- Главная
- Оборудование для печатных плат
- Оборудование для поверхностного монтажа
- Технологии производства плат и поверхностного монтажа
- Инструмент для печатных плат и Запасные части
- Материалы и Химикаты для печатных плат и поверхностного монтажа
- Гальваническое оборудование
- Лабораторное и аналитическое оборудование
- Сервис и техническое обслуживание
- Как нас найти
- Начало раздела
- Оборудование
- Справка
- Контакты
Важность толщины конформного покрытия и покрытие края.
АННОТАЦИЯ.
Поскольку электроника становится все более прецизионной и ожидается, что она будет работать во все более агрессивных средах, использование конформного покрытия становится все более и более важным для защиты узла от эксплуатационной среды и обеспечения приемлемой надежности для предполагаемого применения.
Узлы с конформным покрытием часто подвергаются воздействию суровых условий эксплуатации, включая высокую влажность, высокие температуры, агрессивные газы и изменения рабочей температуры. Важно, чтобы защитное покрытие могло выдерживать ожидаемые условия эксплуатации. В предыдущих статьях испытательные образцы подвергались жесткой последовательной нагрузке, и их способность противостоять коррозии оценивалась с помощью измерения сопротивления поверхностной изоляции (далее по тексту SIR). Во время этого испытания было замечено, что большинство протестированных покрытий не смогли обеспечить хорошую защиту во время испытаний в солевом тумане. Дальнейшие испытания подтвердили важность и сложность достижения хорошего покрытия жидкими конформными материалами.
В этой статье мы сравниваем характеристики новых силиконовых и уретановых материалов, предназначенных для покрытия и их толщины, с популярным акриловым и ультратонким материалом в различных экспериментах, предназначенных для определения того, насколько покрытие является достаточно толстым.
Ключевые слова: конформные покрытия, соленая вода, иммерсия, конденсация, толщина покрытия, укрывистость, силикон, уретан, акрил, ультратонкий, фторполимер.
ВВЕДЕНИЕ.
С ростом внедрения электроники в нашу повседневную жизнь становится все больше требований к условиям эксплуатации и к надежности использования конформного покрытия в качестве средства повышения надежности электроники. Во многих изделиях с высокой надежностью, например, изделия автомобильной промышленности, очистка перед нанесением покрытия обычно не выполняется. Система покрытия и остатки материалов технологии сборки должны выдерживать предполагаемые условия эксплуатации. Остатки процесса сборки и переносимые по воздуху загрязняющие вещества в рабочей среде могут привести к росту металлических дендритов, что приводит к токам утечки, которые могут ухудшить характеристики электросхемы или привести к преждевременному выходу из строя.
IPC-CC-830B описывает требования к характеристикам и методологию испытаний материалов конформного покрытия. Тестирование проводится на плоских, безупречно чистых тестовых образцах, изготовленных из различных подложек (FR4 и стеклянных). Однако в CC-830 не учитываются технологические остатки, резист припоя или геометрия компонентов. Хотя это понятно из спецификации характеристик материала, это означает, что стандарт изо всех сил пытается дифференцировать характеристики материалов. Адгезия к припою, совместимость с остатками техпроцесса или безотмывным остаткам, покрытие проводящих поверхностей, таких как выводы компонентов, влияние покрытия на срок службы паяного соединения или влияние паяного соединения и выводов на тепловой удар не являются частью квалификационного документа, но являются ключевыми критериями эффективности конформных покрытий в реальных приложениях, отсюда и название этой серии документов.
IPC-J-STD-001 описывает допустимый диапазон толщины покрытия в зависимости от общего типа химического состава, но относится только к плоским, участкам платы (без компонентов).
Конформные покрытия могут эффективно предотвращать попадание загрязнения из окружающей среды на собранную плату. Однако они не обязательно водонепроницаемы по своей природе, а дефекты или разрывы в пленке могут привести к попаданию потенциально агрессивных веществ на восприимчивые части.
В готовящемся техническом документе «Материал конформного покрытия IPC-TR-587» и отчете «Состояние отрасли»», подготовленном Дейвом Хиллманом1, для покрытия узлов использовались различные наносимые конформные материалы и процессы нанесения. Затем эти сборки разрезали и измеряли толщину. Одной из выдающихся особенностей было то, насколько сложно было успешно покрыть выводы компонентов и острые края или вертикальные поверхности, как показано, например, на рис. 1. Существуют сотни поперечных сечений, демонстрирующих те же проблемы.
