- Главная
- Оборудование для печатных плат
- Оборудование для поверхностного монтажа
- Технологии производства плат и поверхностного монтажа
- Инструмент для печатных плат и Запасные части
- Материалы и Химикаты для печатных плат и поверхностного монтажа
- Гальваническое оборудование
- Лабораторное и аналитическое оборудование
- Сервис и техническое обслуживание
- Как нас найти
- Начало раздела
- Главный технолог
- Технологии производства
- Консультации
- Контакты
Гальваническое заполнение сквозных отверстий медью на платах различной толщины.
Кешэн Фенга, Билл ДеСесария, Майк Юб, Дон ДеСальвок, Джим Ватковскиа.
а) МакДермид, 227 Freight Street, Уотербери, Коннектикут 06702.
б) Тайваньский технический центр MacDermid.
в) Технический центр МакДермид в Сучжоу.
Electroplated Copper Filling of Through Holes on Varying Substrate Thickness.
Kesheng Fenga, Bill DeCesarea, Mike Yub, Don DeSalvoc, Jim Watkowskia
a)MacDermid, 227 Freight Street, Waterbury, CT 06702.
b)MacDermid Taiwan Technical Center.
c)MacDermid Suzhou Technical Center.
Авторский перевод ЛЕЙТЕСА ИЛЬИ, гл.технолога ООО РТС Инжиниринг.
АННОТАЦИЯ.
В этой статье обсуждается процесс заполнения медью сквозных отверстий в конструкциях межсоединений высокой плотности. Процесс состоит из двух циклов кислотного меднения. В первом цикле используется периодическое импульсное обратное гальванопокрытие для формирования перемычки в середине отверстия, а затем наносится гальваническое покрытие постоянным током, чтобы заполнить образовавшиеся в результате переходные отверстия. Этот процесс может обеспечить бездефектное заполнение отверстий с медным покрытием на поверхности толщиной менее 25 мкм, с ямочкой менее 5 мкм для плат с толщиной 0,2 мм и 0,25 мм. Этот процесс был разработан для внедрения в специально сконструированные вертикальные машины непрерывного действия (VCP), что позволяет сократить объем капитального оборудования по сравнению с имеющимися горизонтальными конвейерными гальваническими машинами. Химические компоненты, медь, кислота и добавки, оптимизируются экспериментальным путем с помощью планирования экспериментов. Определены критические параметры и их влияние на образование полости, на этапе формирования соединения они оценивается количественно. Концентрации добавок и меди играют ключевую роль в уменьшении дефектов при формировании результирующего переходного отверстия. Высокопроизводительный процесс заполнения переходных отверстий используется для заполнения переходных отверстий с глубиной полости на поверхности менее 5 микрон при одновременном нанесении примерно 12 микрон на поверхности. Тонкая поверхность меди обеспечивает четкость линий без необходимости планаризации или шлифовки. Механические свойства нанесенного покрытия соответствуют всем стандартам IPC или превосходят их. Этот процесс применим как к сквозным отверстиям просверленным лазером, так и к отверстиям, просверленным механически. Лазерно-сверлильные сквозные отверстия заполняются быстрее, чем отверстия, просверленные механически. Однако механически просверленные отверстия имеют меньшую тенденция к образованию дефектов, вызванных сверлением, особенно при диаметрах отверстий меньше 0,1 мм. Этот процесс показал способность заполнения сквозных отверстий в более толстых платах от 0,4 мм до 0,8 мм, на которых продолжаются дальнейшие исследования.
ВВЕДЕНИЕ.
Заполнение смолой или пастой сквозных отверстий в платах во многих случаях в последние годы было частью технологии сборки, особенно на подложках ИС. Однако увеличение плотности схем и конструкций в сочетании с устройствами большей мощности добавили дополнительное требование по измерению терморегулирования. Заполнение этих сквозных отверстий медью дает много преимуществ, таких как снижение несоответствия КТР, обеспечивая стабильный техпроцесс для заполнения микроотверстий и измерения терморегулирования для силовых устройств. Начали развиваться новые технологии для полного заполнения сквозных отверстий и отверстий в в HDI платах и IC (подложках ИС). Одним из подходов к заполнению сквозных отверстий медью является технология заполнения постоянным током для тонкой основной платы с просверленными лазером X-отверстиями, как показано ниже (рис. 1).
