- Главная
- Оборудование для печатных плат
- Оборудование для поверхностного монтажа
- Технологии производства плат и поверхностного монтажа
- Инструмент для печатных плат и Запасные части
- Материалы и Химикаты для печатных плат и поверхностного монтажа
- Гальваническое оборудование
- Лабораторное и аналитическое оборудование
- Сервис и техническое обслуживание
- Как нас найти
- Начало раздела
- Оборудование
- Поддержка
- Справка
- Контакты
Изготовление многослойных печатных плат с проводниками 75 мкм и с микропереходами 200 мкм
В статье описана разработка технологии изготовления высокопрецизионных многослойных печатных плат с параметрами проводник/ зазор — 75 мкм/75 мкм, диаметром глухих отверстий — 0,2 мм, диаметром сквозных отверстий — 0,25 мм, и опробование технологии изготовления МПП с параметрами проводник/зазор — 50 мкм/50 мкм.
СТРУКТУРА И ПАРАМЕТРЫ МНОГОСЛОЙНЫХ ПЕЧАТНЫХ ПЛАТ
Многослойная печатная плата состоит из прецизионного полупакета (слои 1—4) с размещением BGA на слое 1 (проводник/зазор — 75 мкм/75мкм), к которому припрессовываются стандартные по прецизионности слои земля/питание (сл. 5, 6, 7) с параметрами проводник/зазор — 150мкм/150 мкм. К слою «1» припрессовывается слой «0», который повторяет рисунок КП для установки компонентов поверхностного монтажа, в том числе BGA, за исключением логических цепей. «Нулевой» слой является вспомогательным, копирует слой 1 по рисунку ламелей под монтаж компонентов и предназначен для того, чтобы согласовать требования тентинг-процесса формирования наружных слоев и обеспечить полный электроконтроль прецизионного полупакета слоев 1—4. «Нулевой» слой связан со слоем 1 при помощи глухих металлизированных микроотверстий диаметром 0,2 мм. Такие же глухие микропереходы имеются со слоя 8 на слой 7. Глухие отверстия сверлятся непосредственно в КП (ламелях) под поверхностный монтаж.
ТЕХПРОЦЕСС ИЗГОТОВЛЕНИЯ МНОГОСЛОЙНЫХ ПЕЧАТНЫХ ПЛАТ
Прецизионный полупакет (слои 1—4) изготавливается отдельно. Проходит визуальный контроль и электроконтроль качества рисунка и металлизированных переходных отверстий.
Слои 5, 6, 7 изготавливаются субтрактивным методом из тонкого фольгированного диэлектрика FR-4 c фольгой толщиной 18 мкм. Для прессования всего пакета используется препрег 1080. Для наружных слоев припрессовывалась 18 мкм фольга на САСе (с алюминиевым протектором).
Многослойная печатная плата (см. рис. 1, 2, 3 ) изготавливалась тентинг-методом по следующему маршрутному техпроцессу:
- прессование пакета;
- сверление сквозных и глухих отверстий ;
- подготовка под металлизацию, плазмохимическое подтравливание отверстий;
- химическое и предварительное гальваническое меднение;
- окончательное гальваническое меднение;
- фотопечать (негативная) наружных слоев
- травление (кислое);
- визуальный контроль;
- электроконтроль;
- нанесение паяльной маски;
- горячее лужение (HAL);
- окончательный визуальный и электроконтроль;
- фрезерование
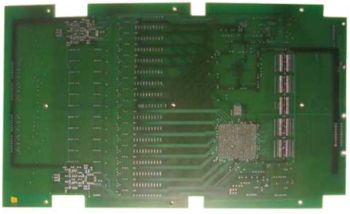
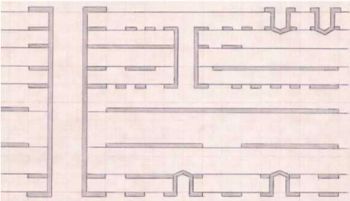
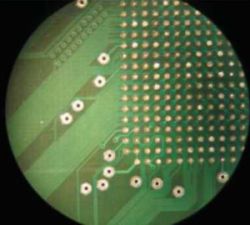
ТЕХПРОЦЕСС ИЗГОТОВЛЕНИЯ ПРЕЦИЗИОННОГО ПОЛУПАКЕТА (СЛ. 1—4)
Техпроцесс изготовления прецизионного полупакета представляет собой изготовление 4-слойной МПП с прецизионными наружными слоями (слои 1, 4), как изображено на рисунках 4 и 5. Слои 2—3 изготавливаются субтрактивным методом из тонкого фольгированного FR-4 c фольгой толщиной 18 мкм. Готовые слои после оптического автоматизированного контроля замеряют на размерную стабильность (усадка не более 50 мкм).