В то время, как в техническом документе освещаются некоторые проблемы, возникающие при оптимизации нанесения конформных покрытий, на самом деле не дается никаких указаний относительно приемлемой толщины (что не входило в намерения). Цель этой статьи — помочь понять, какая толщина должна быть достаточной, чтобы обеспечить защиту, используя как деионизированную воду, так и солевой раствор для имитации реальных загрязняющих веществ.
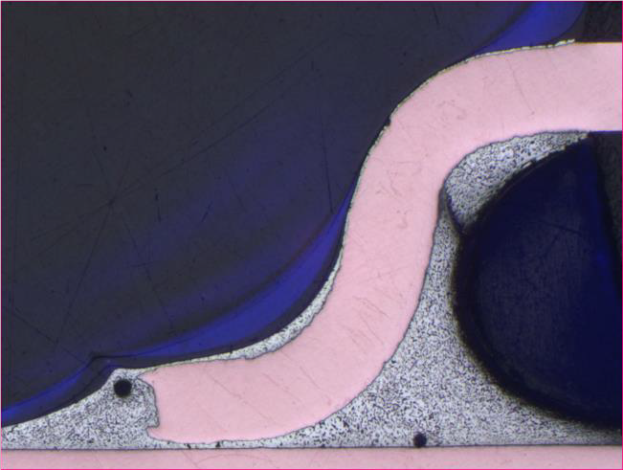
Экспериментальная часть №1
Для простоты была создана простая тестовая установка для измерения SIR различных материалов покрытий в условиях, близких к погружению.
На испытательный образец IPC B-24 были нанесены конформные покрытия с различной толщиной мокрой пленки для достижения требуемой толщины сухой пленки. В случае UT (ультратонкого) покрытия для достижения требуемой толщины было необходимо нанесение нескольких слоев покрытия.
В таблице 1 показаны материалы покрытия и толщина сухой пленки, которые были испытаны на SIR в условиях водонасыщения:
Таблица 1. Типы и толщина покрытия.
Покрытие | T1 (мкм) | T2 (мкм) | T3 (мкм) | T4 (мкм) |
---|---|---|---|---|
UT ультратонкий | 3 | 5 | 25 | 100 |
AR акрил | 5 | 15 | 25 | 150 |
SR силикон | 50 | 100 | 150 | 250 |
UR уретан | 50 | 100 | 150 | 250 |
Толщину сухого пленочного покрытия проверяли механическими средствами с использованием микрометра для вычитания толщины испытательных плат из толщины плат с покрытием в заранее определенных местах.
Испытание на сопротивления поверхностной изоляции (SIR).
Все измерения SIR были выполнены с помощью калиброванного автоматического электрометра Auto-SIRTM-256 с использованием калиброванной испытательной стойки для облегчения сбора данных, как показано ниже на рисунке 2.
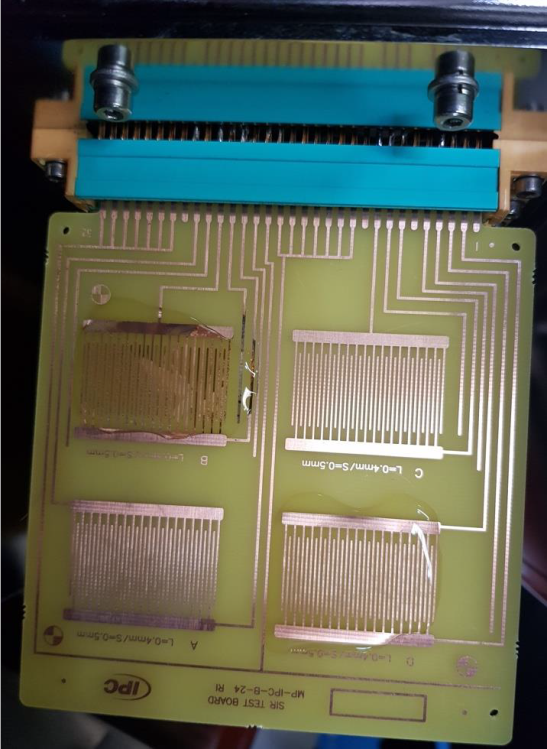
Материалы.
