- Главная
- Оборудование для печатных плат
- Оборудование для поверхностного монтажа
- Технологии производства плат и поверхностного монтажа
- Инструмент для печатных плат и Запасные части
- Материалы и Химикаты для печатных плат и поверхностного монтажа
- Гальваническое оборудование
- Лабораторное и аналитическое оборудование
- Сервис и техническое обслуживание
- Как нас найти
- Начало раздела
- Главный технолог
- Технологии производства
- Консультации
- Контакты
Еще раз к проблеме DFM
Авторы: Дмитрий Щербаков, заместитель генерального директора ОАО НИЦЭВТ, Илья Лейтес, главный технолог ООО "РТС Инжиниринг"
По мнению авторов, DFM-технология пока не стала профессиональным мировоззрением, т.е. целостным подходом к проектированию и производству изделий РЭА. В статье рассматривается влияние этой концепции на два сегмента производства РЭА — изготовление печатных плат и сборку электронных модулей (ЭМ)
Мы стремимся к тому, чтобы все наши заказчики могли принимать продуманные решения по проектированию, которое сегодня обязательным пунктом должно учитывать и возможности производства.
Ана Хантер, вице-президент по технологиям компании Samsung.
В 2006 г. один из авторов этой статьи опубликовал в журнале «Производство электроники» материал под названием «DFM как мировоззрение». Прошло четыре года — олимпийский период — и мы решили проанализировать, что же изменилось за прошедшее время. К сожалению, концепция DFM («Проектирование — Для — Производства ») так и не стала профессиональным мировоззрением, т.е. целостным подходом к проектированию и производству изделий РЭА. В статье мы затронем цикл производства печатных плат (ПП) и, в меньшей степени, сборки электронных модулей (ЭМ).
Впрочем, изложенные далее соображения могут быть распространены на любое направление разработки и производства РЭА. В первую очередь, должны констатировать: в части отношения к DFM — изменилось не многое. Рассматривая сложившуюся ситуацию, приходишь к выводу: большинство отечественных КБ, по крайней мере, в сегменте специальной РЭА (увы!!!) не мотивированы к разработке аппаратуры по канонам проектирования и производства для серийного выпуска. По-прежнему разработчики подвержены заблуждению, что DFM имеет смысл только в том случае, если речь идет о серийной продукции, к которой, как известно, кроме требований функциональности предъявляются требования низкой трудоемкости, т.е. ведется поиск оптимального решения в координатах: цена/качество/технологичность.
Под другим углом это будет звучать так — DFM-технологии связывают проект, технологические нормы и технологический маршрут производства, что повышает контролируемость и предсказуемость результатов и, как следствие, снижает целый комплекс издержек. Подавляющему большинству руководителей и специалистов разрабатывающих подразделений кажется, что серийно — это когда много. На самом деле, серийная продукция — это продукция, имеющая соответствующим образом подготовленную технологическую КД, позволяющую выпускать качественную и адекватную по цене продукцию — продукцию с воспроизводимым качеством и надежностью.
Конечно, разработка такого рода изделий требует гораздо больше усилий, в том числе на создание полного комплекта необходимой документации — нежели выпуск «макетных мормышек», сопровождающийся поиском не типовых материалов и КИ, а также бесконечными доработками «по контуру». Что же на наш взгляд необходимо, чтобы концепция DFM получила распространение в технологии изготовления электронных модулей, в т.ч. для специального применения? Печатные платы, изготавливаемые для проектов, использующих бюджетные деньги, должны производиться в России.
Такое проявление патерналистской политики является естественным для любого государства. Да и согласитесь — с какой стати за счет российского бюджета финансировать рабочие места в том же Китае. Предвидим возражения со стороны контрактных производителей, среди которых полноценными «контрактниками» являются единицы. В большинстве своем это организации, имеющие логистическое подразделение, обеспечивающее заказ и транспортировку печатных плат из-за границы. Привлекательность таких контрактных производителей заключается в том, что они готовы работать по «не технологичной» документации.
Как правило, в составе таких организаций, есть конструкторские подразделения, которые могут провести «редизайн» — т.е. доработку КД по правилам DFM, причем выполняют это быстро, часто без согласования с заказчиком, особенно если это касается внутренних структур ПП, которые не контролируются визуально на готовой плате. К сожалению, система менеджмента качества на российских предприятиях построена таким образом, что технологическая документация — т.е. та, которая используется в производстве, не может отличаться от конструкторской.