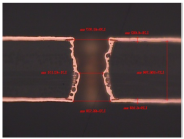
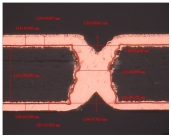
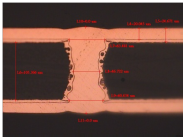
Сквозное отверстие Сквозное отверстие во время Сквозное отверстие после заполнения медью. заполнения медью на этапа заполнения. «переходном» этапе.
Рис. 1. Этапы заполнения медью с помощью технологии заполнения постоянным током.
Толщина медного покрытия на поверхности может составлять менее 25 мкм, толщина ядра около 100 мкм и диаметр микроотверстия около 100 мкм (50-70 мкм посередине). Процесс заполнения состоит из двух этапов. На начальном этапе медь преимущественно откладывается в середине сквозного отверстия до тех пор, пока стенки отверстия в центре отверстия не сомкнутся, в результате чего образуются два слепых микроотверстия. Этот этап называется «мостиком». Второй этап заключается в заполнении полученного двойного слепого переходного отверстия. Первая химия и первый шаг процесса гальванического покрытия идеально подходят для заполнения сквозных отверстий медью. Однако покрытие с постоянным током имеет ограничение по толщине подложки. Когда толщина подложки превышает 200 мкм, склонность к образованию полостей возрастает (рис. 2), а толщина меди на поверхности увеличивается выше 25 мкм. Увеличение количества полостей может снизить надежность, в то время как увеличенная толщина поверхности меди снижает способность формировать узкие линии и сокращать занимаемое пространство. Эти ограничения усугубляются для плат с механически просверленными сквозными отверстиями.
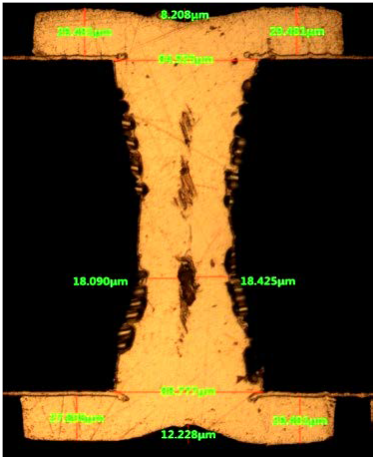
Рис. 2. Дефекты в процессе покрытия постоянным током при толщине платы выше 200 МКМ.
Двухэтапная технология заполнения отверстий.
Двухэтапная концепция применяется при двухэтапном нанесении покрытия, первый этап состоит из формирования «перемычки» периодическим импульсным током, а затем заполнение полученного двойного слепого отверстия с помощью процесса заполнения переходного отверстия. Комбинированные процессы позволяют получить медь без дефектов при технологии заполнения сквозных отверстий, сформированых как лазерным, так и механическим сверлением. Сквозные отверстия изготавливались стандартными процессами первичной металлизации, включая очистку перманганатом или плазмой, удаление замазывания торцев, химическим меднением или процессом прямой металлизации, такой как Blackhole, делающими отверстия проводящими. Чтобы получить проводящий медный слой внутри сквозного отверстия, можно использовать контактирование, чтобы убедиться, что сквозные отверстия имеют хорошую проводимость. Химический состав и технологические циклы предварительной металлизации не были изменены.
Процесс меднения.
Шаг «мостового» соединения сформированногос помощью периодического импульсного обратного покрытия.
Периодическое импульсное обратное покрытие —это широко используемый процесс электролитического меднения. За последнее десятилетие эта технология получили широкое распространение в платах со сквозными отверстиями большого удлинения. Практика периодической импульсной гальваники продолжает развиваться. Новые выпрямители и программное обеспечение теперь обеспечивают большую гибкость в работе, включая формирование асинхронных импульсных волн для ускорения нанесения меди в центре сквозных отверстий, т.е. до 5 раз выше по сравнению с обычным импульсными процессами. Гальваническая медь сливается в середине отверстия, образовав два противоположных друг другу переходных отверстий, как показано на рисунке 3. Этот процесс называется этапом «мостового перекрытия». Стандартизированная вертикальная ячейка для заполнения была разработана для получения нового типа покрытия внутри сквозных отверстий. Вертикальная гальваническая ячейка, оснащенна нерастворимой анодной сеткой из IrO, и предлагает самый широкий рабочий диапазон плотности тока для заполнения сквозных отверстий. Дополнительные соображения по вертикальной гальванической ячейкой включает в себя защиту анода, регулируемое расстояние между анодом и катодом, соотношение площадей, перемешивание панели, движение раствора и систему крепления панели. После этапа соединения два противоположных переходных отверстия заполняются эффективным кислотным раствором меднения для завершения процесса заполнения медью сквозного отверстия, как показано на рисунке 4.
