- Главная
- Оборудование для печатных плат
- Оборудование для поверхностного монтажа
- Технологии производства плат и поверхностного монтажа
- Инструмент для печатных плат и Запасные части
- Материалы и Химикаты для печатных плат и поверхностного монтажа
- Гальваническое оборудование
- Лабораторное и аналитическое оборудование
- Сервис и техническое обслуживание
- Как нас найти
- Начало раздела
- Оборудование
- Справка
- Контакты
Сборка электроники в светодиодной промышленности
Начиная с 2007 г., еще до принятия закона об энергосбережении, в России начался резкий рост числа компаний занимающихся постав кой и производством энергосберегающих светильников. Наиболее перспективными из них оказались светодиодные, которые имеют самое низкое энергопотребление.
В статье рассказывается, как должна выглядеть линия поверхностного монтажа для их изготовления, и с какими особенностями при сборке сталкиваются или могут столкнуться производители светотехнических изделий. Данная информация будет наиболее интересна компаниям, которые уже имеют у себя или хотели бы иметь цех поверхностного монтажа, где осуществляется сборка печатных плат для светотехнических изделий.
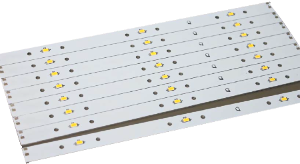
Начнем с простого: что же из плат надо собирать для производства такого конечного продукта, как светодиодный светильник. И здесь, на самом деле, не такая большая номенклатура собираемых изделий. Производство большинства светильников требует сборки только двух типов плат: плата блока питания и сам светодиодный кластер.
Что касается блока питания, то, в основном, в нем присутствуют компоненты, устанавливаемые в отверстия (конденсаторы, трансформаторы, варисторы и т. д.), а также небольшое количество поверхностно монтируемых элементов, без каких-либо сложных микросхем с малым шагом выводов и мелких компонентов.
В самом светодиодном кластере присутствуют только поверхностно монтируемые компоненты, которыми являются светодиоды, резисторы, линзы и т. д.
То есть, количество типов компонентов в светодиодном модуле составляет от двух до десяти, в зависимости от типа модуля и его сложности. Исходя из вышесказанного, на производстве необходимо наладить сборку как минимум двух типов плат для каждого вида светильника.
Номенклатура светильников относительно большая, примерно по пять моделей в каждом сегменте освещения. Компании–производители светодиодной продукции редко работают в одном или двух сегментах и стараются покрыть все области функционального освещения. Таким образом, общая номенклатура собираемых на предприятии плат составляет примерно 40–50 типов изделий.
Опишем решения по организации сборочно монтажного участка на примере крупных российских компаний–производителей и отметим определенные особенности данного производства. В зависимости от масштабов компании, обычно на производстве стоят один или два установщика компонентов с производительностью 15 000–20 000 комп./ч.
Обязательно присутствует принтер трафаретной печати, как правило, автоматический. Печь оплавления — конвейерная, конвекционная, так как камерные печи не подойдут из-за низкой производительности, а более дешевые варианты с ИК-нагревом не обеспечат необходимую равномерность распределения температуры.
Нанесение паяльной пасты
![]() |
Рис. 1. Люминесцентная лампа Т8 |
Сборка начинается с этапа нанесения паяльной пасты на плату. Так как в светотехническом производстве размеры заготовок достигают 600 мм в длину,а иногда и больше, максимальная область нанесения пасты является первой особенностью. Это все связано со светодиодными аналогами популярных в России люминесцентных ламп Т8 (рис. 1). Поэтому для принтеров, работающих в данном сегменте, необходим большой размер области печати. Для данной операции отлично подойдет оборудование всемирно известной японской фирмы Panasonic.
Принтер модели SPG (рис. 2) способен наносить пасту на платы длиной до 650 мм, имеет в базовой конфигурации автоматическую систему очистки трафарета и систему контроля качества нанесения паяльной пасты (SPI), что существенно повышает качество печати и, как итог, качество конечного продукта. Помимо этого Panasonic реализовала в принтере систему поддержа ния постоянного давления печати, которая учитывает даже незначительный прогиб больших плат, а также систему вакуумного прижима плат, что немаловажно при работе с платами больших размеров.
![]() |
Рис. 2. Автоматический принтер трафаретной печати SPG, рабочая область принтера SPG с системой очистки трафарета и система автоматической подачи паяльной пасты SPG |
![]() |
Рис. 3. Полуавтоматический принтер трафаретной печати SP1200 |
Если же рассматривать производство, которое имеет меньший объем, то можно сэкономить на автоматизации. Так, например, вместо автоматического принтера можно использовать полуавтоматический, такой как SP 1200 ф. EMS Technologies (рис. 3).
Данный принтер может осуществлять нанесение пасты на платы длиной до 1200 мм.
Монтаж поверхностно монтируемых компонентов
Установщик модели AM100 (рис. 4) обладает рядом особен ностей, которые позволяют обеспечить высокое качество установки компонентов, а также оптимизировать процесс сборки плат для светильников.
Компания Panasonic вложила в модель AM100 весь опыт, наработанный за многие годы в высокопроизводительных системах. Машина способна работать с платами длиной до 1600 мм, устанавливать поддерживающие штифты автоматически по заданной программе или вручную, с помощью специальной оснастки, скорость установки достигает 35 800 комп/ч.
Помимо SMD-компонентов, машина может осуществлять установку компонентов в отверстия специальным захватом, который имеет несколько конфигураций. Также конструкция установочной головки позволяет осуществлять монтаж с заданным усилием.