При этом мы готовы выполнить тот же «редизайн», но затем вынуждены перед запуском в производство проводить нудную и кропотливую процедуру корректировки КД и согласования ее по всем инстанциям заказчика. Это конечно «напрягает» разработчиков, заставляет их искать более легкие пути и снижает мотивацию к выпуску полноценного и качественного комплекта документации.
Главное возражение, которое мы слышали в кулуарах профессиональных «тусовок» следующее: «Ну вот, сперва запретим делать печатные платы за рубежом, потом покупать материалы и в итоге опять построим железный занавес », и еще: «Да у нас и делать не кому — все заводы развалились, а кто остался, тот по срокам не конкурент моему партнеру в К…» У нас есть ответ на эти типичные реплики: во-первых, мы не призываем запрещать изготовление за рубежом всех печатных плат, но только тех, которые участвуют в проектах, финансируемых за счет бюджетных средств.
Еще раз повторимся: мы не понимаем, почему российский бюджет должен стимулировать образование и поддержание высокоинтеллектуальных рабочих мест зарубежных стран на фоне требований правительства обеспечить опережающее техническое развитие отечественной промышленности. Во-вторых, вовсе не надо останавливаться, необходимо развивать производство печатных плат в России, развивать производство материалов для печатных плат и электронных модулей, и не обязательно делать это самим, можно развивать лицензионное производство на территории России, как это с делается в Китае и делается успешно. Чтобы не быть голословным: все, изображенное на рисунке 1, может делаться и делается в России.
Производства печатных плат необходимо развивать в России как вширь — увеличивая объемы производства типовых печатных плат, сегментируя производства по видам печатных плат и уменьшая сроки производства, так и вглубь — осваивая новые конструктивы и техпроцессы на базе сверхпрецизионных многослойных печатных плат, такие как послойное наращивание (SBU), разработку и изготовление «систем-в-корпусе» (SiP), микросборок на базе многослойных печатных плат, (МСМ).
Эти направления активно развиваются в Европе и США, и пока никто не торопится переносить их в страны ЮВА. Рассмотрим еще один аспект — проблема технологического запаса. Работа на краю технологического окна приводит к увеличению вероятности появления технологических дефектов. И, что самое неприятное, с увеличением числа явных технологических дефектов увеличивается число скрытых дефектов, которые проявляются в процессе эксплуатации узла. Большинство зарубежных производителей не акцентируют внимание российского заказчика на этом аспекте, так как практически не отвечают за проблемы надежности.
Конструирование печатной платы или электронного модуля с учетом требований производства, чтобы при их изготовлении не возникало необходимости работы на краю технологического окна и есть решение проблемы технологического запаса. DFM-технология позволяет учесть данные проблемы еще на стадии проектирования и, таким образом, обеспечить малотрудоемкое изготовление надежных изделий.
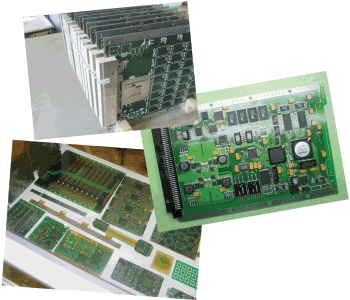
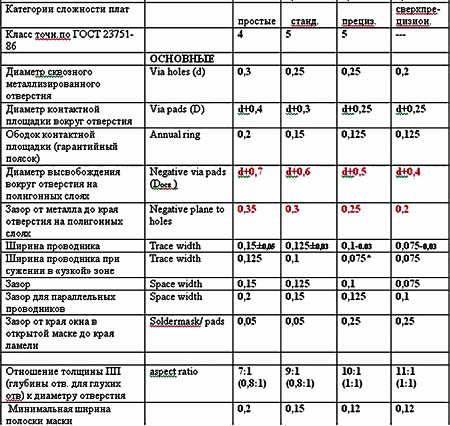
Рис. 1. Многослойные печатные платы и электронные модули, произведенные в цехах ОАО НИЦЭВТ Для примера приведем таблицу технологических параметров, реализуемых на производственном комплексе ОАО НИЦЭВТ в части производства многослойных печатных плат (см. табл. 1). Крайний правый столбец подразумевает работу на краю технологического окна и рекомендуется только при изготовлении прототипов). Так что же происходит с DFM сейчас? Как ни странно, все организации, так или иначе, полностью или частично приходят к осознанию важности этой концепции.
Путем нескольких итераций происходит «приработка» заказчика к стороннему (контрактному) исполнителю. Основные источники проблем, возникающие на этом пути, следующие:
1. При ведении разработки точно не определен производитель.