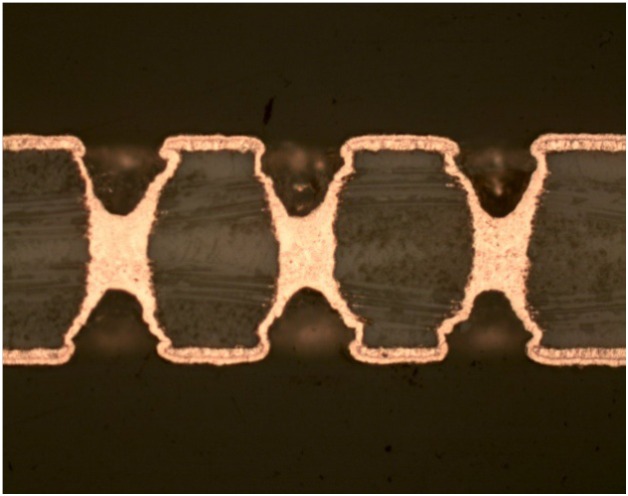
Рис. 3. Разрез после этапа формирования «Мостового» соединения.
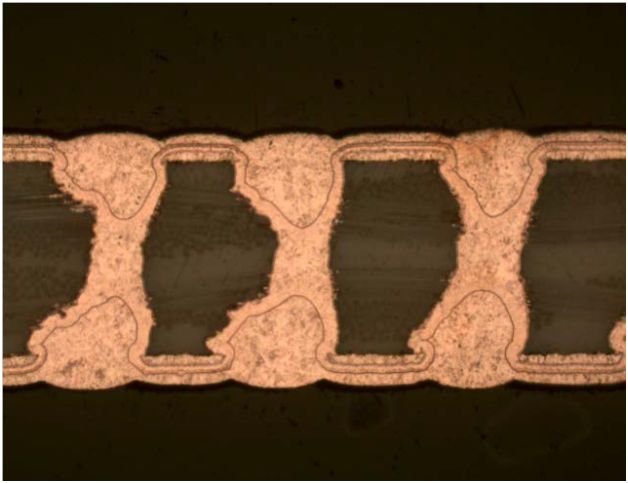
Рис. 4. Разрез после этапа заполнения.
Химический состав на этапе формирования «мостового» соединения.
Химический процесс периодического импульсного обратного кислотного меднения, используемый на мостовом этапе, представляет собой производственную химию. Этот процесс включает специально разработанную систему органических добавок для импульсного нанесения покрытия. Компоненты электролита - это сульфат меди (медный купорос), серная кислота и хлорид-ионы - типичны для стандартных кислых растворов меднения. Чтобы изучить взаимодействие химических компонентов, были оптимизированы концентрации медного купороса, серной кислоты и добавок при экспериментальных условиях, выбранных при планирование экспериментов для достижения хорошего заполнения отверстий, производительности и отсутствия полостей в центре сквозных отверстий. В качестве ограничения при планирование экспериментов концентрация сульфата меди и серной кислоты поддерживали ниже 350 г/л, чтобы предотвратить образование кристаллов сульфата меди в растворе. Платы со сквозными отверстиями, использованные при планирование экспериментов, представляли собой платы, просверленные лазером, с толщиной сердцевины 200 мкм, диаметром отверстий 100 мкм. После этапа перекрытия 10 сквозных отверстий были проверены с помощью поперечного сечения для каждого проверяемого состояния. В медных заполненных сквозных отверстиях присутствовали полости, как показано на рисунке 3 выше.
Химическая оптимизация.
ДИАГРАММА 1. РЕЗУЛЬТАТЫ ПЛАНИРОВАНИЯ ЭКСПЕРЕМЕНТОВ ПО КОНЦЕНТРАЦИИ ДОБАВОК,
ВЛИЯЮЩЕЙ НА ФОРМИРОВАНИЕ ПОЛОСТЕЙ НА ЭТАПЕ «МОСТООБРАЗОВАНИЯ».
