет собой очень стабильную молекулу даже до отверждения, и поскольку он является полимером, он сам по себе имеет относительно высокую Tg ~ 130 °C. На рисунке 1 показан типичный анализ Tg материала А в азоте. Он начинает разлагаться при температуре около 300 °C и оставляет около 40 % твердого остатка при 500 °C.
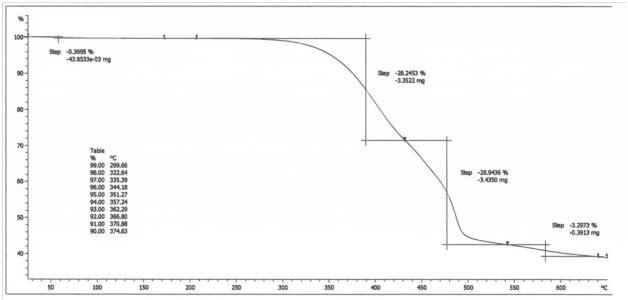
Рис. 1 – Анализ Tg материала А, скорость нагрева 10 град/мин, атмосфера азота.
Подготовка ламината.
Материал А был исследован в качестве агента совместного отверждения для эпоксидных ламинатов. Материал А вместе с фенольным новолаком использовался для отверждения многофункциональной фенольно-новолачной эпоксидной смолы (PEN) и крезол-новолачной эпоксидной смолы (CEN). Вся информация о материалах приведена в Таблице 3. Содержание сухих веществ в лаке поддерживалось на уровне 67% добавлением смеси растворителей МЭК/метиловый эфир дипропиленгликоля (80/20). Из него был приготовлен состав лака с содержанием фосфора 2,4% (в сухом веществе), состав которого показан в Таблице 4.
Таблица 3 – Материалы, использованные при изготовлении ламината.
Имя | Общая информация | Функция |
СД-Новолак | Фенольный новолак (PN) | Вулканизирующий агент |
PEN | Фенол-новолачная эпоксидная смола (ПЭН) | Эпоксидная смола |
Эпоксидная смола CEN | Крезол-новолачная эпоксидная смола (CEN) | Эпоксидная смола |
Метилэтилкетон | Бутан-2-он | Растворитель |
Метиловый эфир дипропиленгликоля | 1-метокси-2-пропанол | Растворитель |
Диметилформамид | N,N-диметилформамид | Растворитель |
2-МИ | 2-метилимидазол | Катализатор |
Стеклянная ткань | Электронное стекло | Армирующий агент |
Медная фольга | Электроосажденный, 1,0 унции/фут2 | Устойчивость к окислению в теплых и влажных средах, а также для точного травления и т. д. |
Таблица 4. Состав эпоксидного ламината 1.
PEN (мас. %) | CEN (мас. %) | Материал А (мас. %) | ПН (мас. %) | 2-МИ (мас. %) |
24,3 | 29,7 | 35,8 | 10.2 | 0,02 |
Добавление катализатора тщательно контролировали путем постепенного добавления небольших количеств раствора 2-метилимидазола (2 MI) (20 мас.% твердых веществ) в диметилформамид (ДМФ) для получения оптимального времени гелеобразования лака - 270 секунд при 171 °C в соответствии с IPC-TM -650 тест 2.3.18. Препрег был изготовлен с использованием стеклоткани (18 дюймов x 72 дюйма), которую непрерывно пропускали через ванну, содержащую лак, и через отжимные валки, так что было получено однородное покрытие. Срезы ткани с покрытием подвешивали на ночь под вытяжкой для медленного испарения растворителя. Препреги изготавливали путем сушки покрытой смолой стеклоткани в предварительно нагретой печи с циркуляцией воздуха при температуре 160°C в течение четырех минут и тридцати секунд, что давало текучесть смолы менее 20,0%. Кроме того, содержание смолы контролировалось на уровне выше 50-55%. Свойства препрега показаны в Таблице 5 ниже.
Таблица 5 - Свойства препрега с материалом А для рецептуры 1.
Состав материала А показан в таблице 4. | IPC-ТМ-650 №. теста | Оценка |
Содержание смолы (мас. %) | 2.3.16.2 | 50-55 |
Время застывания лака (сек) | 2.3.18 | 270 |
Время гелеобразования препрега (сек) | 2.3.18 | 81 |
Расход смолы (%) | 2.3.17 | <20 |
На рис. 2 показан сложный профиль вязкости препрега при повышении температуры смолы B-стадии в режиме испытаний. На рисунке 3 показаны наложенные кривые модуля упругости (G’), модуля потерь (G») и комплексной вязкости (|η|) смолы B-стадии.