2. Если производитель определен, разработчик не учитывает возможности производства (причины разные, одна из самых распространенных — элементарно лень знакомиться с технологическими параметрами производства, а также непонимание, зачем вообще это необходимо).
3. Изготовитель не сформировал конструкторско-технологические нормы (КТН) своей производственной базы, или сформировал не полно и/или не четко.
Но представим, что путем последовательных итераций разработчик «нащупал» возможности изготовителя, в свою очередь, изготовитель понял, что от него хотят, т.е. часть DFМ технологии пройдено путем проб и ошибок. Следующая стадия, которая должна стать непреложным правилом, — очередной «образ» возможностей и требований должен быть отработан как «знание» и внедрен в систему проектирования и разработки.
В результате разработчик РЭА будет обладать системой «красных флажков», и, соответственно, соблюдение этого коридора обеспечит контролируемый производственный цикл и предсказуемый результат. В завершении коротко обратим внимание читателей на некоторые аспекты и существующие проблемы, которые позволят разработчикам и производителям печатных плат и электронные модули более эффективно использовать DFM-технологии:
1. Для решения задач DFM необходимо знание всех инфраструктурных составляющих и понимание их взаимовлияния и взаимодействия. Ведь разработка любого проекта сводится к решению 3-х главных задач: функциональность, минимизация стоимости изготовления, надежность в эксплуатации.
2. DFM имеет смысл как комплексная система всех инфраструктурных составляющих. Выпадение, полное или частичное, какой-либо из инфраструктурных составляющих приводит к существенной деструкции всей системы и невыполнению какой либо из упомянутых выше задач (чаще всего последних двух).
3. Одним из главных заблуждений разработчиков, с которыми мы сталкивались в своей практике, является убеждение, что проблемы DFM (технологичности) являются значимыми только на стадии серийного производства. В реальной жизни это приводит к необходимости кардинальной переработки проектов при подготовке серийного или даже мелкосерийного производства и соответствующим увеличениям сроков. На самом деле, проблемы DFM должны в полной мере учитываться и решаться уже на стадии опытных образцов, а еще лучше — прототипов и макетов.
4. Надо признать, что доступные в настоящее время отечественные базовые материалы (ламинат, паяльная маска и т.п.) плохо вписываются в систему DFM. Пути решения этой проблемы — организация лицензионных производств базовых материалов в России (по этому пути давно уже идет Китай и достаточно успешно).
5. Нормативно - техническая база — еще одна из составляющих инфраструктуры, сдерживающая внедрение DFM из-за своей недоразвитости в России. Создавать собственную систему, значит терять много времени. Мы считаем, следует срочно переводить международные стандарты и легитимизировать их, хотя бы как справочные. Тем более что многие предприятия уже вынуждены это делать в «частном» порядке.
6. Значительно сократит сроки изготовления многослойных печатных плат организация государственного склада базовых материалов (включая пока редко используемые СВЧ-ламинаты и ламинаты с высокой температурой стеклования — HighTg). Отечественные производители печатных плат, испытывая постоянный недостаток оборотных средств, не имеют возможности держать широкую номенклатуру складских запасов, доставка «под заказ» занимает 6—8 недель, что сильно снижает их конкурентоспособность.
7. Существенной частью инфраструктуры DFM является освоение передовых перспективных технологических операций, позволяющих разработчикам реализовать новые функциональные характеристики электронных модулей, как правило, в части увеличения плотности, скорости передачи сигнала, и т.п. Имеем в виду такие актуальные на сегодняшний день операции как: – прямое формирование рисунка, лазером и с помощью струйных принтеров; – изготовление печатных плат методом послойного наращивания (SBU — Subsequent Вuilding — Up); – планаризация путем заполнения отверстий гальваническими методами и органическими составами; – встраивание пассивных и активных компонентов внутрь многослойных печатных плат (в рамках «систем-в-корпусе» и микросборок).
8. DFM, будучи комплексным подходом, должна быть еще государственным делом в части: – формирования внятной технической политики, как в промышленности вообще, так и в нашей отрасли в частности; – выбора и финансирования НИОКР по освоению перспективных технологических направлений, обеспечивающих инфраструктуру DFM; – участия в техперевооружении предприятий в рамках единой технической политики.
Ну что же — успехов вам, уважаемые читатели. А успехи наверняка придут с освоением методологии DFM, которая вполне следует народной мудрости — «делать надо с самого начало хорошо, а плохо… а плохо надо уметь контролировать».