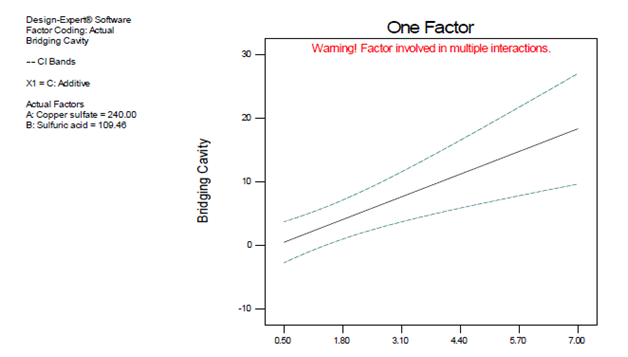
Рис. 4. Разрез после этапа заполнения.
ДИАГРАММА 2. РЕЗУЛЬТАТЫ ПЛАНИРОВАНИЯ ЭКСПЕРЕМЕНТОВ ПО ВЛИЯНИЮ НА ФОРМИРОВАНИЕ
ПОЛОСТЬ КОНЦЕНТРАЦИИ СУЛЬФАТА МЕДИ И СЕРНОЙ КИСЛОТЫ, ПРИ КОНЦЕНТРАЦИИ ДОБАВОК 0,5 МЛ/Л.
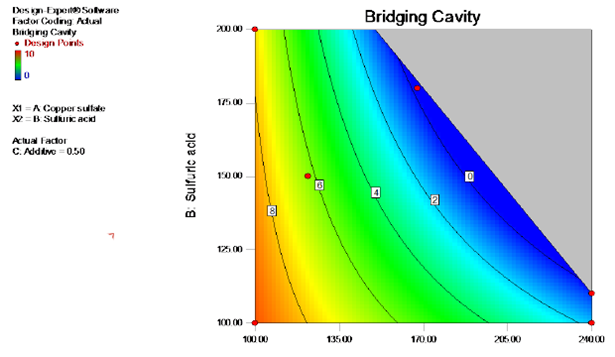
Рис. 4. Разрез после этапа заполнения.
Медный купорос.
Эксперименты показали, что концентрации добавок и меди играют важную роль в получении меди без полостей. При нанесении покрытия на этапе мостового соединения важно иметь меньшее количество добавок и более высокую концентрацию сульфата меди, как показано на диаграммах 1 и 2. Одно из лучших сочетаний каждого компонента — медный купорос 240 г/л, серная кислота 110 г/л и добавка 0,5 мл/л.
Этап заполнения микроотверстий посредством покрытия постоянным током.
Технология заполнения микроотверстий электролитической медью широко используется при производстве HDI плат. Новый процесс производственного меднения используется для заполнения микроотверстий на этапе после перекрытия. Это обеспечивает тонкое медное покрытие на поверхность панели с минимальной глубиной ямок, как показано на рисунке 5 ниже.
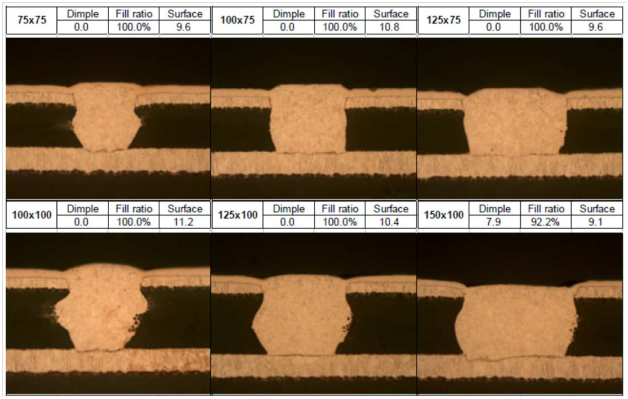
Рис. 5. Процесс меднения с помощью заполнения (единицы в мкм).
Комбинированные процессы покрытия, начиная с формирования перемычки и проходящие через этапы заполнения, обеспечивают технологию заполнения медью на более толстых платах с сквозными отверстиями разного диаметра.
Медные заполнители с различной толщиной ядра.
Эту технологию заполнения отверстий медью можно применять к платам с различной толщиной ядра и геометрией отверстий.
Платы с толщиной ядра 200 мкм, содержащие просверленные лазером сквозные отверстия диаметром 100 мкм КП на поверхности и диаметром 50-70 мкм в середине отверстия.