3,5% солевой раствор готовили путем растворения 35 г NaCl в 900 мл деионизованной воды с последующим добавлением до 1 л деионизованной воды в мерную колбу.
Конформные покрытия были нанесены на испытательные платы IPC-B24 и отверждены в соответствии с их техническими данными. Испытательные платы с покрытием оставляли на 7 дней при температуре 25°C и относительной влажности 50% для достижения оптимальных свойств перед испытанием.
Тестовые платы IPC-B-24 были очищены изопропиловым спиртом перед нанесением материалов покрытия или перед тестированием без покрытия в качестве контроля, за исключением безотмывной паяльной пасты, которую тестировали неочищенной и без покрытия в качестве другого контроля.
5 мл 3,5% солевого раствора наносили на каждую гребенку непосредственно перед началом каждого теста SIR.
Условия испытаний SIR.
Все тесты SIR проводились при 25°C и относительной влажности 50% (окружающие лабораторные условия). 10В подавались непрерывно, измерения SIR регистрировались каждую минуту. Продолжительность теста SIR составила 500 минут.
Результаты (часть 1).
Результаты, полученные для различных материалов покрытия при насыщении жидкой деионизованной водой, показаны в таблице 2. Ток утечки рассчитывается по закону Ома из сопротивления и напряжения. Значения SIR, полученные для плат без покрытия, безотмывной паяльной пасты, с покрытием UT и AR были очень похожи при нормальной толщине. UT (ультратонкое) покрытие показало значительное улучшение SIR при толщине покрытия 100 мкм. Дополнительная толщина, по-видимому, не улучшает SIR акрилового (AR ) покрытия, значения остаются низкими даже при толщине 150 мкм. Однако видимых признаков коррозии, искрения или любые другие признаки чрезмерной утечки тока не было.
Таблица 2. Значения SIR покрытий, пропитанных ДИ водой.
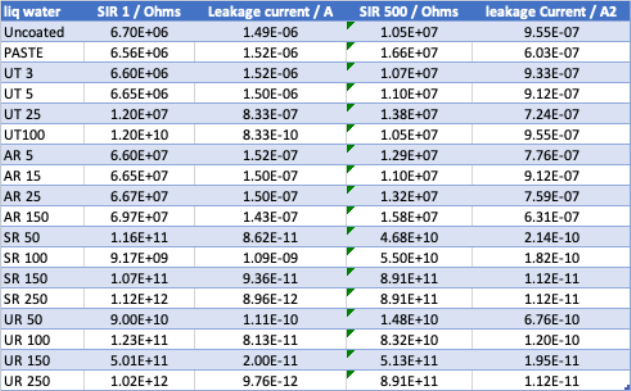
Когда мы рассматриваем результаты для 3,5% солевого раствора, как показано в Таблице 3. Сопротивление изоляции упало еще больше, а ток утечки увеличивается во всех случаях, кроме очень толстых покрытий, и материалов SR и UR. Небольшая коррозия была видна на безотмывной паяльной пасте, а также материалах UT и AR, хотя и не в той степени, которую можно было бы ожидать при SIR измерениях.
Таблица 3. Результаты SIR покрытий, насыщенных ДИ водой.