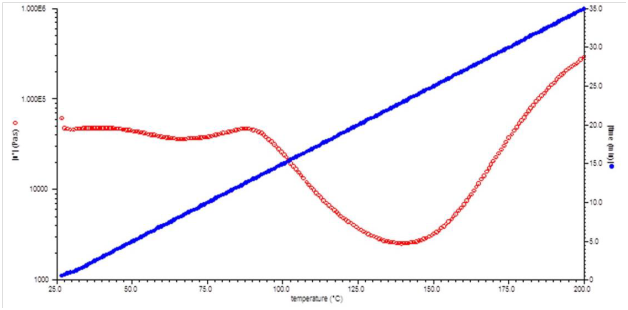
Рис. 2 – Сложный профиль вязкости препрега.
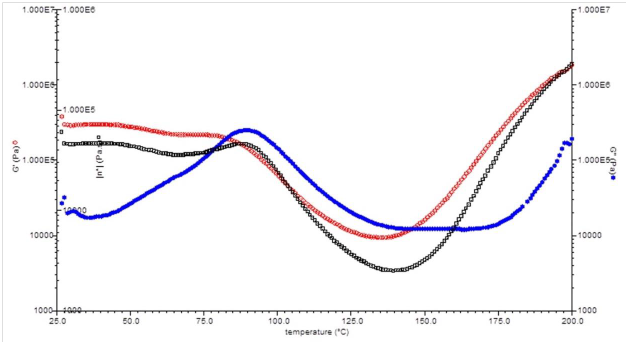
Рис. 3. Наложение кривых модуля упругости (G’), модуля потерь (G») и комплексной вязкости (|η|) смоляной системы B-стадии.
Судя по рисункам 2 и 3, цикл отверждения был разработан для получения хорошей текучести смолы. Низкое начальное давление 10 фунтов на квадратный дюйм применялось при 103-105 ° C (комплексная вязкость препрега составляло около 17560 пуаз х сек) и было достаточным для обеспечения требуемой текучести смолы, как было изучено во время приготовления различных экспериментальных эпоксидных ламинатов. Затем было приложено давление 20 фунтов на квадратный дюйм при температуре 140°С и давление поддерживалось на уровне 20 фунтов на квадратный дюйм до 165°С. Давление снова повысили до 50 фунтов на квадратный дюйм при 165°С и до 100 фунтов на квадратный дюйм, когда пресс достигал 175°С. Давление 100 фунтов на квадратный дюйм было приложено при 175°С и, наконец, давление 220 фунтов на квадратный дюйм было приложено при 195°С. Наконец, пресс поддерживали изотермически при давлении 220 фунтов на квадратный дюйм и 195°C в течение 90 минут. Ламинат показал хорошую текучесть смолы, а толщина конечного ламината составила около 1,3 мм (без меди). Ламинат получил класс V-0 с максимальным временем горения 7 секунд в соответствии со стандартом ASTM D3801-10 с использованием производственной камеры UL-94 (V-0 — максимально возможный рейтинг). Ламинат также был приготовлен с использованием только PEN, а не смеси PEN и CEN, с использованием следующего состава и условий, аналогичных описанным выше.
Таблица 6 – Состав с PEN (Состав 2).
ПЕН (мас. %) | Материал А (мас. %) | ПН (мас. %) | 2- MI (мас. %) |
50,9 | 36,8 | 12,5 | 0,02 |
Основные свойства обоих ламинатов приведены в Таблице 7.