![]() |
![]() |
Рис. 4. Прецизионный полупакет (слои 1—4) |
Рис. 5. Фрагмент полупакета (слои 1—4) |
Для прессования прецизионного полупакета (слои 1—4) использовался препрег 1080 фирм «Mazusita» и «Isola» (70 мкм), а также опробовался отечественный СТП-4 (40 мкм). Для получения сл. 1 и 4 препрессовывалась фольга толщиной 9 мкм на САСе (с алюминиевым протектором).
Маршрутный техпроцесс изготовления прецизионного полупакета состоит из следующих операций:
- фотопечать (негативная) и травление слоя 2-3 (FR-4 -2-18-0,2);
- оптический автоматизированный контроль качества рисунка (слои 2—3);
- визуальный контроль и контроль размерной стабильности слоя 2—3 ( усадка не более 50 мкм) на установке «Визекс»;
- прессование полупакета (слои 1—4) с использованием САСа с фольгой толщиной 9 мкм для слоев 1 и 4;
- вскрытие тест-купонов (локальным травлением, 6 шт. по периметру заготовки);
- контроль размерной стабильности внутренних слоев (слои 2—3) относительно базовых отверстий по тест-купонам (усадка не более 80 мкм);
- сверление сквозных переходных отверстий диаметром 0,25 мм с учетом поправок по тест-купонам слоев 2—3;
- плазмохимическое подтравливание отверстий;
- химическое и предварительное гальваническое меднение заготовок;
- полное гальваническое меднение заготовок (общая толщина металлизации 25...30 мкм);
- фотопечать (негативная) прецизионного рисунка слоев 1 и 4;
- прецизионное травление (кислое) сл. 1 и 4 на установке Resko на толщину 35.40 мкм;
- оптический автоматизированный контроль качества прецизионного рисунка (проводник/зазор — 75 мкм/75мкм) на установке АОИ «Accu-Mach»;
- отмывка заготовок;
- электроконтроль проводящего рисунка и переходных металлизированных отверстий.
Далее прецизионный полупакет (слои 1—4) передается на прессование полного 8-слойного пакета (слои 0—8).
ТЕХНОЛОГИЧЕСКИЕ ОСОБЕННОСТИ И ПРОБЛЕМЫ ИЗГОТОВЛЕНИЯ ПРЕЦИЗИОННОГО ПОЛУПАКЕТА (СЛОИ 1—4)
Прессование
Основной проблемой при прессовании прецизионного полупакета (слои 1—4) является размерная стабильность (усадка) внутренних слоев (слои 2, 3). Если усадка составляет более 100 мкм, то при последующем сверлении отверстий с D — d = 0,2 мм возможен выход отверстия за КП, уменьшение площади торцевого контакта и диэлектрического зазора.
На практике усадка внутренних слоев (слои 2, 3) в процессе прессования могла достигать 200 мкм, хотя исходные слои после травления имели не более 50 мкм усадки. Для изготовления внутренних слоев (слои 2, 3) было использовано несколько вариантов материалов:
- FR-4-2-18-0,2 фирмы «Isola»;
- FR-4-2-18-0,2 фирмы «Mazusita»;
- спрессованные 3 слоя препре-га 1080 (70 мкм) «Isola» с фольгой толщиной 18 мкм;
- спрессованные 3 слоя препрега 1080 (70 мкм) «Mazusita» c фольгой толщиной 18 мкм;
- спрессованные 6 слоев отечественного препрега СТП-4 (40 мкм) с фольгой толщиной 18 мкм.
