- Главная
- Оборудование для печатных плат
- Оборудование для поверхностного монтажа
- Технологии производства плат и поверхностного монтажа
- Инструмент для печатных плат и Запасные части
- Материалы и Химикаты для печатных плат и поверхностного монтажа
- Гальваническое оборудование
- Лабораторное и аналитическое оборудование
- Сервис и техническое обслуживание
- Как нас найти
- Начало раздела
- Главный технолог
- Технологии производства
- Консультации
- Контакты
Количественный анализ коррозионной стойкости химического покрытия никель-фосфор (Ni-P).
Доктор Лэй Цзинь, доктор Джун Нэйбл, доктор Кешэн Фэн, Ленора Тоскано, доктор Эрни Лонг.
Электронные решения MacDermid Inc.
227 Freight Street, Уотербери, Коннектикут 06702.
АННОТАЦИЯ
Слой химического никеля (EN) часто используется в различных промышленных вариантах. Обычно он используется в качестве барьерного слоя в покрытии электрохимический никель/иммерсионное золото (ENIG) в качестве консерванта для пайки в электронной промышленности. Покрытие обеспечивает отличную коррозионную стойкость и хорошую паяемость. Недостатком этого процесса является возможность гиперактивной коррозии поверхности никеля во время иммерсионного золочения. Возникающий в её результате дефект проявляется в виде серого или черного цвета на границе р никель/золото, известного как «черная КП» и др. Для получения высококачественной продукции важно определять и контролировать коррозионные свойства покрытия EN во время процесса ENIG. К сожалению, количественный анализ коррозионной стойкости слоя EN в печатных платах не проведится В этой статье предлагается метод с помощью прибора последовательного электрохимического восстановления (SERA) для количественной оценки коррозионной стойкости покрытий EN. Данные, полученные этим методом, были проанализированы и сопоставлены со свойствами осадка EN. Метод прост в использовании и может применяться для количественного анализа в промышленных процессах покрытия EN.
ВВЕДЕНИЕ
Консерванты для пайки имеют решающее значение для успешного производства электроники. Поверхностная обработка защищает медные схемы от окисления перед сборкой, обеспечивая прочный контакт между печатной платой и компонентами. Последний этап нанесения паяемого покрытия имеет решающее значение, поскольку, если на этом этапе производства возникают проблемы с качеством, во многих случаях они могут оставаться незамеченными до завершения сборки продукта. Обнаружение черной КП на никеле после сборки приводит к образованию дефекта, который невозможно восстановить.
В конечном счете, EN действует как барьерный слой между медью и верхним слоем драгоценного металла, такого как золото или палладий. Медь легко мигрирует через слой золота, окисляется, а затем делает покрытие непаяемым. Таким образом коррозионная стойкость покрытия из химического никеля (EN) является очень важной характеристикой.
По определению, иммерсионное золото может паяться только в результате некоторой коррозии никеля. Поэтому необходимо поддерживать тонкий баланс, чтобы обеспечить достаточное осаждение золота без чрезмерной коррозии никеля. Помимо коррозионной стойкости электролита золотого покрытия, слой химического никеля должен сохранять коррозионную стойкость к воздействию окружающей среды. И в качестве барьерного слоя, и в качестве экологически устойчивого покрытия, финишные покрытия, содержащие EN, имеют самые высокие характеристики среди альтернативных бессвинцовых покрытий [1,3,4,7], имеющихся в настоящее время на рынке.
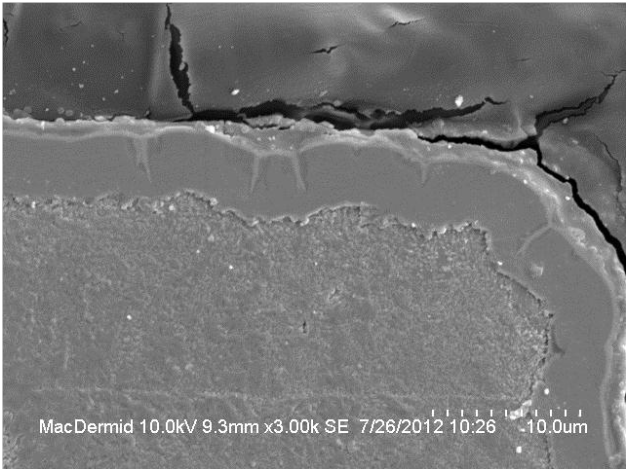
Рис. 1. Типичная коррозия (черная линия) никеля (BLN) после покрытия ENIG.