ДИ водой | SIR 1 / Ом | Ток утечки / A | SIR 500 / Ом | Ток утечки / A2 |
---|---|---|---|---|
Без покрытия | 6.60E+06 | 1.52E-06 | 5.01E+04 | 2.00E-04 |
ПАСТА | 6.53E+06 | 1.53E-06 | 1.26E+04 | 7.94E-04 |
UT 3 | 6.50E+06 | 1.54E-06 | 5.01E+04 | 2.00E-04 |
UT 5 | 6.57E+06 | 1.52E-06 | 4.79E+04 | 2.09E-04 |
UT 25 | 1.28E+08 | 7.81E-08 | 6.17E+05 | 1.62E-05 |
UT 100 | 1.18E+10 | 8.47E-10 | 1.62E+10 | 6.17E-10 |
АR 5 | 6.58E+07 | 1.52E-07 | 5.25E+04 | 1.91E-04 |
АR 15 | 6.53E+07 | 1.53E-07 | 5.37E+04 | 1.86E-04 |
АR 25 | 6.73E+07 | 1.49E-07 | 6.17E+04 | 1.62E-04 |
АR 150 | 6.81E+07 | 1.47E-07 | 3.16E+06 | 3.16E-06 |
SR 50 | 1,20Е+10 | 8,33Е-10 | 4,79Е+10 | 2,09Е-10 |
SR 100 | 1,01Е+11 | 9,87Е-11 | 6,92Е+10 | 1,45Е-10 |
SR 150 | 1,07Е+11 | 9,36Е-11 | 1,66Е+11 | 6,03Е-11 |
SR 250 | 1.10Е+12 | 9.07Е-12 | 2.14Е+11 | 4.68Е-11 |
UR 50 | 8,62Е+10 | 1,16Е-10 | 9,77Е+10 | 1,02Е-10 |
UR 100 | 9,55Е+10 | 1,05Е-10 | 1,41Е+11 | 7,08Е-11 |
UR 150 | 6.31Е+11 | 1.58Е-11 | 4.57Е+11 | 2.19Е-11 |
UR 250 | 1.14Е+12 | 8.77Е-12 | 5.25Е+11 | 1.91Е-11 |
Однако Auto-SIRTM содержит резистор 1 МОм чтобы ограничить ток и сохранить признаки дендритного роста.
Экспериментальная часть №2
Было решено напрямую измерить ток утечки с помощью цифрового мультиметра Keysight 34465A. В этом опыте пипеткой наносили 1 каплю физиологического раствора на тестовый купон, затем была запущена регистрация данных, а затем подавалось напряжение. Измерения были зарегистрированы автоматически с интервалом в 1 с, а пример отображается в Рис. 3 ниже.
Результаты (часть 2).
Можно было видеть обширную коррозию, формирующуюся почти сразу как на непокрытой пасте, так и на 5 микроном UT покрытии, как показано на рис. 4-5 ниже. В пределах 100 секунд плата с UT покрытием показала такую же утечку тока на безотмывной в виде пасте без очистки.
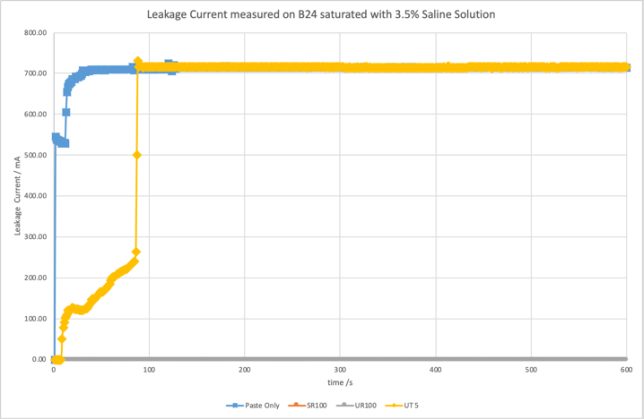
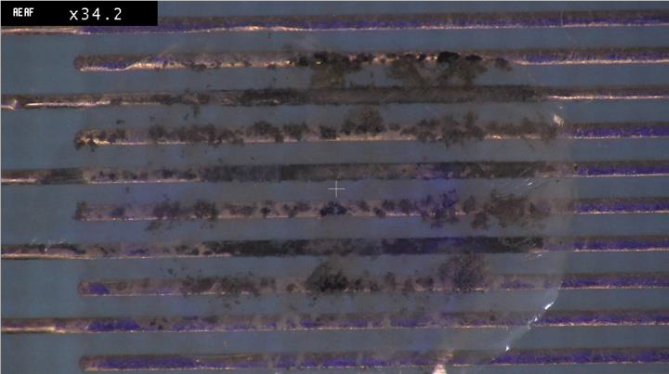
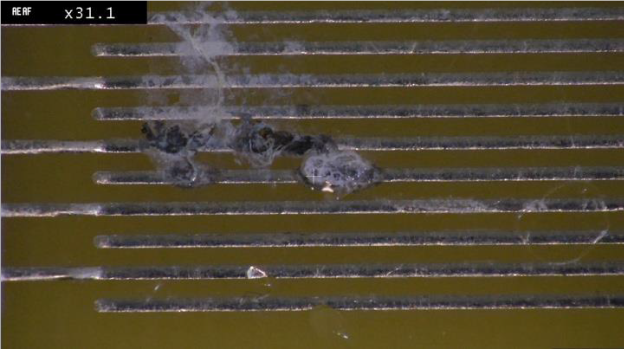
Минимальная толщина проверена для фиксации отсутствия коррозии Насыщение 1800 с 3,5% физиологическим раствором показано в таблице 4.