Таблица 7 Сравнительные свойства ламинатов, полученных с использованием составов 1 и 2 и коммерческой безгалогенной системы 37
Формулировка | 1 | 2 | 37 |
Горючесть1 | V-0 | V-0 | V-0 |
Водопоглощение (%) при комнатной температуре 24 часа2 | 0,06 | 0,07 | 0,2 |
Водопоглощение (%) после 60 мин РСТ 3 | 0,22 | 0,24 | 0,69 |
Водопоглощение (%) после 120 мин РСТ 3 | 0,36 | 0,38 | |
288 °C РСТ 60 мин 3 | >20” | >10’ | <10” отказ |
288 °С РСТ 120 мин 3 | <10” отказ | >10’ | |
Прочность на отслаивание (фунты/дюйм ширины) 4 | 8.3 | 7,7 | 9,0 |
Тg ДМА | 192 | 183 | 175 |
ТгgТМА | 170 | 150 | |
КТР (α1, α2) 5 | 33,7; 234,3 | 52,1; 307,2 | |
Td (потеря массы 5%) °C | 416 | 412 | 394 |
Т288 мин 6 | >60 | >30 |
- UL 94;
- IPC-ТМ-650, Метод 2.6.2.1;
- Процедура испытаний IPC-TM-650, метод 2.6.16;
- Процедура испытаний IPC-TM-650; Метод 2.4.8;
- Процедура испытания: IPC-TM-650, метод 2.4.25;
- Процедура испытаний IPC-TM-650, метод 2.4.24.1;
- Рецептура 3 приготовлена с использованием PEN, CEN, материала B (коммерческого соединения на основе фосфора, не содержащего галогенов) и DICY.
Оба ламината имеют очень низкое водопоглощение при комнатной температуре (0,06 и 0,07 соответственно) и низкое водопоглощение после пребывания в автоклаве в течение 120 минут. Удивительно, но образец с одним только PEN показал лучшие результаты в тесте PCT, и на 5 образцах не наблюдалось расслоения после 120 минут пребывания в автоклаве и после погружения в расплавленный припой при 288 °C на 10 минут. Ламинат, приготовленный из эпоксидной смеси, выдержал испытание через 60 минут, но не прошел через 120 минут. Термические и физические свойства ламината со смесью PEN и CEN и только с PEN были схожими, демонстрируя исключительную термическую стабильность с началом разложения при температуре выше 410 °C. КТР (коэффициент термического расширения) до Tg α1 и после Tg α2 был значительно ниже для ламината, приготовленного из смеси PEN и CEN. На рис. 5 показан график ТМА с КТР α1 и α2. В отличие от бифункционального ДОПО- BPA, Материал А представляет собой многофункциональный отвердитель со средним количеством реакционноспособных групп около 5-6. Это обеспечивает высокую степень сшивки, что приводит к высокой Tg. Кроме того, высокая термическая стабильность материала А и высокая плотность сшивки приводят к беспрецедентной термической стабильности отвержденной эпоксидной смолы с началом разложения при >400°C. Эта высокая термическая стабильность также улучшается благодаря уникальному механизму отверждения, который приводит к образованию исключительно стабильных связей.
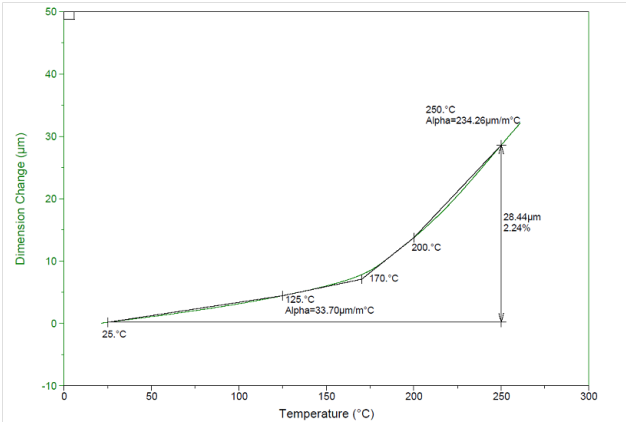
Рис. 4 – КТР α1 и α2 по ТМА.
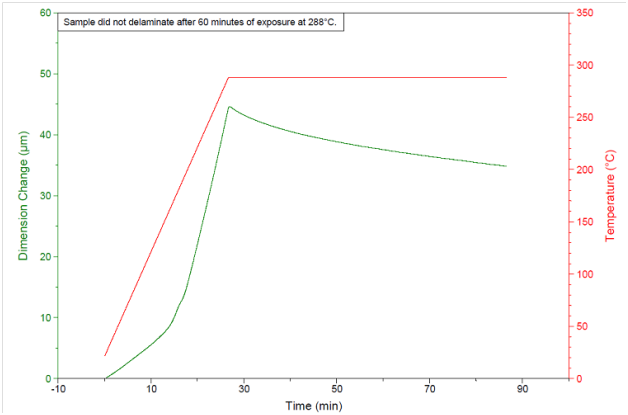
Рис. 5 – Время расслоения ТМА при 288 °C в течение 60 минут.
Отливки из смолы.