Современные методы измерения коррозионной стойкости EN в основном ограничиваются качественными методами, такими как испытание погружением в азотную кислоту. Субъективный подход к этим методам оставляет место для различных интерпретаций. В этой статье мы представляем простой подход для анализа коррозионной стойкости покрытий EN с помощью анализа последовательного электрохимического восстановления (SERA).
SERA — это метод, который в основном используется для анализа толщины металла и оксидов металлов с использованием реакции восстановления или окисления. Измеренный электрохимический потенциал отображается в зависимости от времени анализа при заданной приложенной плотности тока.
С помощью закона Фарадея можно количественно определить толщину металла или поверхностного оксида. Разным материалам соответствуют определенные электрохимические потенциалы, поэтому форма графика дает информацию о природе и качестве анализируемой поверхности.
2. Эксперименты.
Первоначально тестировали раствор электролита с pH 3,5 ( 2 моля KCl с добавкой ацетата натрия). Электролит продували азотом (N2) при комнатной температуре (КТ). Схема 1 представляет собой схематическое изображение измерений SERA на печатных платах. Деталь, подлежащая анализу, контактирует с электролитом KCl с помощью уплотнительных колец (1,6 мм), которые образуют уплотнение вокруг верхней и нижней части печатной платы. Перед анализом на 30 секунд подается ток с плотностью +500 мкА/см2 для удаления пассивации поверхности никеля. Затем плотность тока устанавливается равной -1000 мкА/см2 на 90 секунд, чтобы вызвать коррозию поверхности никеля. Записывается картина коррозии SERA вместе через 90 секунд. Более подробное объяснение принципов SERA можно найти в цитатах из литературы [2,5,6].
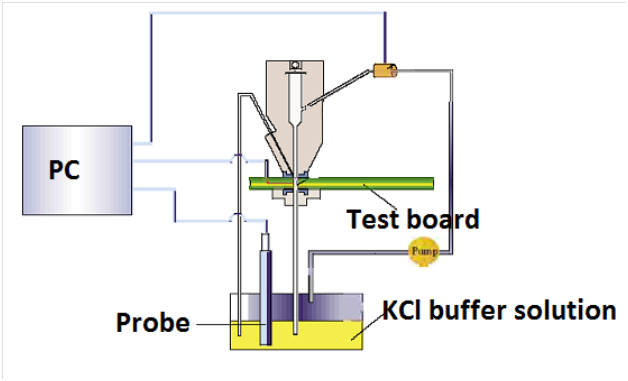
Рис. 1. Схематическое изображение испытательного оборудования SERA.
3. Результаты и их обсуждение.
3.1 Определение подходящих электролитов.
Было обнаружено, что различные электролиты с различным pH и концентрацией хлор ионов (Cl- )играют роль в коррозии поверхности никеля. Для определения подходящих электролитов и надежности этого метода использовались три коммерческих продукта с диапазоном стойкости к поверхностной коррозии от низкой до высокой. С помощью запатентованного метода было определено, что образцы имеют различное массовое процентное содержание фосфора (мас.% P), а именно 7, 9 и 11.
Сначала мы сравнили эти 3 различных образца, используя 0,2 молярный раствор электролита HCl, доведенный с помощью КОН до pH 4,0. Как показано на рисунке 2, образец с самой низкой коррозионной стойкостью (7 вес. % P) показал значительное падение потенциала, уменьшившееся более чем на 0,2 В, между отметкой 15 и 45 секунд, тогда как потенциал образца с 9 вес. % P уменьшился менее чем на 0,15 В за тот же интервал времени. Образец с самой высокой коррозионной стойкостью (11 мас. %P) показал самый высокий коррозионный потенциал и не показал каких-либо существенных изменений потенциала в течение всего периода измерения. Затем эксперимент повторяли с электролитом, приготовленным из раствора 2 моля KCl и 15 г/л мышяка натрия (NAAc), доведенного до pH 3,5 с помощью HAc. Формы диаграмм коррозии отличаются от тех, что показаны на рисунке 3. Образец с самой высокой коррозионной стойкостью оставался стабильным при напряжении, близком к 0,58 В, на протяжении всего испытания на коррозию, тогда как образец с массой 9 вес %P имел стабильное напряжение 0,18 В, а образец с самой низкой коррозионной стойкостью - 7 вес. %P EN достиг минимума 0,05 В, что указывает на лучшее разрешение, чем при тесте с использованием 0,2 моля раствора электролита. В результате данной работы для всех испытаний был выбран последний электролит.