Таблица 4. Минимальная толщина, проверенная на отсутствие коррозии при солевой насыщенности.
Покрытие | Толщина | Максимальный ток утечки (мА) | Коррозия |
---|---|---|---|
UR | 50 | 0,001 | НЕТ |
SR | 50 | 0,001 | НЕТ |
АR | 150 | 39 | НЕТ |
UT | 25 | 119 | НЕТ |
Без покрытия | Нет данных | 723 | ДА |
Безотм. паста | Нет данных | 732 | ДА |
Акриловые материалы и материалы UT испытаны при более высокой температуре, чем обычно. Использованная толщина, дает значительно более высокую утечку тока, чем проверенный уретановый или силиконовый материал.
Экспериментальная часть №3
Плоские тестовые платы могут дать интересную информацию, но клиенты производят 3D сборки. Поэтому, предыдущий эксперимент был воспроизведен с использованием QFN. Модифицированная, полностью заполненная тестовая сборка, собрана с безотмывной пастой. На основе предыдущего результата, уретановые и силиконовые материалы были нанесены при целевой толщине 200 микрон. Акриловый материал был нанесен двойным погружением, чтобы получить номинальную толщину 74 мкм. Материал UT был покрыт погружением 5 раз, чтобы получить номинальную толщину 13 мкм. Платы были погружены в физраствор (следя за тем, чтобы разъем не был в солевом растворе) и все компоненты питались от 10 В. Платы тестировались до тех пор, пока ток утечки не превысил 200 мА между выводами QFP и было зафиксировано время. Затем платы визуально осматривались на наличие признаков коррозии.
Результаты (часть 3).
Результаты погружения IPC-B52 в физиологический раствор обобщены в Таблице 5 ниже.
Таблица 5. Сводка результатов иммерсионных испытаний B-52.
Покрытие | Толщина / мкм | Время до достижения 200 мА | Коррозия |
---|---|---|---|
UR | 200 | >30 часов | Нет |
SR | 200 | >30 часов | Нет |
AR | 74 | 19 секунд | Да |
UT | 13 | 9 секунд | Да |
Ультратонкое покрытие было самым быстрым для достижения текущего порога утечки (всего за 9 секунд). Коррозия была видна на всех компонентах, но особенно преобладала на компонентах QFN из-за открытой металлизации выводов (большинство контактных площадок были закрыты паяльной маской), как показано на рис. 6-8.
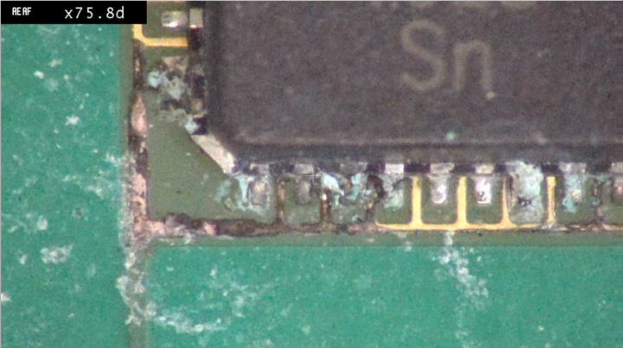
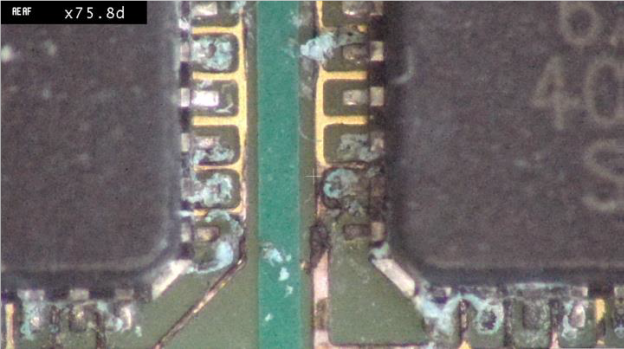
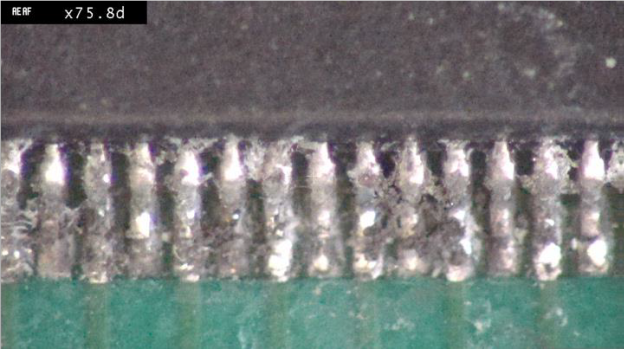
Акриловый материал достиг порогового тока утечки всего за 19 с. Видимая коррозия была не такой обширной, как на UT покрытии, но была совершенно ясно видимой, как показано на рис. 9-11.