Данная особенность актуальна для монтажа штыревых компонентов, а также компонентов с защелками. Panasonic предлагает решения непосредственно для светодиодной индустрии, такие как, например, специальныйкомплект захватов под светодиоды всех типов и программное обеспечение, позволяющее контролировать установку на одну плату компонентов–светодиодов только из одной партии.
![]() |
Рис. 4. Установщик AM100, внутренняя область установщика AM100
и насадки для светодиодов в AM100 |
Оплавление
Если на производстве используется больше чем один уста новщик, то все они располагаются в одну линию (рис. 5). Только немногие компании–производители светотехники могут себе позволить обслуживать сразу две сборочные линии одновременно. Поэтому, как правило, сборка осуществляется поочередно — то блоки питания, то кластеры. Либо, как вариант, работает линия со сдвоенным конвейером, но это очень редкий случай. Печки используются конвекционные конвейерные, начиная от шести зон и более.
![]() |
Рис. 5. Конвейерная конвекционная печь Folungwin |
Количество зон в данной индустрии обусловлено, скорее, требуемой производительностью линии, так как большее количество зон позволяет увеличить скорость конвейера, сохраняя при этом необходимый профиль пайки.
Монтаж и пайка выводных компонентов
Переходим к следующему этапу сборки электроники. У нас уже есть плата с запаянными SMD-компонентами. Осталось только установить компоненты, которые монтируются в отверстия. Это касается только плат блоков питания. Установка компонентов осуществляется вручную операторами с использованием автоматических конвейеров. Конечно, этот процесс можно автоматизировать. Существуют специальные универсальные установщики компонентов, например, NPM-VF фирмы Panasonic (рис. 6), способные устанавливать штыревые компоненты, как аксиальные, так и радиальные.
![]() |
![]() |
Рис. 6. Установщик выводных компонентов NPM-VF |
Рис. 7. Установка пайки волной припоя Folungwin |
Однако автоматизация данного этапа подразумевает использование компонентов, поставляе мых в ленте или пеналах и изначальную разработку платы, оптимизированную под автоматизированный монтаж. После набивки платы выводными компонентами осуществляется их пайка. Пайка осуществляется либо вручную монтажни ками, либо с помощью установки пайки волной припоя (рис. 7). После чего собранные платы отправляются на этап нанесения влагозащиты или сразу на корпусирование.
Контроль качества
Выше были описаны ключевые этапы сборки плат при производстве светодиодной продукции. Но следует отметить и дополнительные этапы, которые существенно повышают качество продукции. Оптический контроль является важным этапом при сборке электроники. При сборке плат, как известно, может возникнуть множество дефектов, таких как смещение или отсутствие компонента, короткое замыкание, недостаточное количество припоя и т. д.
Видов дефектов множество, и осуществлять инспекцию их всех единовременно человеку не под силу. Зато с этой задачей прекрасно справляются системы автоматической оптической инспекции. Например, установки японской компании Omron, которые осуществляют инспекцию по запатентованной технологии трехуровневой уровневой цветной подсветки (рис. 8).
![]() |
Рис. 8. Система оптической инспекции Omron S500. Принцип работы
системы трехцветной подсветки и пример изображения компонента
снятого установкой |
Благодаря данной технологии, установка может определять как все вышеупомянутые дефекты, так и контролировать качество паяного соединения, определяя смачиваемость вывода/ площадки и количество припоя, чего не могут осуществить аналоги, использующие монохромную подсветку. Для осуществления электроконтроля используются специальные системы внутрисхемного контроля.
![]() |
Рис. 9. Система адаптерного электроконтроля Digitaltest |
Ввиду низкой производительности систем с летающими пробниками, производителям LED-продукции невыгодно их использование. На данном этапе система адаптерного контроля будет лучшим решением. Так как при светотехническом производстве, в основном, собираются одни и те же изделия, целесообразно приобрести одну установку тестирования и несколько адаптеров к ней. Системы адаптерного контроля немецкой фирмы DigitalTest позволяют осуществлять контроль как на отдельно стоящей установке, так и на встраиваемой в линию системе.
Вспомогательное оборудование
При производстве светильников, в которых линзы монтируются поверх светодиодов, дополнительно потребуется оборудование, которое позволяет наносить клей на посадочные места линз перед их установкой и затем полимеризовать его. Для нанесения клея может использоваться как отдельно стоящая система, так и устанавливаемый в SMD установщик–дозатор.
Для полимеризации используются специальные конвейерные УФ-печи. Мы нигде не упомянули этап отмывки собранных изделий. Это связано с тем, что в данном вопросе производители светотехники разделились на два фронта. Одна часть всегда отмывает собранные платы, а другая никогда этого не делала и не собирается. Кто же прав? По нашему мнению, здесь имеют место быть оба варианта.
Если не углубляться в технологию, то первый случай — это стандартный подход к производству электроники, где плату необходимо очистить от остатков флюса, чтобы исключить возможные КЗ и отслоения влагозащитного покрытия. Но когда производитель использует безотмывочную паяльную пасту, которую отмывать не то что не нужно, а вообще нежелательно, то и здесь он поступает верно. Что касается надежности собранных изделий — то в данной индустрии принципиальной разницы в ней не наблюдается. Так что право выбора мы оставляем за производителем с его отработанной технологией.
Ориентируясь на вышеописанный комплект оборудования, производитель сможет получить высококачественное надежное светодиодное изделие, способное проработать не один десяток лет. Также не стоит забывать, что, помимо описанного оборудования, производственный цех может быть доукомплектован шкафами сухого хранения, антистатической мебелью, инструментом и другой мелочью, которая облегчит жизнь монтажнику и, как следствие, повысит качество выпускаемой продукции.