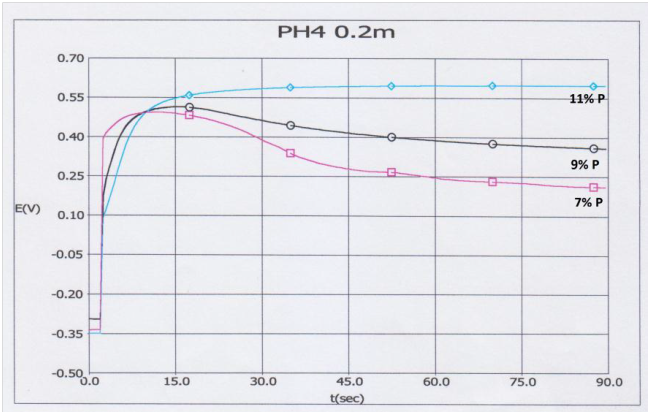
Рис. 2. Испытание SERA на коррозию, сравнивающее поверхности EN с содержанием P 7, 9 и 11 мас. % с 0,2 молями HCl при pH 4,0.
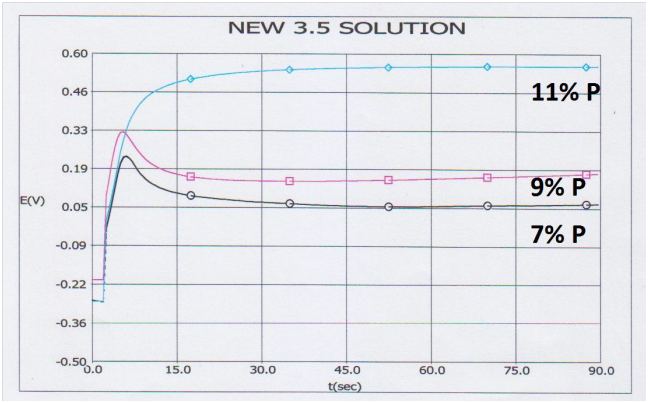
Рис 3. Испытание на коррозию SERA, сравнивающее 7, 9 и 11 вес. %P EN поверхности с 2 молями KCl.
3.2 Надежность.
Предложенный метод определения коррозионной стойкости поверхности EN является надежным.
Как было показано ранее при использовании другого электролита, график коррозии в зависимости от коррозионной стойкости образцов EN остался прежним. Самая высокая коррозионная стойкость, соответствующая более высокому весовому проценту. Образец %P имеет тенденцию иметь более высокий потенциа по сравнению с образцом EN с более низкой коррозионной стойкостью. Относительный порядок диаграмм коррозии образцов может быть полезным инструментом для сравнения % массы P в покрытиях EN (внутри той же ванны EN-нанесения) и, следовательно, коррозионное поведение.
Чтобы дополнительно доказать это утверждение, мы составили коммерческую ванну EN ( 7~8 мас.% P) на 6 оборотах металла (MTO) и исследовали образцы печатных плат с гальваническим покрытием через каждые 0,5 MTO по % массе P и провели испытание на коррозионную стойкость по методу SERA. На рисунке 4 показаны тенденции как % P, так и потенциала SERA на протяжении всего срока службы ванны. Видно, что вес. % P и окислительный потенциал SERA одинаково реагировали на срок службы ванны. Хорошо известно, что в одном и том же продукте EN чем выше вес. % P, тем лучше коррозионная стойкость покрытия EN, и это совпадение указывает на очень хорошую надежность предлагаемого метода.
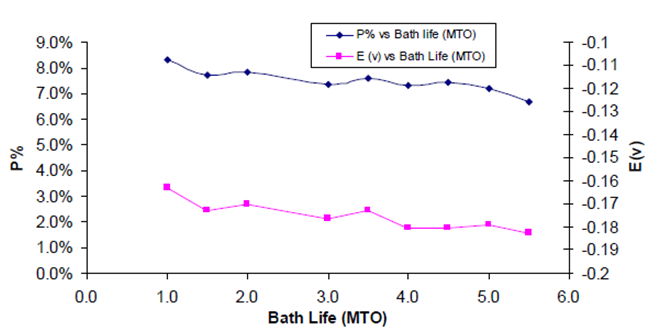
Рис. 4. Сравнение масс. содержания % P с SERA дает разные результаты при разном сроке службы ванны. Для этого эксперимента использовалась доступная в продаже EN-ванна.