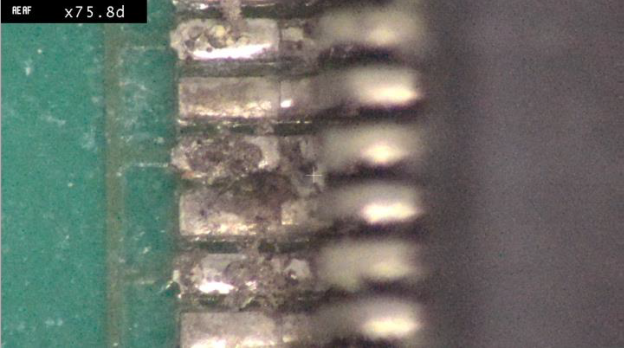
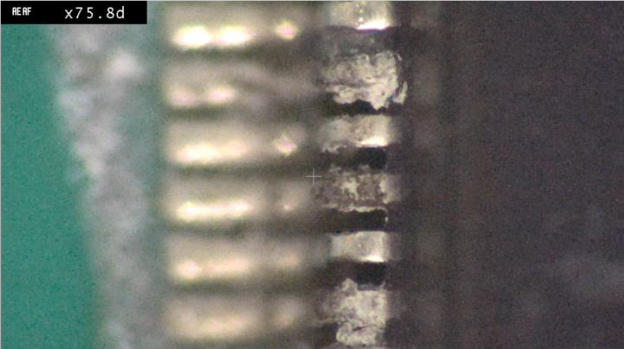
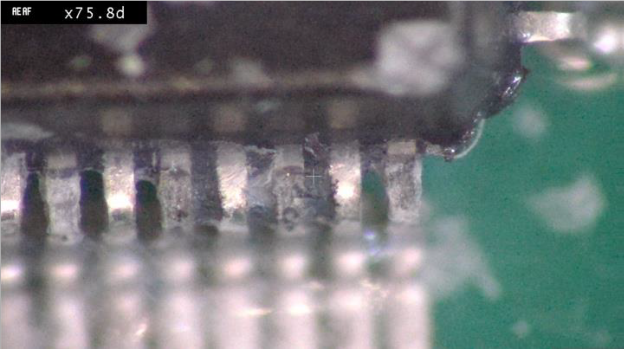
Силиконовый и уретановый материалы выдержали 30-часовое погружение в физиологический раствор без достижения порогового значения тока утечки. Во время визуального осмотра (рис. 12-17) было очень мало различий во внешнем виде плат после завершения тестирования.