Размерная стабильность (усадка) слоев из заводского FR-4 была хуже, чем у спрессованных образцов. Да и у последних усадка так же зависела от качества рулона препрега. Несколько лучше результаты были у отечественного препрега СТП-4, что, возможно, объясняется меньшей толщиной нитей, меньшим размером ячеек, большим количеством слоев и, как следствие, лучшей армированностью спрессованного диэлектрика. Недостатком СТП-4 является нестабильность свойств препрега различных партий.
Для контроля размерной стабильности внутренних слоев относительно базовых отверстий в пакете, были разработаны тест-купоны. Тест-купоны представляют собой круглые КП на наружных слоях (слои 1, 4) и кольцевые на внутренних (слои 2, 3, см. рис. 6). Купоны в количестве 6 штук размещались на технологическом поле по периметру заготовки в углах и по середине боковых сторон (см. рис. 7). Места тест-купонов локально вскрывались на спрессованном полупакете и затем на установке «Визекс» на просвет замерялось смещение внутренних слоев относительно «нулевого» базового отверстия. По результатам замеров строилась векторограмма смещения внутренних слоев. По 6 тест-купонам рассчитывалась поправка для программы сверления отверстий.
Кроме того, по боковым сторонам заготовки на слоях 1 и 4 располагались тест-линии (см. рис. 7) для замера адгезии медной фольги к диэлектрику, что является принципиально важным для тонких прецизионных проводников (75 мкм). Адгезия медной фольги толщиной 9 мкм должна составлять не менее 300 г/3 мм.
![]() |
![]() |
Рис. 6. Тест-купон | Рис. 7. Расположение тест-купонов и тест-линий |
Сверление отверстий
При сверлении прецизионного полупакета (сл. 1—4) необходимо обеспечить точность сверления (уход не более 30...50 мкм), так как разность диаметров КП и сверла очень мала D — d = 0,45 — 0,25 = 0,2 мм. То есть гарантийный поясок всего 100 мкм. На уход сверла также влияет надежный прижим комплекта для сверления: алюминиевая накладка, плата, подкладка. При уменьшении диаметра сверла может наблюдаться так называемый эффект «отскока сверла» и ухода его в сторону, что требует применения специальных материалов для верхних накладок (например, двухслойного алюминия). Также необходимо корректировать режимы сверления: увеличивать скорость вращения сверла и уменьшать подачу.
При сверлении глухих микроотверстий диаметром 0,2 мм на 8-слойном пакете со стороны нулевого и восьмого слоя важным параметром является глубина сверления. Она задается из расчета толщины фольги слоя «0», количества прокладок препрега между «0» и «1» слоями, плюс 50 мкм. То есть, сверло должно пройти нулевой, азатем и первый слой, но не более чем на 50 мкм. В этом случае будут обеспечены надежная связь слоев «0» и «1» при последующей металлизации и необходимое сопротивление изоляции между «1» и «2» слоями (из общей толщины прокладок 200 мкм останется 150 мкм изоляции). При сверлении глухих отверстий точка отсчета определяется контактным датчиком при касании фольги сверлом. Поэтому при сверлении глухих отверстий не использовались верхние накладки, сверление производилось по отдельным программам сначала со стороны нулевого, а затем восьмого слоя.
Для последующей металлизации важно соотношение глубины сверления и диаметра отверстия, которое должно быть не более 1 : 1 (см. рис. 8). Поэтому для сверла Ø 0,2 мм глубина сверления глухих отверстий составляла 200 мкм. Для улучшения гидродинамики в глухих отверстиях при металлизации лучше использовать для их сверления специальные конусные сверла (см. рис. 9).
![]() |
![]() |
Рис. 8. Глухое металлизированное отверстие |
Рис. 9. Глухие металлизированные отверстия при сверлении прямыми и конусными сверлами |
Подготовка под металлизацию и металлизация отверстий
Так как сначала изготавливается прецизионный полупакет (слои 1—4), а затем уже 8-слойная МПП, соответственно, две операции подготовки и металлизации, которые производятся по сходным режимам.