Очень интересно, что когда E(v) отображается как функция весовой концентрации % P на протяжении всего срока службы ванны выявляется линейная зависимость. Как показано на рисунке 5, для линейного графика было получено значение R2=0,97. Это дополнительное свидетельство хорошей надежности метода SERA для испытаний на коррозионную стойкость покрытия EN. Когда он калибруется с помощью линейной зависимости, можно даже определить вес. %P в разных местах печатной платы . По сравнению с обычными методами определения мас. %P, которые сложны и требуют много времени, этот вариант относительно простой и понятный.
Как указано выше, этот метод может быть полезным инструментом для сравнения и количественной оценки коррозионного поведения покрытия EN. Для получения точных результатов необходимо внимательно следить за одним ключевым фактором. Это потенциал пассивации поверхности EN. Этот тонкий оксидный слой не стандартизирован для всех образцов и, вероятно, будет мешать измерению. Чтобы ограничить эти помехи и минимизировать отклонения, вызванные окисленной поверхностью, сначала применяют катодный ток в качестве предварительной обработки для уменьшения пассивированного слоя. После удаления пассивированного слоя подается анодный ток, чтобы начать эксперимент. Таким образом, перед экспериментом по анализу коррозии EN методом SERA рекомендуется подавать первоначальную плотность тока +500 мкА/см2 в течение примерно 30 секунд, чтобы уменьшить пассивированный слой. Этот шаг обеспечивает лучшую поверхность EN перед испытанием на коррозию. Затем начинают измерение коррозии с использованием плотности тока -1000 мкА/см2 на площади образца 0,0201 см2. Время коррозии должно быть установлено достаточно большим.
Тип электролита.
Использование электролита важно, поскольку оно повлияет на коррозионное поведение поверхности, как было сказано ранее.
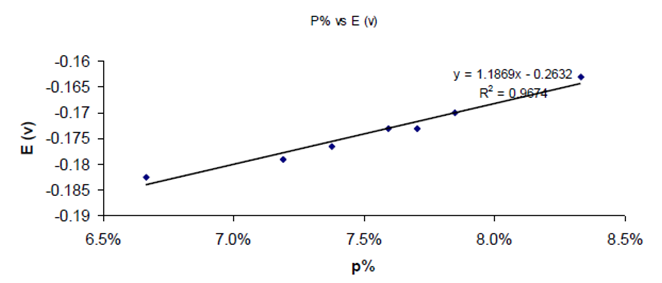
Рис. 5. График окислительного потенциала после испытания в зависимости от P% в покрытиях EN.
4. Анализ предлагаемого метода.
4.1 Вариант контроля качества.
Этот метод также можно использовать в качестве простого метода контроля качества при нанесении EN покрытия. Как показано в следующем примере, две коммерчески доступные ванны EN (M и U) с целевым содержанием 8 мас. %P были выдержаны до нескольких оборотов металла (МТО).
Несколько образцов были помещены в ванну с разными интервалами МТО. Когда коррозионная стойкость была измерена с помощью этого метода, графики коррозии, показанные на рисунке 6a, указывают на очень стабильное поведение коррозионной стойкости для этих коммерческого продукта M, тогда как коррозионное поведение коммерческого продукта U (показанное на рисунке 6b) показало изменения на протяжении всего срока службы ванны. Эти результаты показывают лучшее качество нанесенного EN, полученного из продукта M, чем из продукта U.
Что касается контроля качества покрытия EN, еще одним очень важным параметром является равномерность нанесения EN на печатные платы. В некоторых случаях коррозия отложений EN на маленьких контактных площадках ведет себя иначе, чем на больших контактных площадках на той же печатной плате. Здесь мы выбираем популярную коммерчески доступную ванну EN (продукт U), чтобы проверить однородность нанесения на тестовой плате. Плату поместили в ванну EN на 20 минут, чтобы нанести слой никеля толщиной около 200 микродюймов. Как отмечено на рисунке 7а, для испытания на коррозию SERA были выбраны 3 точки. Результаты (рис. 7b) показали, что большая КП (точка 1) имела лучшую устойчивость к коррозии, тогда как маленькие КП (точки 2 и 3) показали пониженный окислительный потенциал, что указывает на худшую коррозионную стойкость. Это указывает на плохую однородность отложения EN на испытательной плате, а предлагаемый метод обеспечивает прямое доказательство качества этого коммерческого продукта EN.