Сквозные отверстия, просверленные лазером, требуют меньше времени на формирование перемычки, чем отверстия, просверленные механически. Просверленные лазером сквозные отверстия заполняются примерно за 30 минут при толщине сердцевины 200 мкм. Когда просверленные лазером отверстия показали несоответствие диаметра в середине отверстий, как показано на рисунке 3, без полостей в заполненных медью сквозные отверстия еще можно получить. Время нанесения покрытия для сквозного заполнения составляло около 50 минут. Полное медное покрытие на поверхности составляло примерно 20 мкм, как показано на рисунке 3.
Платы с толщиной ядра 200 или 250 мкм, содержащие механически просверленные отверстия диаметром 100 мкм.
Время покрытия механически просверленного сквозного отверстия составляет примерно 60 минут для этапа перекрытия и примерно 50 минут для этапа заполнения. Покрытая медью поверхность имеет толщину около 25 мкм, как показано на рисунке 6.
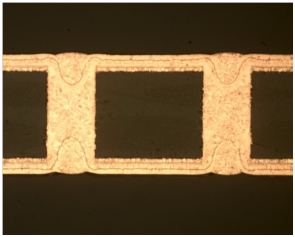
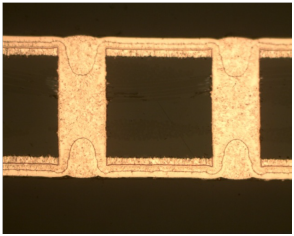
Рис. 6. Механически просверленное сквозное отверстие, толщина ядра 200 мкм.
Платы с толщиной ядра 400 мкм, содержащие механически просверленные отверстия диаметром 100 мкм.
Для более толстых плат с толщиной ядра 400 мкм и механически просверленных отверстий диаметром 100 мкм, требуется более длительное время формирования перемычки. Время нанесения покрытия на этапе формирования перемычки составляло примерно 120 минут, тогда как время заполнения переходного отверстия оставалось равным 50 минутам. Общая толщина медного покрытия поверхности составляет около 35 мкм.
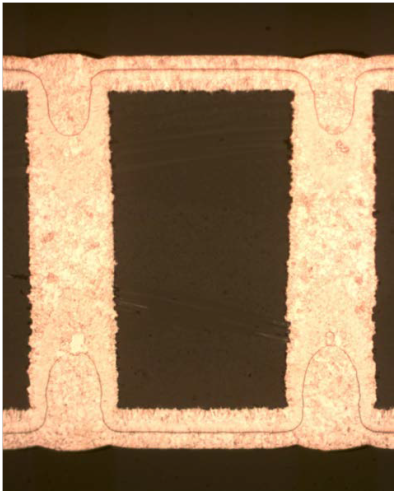
Рис. 7. Механически просверленное сквозное отверстие диаметром 100 мкм, при толщине сердечника 400 мкм.
Плата с толщиной ядра 800 мкм и механически просверленными сквозными отверстиями.
Становится сложно соединить панели с толщиной сердцевины 800 мкм. В отверстиях диаметром менее 250 мкм наблюдались полости.
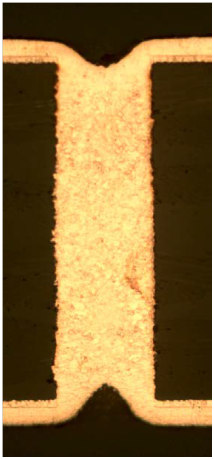
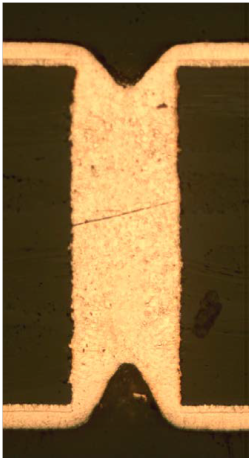
Рис. 8. Механически просверленное сквозное отверстие диаметром 250 и 300 мкм, толщина ядра 800 мкм. После этапа заполнения за 240 мин.
Для сквозных отверстий большего диаметра требуется больше времени для заполнения полученных переходных отверстий, что приводит к более толстому медному покрытию на поверхности платы.
Рентгеновское обследование.
Большая часть оценки проводилась под микроскопом с использованием поперечных сечений. Рентгеновский контроль применялся для проверки плат с толщиной ядра 200 мкм, со сквозными отверстиями, просверленным как механически, так и лазером. Рентгенологическое исследование, после двухэтапного процесса нанесения покрытия показало, что заполненные медью сквозные отверстия, не имеют дефектов, как показано на рисунке 9.