Для определения Dk и Df отвержденной композиции были изготовлены отливки из смолы с использованием композиции из Таблицы 8 и условий отверждения, аналогичных тем, которые используются при приготовлении ламината. Диэлектрическая проницаемость( Dk )и тангенс потерь (Df) измерялись на частоте 1 ГГц с использованием процедуры испытаний: IPC-TM-650, метод 2.5.5.9. В дополнение к контрольному образцу были также приготовлены отливки из смолы, содержащие полифениленовый эфир, цианатный эфир (CE) и дициклопентадиен (DCPD) новолака.
Таблица 8 – Состав приготовленных полимерных слепков.
Контроль | DCPD Новолак | CE | Полифениленовый эфир | Коммерческая безгалогенная система | |
CEN | 29 | 28 | 28 | 25 | 35 |
PEN | 24 | 23 | 23 | 20 | 28 |
Материал А | 38 | 37 | 35 | 36 | |
Материал Б | 37 | ||||
Фенольный новолак | 9,2 | 4,5 | 5,8 | ||
DCPD Новолак | 8,3 | ||||
CE | 13 | ||||
Полифениленовый эфир | 14 |
В Таблице 9 показаны Tg, температура начала разложения, а также Dk и Df отливок из смолы, а на Рисунке 6 показано процентное изменение Dk и Df при добавлении полифениленового эфира, CE и новолака DCPD.
CE оказал наиболее сильное влияние как на Dk, так и на Df, за ним следовал полифениленовый эфир. DCPD Новолак оказал наименьшее влияние на снижение как Dk, так и Df. Однако уровень DCPD новолака был самым низким, поэтому этот эффект может быть более значимым при более высоком уровне. К сожалению, даже при таком низком уровне, Tg отвержденного образца значительно снизилась.
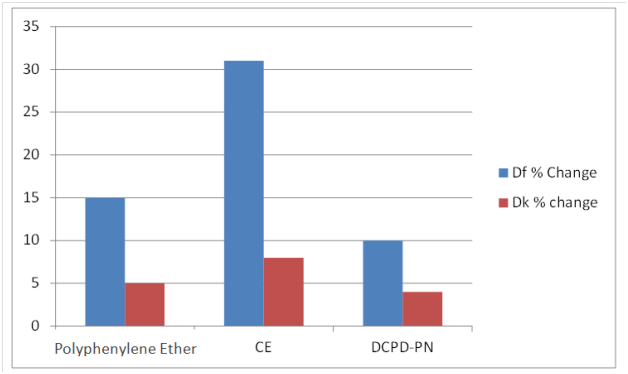
Рис. 6. % изменения Dk и Df при добавлении полифениленового эфира, CE и новолака DCPD.
В составы добавляли полифениленовый эфир - 14 мас.%; CE - 13 мас.%; DCPD-PN - 8,3 мас.% соответственно.
Таблица 9. Результаты Tg, TGA, Dk и Df для экспериментов по отверждению отливок из смолы.
Без добавок | CE | Полифениленовый эфир | DCPD Новолак | Коммерческая безгалогенная система | |
Тg, °С | 175 | 205 | 180 | 165 | 155 |
Температура начала разложения (TGA) | 380 | 365 | 370 | 390 | 345 |
Диэлектрическая проницаемость Dk (при 1 ГГц) | 3.26 | 3.01 | 3.10 | 3.13 | 3.19 |
Диэлектрические потери Df (при 1 ГГц) | 0,019 | 0,013 | 0,016 | 0,017 | 0,034 |
Выводы.
Материал А представляет собой реактивный огнестойкий материал, специально разработанный для высокоэффективных ламинатов. Это полимерный многофункциональный отвердитель на основе фосфора. Высокая степень сшивки при использовании Материала А приводит к высокой Tg, в зависимости от рецептуры. Кроме того, этот материал очень термически стабилен даже до отверждения. Это, в сочетании с уникальным механизмом отверждения, приводит к получению высокотермостойких ламинатов даже при использовании простых эпоксидных новолаков с началом разложения при температуре выше 400 °C. Материал А подходит для применения при высоких температурах. Это позволяет получить V-0 в ненаполненной эпоксидной системе с низким уровнем фосфора (2,5%). Эти свойства в сочетании с низким водопоглощением, совместимостью со смолами с низкими Dk и Df и низким КТР как до, так и после Tg, позволяет использовать материал А в различных областях.