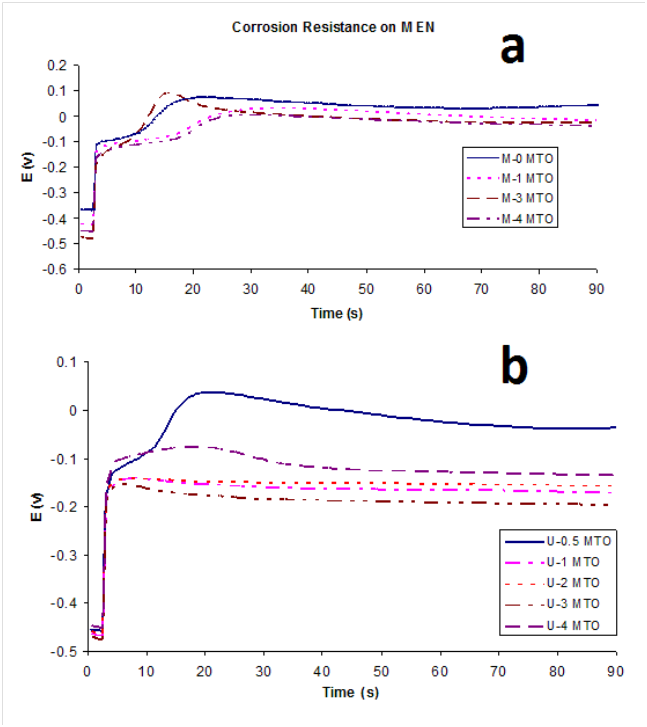
Рис. 6. График коррозии EN на разных интервалах MTO.
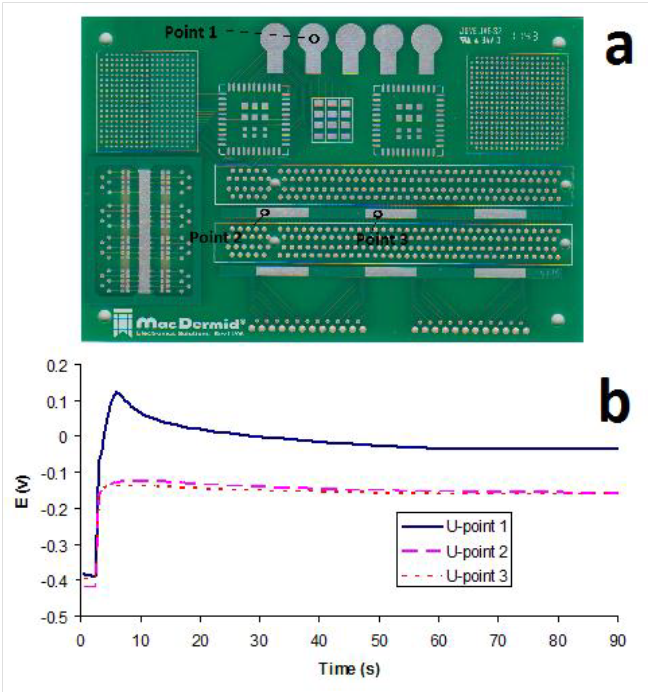
Рис. 7. Коррозионная стойкость на различных участках тестовой платы.
4.2 Сравнение коррозионного поведения различных продуктов EN.
Поскольку большинство продуктов EN уникальны и имеют различное коррозионное поведение, метод SERA можно использовать как быстрый и простой метод для их дифференциации. Как показано на рисунке 8, мы использовали три различных состава нанесения EN с одинаковой массой. Содержание %P дало разные диаграммы коррозии, что указывает на различную коррозию, хотя содержание P в этих трех коммерческих продуктах очень похоже. Считается, что не только содержание P, но и процент серы (S%), морфология поверхности и некоторые другие факторы играют роль в коррозионной стойкости. Традиционное тестирование на азотной кислотой (HNO3) может дать только субъективный, неточный ответ, который трудно интерпретировать. Коррозионное поведение и результаты, полученные при тестировании погружением в HNO3, могут быть противоречивыми. Предлагаемый метод позволяет количественно зарегистрировать коррозионное поведение различных покрытий EN.

Рис. 8. Сравнение различных коммерческих покрытий EN.
4.3. Сравнение составов электролитов.