Подготовка под металлизацию проводится в несколько этапов:
- зачистка валками на установке «Комбибруш» и отмывка струями высокого давления (50 атм.);
- плазмохимическое травление в кислородно-фреоновой смеси (70 : 30) в течение 30 мин. и 10 мин. обработки в чистом кислороде;
- отмывка отверстий струями высокого давления (50 атм.) с целью удаления продуктов плазмохимического травления (пепла).
Плазмохимическое травление отверстий производилось на глубину 5.8 мкм внутрь стенки отверстия. Это обеспечивало полное удаление наволакивания смолы с внутренних торцев и надежное соединение при последующей металлизации.
Перетравливание в плазме более 15 мкм может приводить как к проблеме непрокрытий при химическом меднении сильно выступающих пучков стекловолокна, так и к ослаблению столба металлизации. В последнем случае образуется не сплошной слой металлизации, а металл с включениями стекловолокна. Это проявляется в завышенном омическом сопротивлении металлизации отверстий при электроконтроле.
Химическое меднение как прецизионного полупакета (слои 1—4), так и 8-слойной МПП производились по процессу 200 фирмы Shipley, а предварительное и полное гальваническое меднение — в сернокислом электролите с добавкой «Electroposit 272».
Для металлизации микроотверстий и при большом отношении толщины платы к диаметру отверстий для получения равномерного покрытия необходимо использовать сернокислый электролит с высокой рассеивающей способностью с высокоэффективными выравнивающими добавками, а также уменьшать рабочие плотности тока (до 1 A/дм2 и менее). Такой электролит должен обеспечивать равномерное прокрытие отверстий на платах с соотношением H/d более чем 10 : 1.
При металлизации глухих и сквозных микроотверстий (Ø 0,25 мм и менее) существенной проблемой является удаление пузырьков воздуха из отверстий во время процесса. Данную задачу позволяет решить вибрация катодных штанг.
Фотопечать и травление рисунка схемы
Для получения рисунка на наружных слоях прецизионного полупакета (слои 1—4) и 8-слойной МПП использовался тентинг-метод: негативная фотопечать, при которой рисунок схемы и отверстия защищаются СПФ при последующем травлении. Тентинг-метод имеет свои преимущества в части равномерности покрытия по всей заготовке, отсутствия металло-резиста и др. Но травление прецизионного рисунка (75 мкм/75 мкм) на полупакете сл. 1—4 с толщиной стравливаемой меди ~ 40 мкм потребовало производить прецизионное травление на установке «Resko» с системой прецизионного травления TFS в кислом растворе. С этой же целью для слоев 1—4 использовалась фольга толщиной 9 мкм вместо фольги толщиной 18 мкм.
Эксперименты по травлению пробных образцов показали, что процесс травления пробельных участков в шлейфах (много рядом идущих прецизионных проводников) отличается от травления в районе одиночных проводников: в то время как недотравливались зазоры в шлейфах, одиночно расположенные проводники перетравливались. Поэтому была произведена корректировка на фотошаблонах: при исходных размерах проводник/зазор — 75 мкм/75 мкм в шлейфах ширина проводника уменьшена до 65 мкм, зазор увеличен до 85 мкм, а одиночные проводники увеличены до 85 мкм.
При фотопечати прецизионного рисунка на наружных слоях полупакета (слои 1—4) использовались сухие пленочные резисты «Riston-215» (35 мкм) и «Alfa-340» (40 мкм). Подготовка под печать: струйная химическая обработка (обезжиривание, персульфатное микротравление, декапир) на установке «Schmid». Экспонирование производилось на установке «OPTI-BEAM» с уменьшенными относительно обычных плат режимами экспонирования (~ 30%) для проработки зазоров. Проявление резиста — в содовом (1%) растворе.
При экспонировании при использовании поправки при сверлении отверстий совмещение фотошаблона приходилось производить по прецизионной зоне глухих отверстий по тест-купонам.
Визуальный и электроконтроль
Введение вспомогательного «нулевого» слоя в 8-слойной МПП позволило изготовить отдельно прецизионный полупакет (слои 1—4) и произвести полный автоматизированный визуальный и электроконтроль его качества.
Автоматизированный оптический контроль рисунка прецизионного полупакета (слои 1—4) производился на установке АОИ «Accu-Mach» фирмы Mania-Barco. Особенностью контроля прецизионного рисунка является множество подстроек установки, связанное как с малыми размерами проводников, зазоров, так и с влиянием внутренних, близкорасположенных слоев (слои 2, 3).