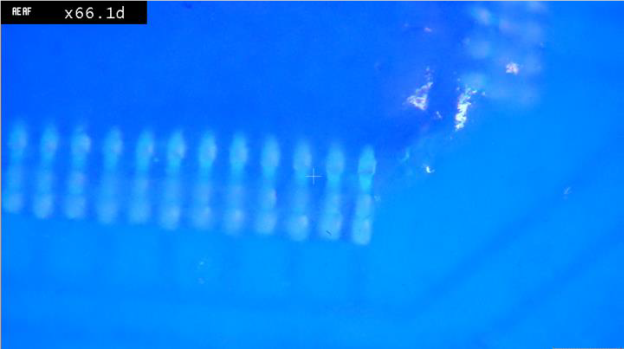
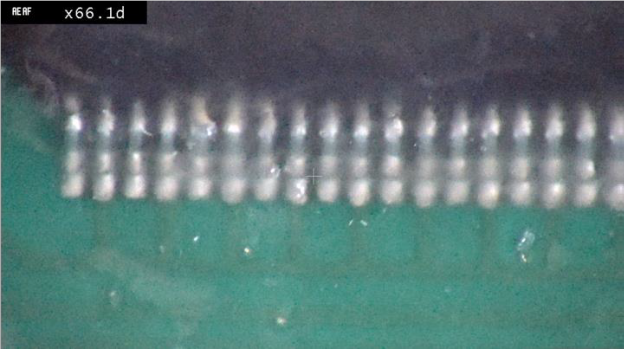
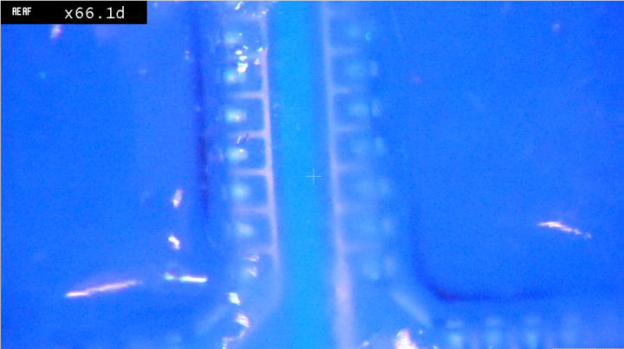
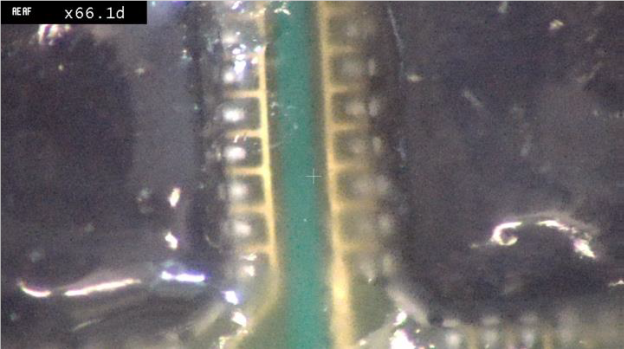
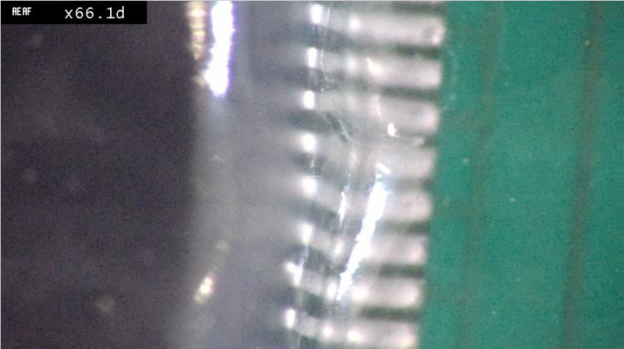
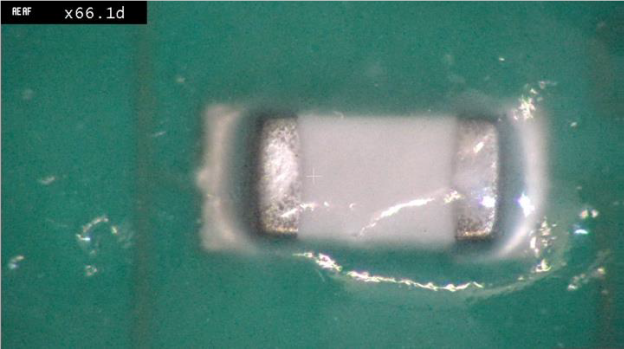
Выводы.
Из этих относительно простых экспериментов становится ясно, что толщина покрытия имеет жизненно важное значение для определения того, выдержит ли сборка жизнь в полевых условиях, независимо от того, вызван ли риск выхода из строя влажностью, конденсацией, брызгами соли, дуговым разрядом или образованием оловянных усов.
Иммерсионные испытания традиционно были чрезвычайно сложным испытанием для обычных конформных покрытий. Новые силиконовые и уретановые покрытия были разработаны для решения проблем с укрывистостью и толщиной распространенных покрытий.