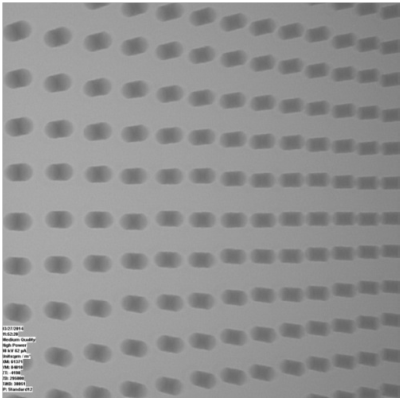
Механически просверленные сквозные отверстия с медным заполнением.
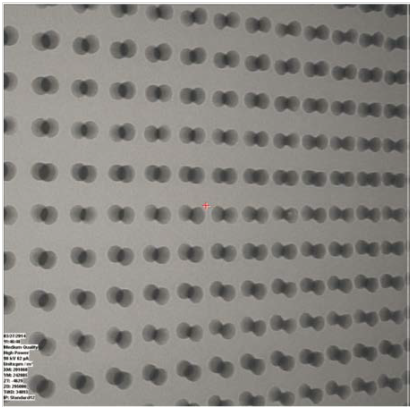
Сквозные отверстия, просверленные лазером и заполненные медью.
Рис. 9. Рентгеновское изображение на плате с толщиной сверления 200 мкм.
Физические свойства.
Физические свойства покрытия имеют решающее значение для обеспечения приемлемого качества готовой платы. Прочность на растяжение и процентное удлинение измеряли с помощью производственного устройства для испытания на растяжение. Результаты приведены в таблице 1.
ТАБЛИЦА 1. РЕЗУЛЬТАТЫ ПО УДЛИНЕНИЮ И ПРОЧНОСТИ НА РАСТЯЖЕНИЕ.
Цикл нанесения покрытия | № образца | Покрытая медью Толщина (мил) | Разрывная сила (фунт-сила) | Вес (г) | удлинение (%) Растяжение | Предел прочности на разрыв (PSI) |
Медное покрытие с формированием перемычки плюс процесс заполнения. | 1 | 2,82 | 62,75 | 0,9726 | 21,92 | 47098,0 |
2 | 3,23 | 72,83 | 1,1146 | 21,19 | 47699,5 | |
3 | 2,71 | 60,21 | 0,9348 | 20,79 | 47018,9 | |
4 | 2,87 | 62,89 | 0,9901 | 19,46 | 46368,8 | |
5 | 3,05 | 68,12 | 1,0510 | 22,47 | 47314,6 | |
Среднее | 3,94 | 65,36 | 1,0126 | 21,17 | 47100,0 |
Плата с толщиной ядра 250 мкм и диаметром отверстий от 100 до 300 мкм была заполнена медью. Эта плата подвергалась оценке термического напряжения в соответствии с IPC TM-650 2.6.8. при плавании на припое 6X в течение 10 секунд при температуре 288 ºC. Целостность покрытия была превосходной, поскольку ни в одном сквозном отверстии не наблюдалось ни трещин, ни расслоения, как показано на рисунке 10.
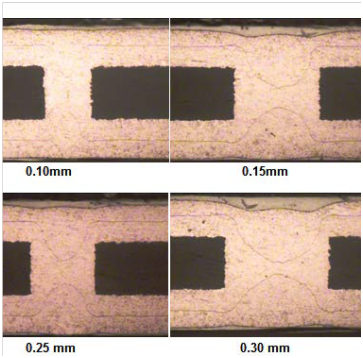
Рис. 10. Поперечный разрез после 6-кратного шока от пайки.
Выводы.
Была разработана технология заполнения медью сквозных отверстий для применения в конструкциях с межсоединениями высокой плотности и подложках ИС.
Процесс состоит из двух циклов кислотного меднения.
Первый цикл – периодическое импульсное обратное гальванопокрытие для формирования перемычки в середине отверстия с последующей гальваническим покрытием постоянным током для заполнения образовавшихся двойных слепых отверстий. Этот процесс может обеспечить бездефектное заполнение сквозного отверстия медью. Механические свойства нанесенного покрытия соответствуют всем стандартам IPC или превосходят их.