Электрический контроль целостности цепей и отсутствия КЗ производился на тестере с летающими щупами «Speedy-508» фирмы Mania. Так же были произведены замеры омического сопротивления металлизированных отверстий.
Остальные операции
В качестве паяльной маски использовался сухой пленочный резист Dinamask KM-3 фирмы Morton.
Горячее лужение с выравниванием производилось на установке HAL 1000 фирмы Life.
Фрезерование по контуру и финишные операции производились по базовому техпроцессу.
Результаты работы
По разработанному техпроцессу были изготовлены 5 прецизионных полупакетов (слои 1—4) и три 8-слойные МПП. Платы прошли все виды контроля и соответствуют требованиям КД.
ПЕРСПЕКТИВЫ РАЗВИТИЯ ТЕХНОЛОГИИ ПРОИЗВОДСТВА ВЫСОКОПРЕЦИЗИОННЫХ МПП
С возрастанием сложности МПП и увеличением плотности монтажа растет прецизионность проводящего рисунка, что требует разработки технологии, позволяющей получать печатные элементы с параметрами проводник/ зазор — 50 мкм/50 мкм и менее. Одним из перспективных направлений, требующих такого рода параметров, является конструктив «система на кристалле» и «система в корпусе». Решать задачи достижения параметров проводник/ зазор — 50 мкм/50 мкм и менее позволит технология «ПАФОС» (Полностью Аддитивное Формирование Отдельных Слоев). Данная технология (ее еще называют метод Переноса) предусматривает получение проводящего рисунка гальваническим наращиванием по рисунку схемы на временных стальных носителях. Затем его запрессовывают (переносят) в диэлектрик, получая таким способом высокоплотный проводящий рисунок, прецизионность которого определяется только разрешающей способностью фоторезиста. На следующих фотографиях представлены фрагменты прецизионных полупакетов (слои 1—4), изготовленных по методу тентинг (негативный) (см. рис. 4, 5) и методу «ПАФОС» (см. рис. 10, 11).
Данная технология позволяет достаточно надежно получать слои с параметрами рисунка проводник/зазор — 50 мкм/50 мкм (см. рис. 12).
Методом переноса можно получать высокоплотный проводящий рисунок с параметрами проводник / зазор — 10 мкм/10 мкм (см. рис. 13). Рисунок приведен по данным специалистов фирмы «Samsung».
Преимуществами метода «ПАФОС», кроме высокой прецизионности и плотности проводящего рисунка, является лучшая механическая стойкость тонких проводников и их адгезия к основанию за счет того, что они запрессованы в диэлектрик. Платы, изготавливаемые методом «ПАФОС», производятся на том же оборудовании, что и платы по традиционным технологиям. Требуется только некоторая дополнительная оснастка и несколько увеличивается длительность техпроцесса. Важен также уровень квалификации специалистов для изготовления МПП с прецизионным высокоплотным рисунком.
![]() |
![]() |
Рис. 10. Прецизионный полупакет (слои 1—4), изготовленный методом «ПАФОС» |
Рис. 11. Фрагмент полупакета (слои 1—4), изготовленного методом «ПАФОС» |
![]() |
![]() |
Рис. 12. Фрагменты внутреннего слоя прецизионной платы (вверху: проводник/зазор — 70 мкм/70 мкм; внизу: проводник/зазор — 50 мкм/50 мкм.) |
Рис. 13. Изображение поперечного сечения внутреннего слоя с элементами рисунка проводник/зазор — 10 мкм/10 мкм. |
ЗАКЛЮЧЕНИЕ
Разработан технологический процесс и изготовлены МПП с шириной проводников и зазоров 75 мкм и с микропереходами 0,2 мм на базе стандартного оборудования и имеющихся на рынке материалов. Разработанный техпроцесс комплексно интегрирован в стандартный технологический маршрут производства МПП.
В проведении экспериментов и изготовлении МПП кроме авторов принимал участие коллектив ведущих специалистов ИТМиВТ: Николаева Е.М., Косоурова Т.Г., Фролова Л.И., Баева О.М.