Из результатов первого эксперимента видно, что акриловый материал существенно не улучшил значение SIR даже при 150 мкм. Ультратонкий материал толщиной < 12,5 микрон требовал 25 микрон, чтобы было какое-либо улучшение по сравнению с отсутствием покрытия, и даже 100 микрон не соответствовало изоляционным возможностям силиконовых или уретановых материалов.
Во втором эксперименте, исключив токоограничивающий резистор и измерив фактический ток утечки, мы снова смогли увидеть, что обычные и ультратонкие материалы дают значительно большие токи утечки, чем силиконовые и уретановые материалы. Распространив эту методологию на сборку B-52 и взглянув на топографию и компоненты в отличие от плоских гребенок для испытаний на SIR, мы еще раз увидели, что силиконовые и уретановые материалы обеспечивают значительное улучшение времени сохранения надежности при погружении с включенным питанием в 3,5% солевой раствор. Силиконовый и уретановый материал выдержал эти условия в течение 30 часов без признаков коррозии или чрезмерного тока утечки, в то время как акриловый и ультратонкий материал выдержал менее 20 секунд, несмотря на нанесение нескольких слоев.
Плата с уретановым покрытием была разрезана, чтобы исследовать толщину нанесенного материала, а также измерялся ток утечки, на рис. 18-20. Там видно, насколько хорошо компонент был покрыт, и результат не удивителен, учитывая типичное покрытие, показанное на рис. 1.
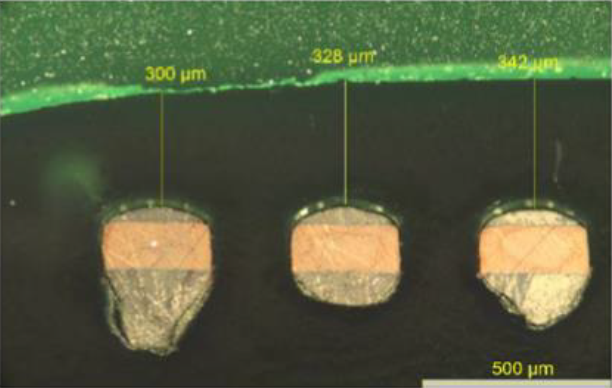
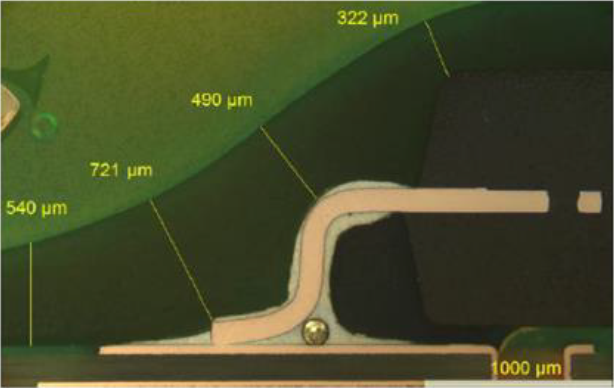
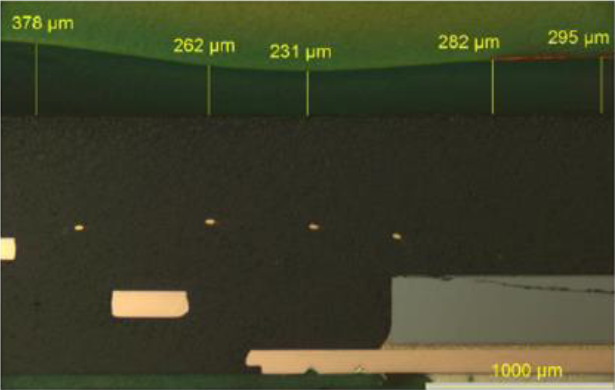
Компания РТС Инжиниринг предлагает широкий ассортимент оборудования для нанесения влагозащитных покрытий. В нашем каталоге представлены:
- Системы селективного нанесения влагозащитных покрытий;
- УФ системы отверждения;
- ИК системы отверждения;
- Вертикальные конвекционные печи.
ИСПОЛЬЗОВАННАЯ ЛИТЕРАТУРА.
IPC-TR-587 Материал конформного покрытия и отчет об оценке «Состояние отрасли».