В настоящее время исследователи по-прежнему уделяют пристальное внимание совершенствованию рецептуры никеля, полученного химическим способом, чтобы смягчить проблемы «черной площадки» или других проявлений коррозии. Коррозионное поведение является одним из наиболее важных параметров для определения потенциального поведения EN в отношении проблем с черными КП. Метод SERA представляет собой очень полезный инструмент для проверки покрытий EN с различными составами. На рисунке 9 показан пример коррозионного поведения, которое возникает при изменении концентрации стабилизатора S в составе химического никеля. Было высказано предположение, что чем меньшая концентрация используемого в ванне стабилизатора S, тем более высокую коррозионную стойкость может иметь полученный осадок EN. Это утверждение теперь подтверждается использованием метода SERA, как показано на рисунке 9. Чем ниже концентрация стабилизатора S, используемого в ванне, тем выше окислительный потенциал полученный при методе SERA, что указывает на высочайшие свойства коррозионной стойкости. С увеличением концентрации стабилизатора S окислительный потенциал падает. Таким образом, этот новый метод представляет собой прямой, эффективный, количественный и понятный инструмент для исследователей покрытия EN.
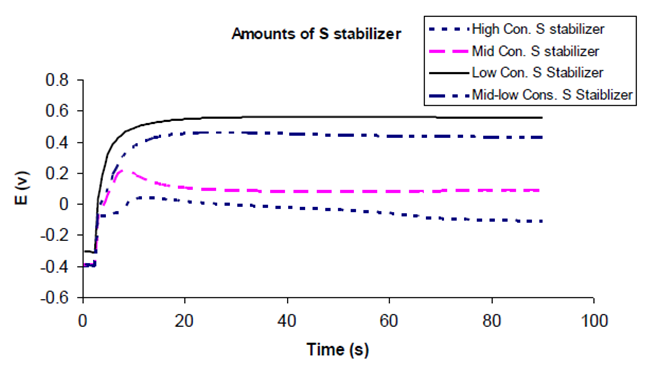
Рис. 9. Результаты различного коррозионного поведения покрытий EN с различной концентрацией стабилизатора S в ванне EN.
5. Вывод.
Представленные здесь результаты показывают, что новый метод испытаний SERA можно применять на регулярной основе для оценки коррозионной стойкости покрытий EN. Этот метод представляет собой относительно простой, быстрый и количественный анализ. В пределах одной ванны EN этот метод можно использовать даже для определения P% в разных точках печатной платы. Этот метод также может применяться в других случаях, таких как контроль качества покрытия EN, проверка продукции и сравнение рецептур.
Благодарности.
Мы хотели бы поблагодарить г-на Льва Тайцаса (Центр исследований и разработок, MacDermid электронные решения) за его помощь в настройке оборудования SERA и большое спасибо г-же Вэй Янь (паяемые покрытия, MacDermid электронные решения ) за ее помощь в установке EN-ванн и сбор данных.
Использованная литература.
- [1] Д. Беккет, « Опыт эксплуатации органического стабилизатора химического никеля.» Материалы ежегодной международной технической конференции 2008 г.
- [2] П. Братин, М. Павлов, Г. Чалыт, Р. Глузман, «Новое применение метода SERA - оценка защитной эффективности органических консервантов паяемости.» Материалы ежегодной технической конференции (1995г.).
- [3] Ю. Лю, Д. Беккет, Д. Хоторн, «Влияние термообработки, паяемых покрытий на коррозионные свойства черных никелевых пленок методом химического восстановления»., Прикладная наука о поверхности. (2011 г.).
- [4] Н. Мицюс, «Коррозионная стойкость никеля со средним и низким содержанием фосфора методом химического восстановления.» Ежегодная международная техническая конференция (2008 г.).
- [5] Д.М. Тенч, Д.П. Андерсон, «Электрохимическая оценка паяемости олова и свинца.» Гальваническое покрытие и обработка поверхности (1990 г.).
- [6] Д.М. Тенч, М.В. Кендиг, Д.П. Андерсон, Д.Д. Хиллман, Г.К. Люси, Т.Дж. Гер, «Производственное применение метода испытания паяемости SERA.» Технология пайки и поверхностного монтажа (1993 г.) .
- [7] Л.М. Тоскано, Э. Лонг, В. Поу, Д.М. Кологе, К. Коясу, К. Нишу, «Метод обработки металлических поверхностей, пригодных для изготовления электронных корпусов», 2012 г.